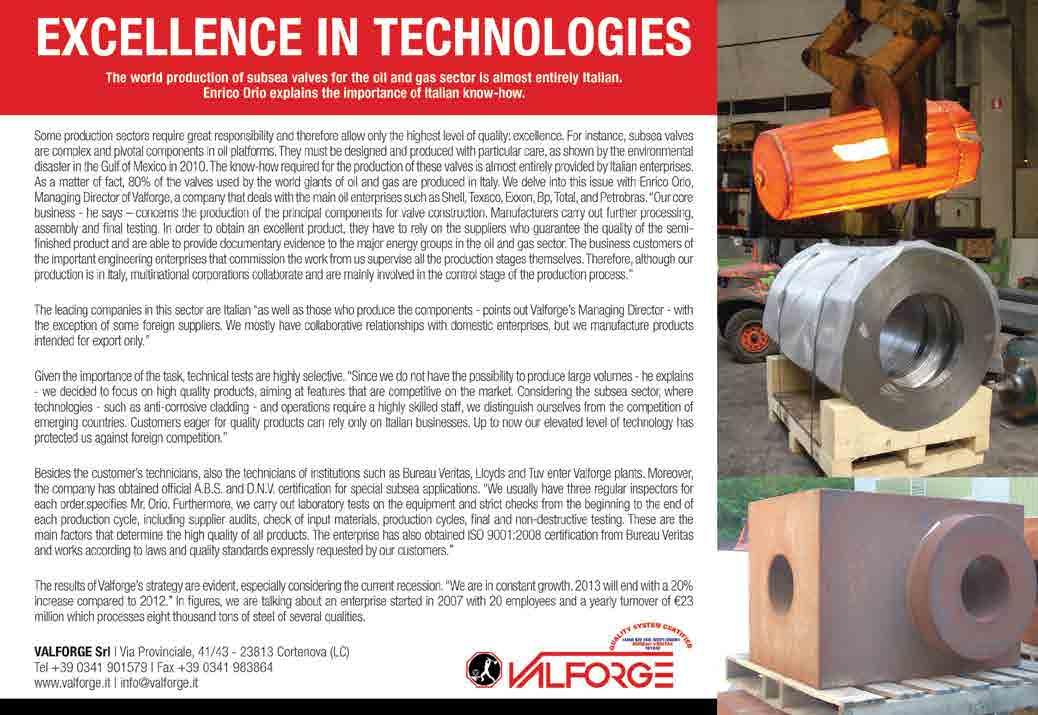
7 minute read
Powering ahead Riello Elettronica
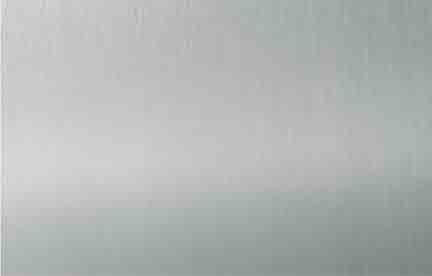
An ISO 9001:2008 certified foundry supporting the requirements of Annex I, chapt. 4.3 of Pressure Equipment Directive (PED) 97/23/EC.
Sand Castings in Stainless Steel, Duplex, Superduplex and Nickel Base alloys up to 5 tons.
