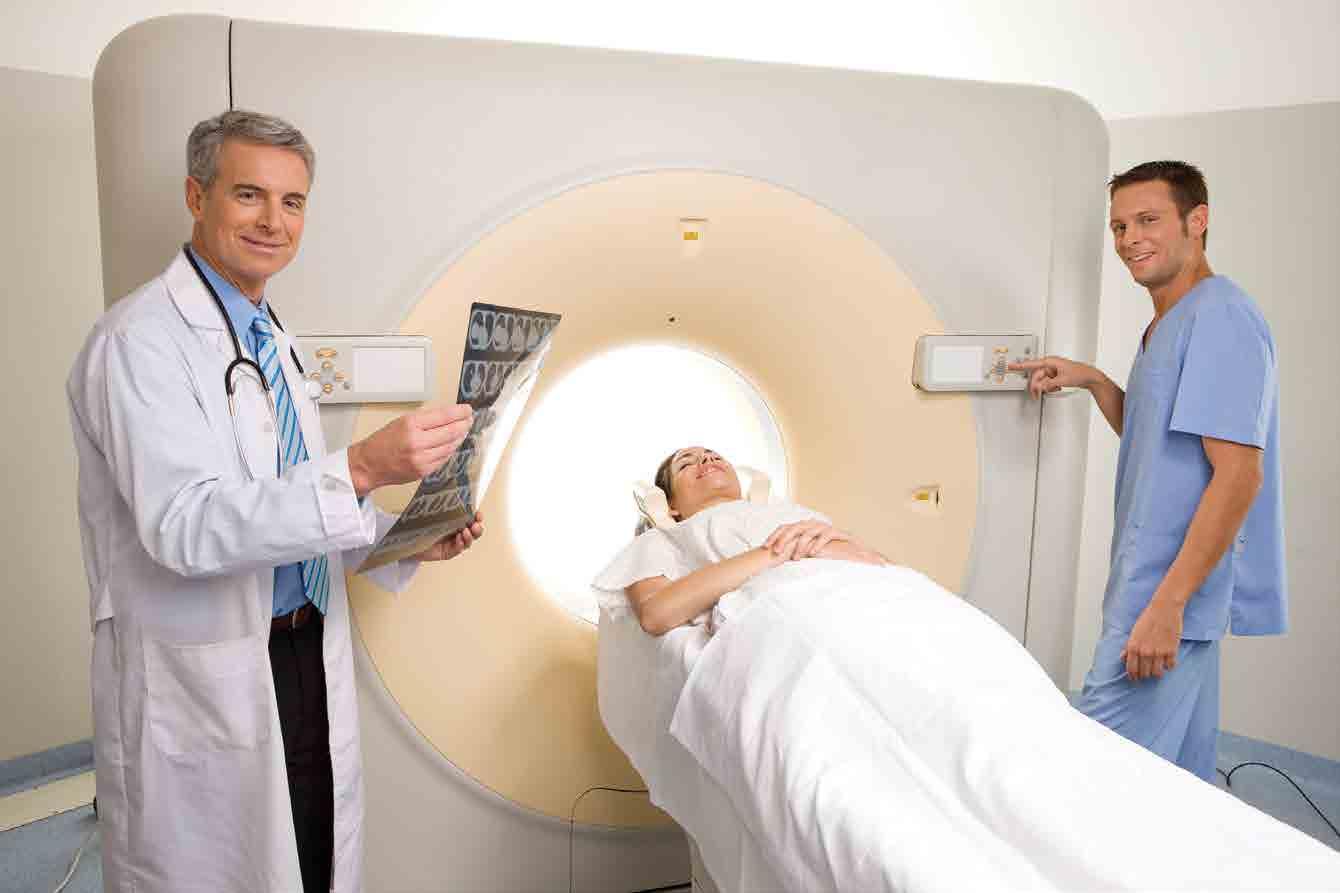
6 minute read
Special steels – a new dimension ABS

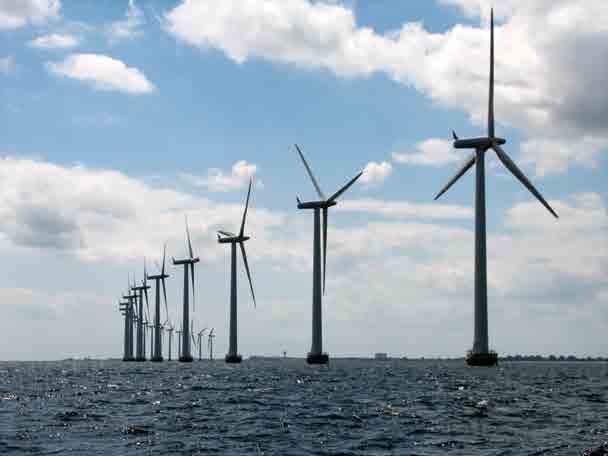
ing all the tasks that are labour-intensive to minimise our production costs and maintain our competitive edge.”
