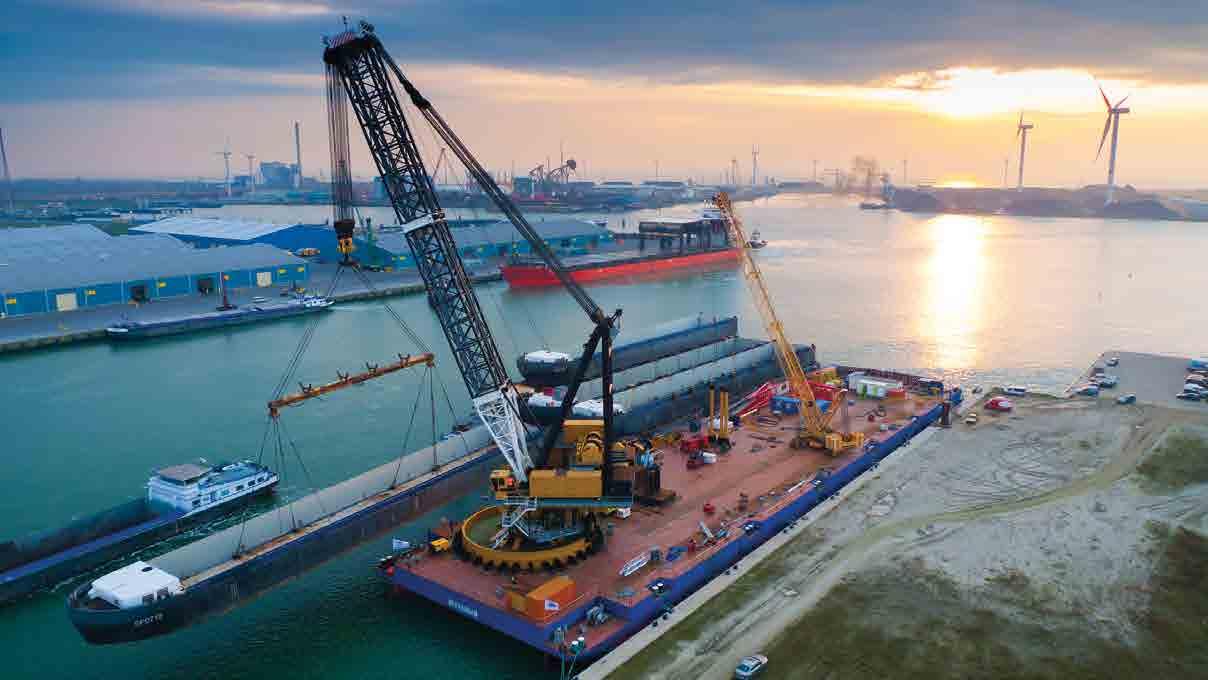
11 minute read
Pressure for perfection Avure
Conquest Offshore BV was formed as the result of a joint venture between Concordia Offshore, Paul van Es Holding and Zwaggerman Offshore Services to provide exceptional offshore heavy-lift services. The participating partners have a long and proven track record of success in the marine and offshore industry. Together the companies have united to form a strong and unrivalled coalition that offers a unique product portfolio and extended range of marine services. Today Conquest offshore is leading the world in the development and supply of heavy-duty crane barges, and is capitalising on the growing demand for very large offshore barges with exceptional heavy-lift capabilities. The all-new MB1 Conquest multi-purpose barge is specifically designed for year-round operation in harsh marine environments and is in full compliance with UK, Dutch and Danish operating regulations.
As part of the well-known Concordia Group, the company benefits from its expertise in the building of pontoons, seagoing ships, accommodation vessels and mobile offshore units. Conquest Offshore also inherits Concordia’s culture of innovative thinking and an open-minded approach to complex turnkey marine projects.
Unique capabilities
Conquest’s unique multi-purpose crane barge sets new standards in efficiency and offers a wide variety of heavy-lift capabilities. The new crane barge offers exceptional working characteristics due to the many special features built-in to its advanced design. For example the crane has a movable foundation placed on deck with 32 specially designed clamps with elastic damping and it also has a unique dynamic load system.
Bomers said, “Since we were founded in 2012 to meet the growing global demand for highly specialised heavy-lift crane barges, we have seen a steady increase in the demand for our heavy-lift equipment and services. In 2014 we joined the major marine league when we were selected to help re-float the stricken Italian cruise ship, the Costa Concordia. In cooperation with a large group of international marine companies, we installed the sponsons to re-float the Costa Concordia. Our unique crane vessel accommodates 60 people and is characterised by its 1,400 ton full revolving crane and its huge deck area.
