
4 minute read
Cutting-edge sand-casting solutions Thoni-Alutec
CUTTING-EDGE SAND-CASTING SOLUTIONS
Thoni-Alutec is a technology leader in the production of aluminium sand castings and die castings for manufacturing industries. Philip Yorke talked to Mr Jay Kitchen, the company’s senior technical manager at its UK facility, about its current production facilities, complete value-chain services and move into new markets.
Thoni-Alutec is an independent, privately owned company that was founded in Germany in the 1960s and is now in its third generation of family ownership. Following consistent growth since its inception, the company established a state-of-the-art manufacturing facility in Poland in 1998 and has since invested in another facility close to the original plant. The combined total of available production space is more than 72,500m2, which is set in an area covering over 27 acres.
Today, Thoni-Alutec continues to maintain its European sales office in Germany, as well as a sales and technical support facility in the UK. Thoni-Alutec supplies aluminium castings to its customers in Europe, the USA, the Middle East, India and China. With more than 1250 employees and a turnover of over €100 million, the company has grown to become one of the largest aluminium jobbing foundries in the world.
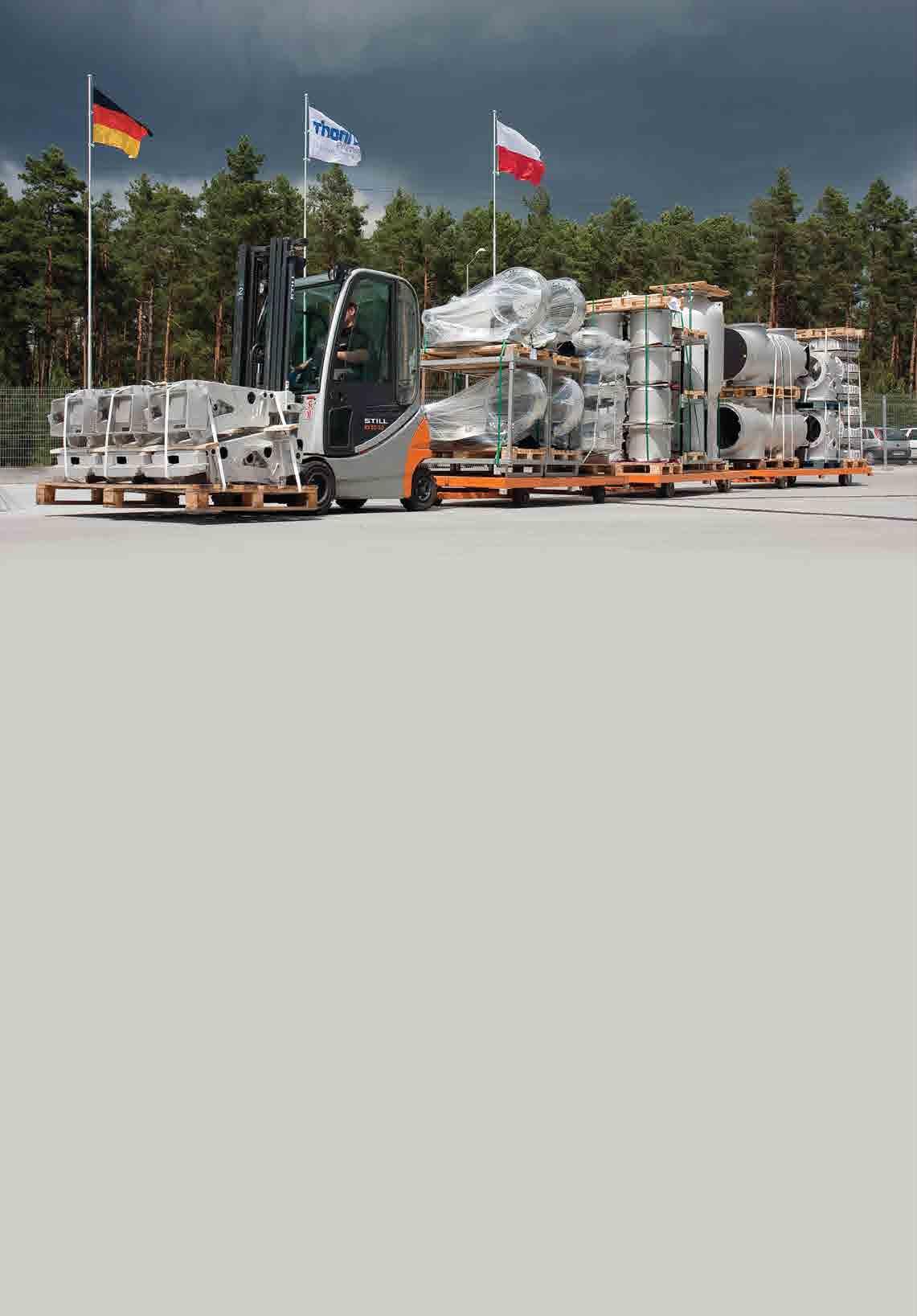
Complete supply chain expertise
Experience gathered over many decades combined with continuous expansion of its manufacturing facilities along with the training of highly skilled staff has made Thoni-Alutec one of the world’s most competent and successful foundries in its sector. Further diversification of its core activities provides customers with complete supply-chain service operations in relation to aluminium castings. In addition, ThoniAlutec’s customers are individually supplied with tailor-made castings according to various international standards and thereby receive the optimal solution to their requirements.
