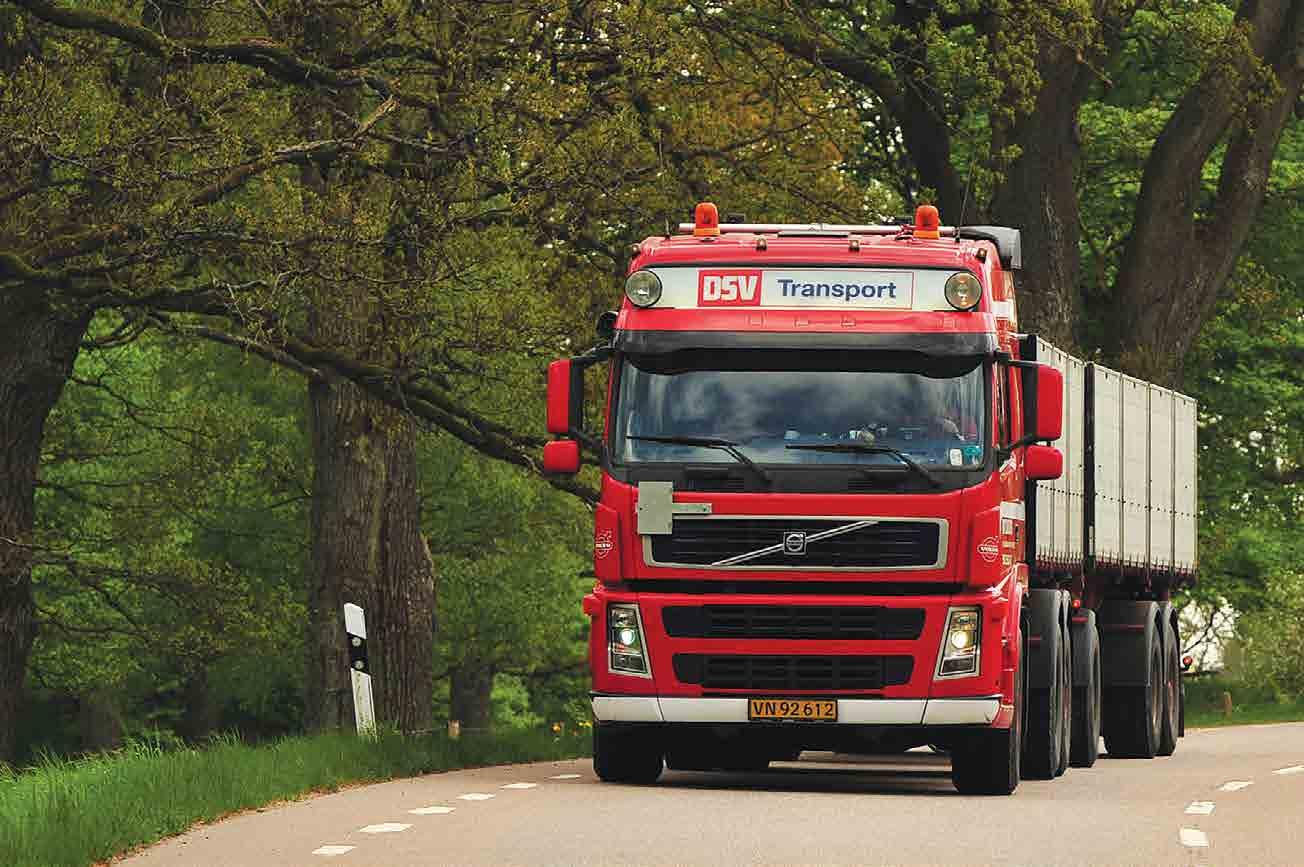
4 minute read
Clean and green Alfdex
CLEAN AND GREEN
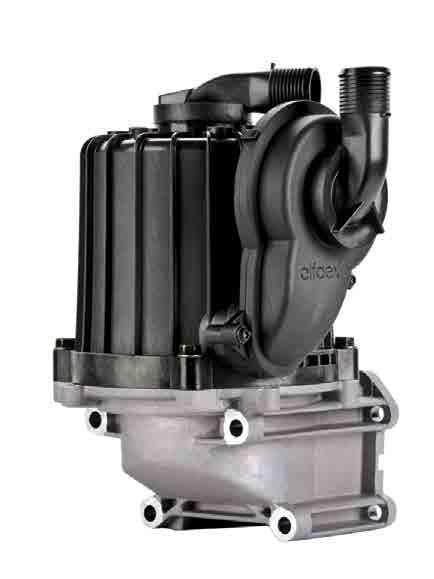
Alfdex AB is the world’s leading supplier of highly efficient solutions for cleaning of crankcase gases from diesel engines. Abigail Saltmarsh looks at its exciting future.