“We are market leaders in monorail roller technology especially in Germany and Japan and our latest feedback system is also unique in monorail systems technology. Mechatronics application technology is another area where we lead the field and this is all part of our drive towards providing more integrated business systems. Today our semiconductor business remains our biggest business sector and represents 75 per cent of sales, with industry, life sciences and others making up the balance”.
Mr Fuscher added, “In terms of our geographical reach, Asia remains our main target market when it comes to our future growth prospects. This region is currently contributing 40 per cent to our revenues with Europe providing around 50 per cent and North America representing approximately 10 per cent. We can see what the world economy is telling us and we believe that India will surpass China when it comes to growth potential over the next few years. Our future drivers for growth will clearly be the Asian markets, as well as our new technology offerings in mechatronics, the Minirail commodity markets and our lowcost production technology.”
Extending the boundaries of linear technology
Positioning systems used in particularly demanding branches of industry such as semiconductor technology, medical engineering, and solar technology must guarantee the highest level of precision and reliability while maintaining an extremely high degree of cleanliness. Schneeberger Linear Technology is able to meet these requirements effectively by providing customer-specific solutions. This is possible thanks to the investments made in its new clean room designed specifically for the production of these systems in accordance with ISO 14446 Class 6. This clean room is used exclusively for the production of positioning systems which must meet the most stringent cleanliness requirements.
If extremely high accuracy is consistently required in the most compact spaces, the Schneeberger MINIRAIL is the number-one option. MINIRAIL guideways always ensure that linear movements are carried out extremely quickly and precisely. Preferred
areas of application include the semiconductor microelectronics, medical, measuring, laser and nanotechnology industries. Eight rail widths and four carriage lengths are also available.
The user can choose between two accuracy and preload classes. At the other end of the scale, Schneeberger’s Gear racks allow linear movements to be carried out along almost limitless stretches. In this regard, they are well-suited for use in large machines and systems in which enormous axial forces must be transferred. Even dirty working environments do not present a problem. Schneeberger provides cost-efficient solutions for all applications.