Starting from casting design and pattern shop to foundry, machine shop and assembly, the company supplies high-precision aluminium castings up to 10 tonnes in weight and more than 10 metres in length. During the entire production process the casting integrity is checked in relation to international standards using X-ray, ultrasonic, and dye penetration tests. Dimensional inspection and mechanical testing is also included.
Mr Kitchen said, “We serve a broad section of industry from automotive to medical and from energy to aerospace. We also supply some of the world’s biggest OEMs, as well as smaller and medium-sized busi-
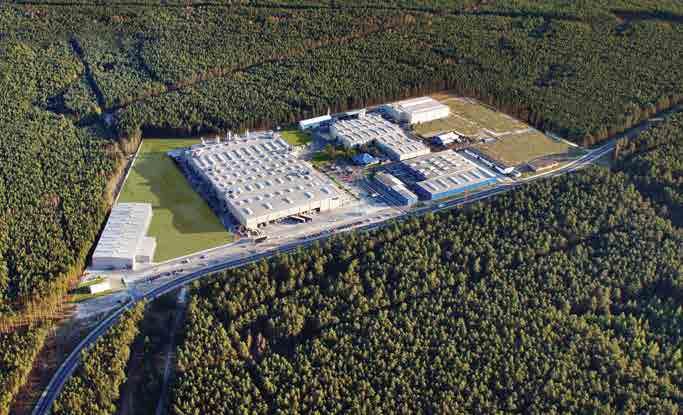
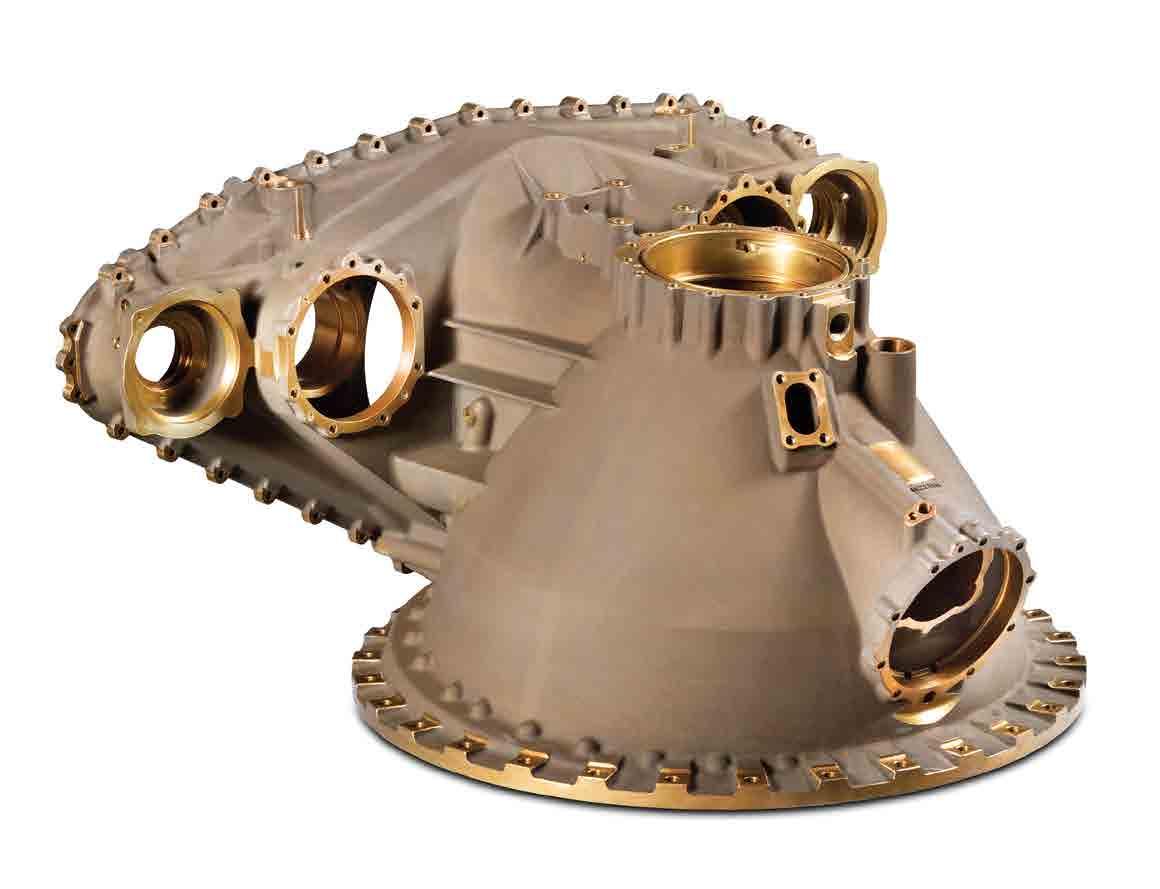
nesses. The renewable energy sector is a growth area for us, which not only involves the manufacture of wind turbine parts but also the more traditional large generator sets and power distribution centres. We are also seeing growth in the demand for castings used in power stations for high-voltage switch gear applications.
Mr Kitchen added, “We specialise in sand casting, low-pressure sand castings, low-pressure die castings and gravity die casting everything is conducted in-house so that we can control the quality and precision of everything we do from concept to final assembly. We are also very environmentally aware and recycle all our sand and use the heat from our furnaces to power our equipment and to heat our buildings. We see organic growth as being the main growth driver with our focus on Indian and eastern European markets delivering significant growth for the future. Our automotive business has seen little slowdown which is normally associated with that particular market, we are currently working with Aston Martin cars to produce torque and transmission components, as well as with other Niche car manufacturers.
