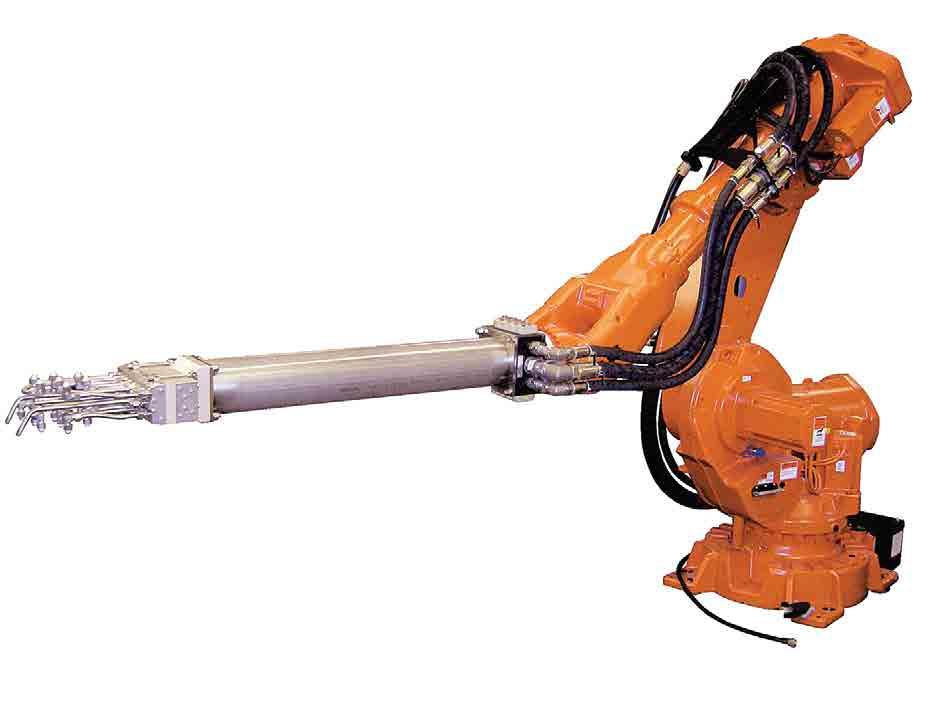
5 minute read
Developing high-performance process solutions AED Automation
AED-Automation is a global leader in the development and manufacture of automated process solutions for the world’s forging and casting industries. Philip Yorke talked to Franz Neuner, the company’s international sales director about its latest high-pressure ‘inner-coating’ systems and its growing presence in the emerging economies.
DEVELOPING HIGH-PERFORMANCE PROCESS SOLUTIONS
AED Automation was founded in 1973 at a time when it was known as the Acheson Group, which was for many years the market leader in the area of graphite dispersions and graphite coating systems. The company’s extensive manufacturing plant at Dornstadt was built in 1973 by the Acheson Group and has since seen major investments to make it the leading, state-of-the-art facility in its market sector. After being acquired by the ICI Group in 1998 and subsequently by Henkel in 2008, the company returned to private ownership in 2010 when it was purchased by the family-owned Wollin Group of Germany, thus bringing together almost 40 years of advanced automation technology.
Leading in automated process solutions
AED Automation continues to set the industry standards when it comes to foundry and die-casting automation and in particular, the area of specialised cooling and lubrication processes. Perfect lubrication for casting or forging dies requires perfect application technology to optimise both the processes and a customer’s profits. This was the driving force behind the construction of the original engineering site in Dornstadt in 1973, since which time the company has grown to become a global pioneer in precision spraying technology in this highly specialised market segment. Today, AED Automation offers a complete line-up of high-performance spraying systems, as well as lubricant mixing and dosing units, in addition to ground-breaking foundry automation solutions and services.
AED Automation offers standardised as well as tailor-made casting-line solutions for its customers with an unparalleled range of linear, robotised and gantry solutions, all of
which can be adapted to suit almost every known casting process requirement.
