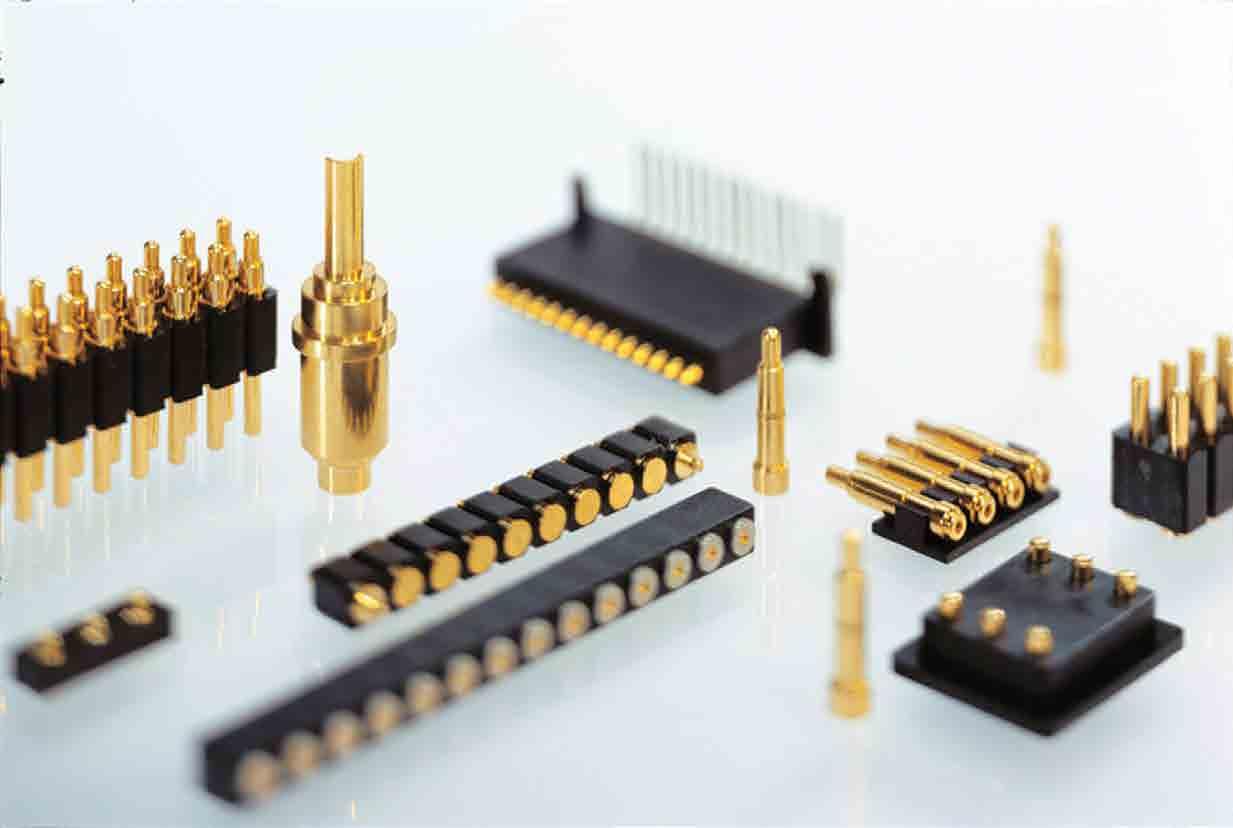
4 minute read
Making contact Preci-Dip
MAKING CONTACT
Preci-Dip is a world leader in the development and manufacture of highly reliable contacts and spring-loaded pogo pins that are used in a variety of demanding interconnect functions in the automotive, telecommunications, medical, industrial, aircraft, missiles and helicopter applications, to name but a few! Marco Siebel spoke to managing director Raymond Kerrison.