“This high profile project has provided us with a big PR coup and we performed our role excellently which helped to significantly speed up the re-floating process, thus eliminating the risk of expensive delays. We installed 19 special sponsons along the side of the Italian vessel, and now our MB1 Crane Barge is on stand-by awaiting further instructions. Our MB1 crane barge was also
MirTac
MirTac is a no-nonsense consultancy firm with a vast background in the maritime industry and leading provider of the StarIPS fleet management software developed by SIS Marine. The software is used onboard vessels, heavy-lift barges, maritime offices, assets and rigs worldwide, linking them seamlessly.
MirTac specializes in: • Consultancy and Analysis of Fleet Management • Redesign and Organization of processes such as Maintenance,
Quality Assurance, Safety, Crew, Admin onboard • Translating customer practice with all available data into a proven and effective IT backbone, Star IPS
Customers such as Conquest Offshore claim MirTac to excel in comprehensive knowledge of fleet operations. Combined effort and teamwork with customers lead to increased efficiency, less downtime, compliance with regulations, transparency and a highly professional organisation.
Some references: Jumbo Shipping, Jack-Up Barge, Anthony Veder, Fugro, JR Shipping, RollDock, Scaldis…
www.MirTac.nl
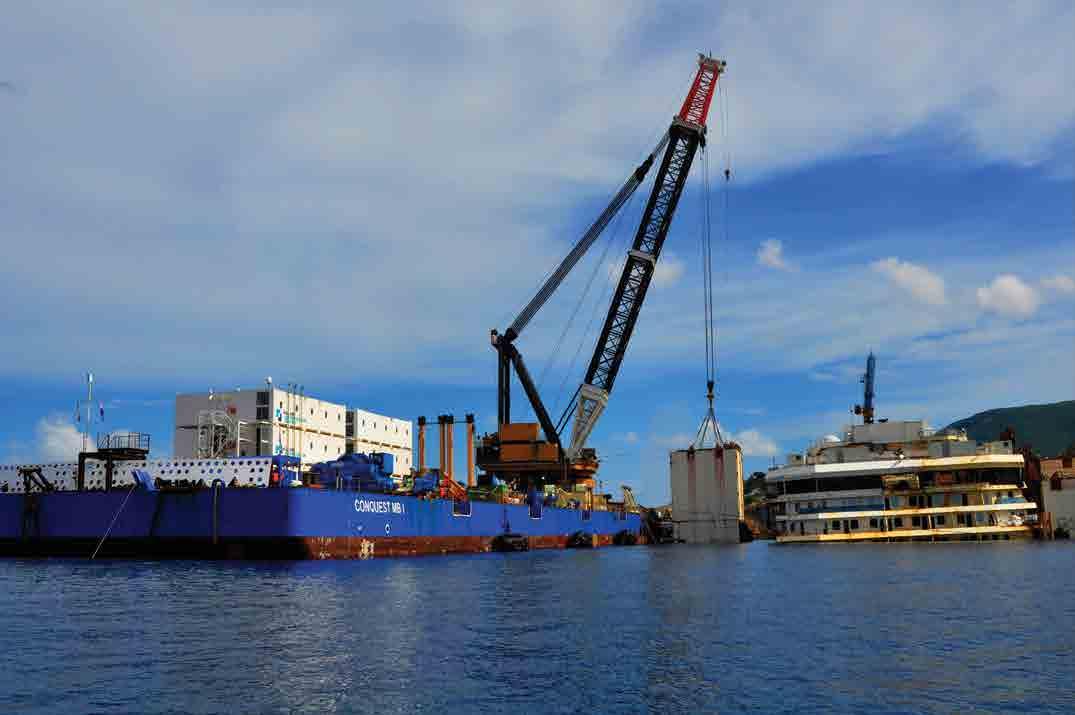
involved in another high profile project in the UK recently when we laid a series of large concrete mats in the Thames estuary.
“We are also expanding our range of marine services to include the salvage and de-commissioning of older offshore drilling platforms in the North Sea, as well as in the Mediterranean, the Black Sea and the Persian Gulf. We are well placed to serve this market and it complements our other offshore services such as the installation of wind turbines and other heavy-lift activities. In addition to our sister companies, we work with other specialist marine companies,such as Zwagerman International, the Concordia Group, Jack-Up Barge BV, the Rotterdam Offshore group, Holland Shipyards BV and The Offshore Partners BV, which allows us to offer our customers the most comprehensive and cost-effective range of state-of-theart marine facilities and services”.
