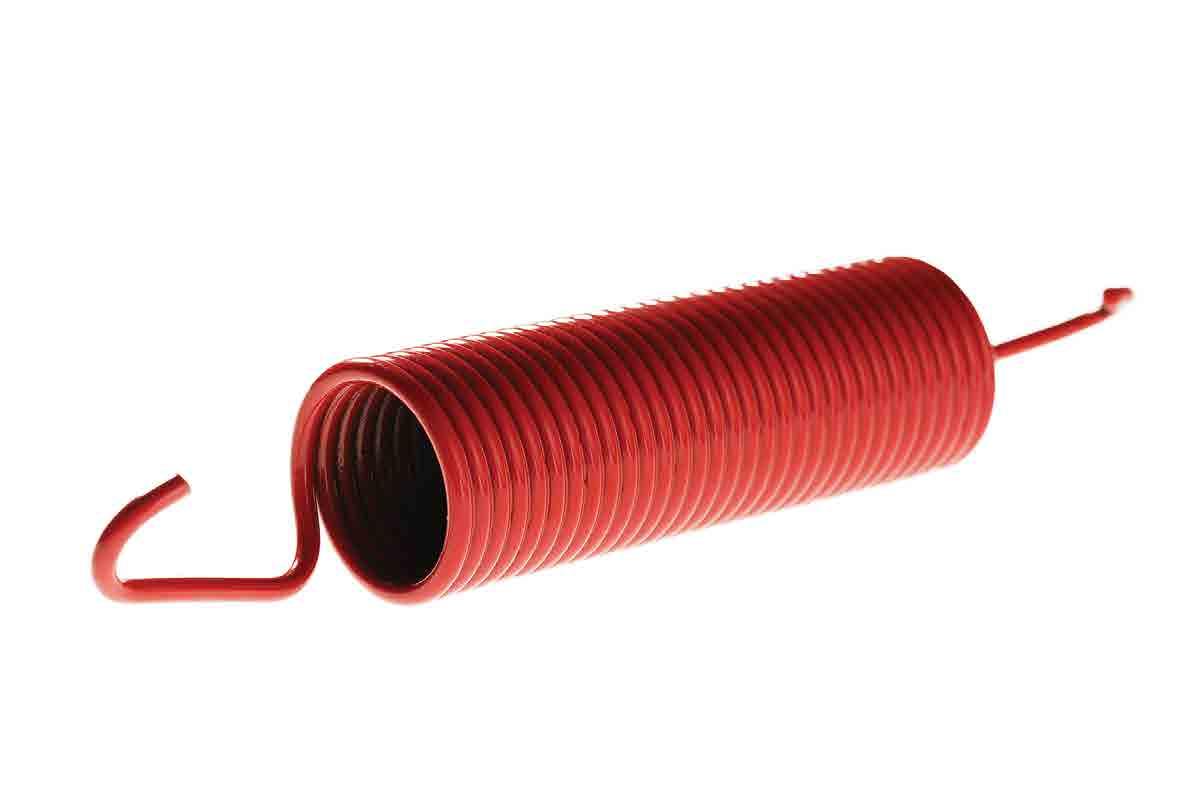
5 minute read
International spring supplier Lesjöfors
INTERNATIONAL SPRING SUPPLIER
Sweden’s Lesjöfors is a market leading spring manufacturer which produces not only a wide range of standard springs but can also tailor-make other designs to meet customers’ unique requirements. Problem solving is its key offer.
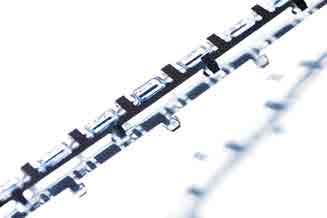
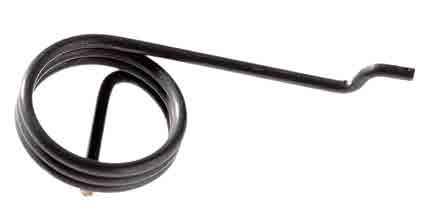
Lesjöfors has been making springs since 1852 although the company itself goes back even further – to 1675, in fact. Today it is an international supplier of a full range of standard and bespoke springs, as well as wire and strip components, with manufacturing operations in Sweden, Finland, Denmark, Germany, the UK, Latvia, and China. Since 1989 the company has been part of Beijer Alma, a Swedish-headquartered international group that focuses on component production and industrial supplies.
Lesjöfors’ operations are organised in three business areas – Industrial Springs (standard springs and customised products made from wire), Flat Strip Components (springs and other components made from flat materials) and Chassis Springs (aftermarket for springs for passenger cars and light commercial vehicles). The largest customer segments are Industrial Springs, where it has about 40 per cent of the Nordic market, and Chassis Springs, which account for some 45 per cent of the same market.