“There is a distinct trend to move away from steel to aluminium, and we have seen examples of this in our work with the aerospace industry where we are working closely with Individual clients from our facility in Poland. We are located very close to a high-tech industrial area known as ‘Aerospace Valley’. We are convinced that aluminium castings have major future potential as in many cases welded steel and cast-iron castings can be replaced with aluminium castings that offer a significant advantage. These include corrosion resistance, low weight, high thermal conductivity, ease of machining and low stress. What’s more, aluminium is fully recyclable.”
Serving diverse global markets
Thoni-Alutec’s portfolio demonstrates the company’s achievements in the area of light aluminium casting. Its international customers in various industries regard the company as a high-performance and reliable partner. Its clients in the USA, China and India are testimony to the high level of service and the precision products that the company provides. Thoni-Alutec works in close partnership with all its customers whose original innovative ideas it supports with enthusiasm and with its cutting-edge expertise.
The company’s design engineers are experienced in successfully converting manufactur-
ing processes and materials, and can support a client from the initial concept stage through to full serial production. Thoni-Alutec’s design offices will also convert any new development into a lean and production-friendly design, while taking into account the entire production value chain process. Furthermore, the full integration of all design and production processes in-house provides customers with the shortest possible delivery times, and guarantees the highest levels of service and product quality.