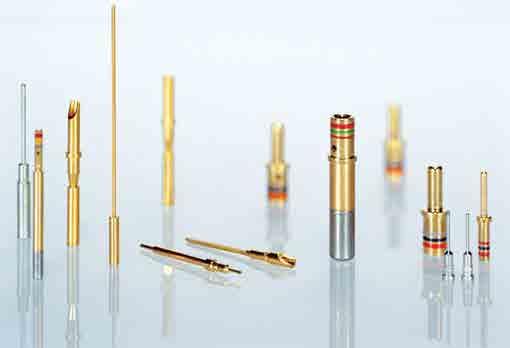
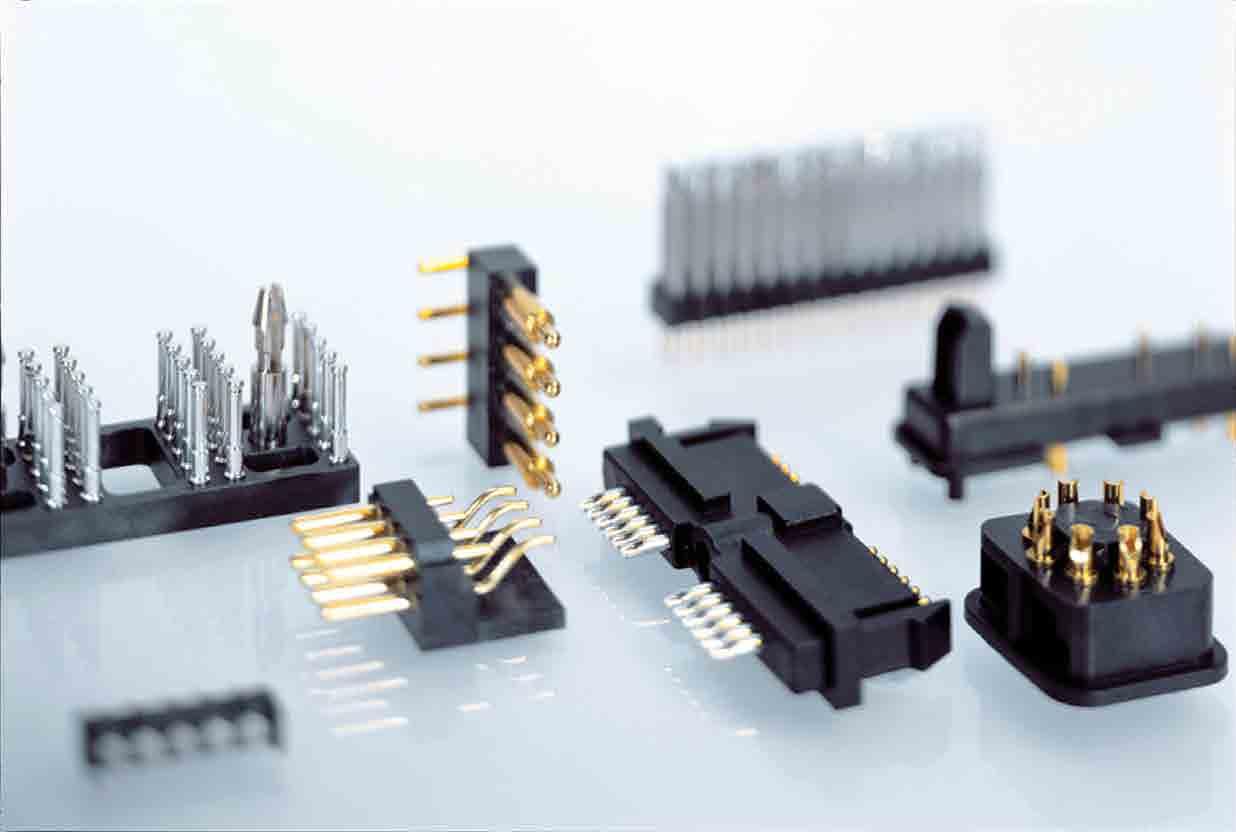
Preci-Dip has its headquarters in Delemont, Switzerland and employs 240 people. “We invested significantly in 2012 in reinforcing our project management teams and in our development capabilities,” says Raymond Kerrison. “We have hired people in quality, product development, our laboratory and advanced engineering in order to respond to the many diverse applications that we are seeing today. People are not just looking for the standard product lines; rather customers are coming to us and saying ‘We need a solution that can respond to these specific requirements.’ So we see growth in custombuilt specific applications, often in demanding environments, which is a significant differentiator for our company.”
