
6 minute read
Continuous expansion for logistics leader
Ahlstrom has four key business areas, Advanced Filtration, Building and Energy, Food and Medical and Transportation Filtration all offering value added fibre-based materials to their customers. It enjoys a wide customer base; none of Ahlstrom’s customers have a dominating position, with its ten biggest customers constituting just 20 per cent of net sales. This gives the company a very strong, well-balanced position across market segments and has proved to be a profitable strategy during the economic downturn.
In 2012, Ahlstrom employed over 5000 people worldwide and its net sales amounted to approximately €1.6 billion. This year after the Label and Processing business area demerger the sales are some €1 billion with over 3800 employees. With operations in more than 20 countries on six continents, it truly is a worldwide company. Green and global
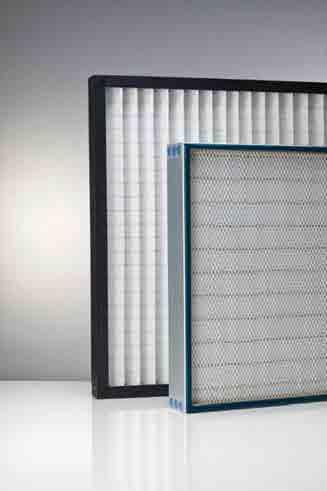
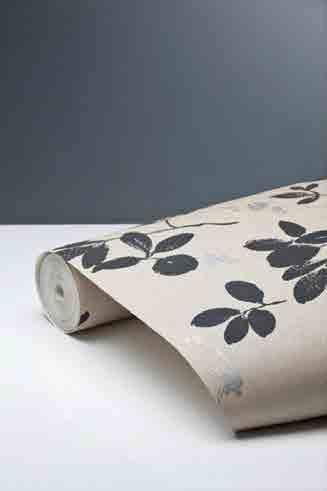
Recognising the global megatrends of environmental awareness, resource scarcity and demographics and urbanisation, its unique expertise in fibres, chemistry and materials technology enable Ahlstrom to create products with sustainability as a driver. Vice-president for sustainability, Anna Wessman, is dedicated to ensuring that the whole company works in as responsible a manner as possible, for the benefit of the environment, the business and its people, both employees and customers. Ms Wessman spoke to Industry Europe about how this is being achieved. She said, “We have a leading market position in all the sectors where we are active and we have been established for over 160 years. With sustainability in mind, we make products that protect people, purify air and liquids and provide surface and structure to our customers’ products. As all human activity has an impact on the environment, we only want to make products with purpose, such that are truly needed by people. With them we help our customers to achieve their own sustainability goals.”
Economic responsibility at Ahlstrom is characterised by its responsible business conduct. As a company, it observes the law of the host country, offers local job opportunities, pays local and national taxes and brings prosperity to the region. Ahlstrom’s social responsibility is also a natural part of how the company operates, with safety, taking care of employees and offering excellent training and personal development all central issues. Furthermore, the products with purpose are made in order to have a favourable social impact.
Environmental responsibility is certainly an area where Ahlstrom shines. Passionate about both finding innovative ways to enhance
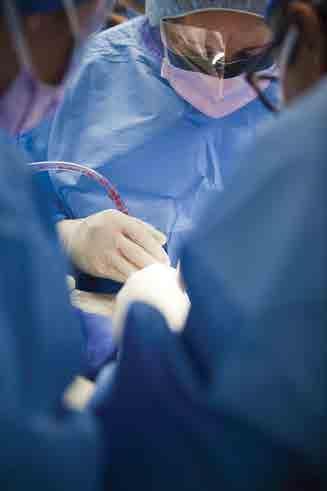
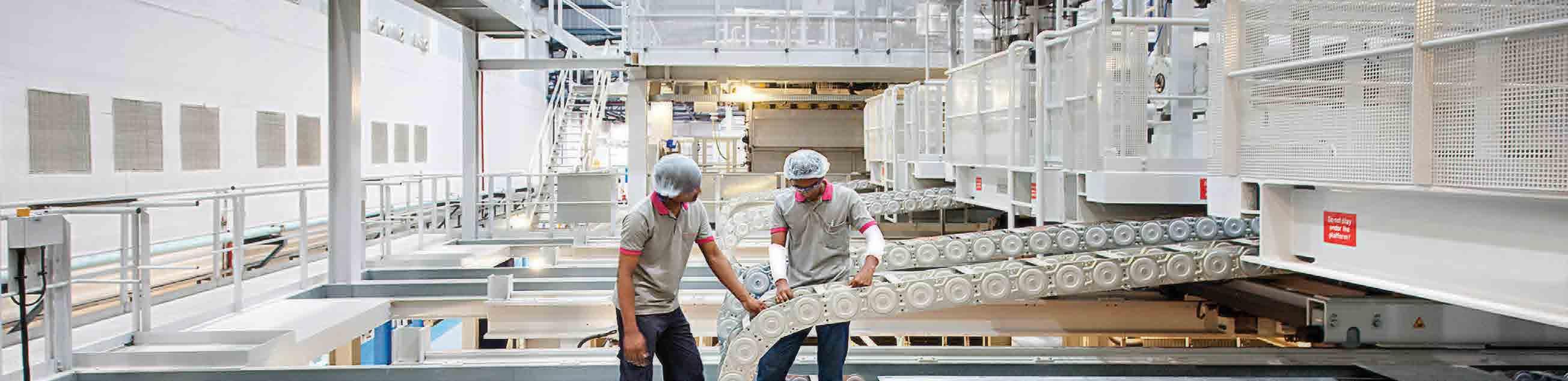