The company’s broad spectrum of activities serves an equally diverse range of markets, which includes robotics, medical, energy, railway, mechanical engineering and engine technology, as well as aerospace, defence, marine and the automotive industries. n
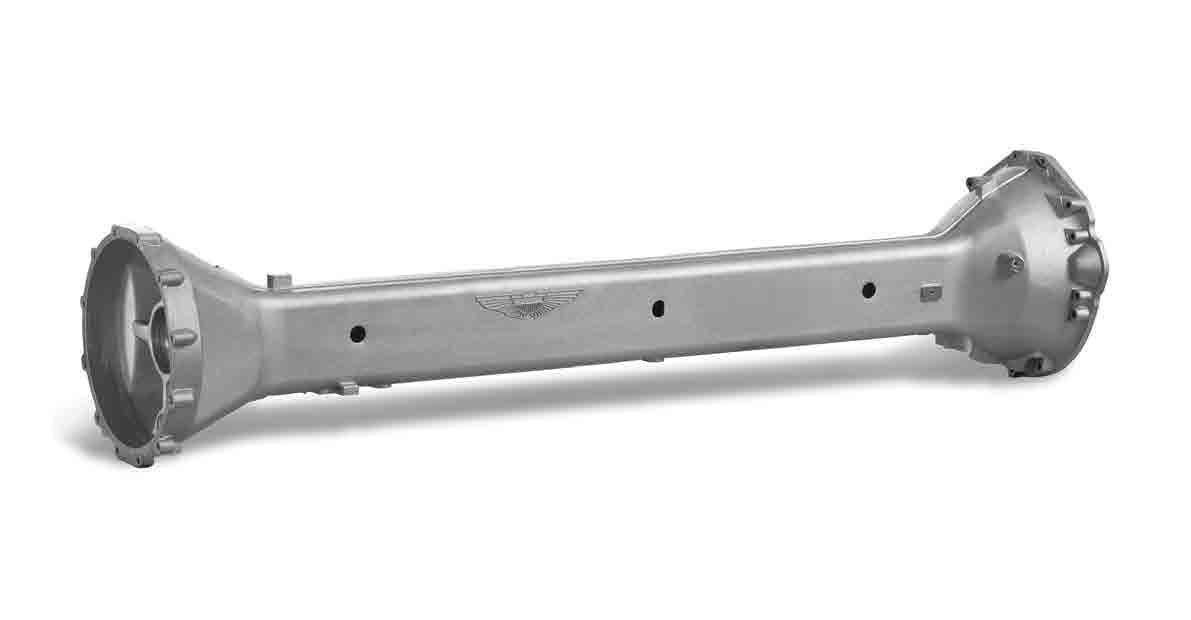
For further information about ThoniAlutec’s high-precision products and services visit: www.thoni-alutec.pl
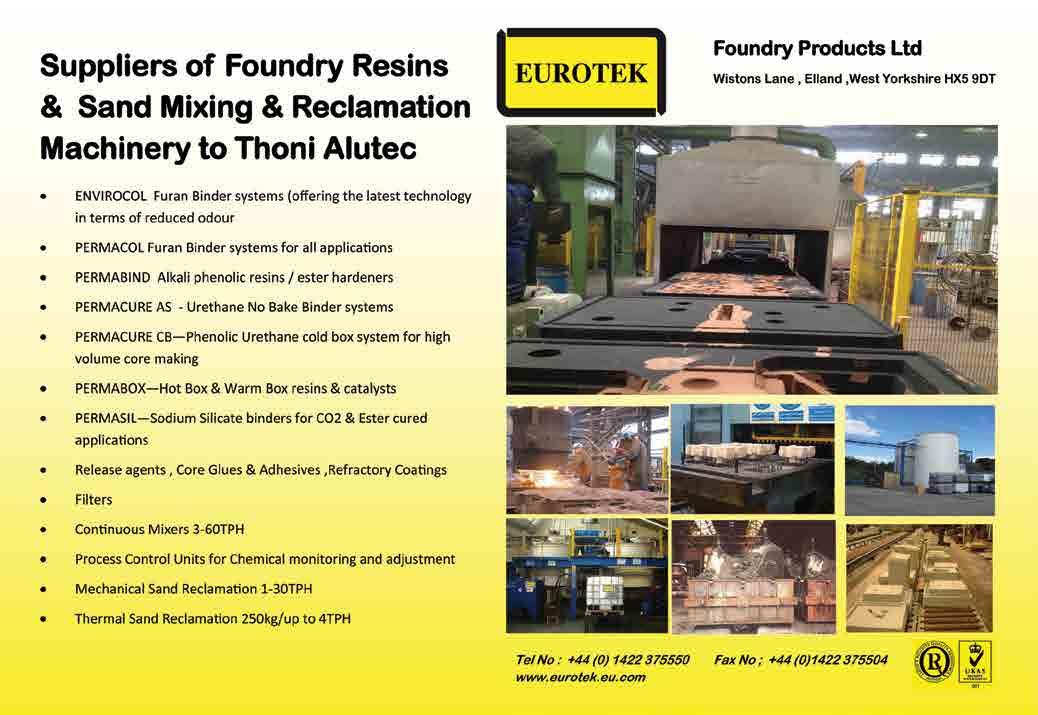