Lesjöfors Automotive produces an extensive range of springs for the European car and light commercial vehicle market; in addition to replacement coil springs, it also stocks market-leading ranges of gas, leaf and sport springs for supply to parts wholesalers and distributors across Europe and worldwide.
Overall, Lesjöfors’ products are delivered to some 60 markets across the world.
The right solution
Lesjöfors believes that its main competitive advantages are its wide product range, its consistently high quality standards and its excellent customer service, as well, of course, as its unequalled experience and its overall technical competence. The company’s spring range has a unique breadth and its products are well known for their durability, adaptability and variation ability. Lesjöfors springs are used in just about every industry sector, from automotive, aerospace and telecoms to power generation, offshore and paper and pulp. Whether the requirement is for a standard spring or for a specially-made component, Lesjöfors can help its customers to always find the optimum solution.
The company’s operations are focused on manufacturing, stocking and distribution. It holds stocks of more than 10,000 standard items for direct delivery; all the standard spring items are available as 3D CAD models.
Each of Lesjöfors’ 14 manufacturing facilities specialises on specific products ranges and markets. The spring material is selected to suit the application and the demands that

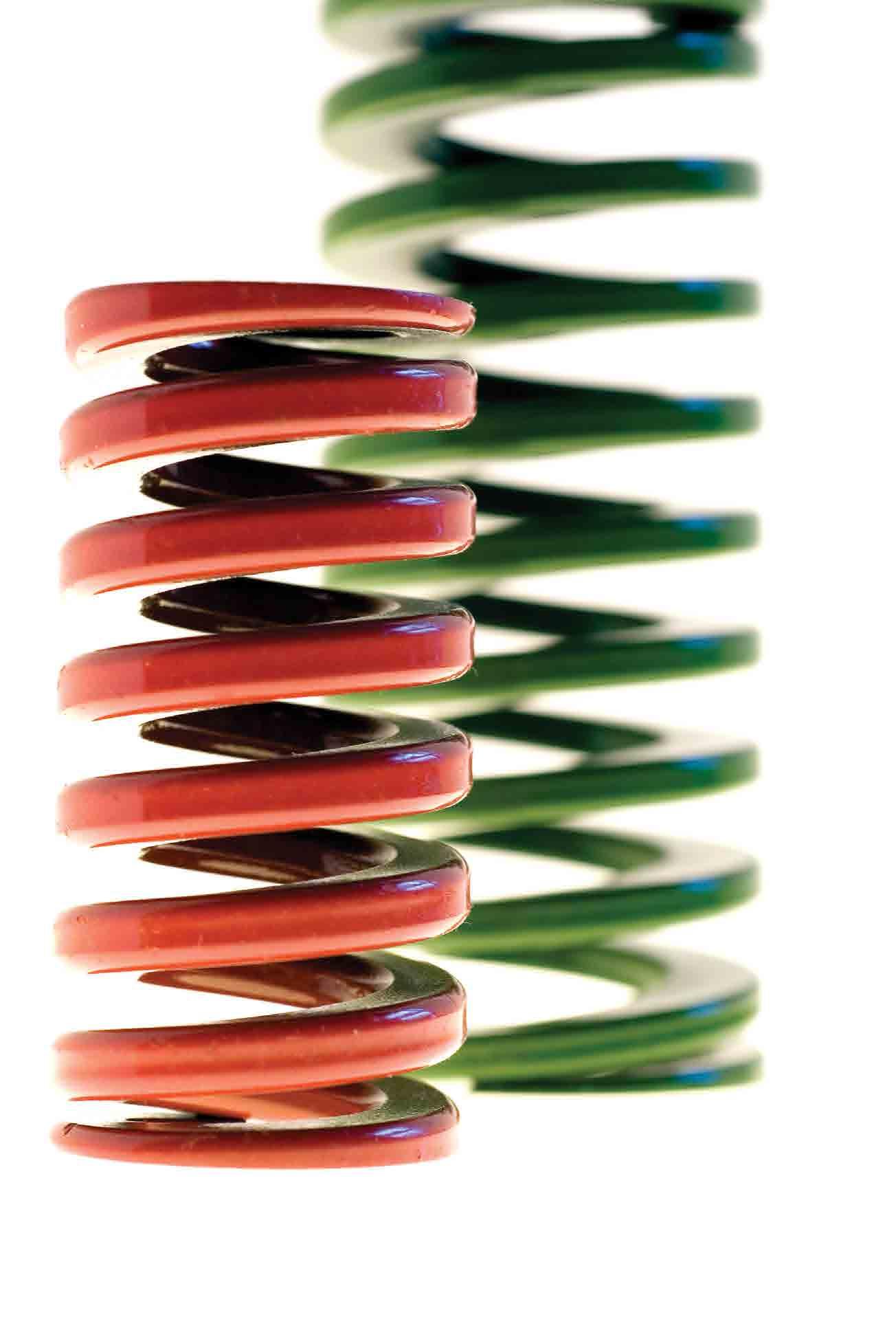

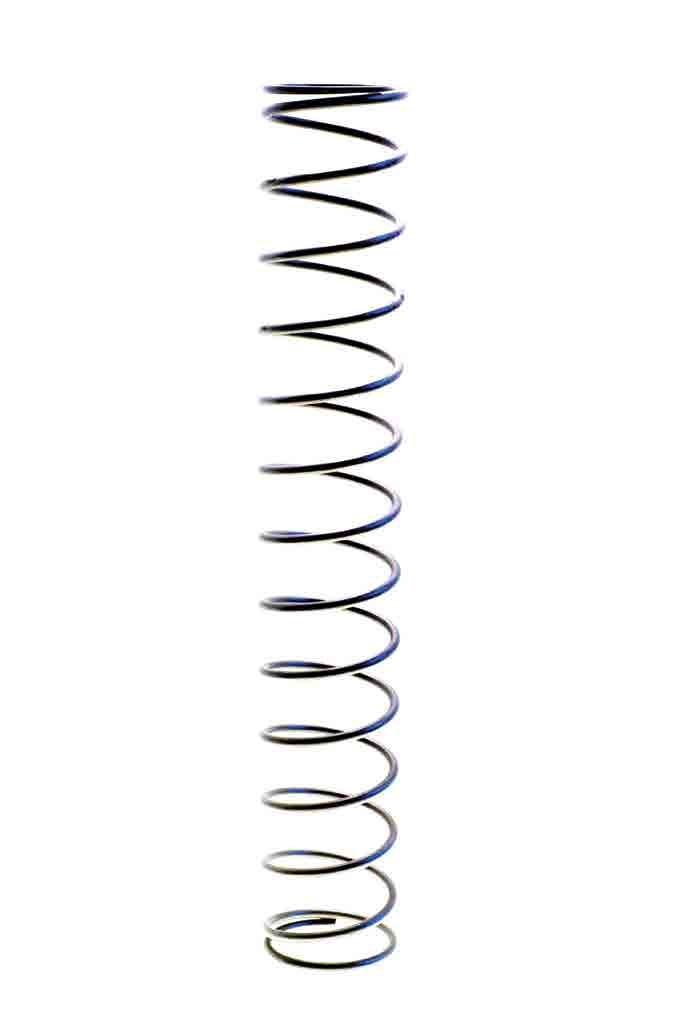