Preci-Dip spring-loaded (pogo) contacts
Preci-Dip spring-loaded contacts are made of a contact body or barrel, a piston and a helical compression spring. The electrical contact is established by pressure against a fixed, flat area called the pad connector. Preci-Dip has developed additional designs featuring specific advantages such as contacts with a slant or polygonal piston; this design leads to a radial force on the piston resulting in a lower electrical resistance. Another model has a patented coaxial or in-line design with an integrated multi-finger sliding clip contact, establishing electrical continuity between the body and the piston. The multipoint connection guarantees low, stable electrical resistance values without micro-discontinuities, even when the piston is moving or subject to vibration, thus assuring maximum reliability. Since 1995 Preci-Dip has been producing a wide range of contacts of many sizes and with a variety of technical specifications. In certain areas where high insertion cycles and/or a large stroke is required in a reduced space, the spring loaded contact solution is recommended. SLCs also excel in demanding vibration environments.
MIL contacts
Preci-Dip has drawn on its unique expertise and know-how to develop new MIL socket contacts based on clip technology. Two socket contact technologies are available – hooded contacts using a reversed clip and hoodless contacts using an Eagle Grip clip. Both types of contact have successfully passed all the qualification tests according to AS39029 and are listed on the QPL. Preci-Dip also manufactures the corresponding precision-machined pin contacts.
Separate electroplating processes for the body and clip allow the best cost-performance ratio, effectively assuring the ideal gold plating in the contact area. The assembly of the parts is then carried out on dedicated, fully automated assembly lines. Reversed clip contacts are presently available in in size 12, 16, 20 and 22. This proprietary technology, entirely developed by Preci-Dip, is protected by international patents. In comparison with the traditional slotted contact body, the reversed clip design has several advantages: there is a smaller difference between insertion and extraction force, a reduced dispersion of the force values and better redundancy at the contact point, thanks to six or eight contact fingers.
