
10 minute read
Flexible roll-forming technology Dreistern International
at Dubai Airport Terminal 3 where around 5000 luggage trays can currently be stored. “This is like a small warehouse that allows passengers to store their luggage safely and enjoy their time at the airport.”
Major airport projects
In the Airport Solutions segment, LAS continues to win high-profile contracts for some of the world’s biggest airports. In early 2014, together with the South Korean company Posco, it won a contract to install a baggage handling system at the new Terminal 2 of Incheon Airport. This will cover the layout, engineering, assembly, commissioning and integration of the system, as well as connecting it to the existing baggage handling system. The entire project, which will allow for throughput capacity of more than 22,000 items of baggage per hour, is due to be completed by 2018 in time for the Winter Olympics in Pyeongchang.
Mr Ernst says of this contract win: “Incheon is a masterpiece – one of the highest quality airports in the world. It is expecting more than 40 million passengers per year and it will be served by more than 88 airlines.”
The company has also just completed, on time, a huge air cargo project at Hong Kong airport. It was designed for a throughput of 2.6 million tonnes of freight per year, thereby increasing the annual capacity of the airport’s existing terminals by 50 per cent to 7.4 million tonnes. The contract involved the installation of modern storage and conveying systems. The handling processes were specially adapted to the requirements of Hong Kong International Airport because particularly large quantities of transit and export cargo are handled there in comparison to other hubs.
Furthermore, LAS has recently received an order from Emirates SkyCargo to expand its cargo capacity with a new terminal for its freighter operations at Dubai World Central Al Maktoum International Airport. The company’s brief is to equip the new cargo terminal with modern storage and conveying systems to achieve a throughput of 700,000 tonnes of freight per year. By 2015 this is expected to increase by a further 300,000 tonnes. Work will commence on this project at the start of May 2014.
Temporary terminals
Another growing aspect of Airport Logistics offering is the installation of its CapacityPlus temporary terminals. Mr Ernst explains what this involves: “If airports are going to be han-

dling unusually large amounts of passengers, for example for a major sporting event, then they may want a temporary capacity increase. Our systems are highly flexible and perfect if a client has limited money and only wants a terminal for a certain period. The solutions come with high security features, air-conditioning, screens and everything needed for smooth check-ins. We have already had excellent feedback on this and it has huge future potential.”
To use one example, Siemens recently installed four modern temporary terminals in Angola in a very limited time frame. These were in the regional airports of Soyo, Dundo, Saurimo and Luena.
Positive outlook
Looking ahead, Mr Ernst sees strong prospects for growth in both the airport and logistics sectors. “This is a good business to be in long-term. If you just look at the order books for the two biggest airline builders – Airbus and Boeing – you can see how full they are so, there are going to be a lot of goods and people transported around the world in the coming decades. This means the airports are going to need ever-more sophisticated systems of the kind we can provide, as well as increased capacity.”
But this will not be its only focus for the future. The aim is to be close to its customers wherever they are in the world, providing them with a total solution.
Mr Ernst concludes: “We want to be responsible for the systems we deliver throughout their whole lifetime. We work closely with our clients on each project, to tailor it to their needs and help them make the right decision for the future. We don’t just want to complete a project: we also want to leave a good name behind us. This is what makes us stand out in our field.” n
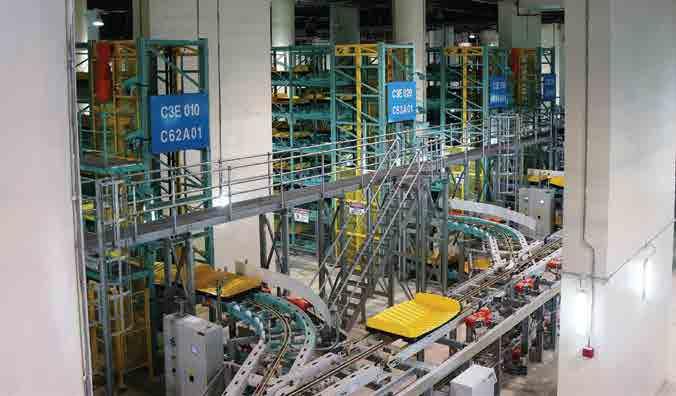

FLEXIBLE ROLL-FORMING TECHNOLOGY
German company Dreistern International is recognised as a leading provider of roll-forming systems to companies throughout the world. Dedicated to remaining at the forefront of technology in this sector, this year it has introduced yet another brand-new machining concept: multifunctional roll-forming. Victoria Hattersley spoke to the sales director, Heinrich Weber, to find out more about this family-owned company.