The uses for Schneeberger gear racks in practice are just as multifaceted as the product range. Their use in standard machine tools operating in dirty working environments, for example, is equally as common as their application in precision measuring machines. n
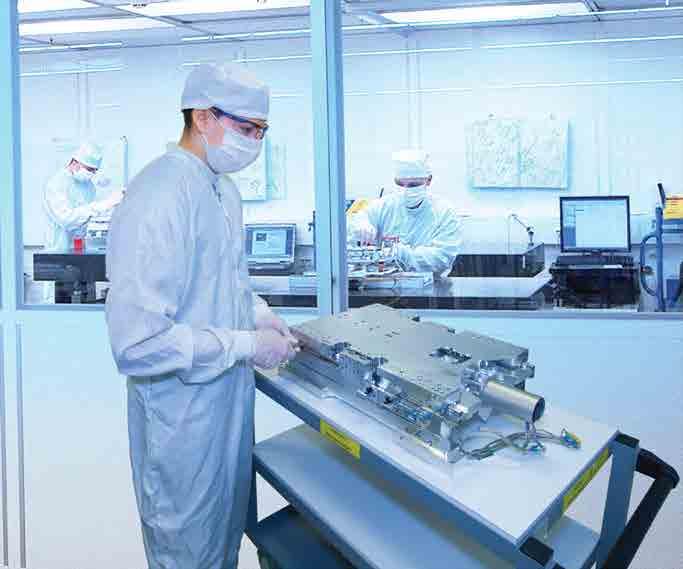
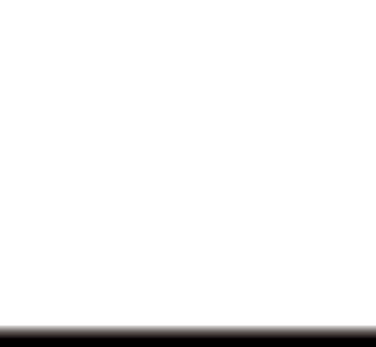
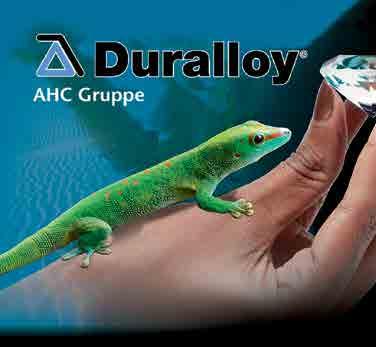
DURALLOY® more than only coatings
Duralloy is a specialist and leading manufacturer in the area of thin dense/structural chromium coating technology. Duralloy offers individual solutions for functional plating needs in different industries like the automotive sector, industrial gears, machine tools, textile machines, printing machines, hydraulics, medical technology, bearing technology and linear guide rails.

Linear systems are typical applications of Duralloy
Germany
Duralloy Süd GmbH Eckweg 6, D - 78048 Villingen-Schwenningen Sales service: Helmut Grotenrath Phone: +49 (0) 7721 40444-10 E-mail: contact@duralloy.info Fax: +49 (0) 7721 40444-29 www.duralloy.info Switzerland
Duralloy AG Schweiz Industriepark Altgraben, CH-4624 Härkingen Sales service: Albert Rölli Phone: +41 (0) 62 3888000 E-mail: admin@duralloy.ch Fax: +41 (0) 62 3888008 www.duralloy.ch Great Britain
Acorn Surface Technology Ltd. Clover Street - Kirkby in Ashfield, UK - Nottinghamshire NG17 7LJ Sales service: David Cox Phone: +44 (0) 1623 753107 E-mail: information@acornst.com Fax: +44 (0) 1623 754538 www.acornst.com
SPECIAL STEELS - A NEW DIMENSION
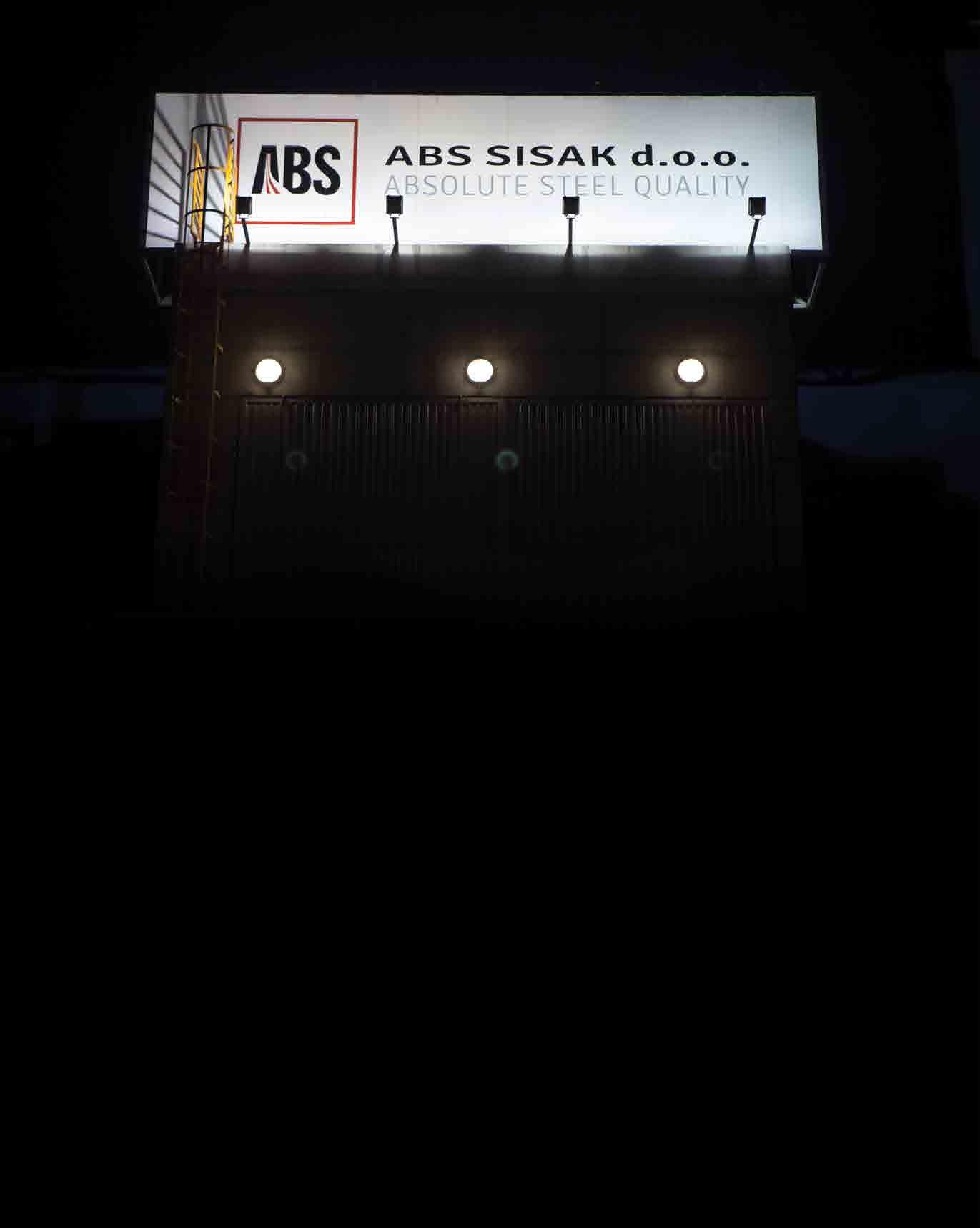