Norsok Standard M-650 for: ASTM A890/A995 grade 4A UNS J92205 ASTM A890/A995 grade 5A UNS J93404 ASTM A890/A995 grade 6A UNS J93380 ASTM A494 grade CW6-MC Inconel 625 ASTM A351 grade CK3MCuN
Advanced casting simulation software 6 tons AOD refining system Surveyed Heat Treatment Furnaces

Via delle industrie 23 – 30020 Marcon (VENEZIA) Tel: +39 041 4567644 • Fax: +39 041 4569570 E-mail: info@facesspa.it • www.faces.it
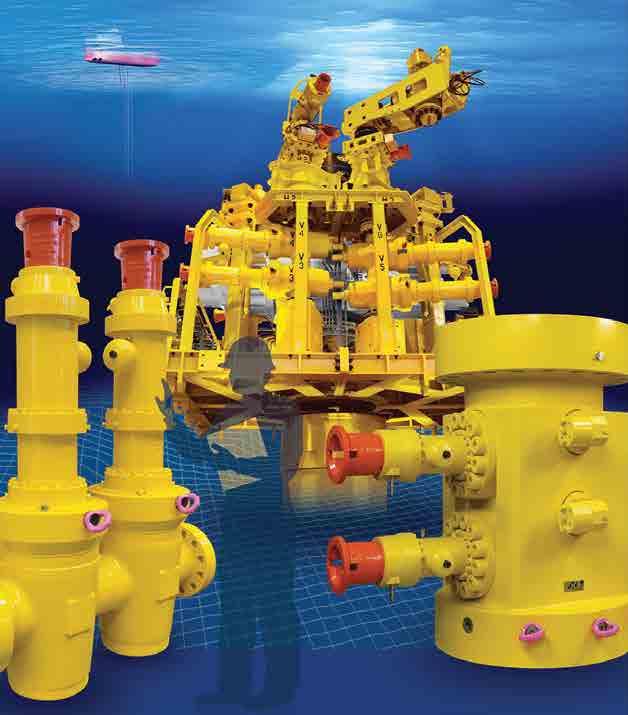
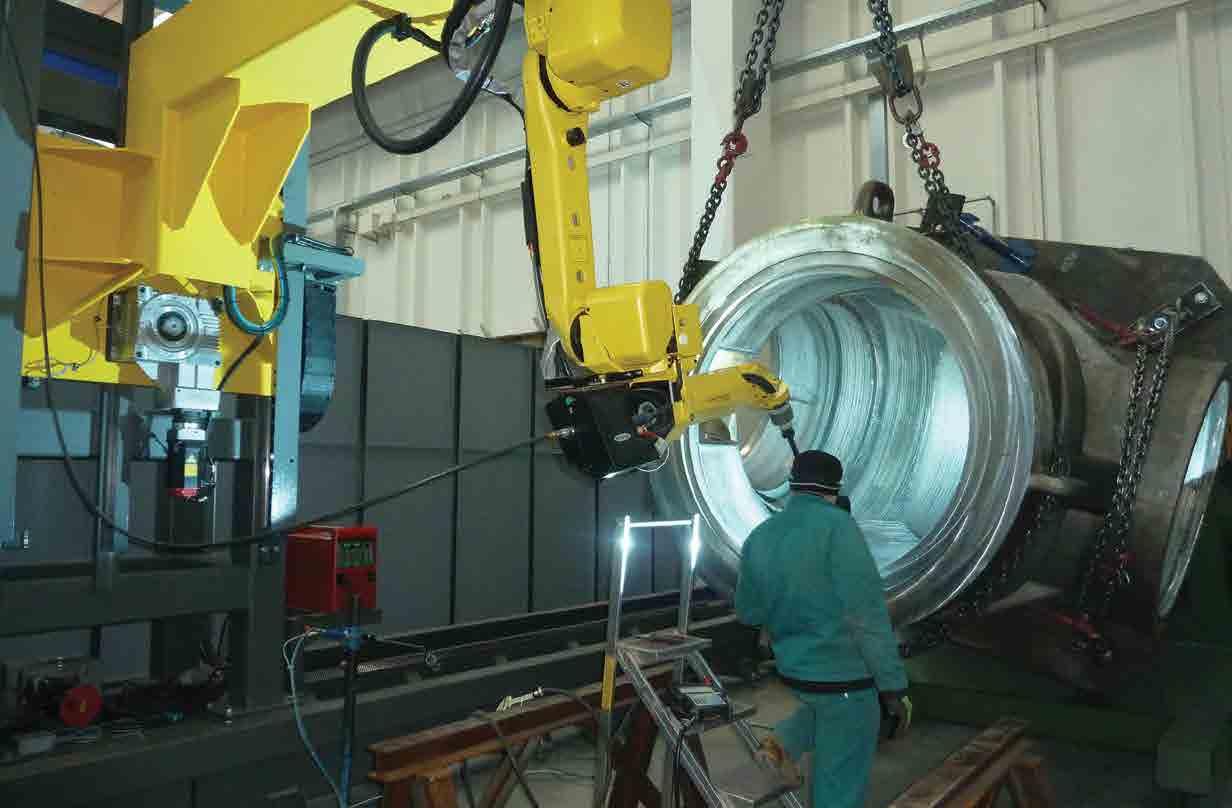
shore installations in the North Sea, south-east Asia, western and southern Africa, Brazil and Australia. They are in high demand, as they are necessary for the safety systems which, after the Gulf of Mexico accident, are required to be located very close to the actual drilling facilities. In fact, 99.9 per cent of our turnover is generated from export.”
