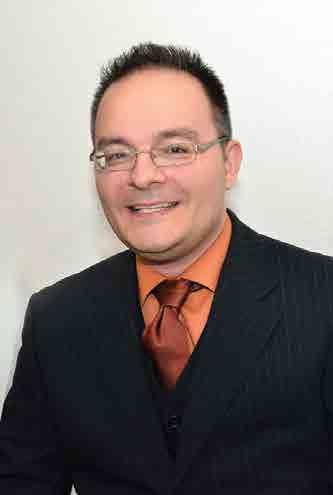
6 minute read
Continued growth for chemical giant TVK
CONTINUED GROWTH FOR CHEMICAL GIANT
The Hungarian Tisza Chemical Group Plc. (TVK) and Slovakian SLOVNAFT a.s. (SLOVNAFT) are an integrated part of the Downstream division within the MOL group, exploiting optimised refinery and petrochemical production processes in accordance with the group’s philosophy ‘from crude oil to plastics’. We asked Mr Sándor Gera, MOL head of Group Polymer Products Sales, about the focus areas, investments, new products and goals for the future.
IE: In which areas are there synergies to be exploited between Petrochemicals and Downstream’s other activities?
SG: There are many interesting intermediate chemicals along the propylene value chain which are currently being revised and may prove to be attractive. However, we would not enter into any derivatives business until the corresponding end-product markets appear to be more promising on the strategic horizon.
Shifting petrochemical feedstock (mostly naphtha) towards lighter composition is another possibility. Regarding the raw materials of olefin production, there might be other options rather than steam cracking, some of which would significantly affect Downstream. However, the examination of such options will need particular caution.
IE: What are your core products?
SG: MOL Group’s crackers produce ethylene and propylene from naphtha and gas oil, then these products are processed further in the polymer units using world-class technology to supply low-, medium- and high-density polyethylene and polypropylene products. Both TVK and SLOVNAFT are producing commodity polymers in competitive quality for the plastics processing industry, which are fundamental for a wide range of industrial application and for production of a huge number of consumer goods that are essential to our everyday lives. IE: What production facilities do you have?
SG: We have two steam crackers in Tiszaújváros with 370 kt and 290 kt capacities, and one in Bratislava with a 220 kt capacity. We are running two HDPE plants in Tiszaújváros (Hungary): one for unimodal products (200 kt capacity) and one for our bimodal portfolio (220 kt capacity). We are producing LDPE in two locations: the Tiszaújváros site has a 65 kt capacity, while the capacity of the old units in Bratislava is 130 kt. The PP capacity of TVK is 280 kt, while SLOVNAFT has a 255 kt PP capacity.
IE: Have you made any major investments recently or are any planned?
SG: MOL’s management has decided to invest into Downstream activities, so we are facing big changes in the near future.
In Bratislava SLOVNAFT is building a new LDPE unit with a 220 kt yearly capacity. The licensor is LyondellBasell and the planned startup is Q3 2015.
At the same time TVK is building a butadiene extraction plant in Tiszaújváros that provides us with a further option to enter the attractive synthetic rubber market. The construction is going according to plan, so the 130 kt/annum capacity butadiene plant is expected to become operational in 2015. Following the butadiene plant we will start up a synthetic rubber plant together with the Japanese company JSR in 2017. IE: Petrochemicals is an important pillar in the refining of by-products. How will recent investments by MOL Group change the value chain?
SG: The recent investments will extend our value chain, which is actually integrated from crude to plastics. Owing to the lack of lighter gas feedstock available in central Europe, MOL Group’s petrochemical business consumes a mixed feed of naphtha, LPG and gas oil. Thus, we have a higher yields of heavier olefin products.
IE: What about ‘old’ assets? Is there any efficiency/modernisation program in progress?
SG: Regarding petrochemical developments, we must always bear in mind the capital intensity of this industry. If modernisation of an existing older plant requires considerably less capital investment than building a new unit, reconstruction can easily provide superior economics. However, the competitiveness of products must be the decisive factor of a revamp – improved unit cost can hardly compensate for disappearing demand or declining price levels.