The hoodless contact consists of two parts – the contact body and the clip are

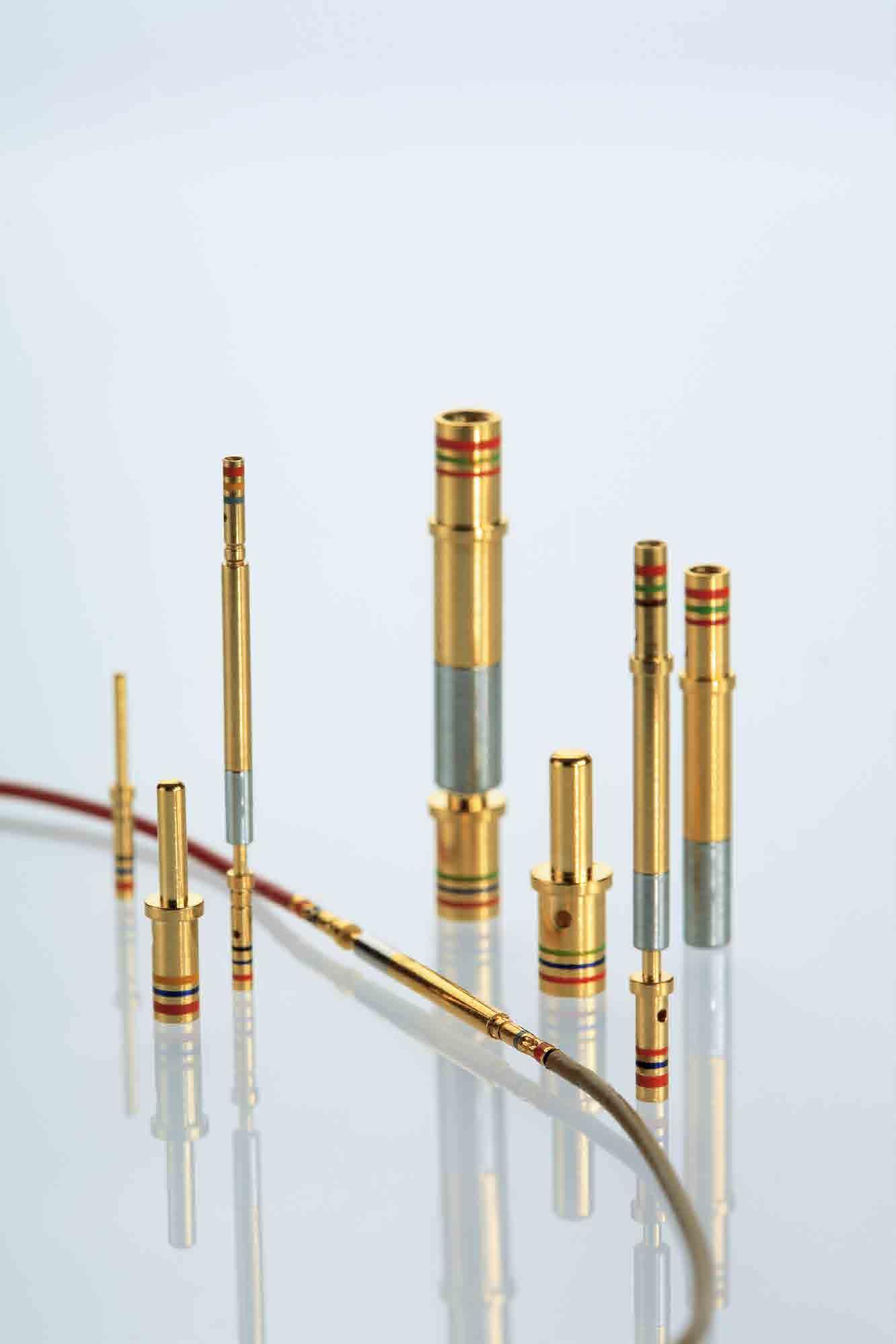
made from different base materials. The high-speed screw machined contact body is made of brass and the use of quality crimping brass makes annealing unnecessary. The precision stamped and formed Eagle Grip clip is made of beryllium-copper. Separate electroplating of the body and clip offers the best cost-performance ratio.
“We are a very innovative company, very responsive to customers,” says Raymond Kerrison. “What facilitates that responsiveness is that we do everything in-house: we manufacture our own springs, we do all our own screw machining, stamping and moulding and we even manufacture our own tape and reel for packaging.”
Worldwide sales
Prec-Dip has sales offices in Germany, Italy and France as well as in the USA, China and Japan with 20–25 per cent of sales are generated in the USA, 15–20 per cent in Asia and 60 per cent in Europe.
“Last year we were present for the first time at trade fairs in China, India and Japan,” says Mr Kerrison. “We were also at the Farnborough International Air Show in the UK and we had a very successful Electronica trade fair in Munich. We anticipate approx. 10 per cent growth in 2013 and up to 40 per cent growth by 2015. We see a huge potential in the military and aerospace industries. To enhance our position in this market, our production facility has recently successfully completed EN 9100 certification. We are targeting TS16949 certification for the end of this year to reinforce our position in the automotive market. Our growth will come organically. There is also a possible extension of our manufacturing operations to Asia.”
Positioning for the future
“We will continue to enhance our standard product range of contacts, sockets and SLCs with high-quality competitive products but we are also going to differentiate ourselves by providing our customers with high-quality customised solutions,” explains Raymond Kerrison. “Where the environment is challenging and standard solutions do not provide satisfaction, we will excel. We are positioning ourselves where we will not have any serious competitors because we will offer customised solutions that no-one else can implement and industrialise as effectively as we can.” n
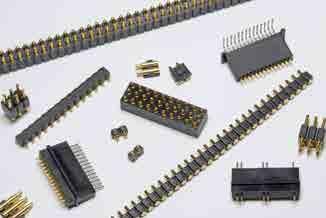
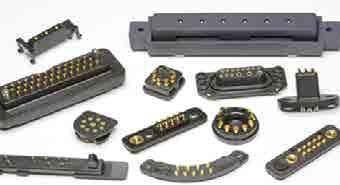