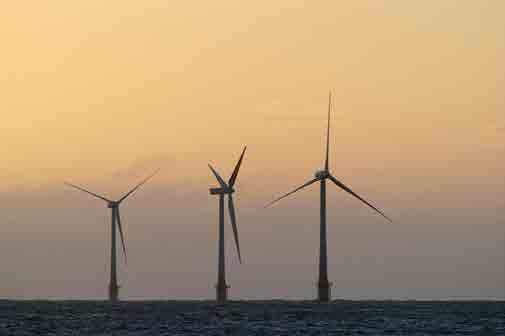
4 minute read
Moving on Relocations and expansions
NEWS
MOVINGON
Relocations and expansions across Europe
E.ON to build Rampion offshore wind farm
E.ON has confirmed the investment decision for the Rampion Offshore Wind Farm in the UK. The total investment is approximately €1.9 billion. The UK Green Investment Bank plc (GIB) has acquired a €327 million stake in the project. The project is located in the English Channel, 13 kilometres from the Sussex coast due south of Brighton. The development will have the capacity to generate 400 megawatts of electricity and is expected to generate 1300 gigawatt hours of renewable energy annually, enough to supply the equivalent of up to 300,000 homes and reduce CO2 emissions by up to 600,000 tonnes a year.
The project is comprised of 116 3.45 megawatt wind turbines, associated foundations, an offshore substation and cabling. The water depth ranges from 19 to 40 meters. Mike Winkel, E.ON board member, said: “Technically, the project is an optimised evolution of our four most recent offshore wind projects. We rely on proven technology and installation processes. With these preconditions E.ON will demonstrate its top-class competencies that we have developed in managing the construction and operation of offshore wind farms.” Visit: www.eon.com
Volvo Cars Torslanda plant starts up a third production shift
The third shift in Volvo Cars’ Torslanda plant has started, creating nearly 1500 new jobs in the company’s Western Swedish home region. The introduction of the additional night shift comes as Volvo has now started production of the all new XC90 seven-seater SUV, for which the company has already received close to 30,000 pre-orders.
Following this latest expansion, Volvo Cars has approximately 17,300 employees in Sweden, of which 13,500 are in Gothenburg where 4800 people work in the Torslanda plant.
“I am very pleased by the extraordinary positive reception of our new XC90 model and that we can welcome 1,500 new employees to the Torslanda plant to produce this new car’, says president and CEO Håkan Samuelsson. “This is just the start – we will launch a whole range of new cars in the coming four years, many of which will be produced here in Torslanda.” Visit: www.volvocars.com
Million pound investment for Newark Steel
AN investment worth £1m has been announced at Barrett Steel’s Newark plant, which will result in a 50%-plus production increase in painted product. Part of the General Steels Division, Newark Steel plans to boost production from 200 tonnes to 500-plus tonnes each month of CE accredited shotblasted and painted product.
Adrian Spencer, managing director of Barrett Steel’s Eastern Region, explains how the investment will dramatically improve efficiency in the shot blasting and painting areas: “We have installed two new Kone 28.5 span, 5-tonne, twin hoist cranes, a pre-heater, a paint booth and drying tunnel. The equipment will help us to overcome the problem of blasting what was quite often a ‘wet’ product. Now steel products will originate from our outside gantries, hence the need for the new twin hoist, purpose-built outside cranes. The products will run through a pre-heater using recently installed natural gas, reaching a temperature of 30/35, and enter the shotblaster completely dry. From the blaster they will proceed immediately to the automated paint booth.” Visit: www.barrettsteel.com
Bauer opens flagship production facilities to halve lead times
Tuesday 5 May marked the official opening of the new Bauer production facility at the company headquarters in Esslingen. The facility will act as the flagship for Bauer’s new production concept, which increases the flexibility of the company’s ability to deliver engineered solutions for all applications on extremely short lead times.
Karl-Peter Simon, Bauer Gear Motor managing director, explains: “This new facility represents the next step in Bauer’s production concept, which will eventually expand to our key regions around the world. We have adapted our production facilities to operate as one piece flow, moving assembly lines. This prepares us for fast delivery of both small and large customer orders.
“We have been able to create a connected factory concept whereby our production facilities in Germany are supported with just-in-time deliveries from our production factory in Slovakia. With this concept we are prepared for implementing Industry 4.0. This means that the two sites are operating on the same production schedule. This will allow us to reduce our current standard production time for configurable gear motors from 10 days to 5 days.” Visit: www.bauergears.com
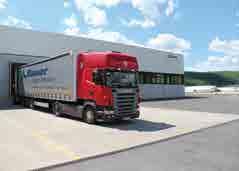
WACKER Expands Technical Centre in Moscow
Munich-based chemicals group WACKER has expanded its technical centre in Moscow, Russia. The facility will serve as a test lab for silicone elastomers and readyto-use silicone compounds and will cater to the energy, electrical and automotive industries. This investment aims at further enhancing services to key customers in Russia and eastern Europe and spurring WACKER’s silicone business in the region.
The lab is located south of downtown Moscow, right next to the technical centre, which has supported customers since 2003. The new lab is entirely geared to silicones customers. It will formulate and test high- and room-temperature curing silicone rubber and ready-to-use silicone compounds. WACKER also expects mid- and long-term business growth from the Russian automotive industry. Silicone rubber is increasingly used in cars because of its unique set of properties and because it meets the industry’s ever more complex requirements better than other plastics. Visit: www.wacker.com