Dreistern’s technological leadership in roll-forming technology has been built up over more than 60 years of continuous operation. Established in 1949, it is a family business currently managed in the third generation by Thomas Krückels, the grandson of the original founder.
The company’s production plant is based in Schopfheim, Germany, where it operates on an area of over 33,000m2 and continuously invests in the latest machining centres and production processes. It currently employs over 230 people who work on developing innovative solutions for its clients, based on the specific needs of their industry sectors. Flexible production profile
Dreistern’s comprehensive range of rollforming machines are offered for a diverse range of applications, including automotive, building, electricals, logistics, furniture manufacture, tubes and indeed any other sectors where roll-formed products might be required.
For Dreistern, flexibility is the key when it comes to innovating to meet its clients’ needs. Mr Weber explains: “Design is oriented to the application, so we have dedicated machines for certain applications. However, one of the things they have in common is that they have an ‘open profile’ so that, for example, they can produce many different kinds of automotive parts using several different processes.
“We also have many major clients in the racking industry. The major trend these days amongst the major players in this field is for brand-specific applications. Customers need different profiles to produce different systems. We can offer highly flexible machines for our customers to make whatever they want quickly and efficiently.”
So much for the benefits these machines bring for Dreistern’s direct clients – but these benefits also filter down to the end users, as Mr Weber tells us: “For our clients’ clients, the main advantages of our products are reduced
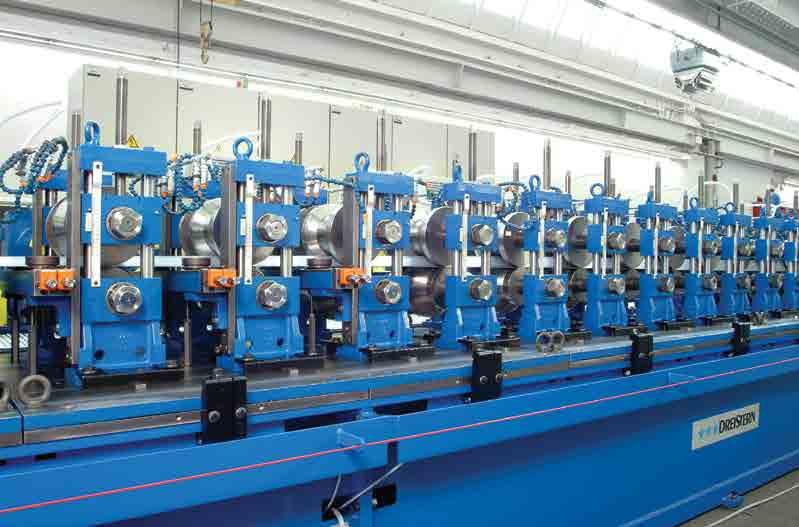


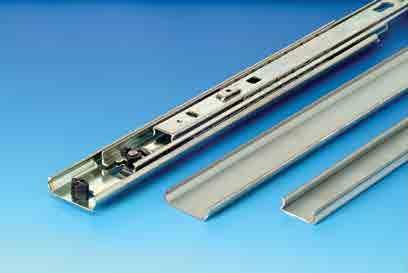
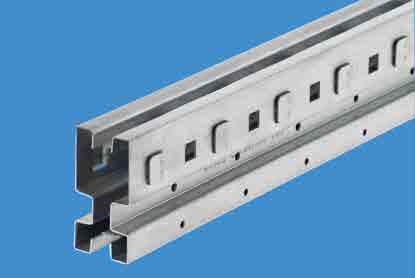
costs and lead times for them. It means our clients can provide tailor-made solutions to their customers. It also means they can offer smaller runs of products which more and more companies are demanding these days. The flexibility we offer allows them to switch quickly between different kinds of products.”