• Rygene-Smith & Thommesen is a Termomechanical pulp mill established in 1883 • Capacity approx 40.000 ton TMP on a 3 shift system • Freeness from 100 LWC up to 400 CFS • Brightness up to ISO 68 • Certified according to PEFC and FSC standard • Located in southern Norway
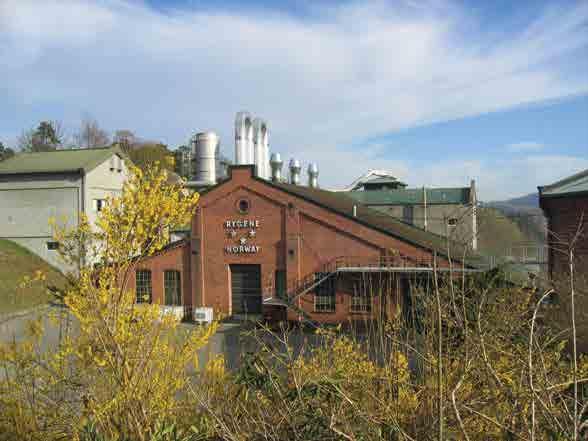
www.rygene.no
its green performance and to minimise the environmental impact of its operations, Ahlstrom’s focus is throughout its entire process. Ms Wessman continued, “Our environmental responsibility programme starts in product development where 80 per cent of the environmental impacts of products are determined. We are committed to EcoDesign. All our plants are environmentally certified. We only buy pulp from companies that are certified, so that we can guarantee that the whole of our value chain is committed to sustainability too.”
Identifying excellence
Ahlstrom has identified five key performance indicators that support its sustainability programme and reflect its targets with regard to reduced environmental impact. Water intake, electrical efficiency, fuel energy, waste to landfill and CO2 emissions are all major areas of importance, with each area given substantial concentration. Ms Wessman pointed out, “We have set ourselves a zero waste to landfill target to be achieved by 2015.”
With 91 per cent of its fibre raw materials coming from renewable sources in 2012 and all its wood fibre suppliers having thirdparty certification in their forests, responsible sourcing and knowing the origin of the fibres is an important issue.
Ahlstrom’s vision is to be inspiring people, passionate about new ideas and growing with customers. Ms Wessman added, “We are continually driven to create sustainable and profitable relationships with our customers. By offering competitively priced, value added products to our customers across the world we will continue to grow and succeed. As all of our products are developed and manufactured in as sustainable a manner as possible, our customers can work with us safe in the knowledge that we can positively contribute to their own sustainability aims and help them stay ahead.” n
Lenzing
Lenzing is the global market leader and expert in the production of man-made cellulose fibers benefiting from 75 years of experience in fiber production. The renewable raw material wood is the basis for Lenzing fibers. The choice of TENCEL® and Lenzing Viscose® combines enhanced performance, comfort and environmental responsibility from the outset. Lenzing is dedicated to continuous development of fiber properties and ecological sustainability is a specific target in all innovation efforts. Wolfgang Plasser, VP Nonwoven Fibers, comments: “It is our aim to create value for our customers by focusing on consistent quality, innovation, reliable partnerships and sustainability achieved through long-term thinking.”