Mr Neuner said, “As a flexible, familyowned business, we take care of every aspect of our customers’ cooling and lubrication processes. We understand the needs of our customers and the daily challenges they face in today’s competitive marketplace. We like to think outside the box in order to provide smart, effective solutions that overcome complex production problems and to optimise our customers’ efficiency. We really take care of our customers’ requirements and offer a comprehensive range of products and services. These do not end simply at the design and installation stage, but include cutting-edge solutions that are setting new standards in today’s ‘minimum quantity’ spraying technology requirements. We have also developed a unique system for inner-coating pipes and tubes as small as 3cm in diameter. This precision inner-coating technology is extremely accurate and will be launched in 2013.”
Mr Neuner added, “We begin every project by understanding fully our customers’ needs and expectations and then we adapt our machinery and technology to create optimal solutions for them. We don’t sell standard products but we do sell product platforms upon which we can build the perfect, tailormade ‘smart’ solutions for our customers. Today, we are able to offer the world’s most sophisticated and reliable technology and our customer-orientated approach guarantees the highest levels of service and efficiency. Recently we completed a major project in India, where we designed and installed an advanced 1000kg precision spraying system, as well as developing a complete range of automated spraying systems for our customers in Italy and China.

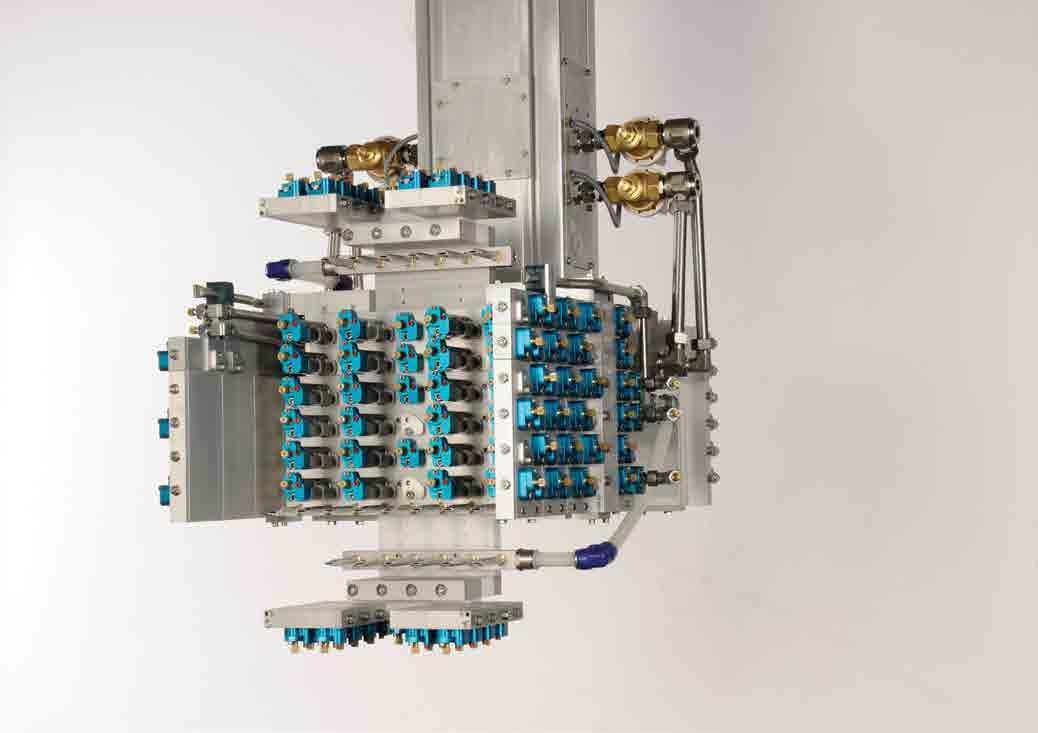
“We are a global supplier and as such are present wherever you find die-casting and forging on any scale. We are also fortunate in so far as our location is concerned, because being situated near Stuttgart, we are in an area where some of the world’s best and brightest design and engineering specialists can be found. This in turn means that we have the cream of the crop when it comes to employing the best-qualified and most motivated engineers. Whilst Europe and the USA remain our biggest markets, our growing presence in many of the world’s emerging economies is providing the strongest growth opportunities for us for the foreseeable future.”
