
8 minute read
All-round quality development IRO
ALL-ROUND QUALITY DEVELOPMENT
Just as in the past, the core business of IRO (Industrie Riunite Odolesi) SpA is still the production of reinforcing bars, but for some years now the company has started diversifying its activity, manufacturing niche products and billets. Barbara Rossi interviews Mr Carlo Leali, the company’s vice-president.
IRO SpA has a 60-year history, having been established in Odolo (Brescia) in 1951, as a rolling mill for the production of reinforcing bars. The company further developed its activity over the years, with the installation in the 1960’s - of the first electric furnace for scrap melting and the introduction of one of the first continuous casting lines for billet manufacturing, followed in the 1970’s by the installation of a new rolling mill and a new continuous casting machine, always with the aim of increasing production and improving product quality. In the 1990’s there was another quality leap, thanks to the inclusion of the Tempcore system, for product welding and ductility, into the manufacturing process; and to gaining the UNI EN ISO 9001 certification, in addition to which today the company has also achieved the UNI EN ISO 14001 environmental benchmark.
Two years ago IRO, which currently has 215 employees and an annual turnover of about €200 million, made investments totalling €12 million for the construction of a new continuous casting line, which has allowed it to widen the dimensional range of the billets that it manufactures, which can now reach maximum square section dimensions of 180x180mm. Moreover, thanks to this line, the company can manufacture quality steels, a sector which the company is trying to expand, to counterbalance the dip in demand for reinforcing bars, due to the crisis affecting the construction sector in Europe.
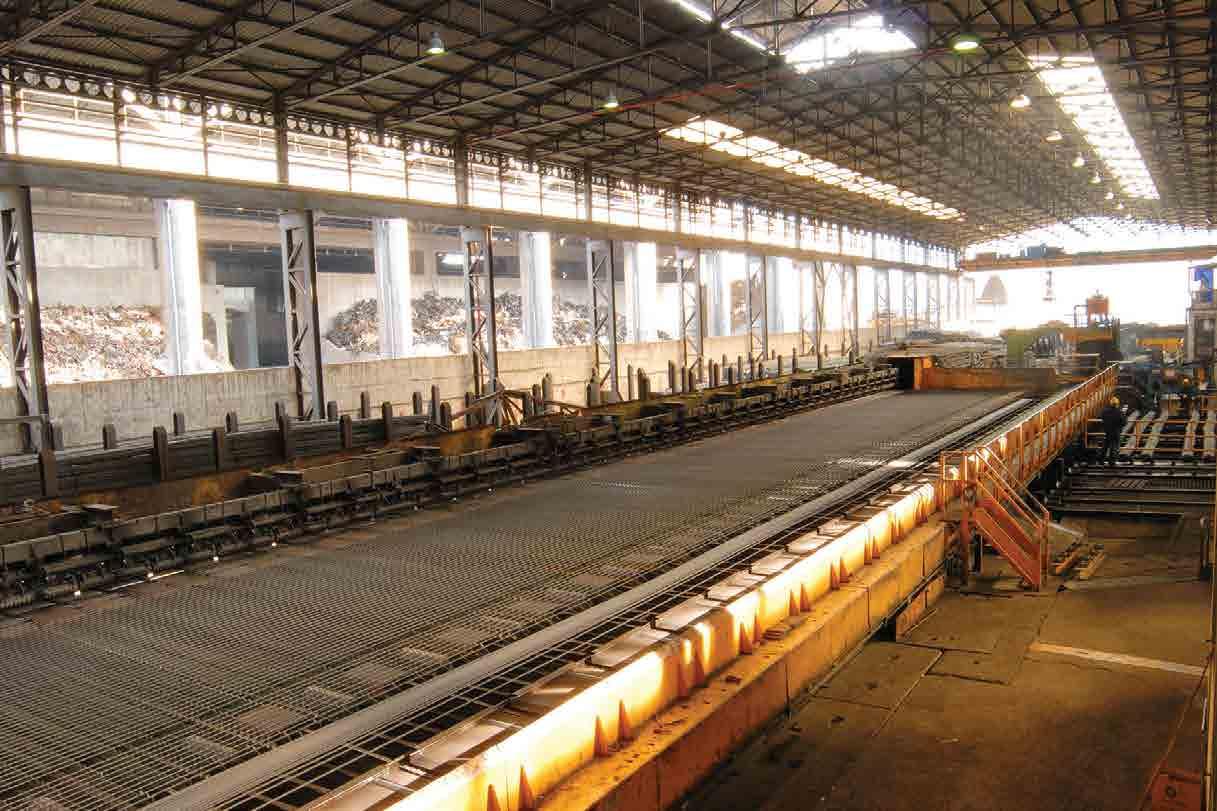
Following the diversification route
Nowadays about 70–75 per cent of the company turnover derives from the sales of finished products, in other words bars. 80 per cent of this percentage is generated by reinforcing bars, which anyhow remain the company’s main activity. The remainder derives from the previously mentioned niche products – mainly in the form of smooth bars for various uses, mainly produced using highquality steel, according to the