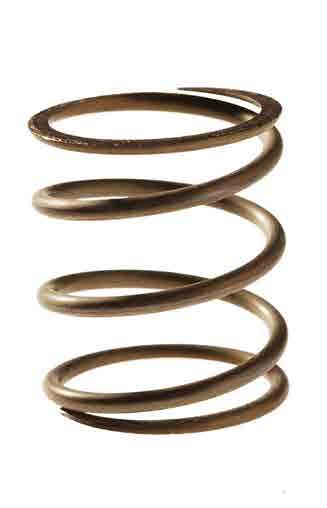
will be made on the spring. Cold drawn wire is generally used for uncomplicated springs and normal temperatures while copper alloys are used for contact springs, Stainless steel is used for difficult environments and even tungsten alloys are used for certain medical components.
The material is formed to the correct geometry by special machinery, usually be bending when cold. But stamping and hot forming are also used for appropriate products. Lesjöfors uses the most modern machinery and processes, including numerical control and automation. Investing in technology

Throughout the past year (2013) Lesjöfors has been making significant investments in new technology. For example, it purchased a new, modern hardening and tempering system for the manufacture of hot coiled springs at a cost of some 10 million SEK. Further investments of around 25 million SEK were made in the best available technology for chassis springs to meet increasing demand.
In Slovakia, the company’s machine park has been expanded with new presses and spring coiling machines to meet the growing demand for its many German customers. Investments here amounted to around 15 million SEK.
“We are constantly updating our machine park in our company to ensure the best possible quality in competitive terms. It is a very important part of Lesjöfors success strategy,” said CEO Kjell-Arne Lindebäck.
International growth
In 2012 Lesjöfors took a major step in strengthening its position in the key German markets with the acquisition of spring manufacturer Stumpp+Schule GmbH.