In the case of polymer units, this is a major concern for TVK, since Slovnaft is already on track to have two modern, competitive-scale units (PP-3, LDPE-4). At TVK we are facing some strategic decisions in the coming years. As for the olefin plants,
Construction of brand new LDPE unit is in progress
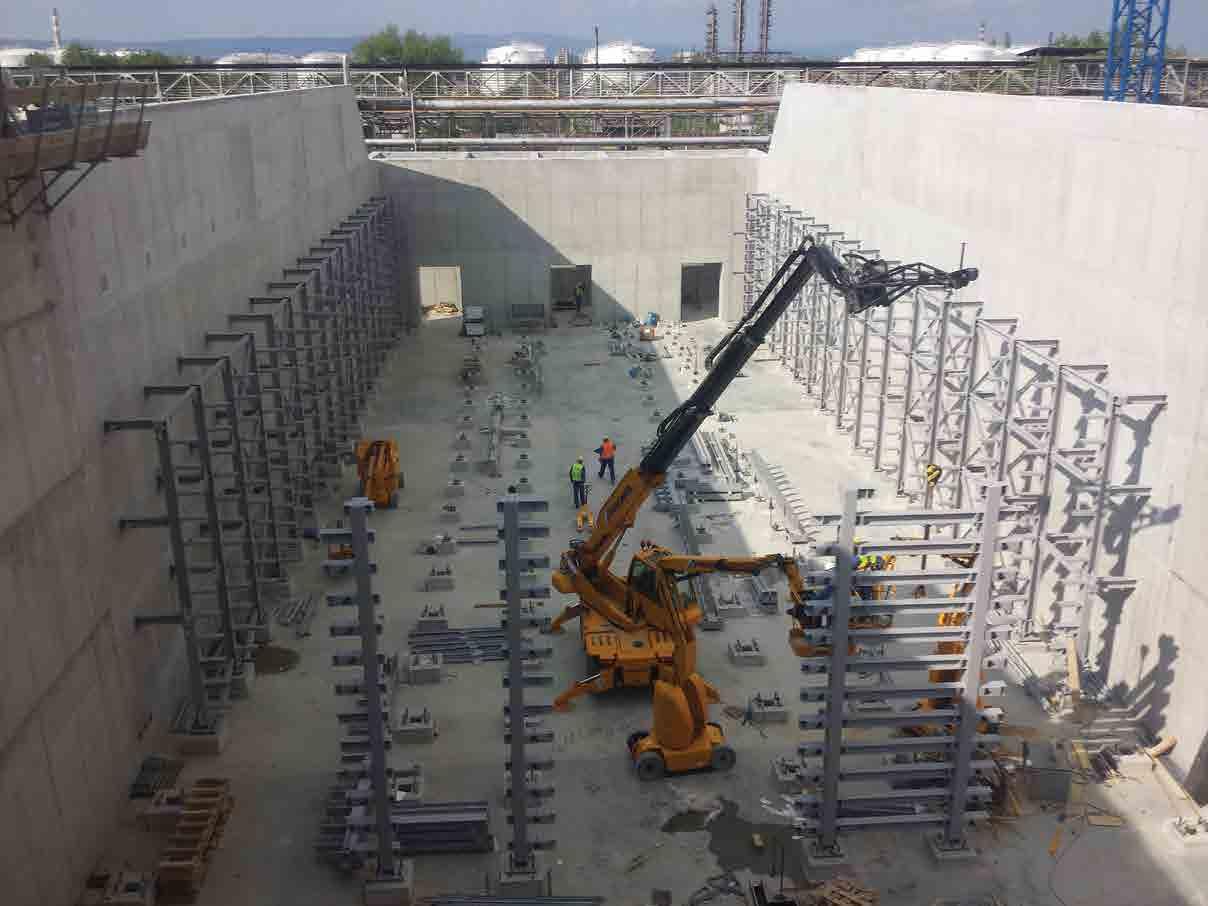
all modernisation must aim at improving profitability through modified feedstock composition and reduced energy consumption. As these units play a key role in refinery petrochemical integration, evaluation of the feasibility and economics of any major intervention will require extensive study.
IE: How do you see the company developing over the next few years?
SG: There is major growth potential in the central and eastern European markets, as the per capita plastic consumption in these regions is significantly lower than at the western European level. We will be able to exploit this opportunity through our favourable geographic location and efficient operations. Our aim is to ameliorate our successfully working product and customer management. We also treat the issue of reducing our biological footprint as a priority, and within that we have, for instance, launched a joint research program with a Hungarian university focusing on developing bio-degradable polymer products. The group also continues to run energy saving and emission reducing development programmes. IE: How does Petrochemicals affect Downstream’s unfavourable external environment?
SG: Owing to this year’s results and shortterm analyst forecasts, we look to the future with cautious optimism. Butadiene prices are expected to rise from their relatively low current levels. Consequently, the profitability of Butadiene production will be restored to the level that initially made it an attractive investment option. Concerning LDPE-4, we hope a smooth operation will allow us to monetise the development from the very beginning through reduced unit cost of production. On the sales side, we will definitely have a competitive product portfolio, especially for film grades, the introduction of which will be supported by extensive premarketing. As far as market analyses are reliable, the European LDPE segment is the least threatened by import competition. Further penetration of LDPE grades into film applications will certainly influence market opportunities. Having high quality products is also definitely an advantage from this point of view.
MOL Group Polymers can also be competitive when it comes to the level of services it provides and in its knowledge of CEE markets. In the latest customer satisfaction surveys, we have found that price isn’t the only important factor for our customers when choosing a supplier. The availability and quality of materials is as important as price, or even more important. As we can’t be competitive with Middle Eastern polymer producers on the cost side, we must focus on the above-mentioned areas.
IE: Are there any new products being developed?
SG: Over the past few years we have implemented several technical innovations and technological developments. Our aim is to continuously follow the new market requirements and the changes to the reprocessing trends in order to maintain a constant product development process and to complete our product portfolio. We focus on the specific demands of our customers and develop so-called ‘tailor-made’ products.
We do believe that a high level of customer service and continuously improving customer satisfaction are the key areas through which we can maintain and improve our current strong market position in the core region. n