New fleet management system
Earlier this year Conquest Offshore purchased Star software and related database implementations services with maritime consultancy firm MirTac. This cutting-edge software will assist Conquest Offshore with its management of efficient maintenance planning, inspections, procurement and spare part inventories. In addition, it will streamline the company’s document control, safety and environmental procedures.
MirTac’s proven track record in the offshore industry will further enhance Conquest’s fleet management system and will reduce down time, as well as supporting the barge master with detailed instructions and ready-to-use procedures on board. Barend Tooten, the managing director of MirTac said, “The Conquest MB1 multi-purpose crane can install wind turbine foundations as well as play a part in transporting and unloading heavy equipment. We are proud to support Conquest in their day-today operations.”
Bomers added, “There is a large market out there in logistics and installation work for the wind turbine industry as well as for other maritime work such as decommissioning, which requires the unrivalled mobility and capacity that our unique facilities can offer. The acquisition of MirTac’s star software will enhance our services across the board and benefit our customers through increased efficiency and cost savings” n
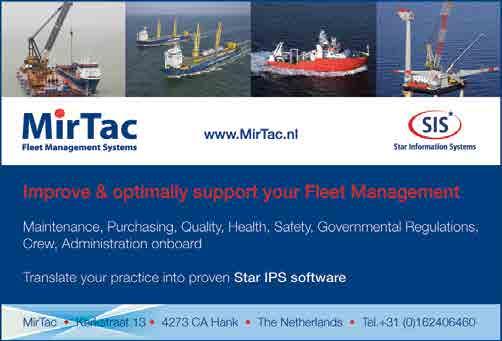
Ever since it found a way to turn carbon into synthetic diamonds 60 years ago, Avure has been using high pressure technology to produce innovative and costeffective solutions for metal processing and forming. Peter Mercer reports.
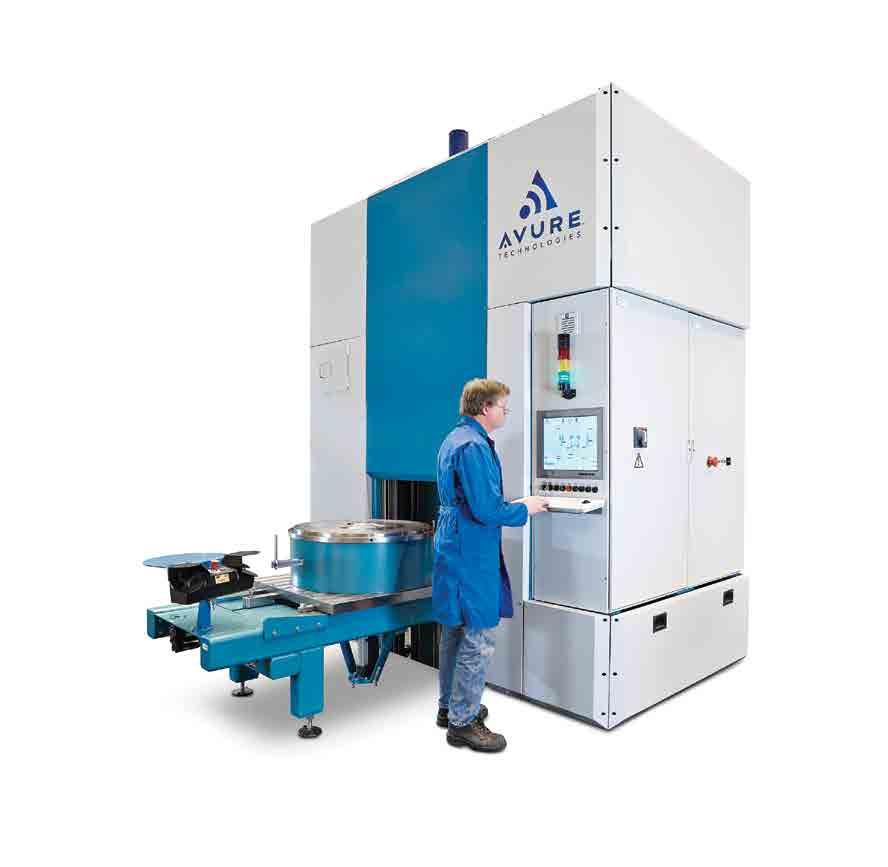
PRESSURE FOR PERFECTION
For nearly six decades engineers and scientists at Avure Technologies have led the world in the design and construction of high pressure processing systems to meet the needs of many industries. The company’s isostatic processing equipment has opened up a whole new world of possibilities in metallurgy and ceramics and its Flexform sheet metal forming systems have enabled customers to create complex shapes while saving up to 90 per cent in tooling costs as well as significant savings in man hours thanks to a reduction in the need for grinding / manual correction. Its high pressure technology has also been extended to the pasteurisation of food products such as seafood, vegetables and beverages.