A unique new concept
Continuous innovation is one of the keys to Dreistern’s continued growth. This year has been a particularly important one for the company in this regard, as it has recently introduced an entirely new technology, ‘multifunctional roll-forming’, which it will be demonstrating at an innovation forum in May this year. This involves the integration of additional processes such as piercing, notching, embossing, bolt fixing and so on into one tube mill or roll-forming machine.
Mr Weber explains exactly why this technology represents such a breakthrough for the industry: “A roll-forming machine will typically consist of a roll-former and a press. You will then go on to the final shaping, cut-off, and sometimes for technical reasons there will have to be some punching and welding too. In a typical machine, all parts of the process will have to happen in this order and all from fixed positions, which can be limiting. Processes such as cutting and turning would have to go to external handling facilities.
“Our idea was to make the entire machine more flexible with each step available to be completed in any order to best suit the demands of the product. All the customer has to do is to change Work Modules. If they have several lines they can even move a laser cutter across or use it in different positions so they can keep several lines running all at the same time.”
All this is obviously far more efficient when it comes to both cost and time saving. Furthermore, the footprint of these machines can be up to 50 per cent smaller compared to conventional technology, so the user can also make the best use of their production space.
Lightweighting and customised solutions
The issue of lightweighting is a major one for all industry sectors today. For example, Mr Weber points out that almost all major car makers use roll forming technology today in order to cut CO2 emissions and reduce the weight of the car body.
He tells us: “Anyone working with highstrength steel is affected by the increased pressure to reduce the overall weight of their products. With roll-forming we can achieve the highest strength steels at a lighter weight without excessive wear on the material. You could maybe achieve the same strengths of material using hot stamping but this creates high energy costs. Roll forming, on the other hand, is more cost effective for both light and high-strength parts.”

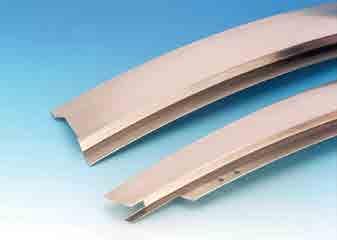