Fully integrated automation
AED is dedicated to improving process cycle times, providing perfect lubrication solutions and guaranteeing reliability throughout its customers’ forging processes. AED’s forging experts create individual process solutions that are tailor-made to optimise value and provide optimal manufacturing performance. Today, the company is committed to an ongoing programme of continuous investment in technology and R&D, which is designed to improve overall productivity and performance and to offer a significant increase in the life of the dies in use. Its casting lines are also highly automated and offer the perfect opportunity for integration into a customer’s own improved production line capabilities.
AED also recognises that forging lines are very individual concerns and that almost every line has its own unique features. The flexibility and creativity that exists within the extensive AED resource at Dornstadt offers

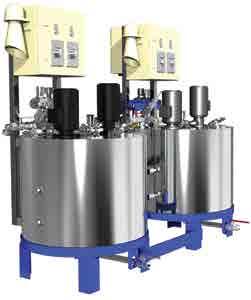

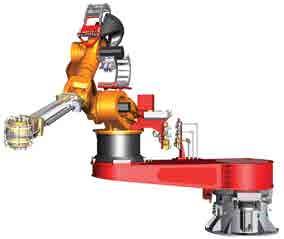
customers unique, tailor-made solutions that achieve the best possible outcomes. However, spraying technology remains the company’s core competence and AED has also extended its portfolio of advanced foundry automation equipment. Its external atomisation technology has proved to be the best solution for any number of diverse industrial applications. All AED systems work with low-pressure thresholds to achieve greater efficiency and to be able to offer the best cooling and coating performances available on the market today. n

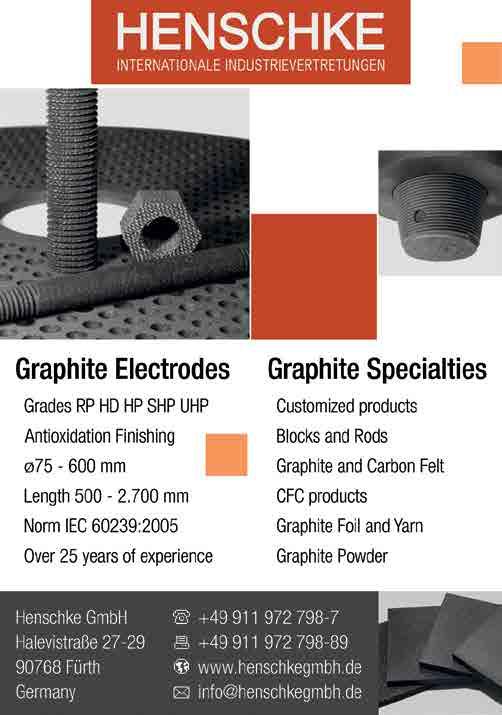
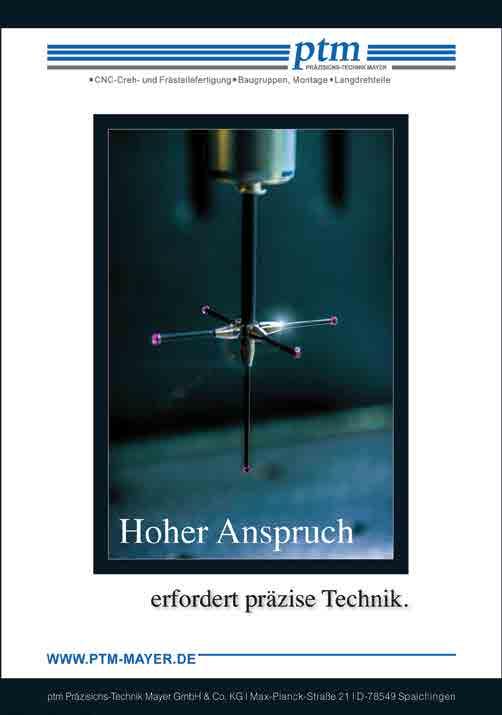