Avure’s history goes back to the mid-1950s when the Swedish electrical power company ASEA began to commercialise isostatic pressure technology. In fact, ASEA was one of hte first companies in the world to create systems to produce synthetic industrial diamonds, employing pressures of nearly 1 million psi. In the 1960s it introduced isostatic presses and Flexform sheet metal forming presses to the industrial market and these were further developed when ASEA became part of Sweden’s ABB. In 1999 the high pressure business unit of ABB was acquired by Flow International of the USA who subsequently took forward the expansion of its high pressure technology into the food preservation market under the Avure brand. In 2009 Avure Technologies was sold to the privately-owned US company Milestone Partners. Then, in 2013, the company was divided into two stand-alone divisions – Avure Food, headquartered in Middleton, Ohio, and Avure Industry, headquartered in Vasteras, Sweden, where 90 per cent of current industrial production and assembly takes place. Avure Industry also has a facility in Columbus, Ohio, which takes care of projects in the North and South America regions and customer serivce for North and South America.
Today Avure Industry is focused on two high pressure technologies – isostatic presses for advanced material densification and Flexform presses for sheet metal forming.
QUINTUS
“After it had successfully developed systems that could withstand the huge pressures required to transform carbon into industrial diamonds, ASEA realised that the same technology could be used to compress other metallic or ceramic powders. The problem, however, was how to ensure the safety and reliability of containment systems with pressures of 1 million psi that would be in regular
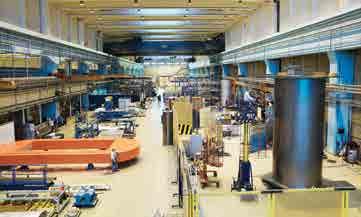


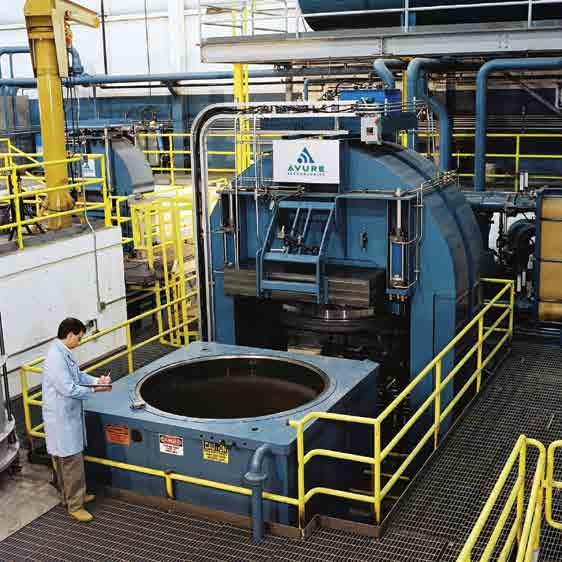
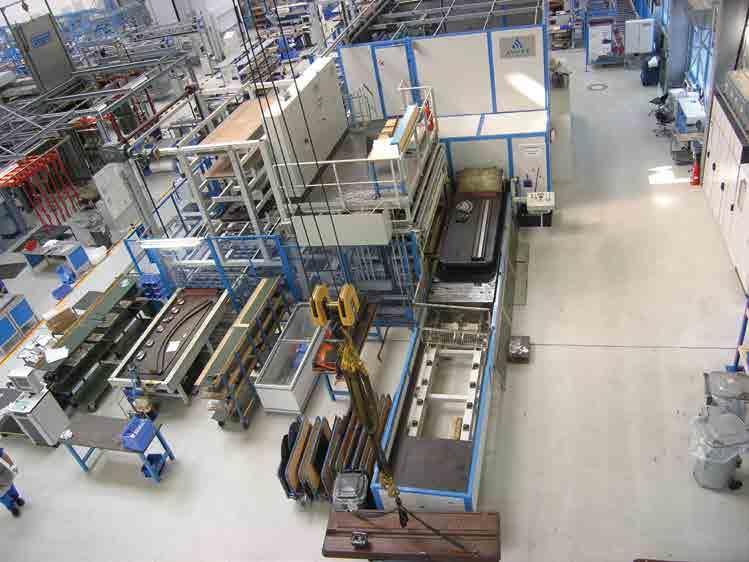
industrial use,” explains Avure Industry Sales and Business development Director Mats Sjostedt. “The solution was the development in the early 1960s of the QUINTUS wirewound pressure vessel, which is still considered to be the safest and most reliable pressure containment system ever designed.”