Unique testing facility
As mentioned ATV’s valves are used at subsea depths of up to 3000 metres and, in order to test them under the actual pressure and temperature existing at 4500 metres under the sea, ATV has developed and constructed its own hyperbaric chamber, the most advanced of its sector. This is the only hyperbaric chamber of large dimensions – it weighs 200 tonnes when empty – working at a pressure of 450 atmospheres. Similar facilities exist in other countries, but for lower pressures only. The company’s hyperbaric chamber is used by third parties for the testing of their own products, which although related to the subsea industry, are not valves. When working with his previous company Mr Sanguineti also collaborated with universities and he pointed out how this chamber has the additional potential to be employed for the development of defence sector products.
The growth experienced in recent years – in the last 12 months almost one hundred people have been taken on, mainly young staff – is expected to continue. Having the right kind of products is at the basis of this success. “We do not carry out research as such, which is something best done by universities and research institutes, whose collaboration we sometimes seek for the resolution of issues, but we continuously carry out product development, often involving the resolution of issues concerning other areas, such as welding or metallurgy. Often the stimulus for this comes from the market. If a client wants to develop its work in a high temperature or high pressure environment, we have to develop suitable safety valves for it. Our products comply with international standards, but then they have to be adapted to clients’ needs, as each project is unique. We always accept a challenge and invest up to 4 per cent of turnover in innovation This percentage varies from year to year, but for instance we invested a lot in the difficult years (2008–2009) so as to be ready for better times. We are currently working on products which clients will need in 12 to 18 months. Sometimes clients contribute financially to product development.”
Production takes place at the company’s sole site in Colico, for which three latest generation machines have recently been acquired. One of these was installed at the end of July 2013, one at the end of October whilst the last is due to be installed around next March–April. This substantial investment has been carried out to make this production unit even more efficient. This site includes an outstanding welding department. All production phases, from welding and assembly to mechanical processing and testing, are carried out in-house, as they are critical in terms of quality of final products.