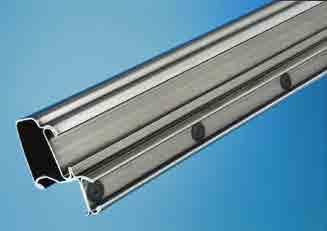
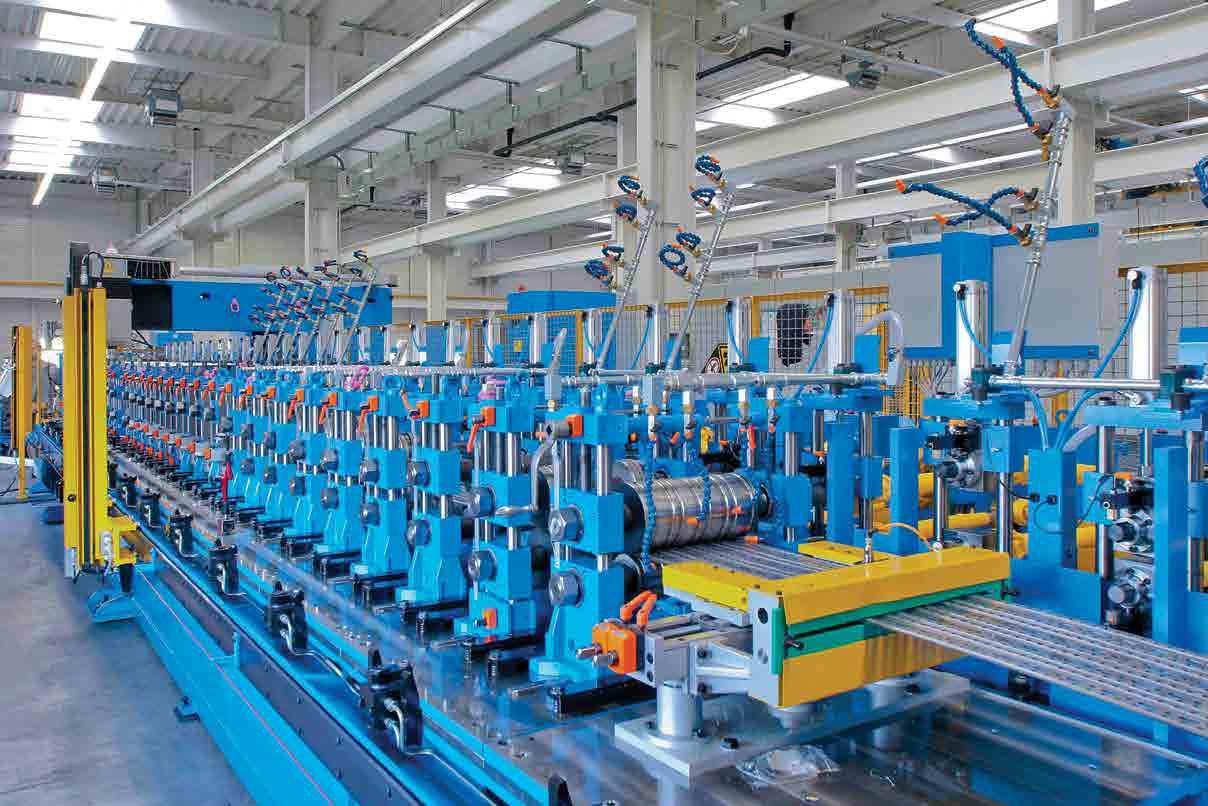

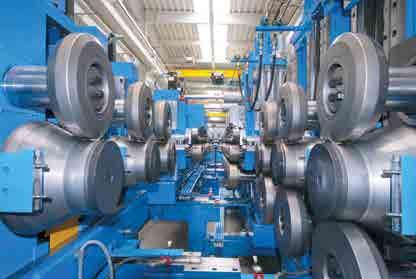

Dreistern engineers can work with a wide range of materials to meet its clients’ functionality demands both reliably and cost effectively. Whether it is steels of varying strengths, aluminium alloys, copper, titanium or gold, almost any material suitable for forming has been developed into a product on a Dreistern machine. Even when working with particularly challenging materials, which have heavily fluctuating properties, its machines are flexible enough to adjust to any changes.
Furthermore, the company’s use of rapid prototyping technology means it can work with its clients right from the conception of an idea to create a totally unique product to meet their needs. “At our facility we have 10 testing machines to produce prototypes. For example, if a client is looking to develop a new bumper they will often come to us to create their initial parts because we can do this quickly on a machine which is very close in execution to those used in later roll-forming processes. In this way, the customer doesn’t need to pay for roll-forming at this time, just the tooling. Then they already have the tool set ready if they decide to go ahead with full production. It’s much for cost effective for them.”
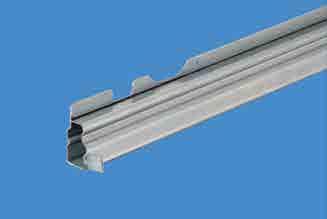
Global sales strategy
Dreistern supplies its products globally, although the majority of its customers are still in Europe – particularly eastern Europe. Elsewhere, the USA and China are major growth markets. As Mr Weber explains: “In Asia the automotive industry is particularly important. We also have some very specific partners in China. One of the reason for this is the huge number of high-rise buildings there are in this market. This means we have customers who ship parts every year for more than 50,000 elevators.”
The company’s strategy for growth is to develop steadily rather than making any acquisitions or sudden advances. It aims to achieve an average 5 per cent growth rate each year. Mr Weber believes that the key to its continued success will be the solid reputation it has built as a total solutions provider.
“Dreistern is known as a company that develops new processes. If a company has an idea for a product that could be roll formed they should talk to us at a very early stage. We have the capabilities to produce what they want in a cost-effective way.” n