requirements of the final application for which they are meant. Smooth bars are supplied to a wider range of sectors, including the mechanics, prefabrication and moulding industries. “Our billets are a semi-product, not a finished product like bars. 25–30 per cent of our turnover derives from these products, which are then transformed by other rolling mills or moulders. The type of steel employed in our billets varies according to the final application,” Mr Leali explains.
IRO also owns an 80 per cent share of Nova PM Sider, a pre-forming company based in Bologna, engaged in customising, with tailored modifications, reinforcing bars so that these fulfil the design specifications of the architects in charge of the construction projects. “This is an activity which until 20–30 years ago companies used to carry out internally, but which in recent years, due to cost optimisation, has been outsourced. About 5 per cent of the reinforcing bars that we produce are for Nova PM Sider, while the rest is sold to other processing plants which also carry out pre-forming. This is what happens in terms of the reinforcing bars that we sell in Italy. With regard to foreign sales, in particular those in nonEuropean countries, predominantly concentrated in Algeria, we supply large local distributors, which then resell our products. In terms of reinforcing bars, the export share has significantly increased in recent years; suffice to say that today it almost reaches 50 per cent, while 20 years ago it was about 15–20 per cent. This increase in the export share is mainly due to the crisis which has hit the construction sector in Europe, and particularly in Italy, causing a reduction of the volumes supplied to these
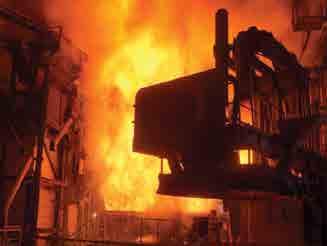
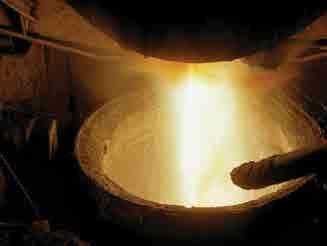
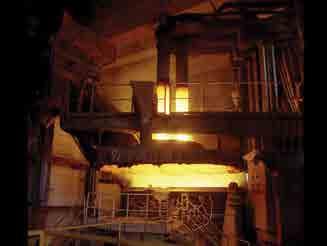
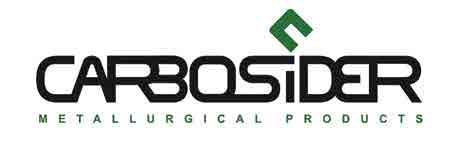
Sede Legale: Via Marzabotto n.3 - 25040 - Corte Franca (BS) Sede Commerciale: Via C. Battisti, 18 - 25040 - Corte Franca (BS) Phone: +39.030.8364280 | Fax: +39.030.9826242 | Email: info@carbosider.eu
Carbosider is a slim, modern company, with strong roots in the metallurgical sector, with several years of experience in the supply of raw materials to steel plants and foundries, an area in which it has gained recognition for its reliability and competence.