Demand from the offshore subsea sector is expected to continue. As well as continuing to operate in all the geographical markets currently served, the company has started being active in China. Important development in the near future is expected in the Middle East – thanks to oil fields in the Red Sea – and in the Arctic region. Future growth is expected to take place through organic expansion and the set target is that of achieving a €100 million turnover within five years. “This is our plan, as long as no major macroeconomic events disrupt the global picture. Who, at the beginning of 2008, predicted what happened later that same year?
“We have excellent partners, in term of suppliers, who can offer us very high quality. We work with companies of the calibre of Valforge, Foc Ciscato, Lucchini and Praxair. Whenever possible we favour forging for subsea products, rather than casting. Italy, where 99 per cent of our suppliers are based, is particularly strong in this field, offering high quality. We employ casting for only 10 per cent of products, as forging can offer us higher safety and quality levels.” n
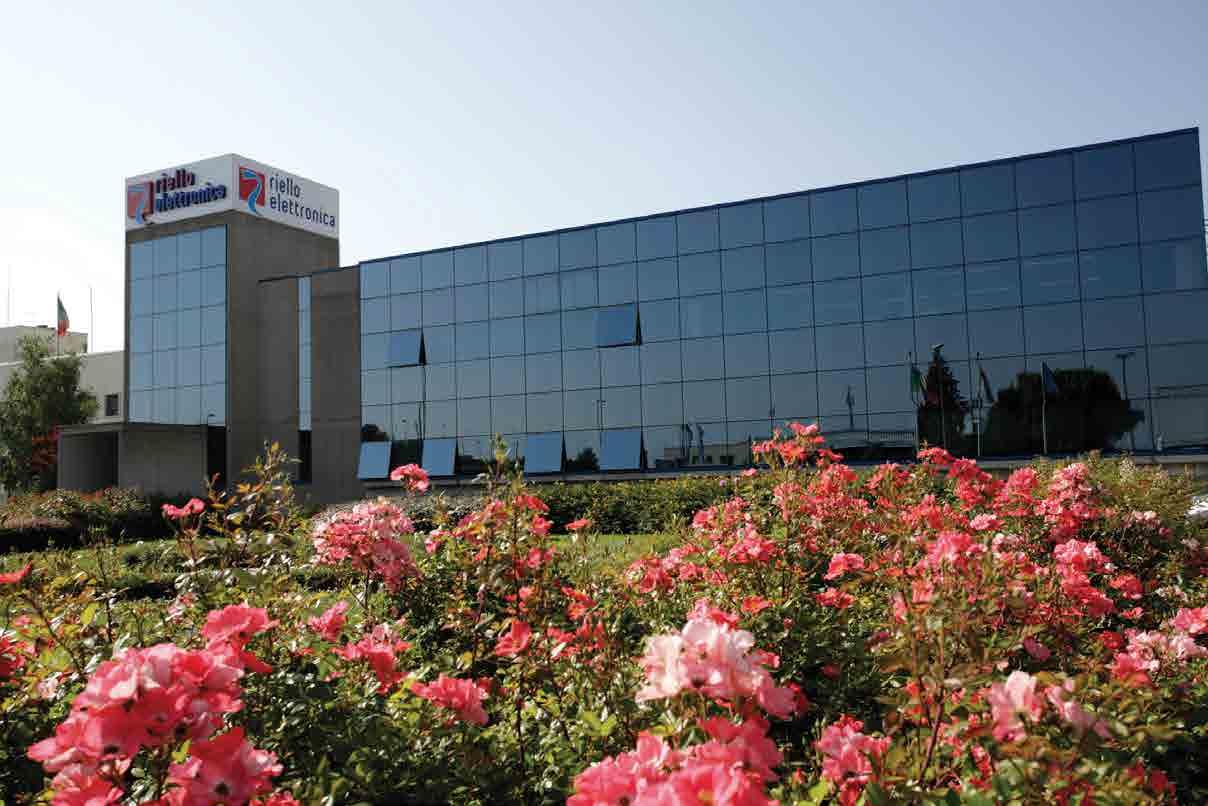
POWERING AHEAD
In just 25 years Riello Elettronica SpA has developed a wide range of energy products. Its expertise in UPS (uninterruptible power supplies) has attracted hundreds of prestigious clients and established it as a market leader at the global level. Barbara Rossi speaks to Mr Buscherini, the marketing director of Riello UPS.
Master HP Series Riello Elettronica SpA operates in the energy market, as well as in the automation and security device sector. For the latter it produces automatic gates and alarms, as well as home automation devices, among other products, through brands such as CEMU, Cardin and AVS. Riello Elettronica SpA operates in the energy market through two brands: Riello UPS and Aros Solar Technology. As is obvious from the name, the former is focused on uninterruptible power supplies while the latter manufactures solar technology inverters. The energy sector accounts for about 75 per cent of Riello Elettronica SpA’s turnover, and approximately 90 per cent of the energy turnover is generated by the Riello UPS brand.
Thanks to the progress made in the 25 years since its establishment, today Riello UPS ranks as number one in Italy, number three in Europe and is in fourth position at the global level (according to IMS research institute). The company offers a wide choice of UPSs ranging from 400VA to 6.4MVA, thus offering a complete portfolio of solutions. The wide range of markets served include the financial, IT, telecommunications, retail, hotel, transportation, public and health industries, as well as the sport and leisure, military, industrial, energy, government and education sectors.