ABS is a global leader in the development and manufacture of special steels. Philip Yorke talked to Andrea Landini, the CEO of ABS Sisak d.o.o. about its latest innovative products, its ongoing investments in new plant and its recent move into the Croatian market.
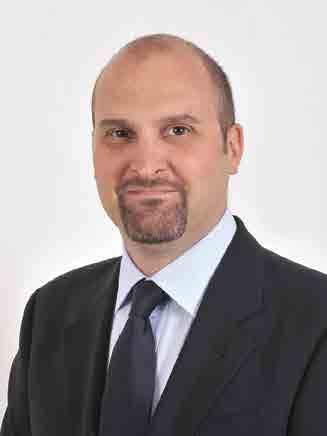
The roots of ABS can be traced back to 1813 when the first water-powered forge was established in Udine, Italy. The company’s initial iron-processing plant was originally dedicated to the production of agricultural equipment and was later expanded to cater for the manufacture of industrial steel products. Its early successes resulted in its ability to invest in a programme of constant improvement and technological advancement. ABS subsequently integrated these new processes resulting in the construction of a new foundry and steel mill, as well as new rolling mills, heat treatment plants and cold-finishing facilities.
The ABS brand itself was established in 1988, following the merger of two of Italy’s most successful and long-established steelmaking companies: Officine Bertoli, founded in 1813 and Safau, established in 1934. In June 2012 ABS acquired a leading steel producer in Croatia, which is the only ‘melt-shop’ in the country and which provides a major foothold in the Balkans for ABS. Together with the considerable resources and know-how of the Danieli Group, ABS’s parent company, the Croatian operation can guarantee its customers unparalleled quality and service, backed up by steel products that are designed to meet the most demanding industrial challenges.