QUINTUS wire-wound vessels combine unmatched strength with a light, compact structure. Unlike conventional forged steel mono-block vessels they are pre-stressed and wound completely with high tensile cold-rolled spring steel ribbon. Pre-stressing causes the forged steel vessel wall to remain in residual compression even when subjected to maximum loads and the wire winding is not only much stronger than forged steel but more layers of wire can always be added to increase the strength. QUINTUS wire-wound vessels are typically half the weight of conventional presses and will leak before they break, so avoiding the catastrophic failures that can occur with mono-block vessels and the frequent and expensive inspection procedures that are required to prevent such failures. They also have a working life that is typically twenty times that of conventional designs.
Material densification
Avure’s Hot Isostatic Pressing systems (HIP) use compressed high pressure gas to produce parts that have excellent isotropic material properties and show the highest possible density of all available compaction methods. HIP Castings presses are widely used to completely remove internal porosity in castings. The HIP-ing of casted parts results in parts with a better fatigue and strength and provides more uniform properties in various metals such as aluminium, titanium, nickel-based super alloys and stainless steel. Hip’s unique ability to densify castings is crucial to the production of components such as turbine blades, joint implants and engine parts. The removal of potential initiators of failure, such as shrinkage defects, pores and voids, significantly improves the strength and durability of cast components.
The use of HIP also widens the range of titanium alloy compositions possible for castings in comparison with wrought systems. Significant cost savings can also be achieved with investment casting and HIP in comparison to machining parts from solid.
“Avure’s material densification systems are widely used for refining castings in the aerospace, automotive, bio-medical, energy and consumer electronics industries,” says Mats Sjostedt. “In essence you put a cast part into a hot isostatic press and all the cracks and other defects just disappear, resulting in parts with highly accurate tolerances and very long lifetimes. A critical advantage of HIP is that parts for aircraft or automobiles, for example, no longer have to be over-designed to ensure their strength, which means they can weigh less and cost less. Reducing weight is essential in new-generation, fuel-efficient airplanes and with an estimated 35,000 new airplanes required by 2035 and 137,000 engines the potential demand for Avure’s HIP casting systems in immense.
“In the automotive industry too the drive towards reducing the weight of cars and trucks means increasing use of aluminium parts. But aluminium is a low viscosity metal and it is easy to get cracks in castings. With HIP, defect-free aluminium castings can be guaranteed for critical applications such as engine blocks and costs reduced thanks to much lower scrap rates. And in the energy industry the expansion of deep-sea oilfields and the likely demand for up to 500 new nuclear reactors over the next 20 years will also drive the increase in demand for our HIP systems.”
Avure’s HIP technology is also widely used in powder metallurgy. The hot isostatic pressing of encapsulated powder metals produces net or near net shape parts with special particle properties. HIP treated PM parts are isotropic and deliver significant savings in materials and lead times compared to wrought components. HIP also enhances the versatility and design flexibility inherent in powder metallurgy by allowing, for example, freedom in chemical composition, particle size, distribution, form and even permitting graded structures.
HIP PM parts are increasingly used in the oil and gas producing industries for valves, pumps and drilling components, where they reduce the need for costly frequent inspections, and as components for solar panels, electrodes for steel production and, of course, in the aerospace industry. The technology is also critical to the fast-growing 3D Printing industry, where parts such as hip implants need to be structurally perfect.
Flexform
Avure’s solutions for metal forming are centred on its Flexform fluid cell forming system. Introduced by ASEA in the 1960s, Flexform employs a soft rubber diaphragm filled with highly pressurised fluid to press flat metal blanks uniformly into and around a lower tool half, which can be a punch or die. It is a highly versatile solution for manufacturing highly defined prototype components, particularly in industries where speed and lower costs are crucial in reducing time-to-market and staying globally competitive. Flexform is also ideal for low volume parts production.
Today Avure is the leading fluid cell press supplier to the aerospace industry, with