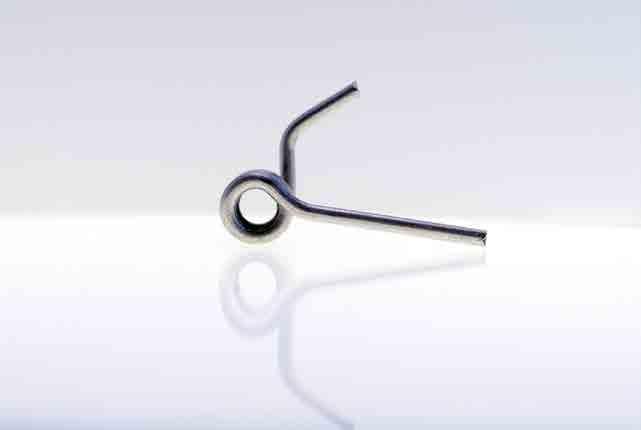
Stumpp+Schule is based in Beuren, near Stuttgart, and also has a manufacturing subsidiary in Slovakia. Germany is by far the largest spring market in Europe and, with this acquisition, over the past two years Lesjöfors has been able to grow into one of the largest suppliers of springs in the country.
Lesjöfors has been manufacturing springs in China since 2002 and continues to invest heavily in this region. It currently has around 250 employees in this market, who are operating 16 pressing processes and several machines for spring production. The main objective here is to assist European customers with spring production according to their specific needs in China.
Looking ahead, in terms of further global expansion Lesjöfors has its sights set on additional acquisitions in North and South America to add to its portfolio here. Mr Lindebäck puts this down to “the strong need expressed by various existing customers.” As ever, the company’s intention is to grow in line with customer demand to offer the highest possible service wherever its clients are in the world. n
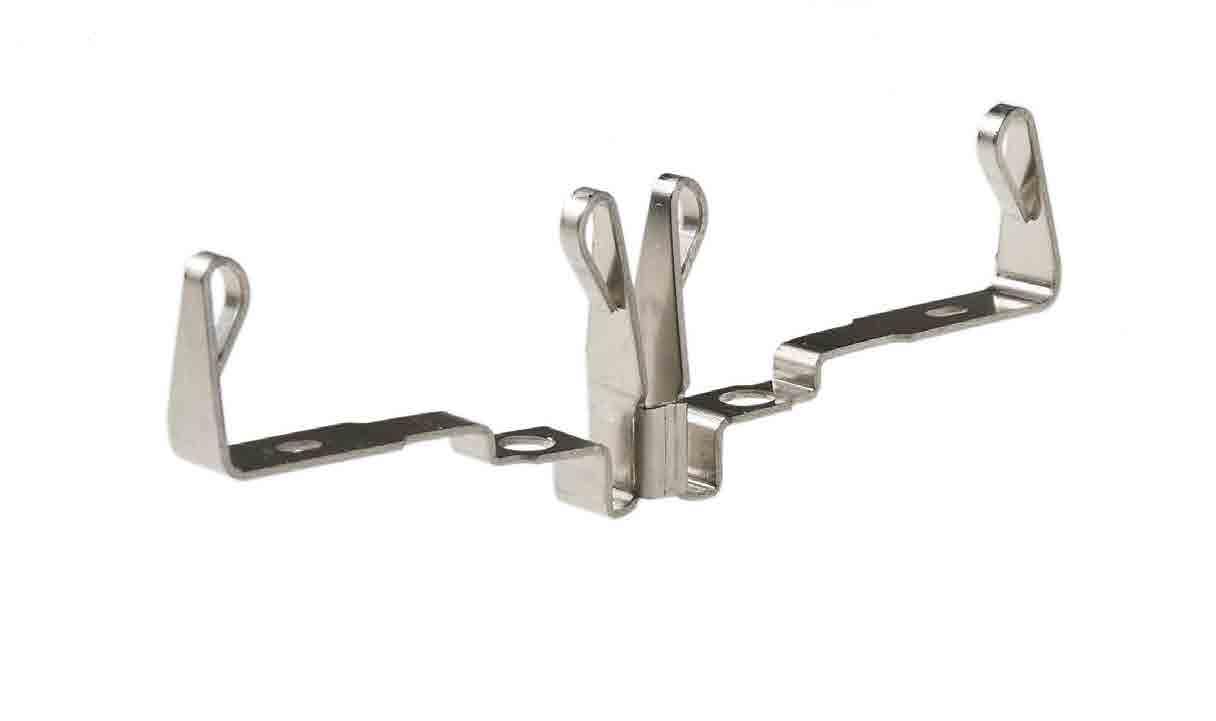
OMD S.p.A.
Performance, functionality and reliability are the key features of OMD machines. Its new range of electronic spring end grinding machines includes: • The enhancement of the special spindles for improved performance. • The possibility of independently changing the rotation speed of the grinding wheels to optimise the work cycle. • A new centrifugal cooling system to cool the surface of the grinding wheels, increasing the cutting capacity and lifetime of the abrasive product. • The operation of the spindle movements, loading plate and grinding wheel dressing system is controlled by servomotors. • An integrated spring length control system for controlling the final length of all springs produced. • An automatic centralised lubrication system. • Remote connection for direct online assistance from the manufacturer. • Graphic program interface which allows for ease of operation and cost analysis.