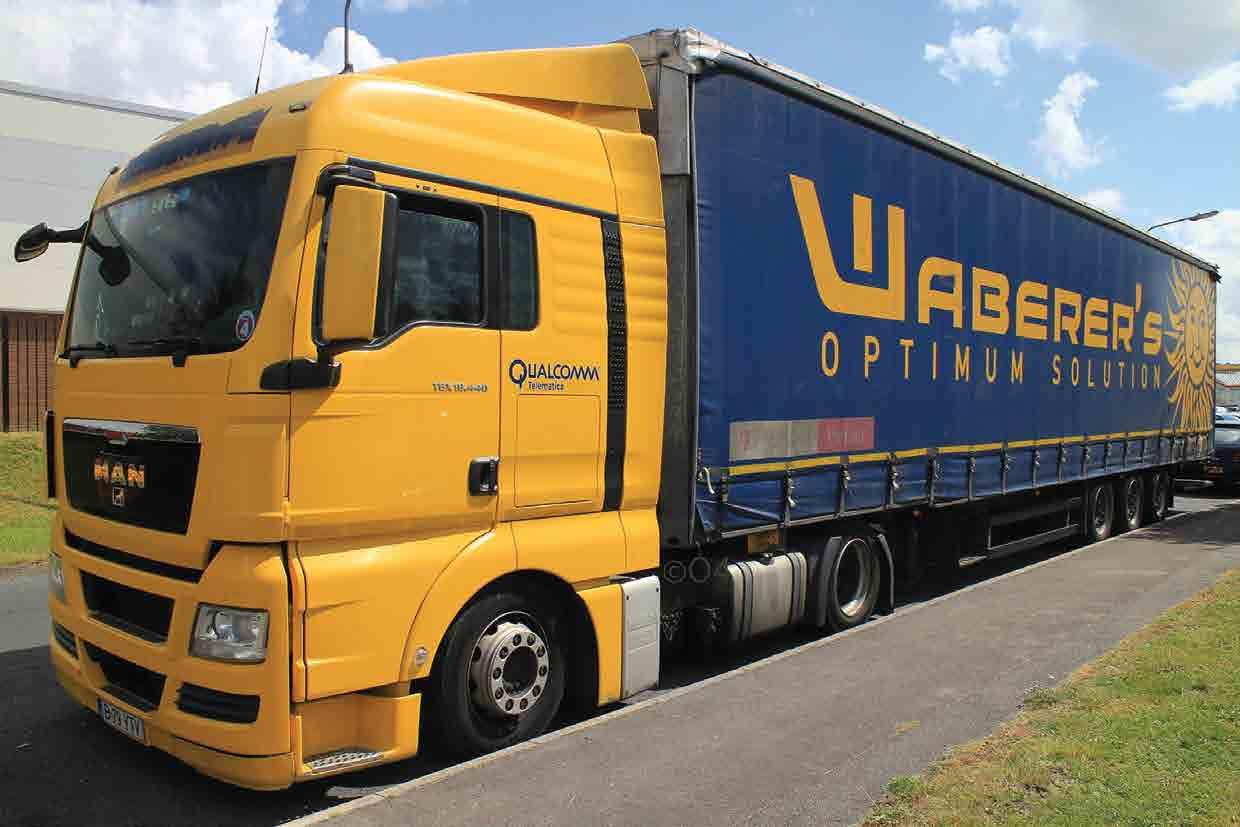
CONTINUOUS EXPANSION FOR LOGISTICS LEADER
Hungarian transport logistics group Waberer’s Holding Zrt is the market-leading logistics service provider in Hungary and central eastern Europe. The companies within the group provide a global range of logistics services and it constantly expands its fleet to meet increasing demands. Industry Europe looks at its activities.
Road transportation is the simplest and most secure form of logistics; however, without flexibility and efficiency a company cannot succeed in this industry. In order to provide more flexible customer service and to improve operational efficiency, in 2010, Waberer’s changed its company structure and shared out the majority of its fleet of 2300 vehicles to smaller individual enterprises holding 60–100 trucks each.
As the company reacts quickly to changing market needs, the most advanced information technology systems and tools have also been implemented to run the new type of operations efficiently. Whilst the mediumsized companies operate as individual enterprises, they are still backed up by the holding’s incredible financial power and provided with the support of its international business network system.
The year 2012 marked another chance for Waberer’s when four companies within the Group – Waberer’s International Pte. Co., Delta Sped Ltd, Interszerviz Ltd and Inforatio Ltd – merged with Waberer’s Holding, thereby becoming Waberer’s International Pte. Co.