Always striving to achieve increasingly high product quality, Carbosider Srl has established close commercial and representative relationships with some important manufacturers of materials for the metallurgical industry, from which are sourced high quality products.
The continuous search for technological improvement and service quality means that the company can avail itself of two warehouses where the various types of materials are stocked, so as to be able to offer fast and accurate deliveries to clients, who need high quality products to be delivered quickly. In order to fulfil customers’ needs, the company also has a plant for grinding and screening of ferroalloys, where it is able to achieve any requested granulometry and to produce any type of packaging (big bags, barrels), as well as various materials.
In addition to the Italian market, where Carbosider Srl was born, the company has expanded its activity to other European, Asian and North-African countries, continuously widening its network of clients and becoming a reference point on the global market.
The main products handled by the company are as follows: • Standard and noble ferroalloys • Metallic silicon • Recarburizers • Graphite electrodes • Refractors And other high-technology products for the metallurgical market.
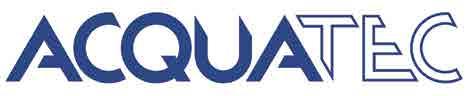

For over thirty years our company has been engaged in pump maintenance and repairs and we have held the ISO 9001 System Quality certification since 2001.
We are an authorised KSB, ABS, and Varisco workshop, but we do not limit ourselves to these brands, as we are able to repair pumps of practically all the brands available on the market.

We also act as Danfoss Service providers for inverter repairs in Lombardy.
In addition to our repairs activity, we carry out supply/installation of pumps, valves, inverters and all the hydraulic, electric and electronic equipment for fl uid shut-off, measurement and treatment; as well as fi re systems and connected maintenance/assistance.
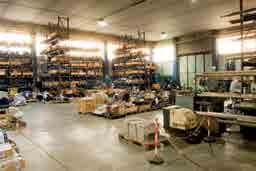

www.acquatec.it
Acquatec Srl • Via Averolda 25, 25039 Travagilato (Brescia) - Italy Tel.: +39-030-662261/2 • Fax: +39-030-662263 • Email: info@acquatec.it Meccanica Resinelli Srl has a consolidated experience as a mechanical processing workshop specialised in mechanical turning, milling, repairs, welding, assembly and carpentry.
For years we have mainly been serving the metallurgic sector, manufacturing any type of components for steel plants, continuous casting and rolling mills.
We process and carry out welding of any kind of materials, including copper, aluminium and stainless steel; and we also manufacture components for robotics and pliers for transfers.
The staff is composed of personnel highly skilled in any kind of processing. Furthermore, within the company, there is a technical offi ce which deals with design development with regard to two and three dimensional processing with CAD and CAM technology.
In the last few years the company has invested in ultra-modern tool machines, with the purchasing of a 5-axis work centre able to perform any type of processing, even if complex.