Mr Buscherini explains, “Two products which stand out in our offer are the Multi Sentry and the Master HP. They have both been on the market for a few years and offer an exceptional performance in terms of efficiency and reliability. We produce thousands of these products each year and they are
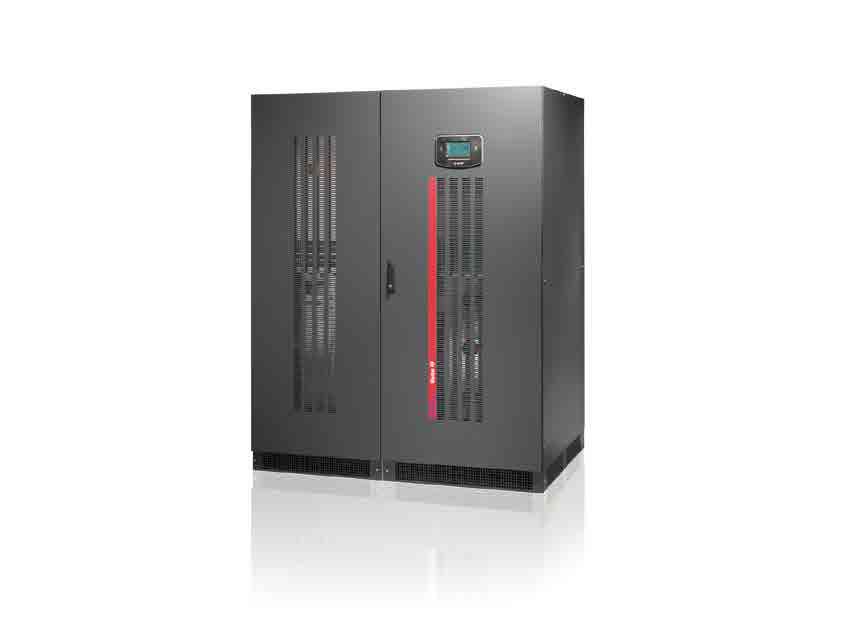

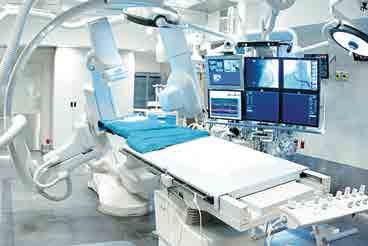
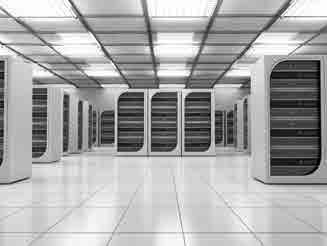
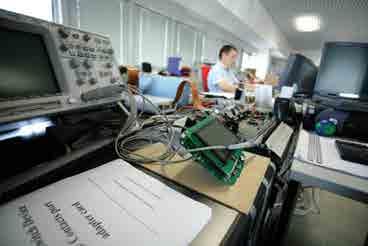
used by clients all over the world. The Multi Sentry is a transformerless state-of-the-art uninterruptible power supply with a TUV certified high efficiency level -exceeding 96 per cent – a world record. “The Master HP series also features very high efficiency (exceeding 95 per cent). It has an insulating exit transformer, with ensuing high levels of reliability and sturdiness. It is an extremely compact and versatile product with transformer, which has been chosen by ENI (one of the largest integrated energy companies in the world) to be used in their brand-new green data centre (ENI Green Data Centre) under construction in the Pavia area, which will be the largest in Europe and whose target will be that of having a PUE (power user effectiveness) lower than 1.2”
New products are continuously being developed, as innovation is one of the missions of the company. “We have many new projects in the pipeline: just two examples, we are currently developing a new transformer-less series of over 120kVA and a high concentration modular UPS for the data centre sector.”
The company is responsible for its products from the design right through to the commercialisation phase, including their development and production. All research and development is conducted internally, and both sites, based in the Verona (Legnago) and Milan (Cormano) areas, are equipped with R&D laboratories, as well as being engaged in production. A very high share of turnover is channelled into research and innovation. Truly made in Italy
Mr Buscherini adds, “We offer a truly ‘Made in Italy’ range, as all our products over 3kVA are produced in the country. Each of our two sites has a specialism, with Cormano developing and producing high-power UPSs usually with transformer – and Legnago developing and manufacturing transformerless and lower power UPSs. The two sites also produce the solar inverters for the Aros Solar Technology brand. This is very important, because increasingly we find ourselves supplying integrated solutions, combining UPS and solar inverters.”
In its quest for further expansion the company is opening a site in India, where it has set up a joint venture, of which it currently holds the majority share and of which it will soon take total control, for the purpose of