In 2013, the Hungarian Competition Authority approved the merger of Waberer’s Logistics Ltd and Szemerey Transport Inc. The companies will continue to operate under a common ownership structure led by a unified management. They are respectively Hungary’s leading logistics enterprise and the market leader in domestic refrigerated freight and distribution. Their combined logistics fleet, now under unified management, is able to satisfy all logistical needs related to refrigerated, fresh and dry goods to the highest standards.
Company history
Established in 1948, Waberer’s predecessor Volan was previously a state-owned road cargo transportation company which was privatised in 1994 by entrepreneur György Wáberer and his associates. As a result of the turnaround strategy implemented by the new management in 1994, the company established new foundations and began a series of acquisitions to extend its product and service portfolio. In 2001 the company partnered with MAV (Hungarian State Railways) and began to develop the BILK (Budapest Intermodal Logistics Centre), central Europe’s largest forwarding and logistics centre. As a result of the acquisition of Hungarocamion Co. in 2002, the company became a market leader in Hungary and gained a significant presence in eastern and central Europe. In 2003 the company was once again restructured, changing its name to Waberer’s and introducing its unique customer service system, Waberer’s Optimum Solution.
In 2005 the company began its regional expansion by establishing subsidiaries in Slovakia, Poland, Romania and Spain. Today Waberer’s Holding is the sixth largest road haulage company in Europe, offering a wide
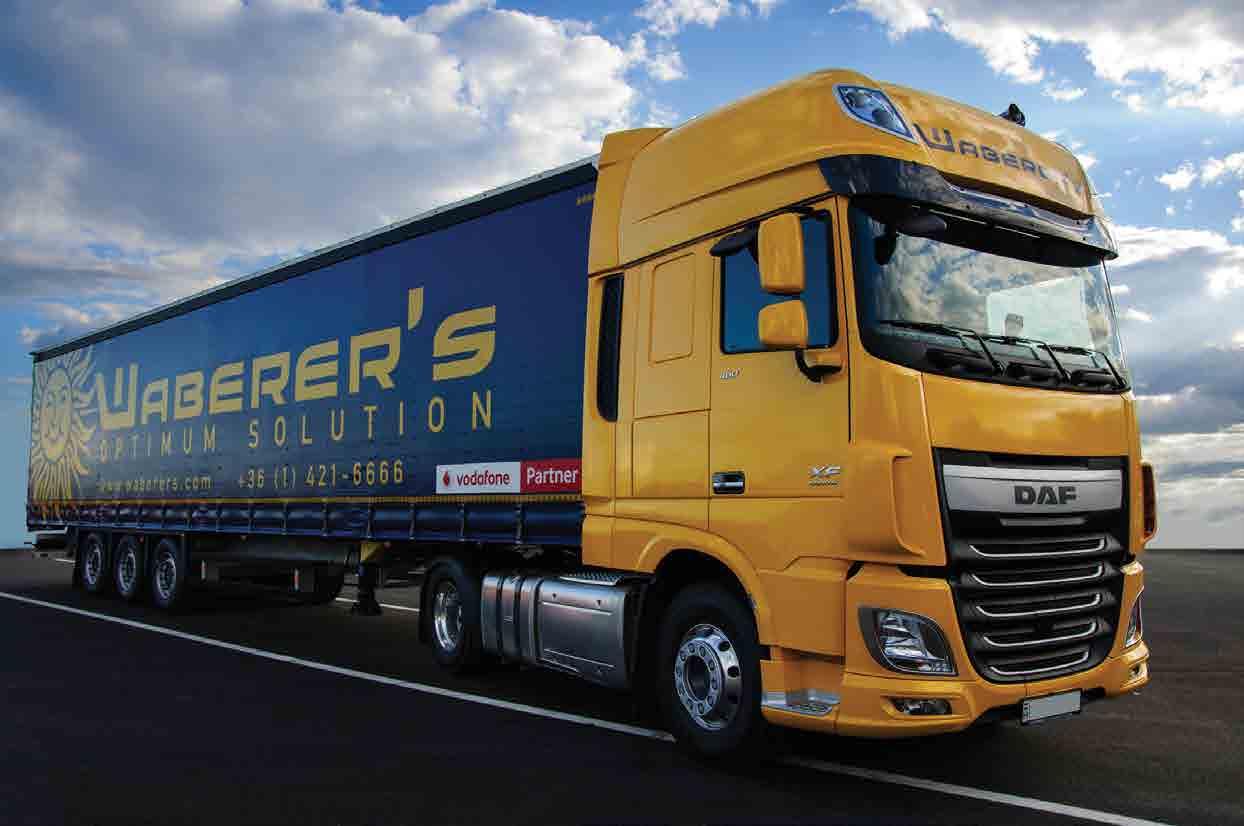

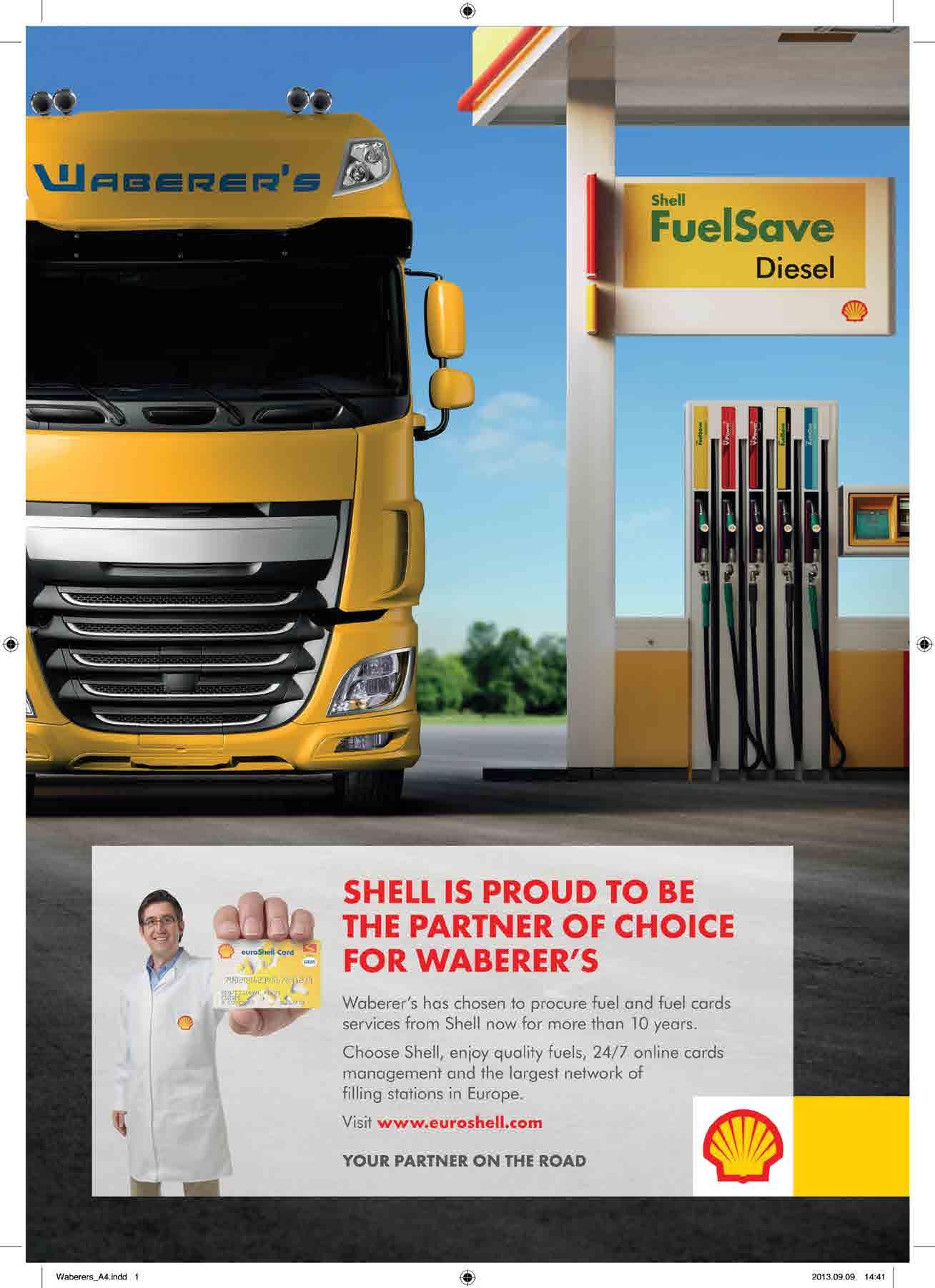