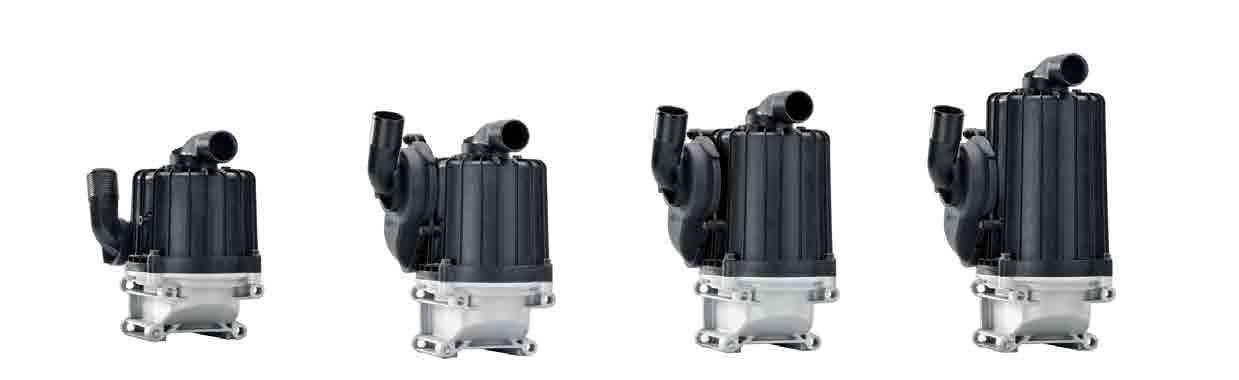
IN 2014, with the arrival of Euro 6 legislation, it will not only be emissions from exhaust pipes that will be subject to rigorous restrictions but also those from diesel crankcases. But Swedenbased Alfdex is ready for the change with its pioneering separation technology, which not only cleans the gases but also puts the oil back to the diesel engine rather than out into the environment.
President of the company, Mats Ekeroth, explains that Alfdex has been supplying the US market up to this point. There, legislation was brought in earlier, and manufacturers are already building the technology into their trucks on a much higher scale.
“We have been using this technology in North America since we started high volume production in 2007,” he explains. “When the new legislation arrives in Europe we will be ready with a new generation of products. We are already investing in new assembly lines for this new version and we expect to double the number of separators we are producing.”
Crème de la crème
Alfdex was founded in 2002 as a joint venture by the two Swedish companies Alfa Laval and Haldex. In 2011, Concentric took over the Haldex holding in Alfdex, so now Alfdex AB is a 50/50 joint venture between Alfa Laval and Concentric. Alfa Laval is a leading global provider of specialised products and engineering solutions based on its key technologies of separation, heat transfer and fluid handling.
Concentric is a global company specialising in fluid dynamics and fluid power technologies. Its aim is to provide better fuel economy, emissions reduction, vehicle control and productivity in trucks, buses and off-road vehicles.
Although Alfdex was established as late as 2004, its roots go back much further, as Mr Ekeroth points out. In 1877, the Swedish inventor Gustav de Laval demonstrated his idea of using centrifugal force to separate cream from milk. De Laval’s idea has over the years created one of Sweden’s largest companies – Alfa Laval.
“The idea for our product comes from developing this product. We have been reusing similar technology but for a very different application.”
Reusing the oil
Many people do not realise that, in addition to exhaust pipes, crankcases are responsible for emissions, says Mr Ekeroth. Without a cleaning system, some 20 to 30 litres of oil is released to the environment.
“The beauty of our system is that almost 100 per cent of that oil is taken back into the engine. It can be fitted into any diesel engine and it meets the requirements of the new emissions legislation,” he says.