As a major European steel producer, ABS is one of the oldest and best qualified businesses in the industry, and its continuous product research and process technology innovation has enabled it to achieve a leadership position in the field of speciality steels. Today ABS delivers exceptional steel products of any dimension to a broad range of indus-
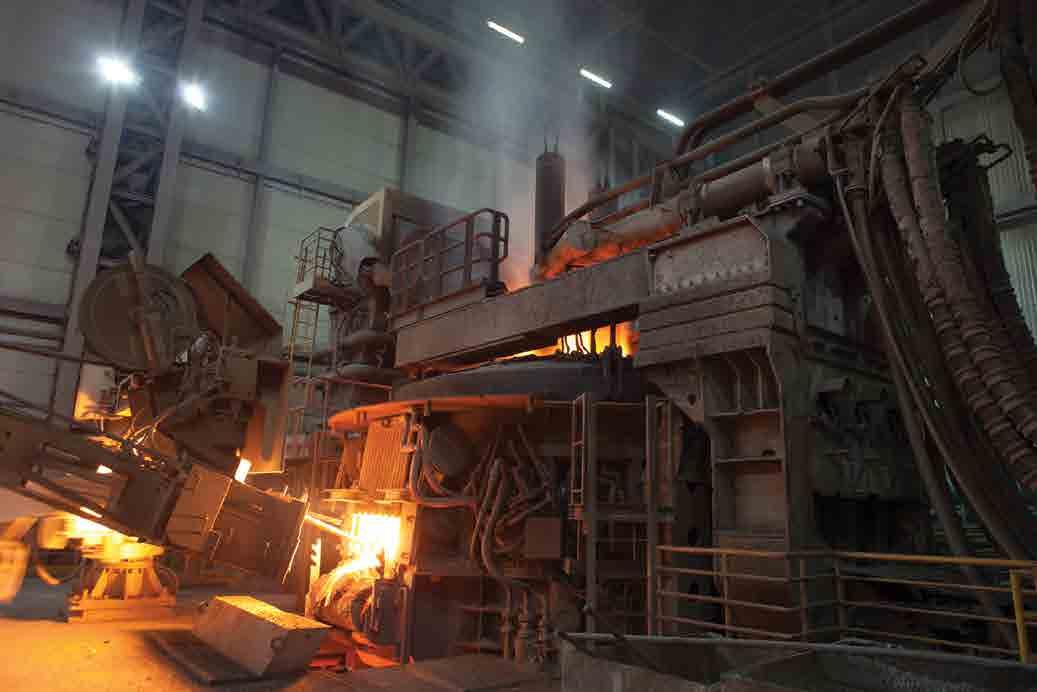

tries. These include companies involved in the manufacture of automotive products, trucks, earth-moving equipment, wind turbines and railway structures as well as military vehicles and oil and gas plants. This is in addition to those involved in nuclear power, agricultural equipment and industrial vehicles.
Product and process innovation driving sales
For ABS, the establishment of its modern research centre in Metz, France, the ABS Centre Métallurgique or ACM, demonstrates its solid commitment to product and process innovation. The on-going and close collaboration between ACM and its customers is a fundamental resource for the identification of innovative processes and products that are designed to meet the most demanding requirements of its big OEM customers. The company’s highly qualified and experienced R&D team also works closely with leading European universities and other major research centres.
Mr Landini said, “We specialise in the manufacture of low-carbon and mediumcarbon steels and are able to achieve exceptionally high purity thanks to our hightech processes and advanced technology. Our biggest customers come from the oil and gas industries where consistent, high quality steel is essential for their hazardous operations and where extreme conditions and pressures prevail.
“As the only major producer of special steels in Croatia we need to remain ‘lean’ and to maintain the high standards that ABS is well known for worldwide.
“We expect to reach our target output of 300,000 tonnes per year of high quality steel within the next two years. In Croatia we currently employ around 150 people and step by