Via San Lino, 44 - 25071 AGNOSINE (BS) Phone/Fax: +39 0365 826022 • Mobile: +39 339 7515514 E-mail: meccannicaresinelli@libero.it


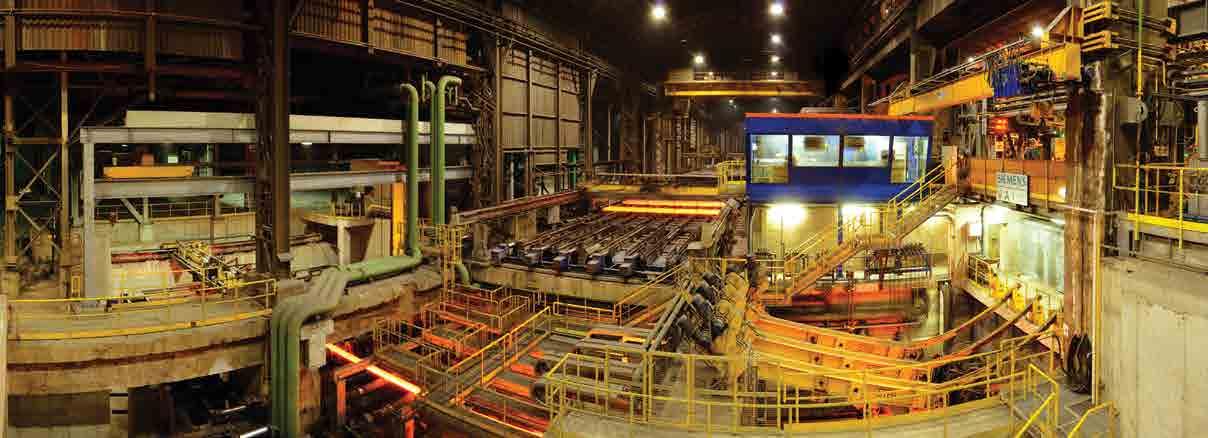
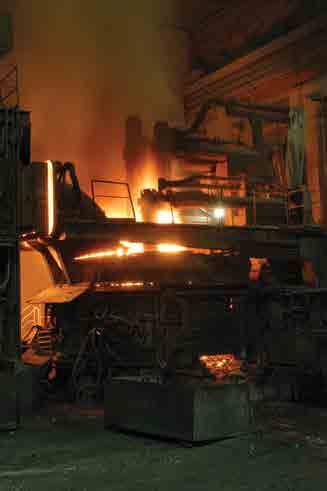
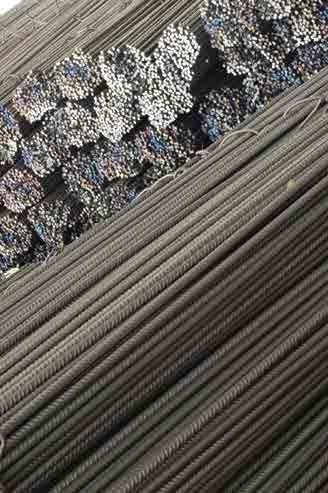
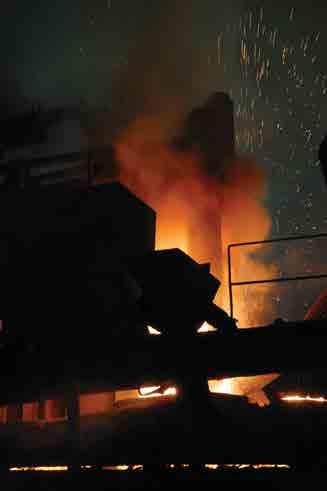
geographical areas. This reduction took place four or five years ago, while I would say that in the last two or three years volumes have stabilised. In this framework the level of overall product volume has remain unchanged, but the foreign market has acquired an increasingly greater importance and our international share has grown in comparison to the total.”
Concluding our conversation, Mr Leali states, “Precisely the crisis of the construction sector in Europe, Italy included, which started a few years back, has made us take the decision to differentiate our activity both in terms of new geographical markets – as we did for reinforcing bars – and in terms of new market segments – which we have done with the development of quality steel production and with the widening of the dimensional range of the billets that we produce. Both smooth bars and billets will allow us to supply a wider range of industrial segments, which in future we would like to expand so as to also include the automotive sector. Our smooth bars are mainly sold in Italy. Our billets also mainly supply the national market. In terms of our traditional product and core business, which is reinforcing bars, differentiation has mainly taken place in terms of new geographical markets. As already mentioned, Algeria is our main export market, thanks to the significant development of this country and the fact that other areas around the Mediterranean basin are experiencing particular political phases. Clearly, we are still exporting in Europe, to places such as France, Switzerland, Germany, Croatia, Slovenia and other nearby countries. We will continue our diversification process, and reinforcing bars will remain our main product. Geographically we are always looking for new markets which, due to the nature of reinforcing bars and to the bearing of transport costs on the final price of this product, must be in areas close to us.” n