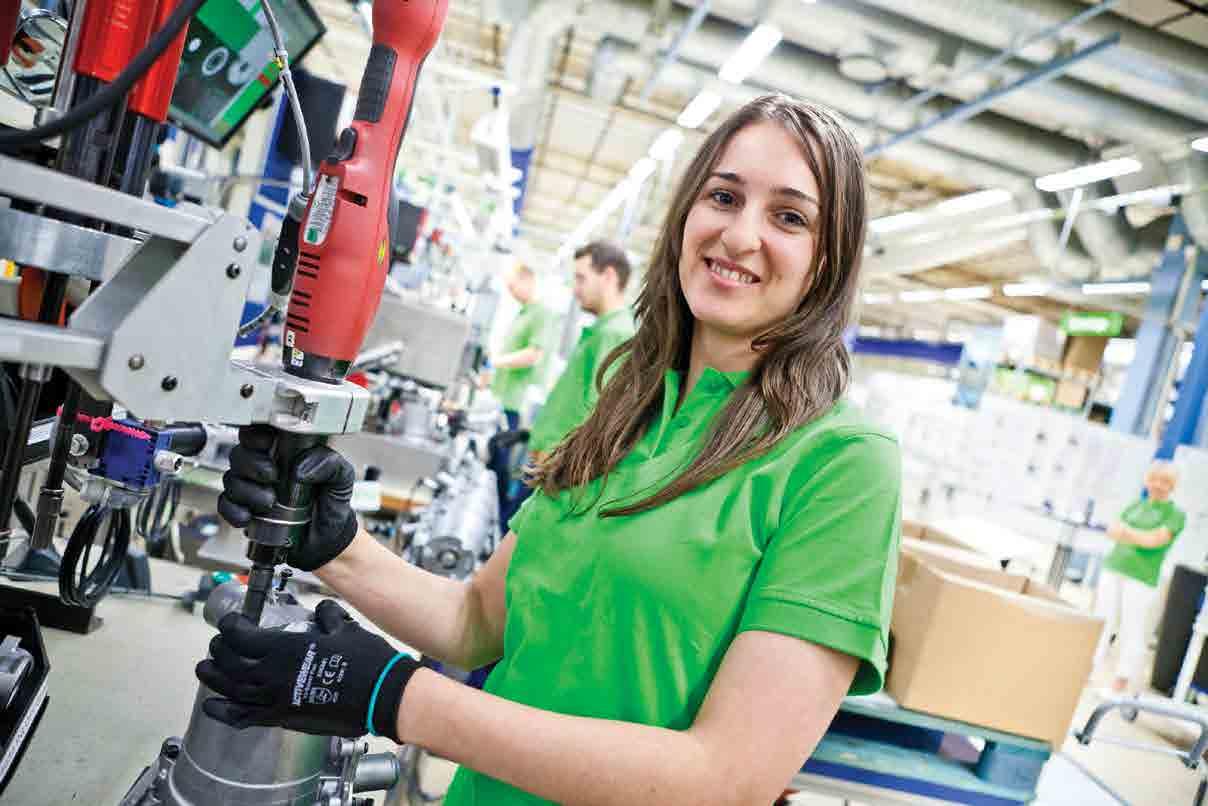

www.evometall.com
Located in south-sweden.
Metallfabriken EVO AB
• Pressure die casting in aluminium with machines from 150 to 650 ton. (1500 to 6500 kN) • Pressure die casting in zinc with a 90 tons machine (900 kN) • Gravity die casting (kokill) in aluminium and zinc
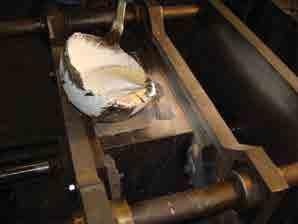
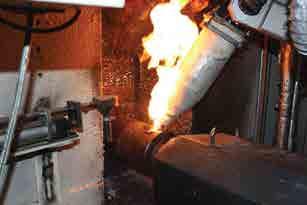
The oil-driven separator already has a surplus of oil flow available from the engine’s lubrication pump, and this is more than sufficient to drive the separator. Using oil to drive the unit also guarantees that the bearings are properly lubricated throughout the separator’s service life, which is the same as the lifetime of the engine.
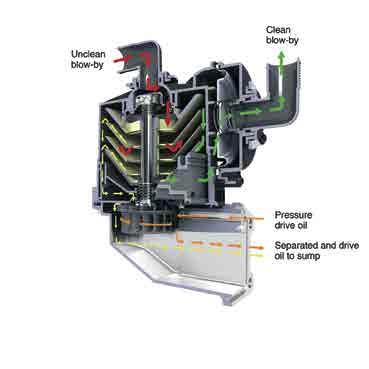
Centrifugal force
The oil mist separator is built around a rotating conical disc stack. An oil turbine at the bottom of the centrifuge drives the disc stack. Part of the lubricating oil circulating in the engine is routed to a nozzle that directs an oil jet to drive the turbine.
The oil and soot particles are removed from the gas by means of centrifugal forces of around 2500 to 3000g at a separator speed of 7000 to 9000rpm.
The centrifugal force makes the droplets and particles coalesce and form larger clusters that flow towards the outer edge of the discs. From there they are discharged onto the inner wall of the separator housing. The droplets and particles then flow down to the bottom of the separator, before finally being returned to the engine sump. The next step
Operating today from a facility in the south of Sweden, the company sends approximately three-quarters of its output to the USA. There are currently no plans to relocate production, as the company feels well-placed to serve its growing European market.
“In North America we have a market share of about 70 per cent. In Europe, it is about one-third but when the new legislation comes in we expect that to double to two-thirds, which is why we are making this significant investment in readiness,” says Mr Ekeroth.
“After the legislation comes in here we expect it to be rolled out across the rest of the world over the next five to ten years. At that point it may be a different story when it comes to considering setting up a second production facility.”
Today, Alfdex, which saw a turnover last year of around €30 million, has 100 employees. Over the next two years this will grow significantly, thanks to the new European legislation.
“Last year, we celebrated the production of our one millionth separator,” he adds. “This is an exciting time for us and we are ready for this next big step.” n
