
6 minute read
World leader in carbon fibre production Zoltek
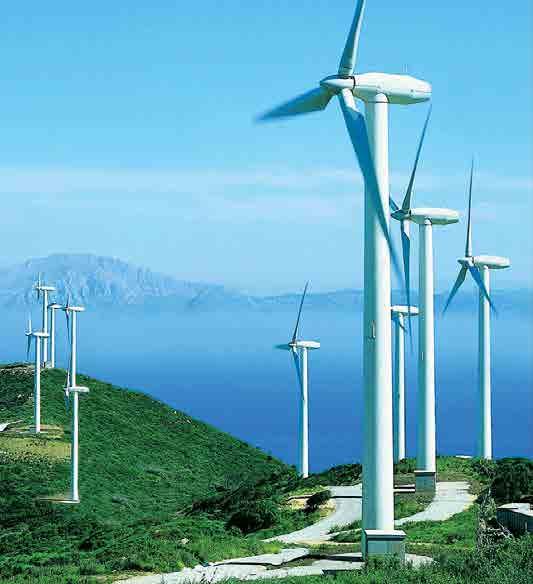
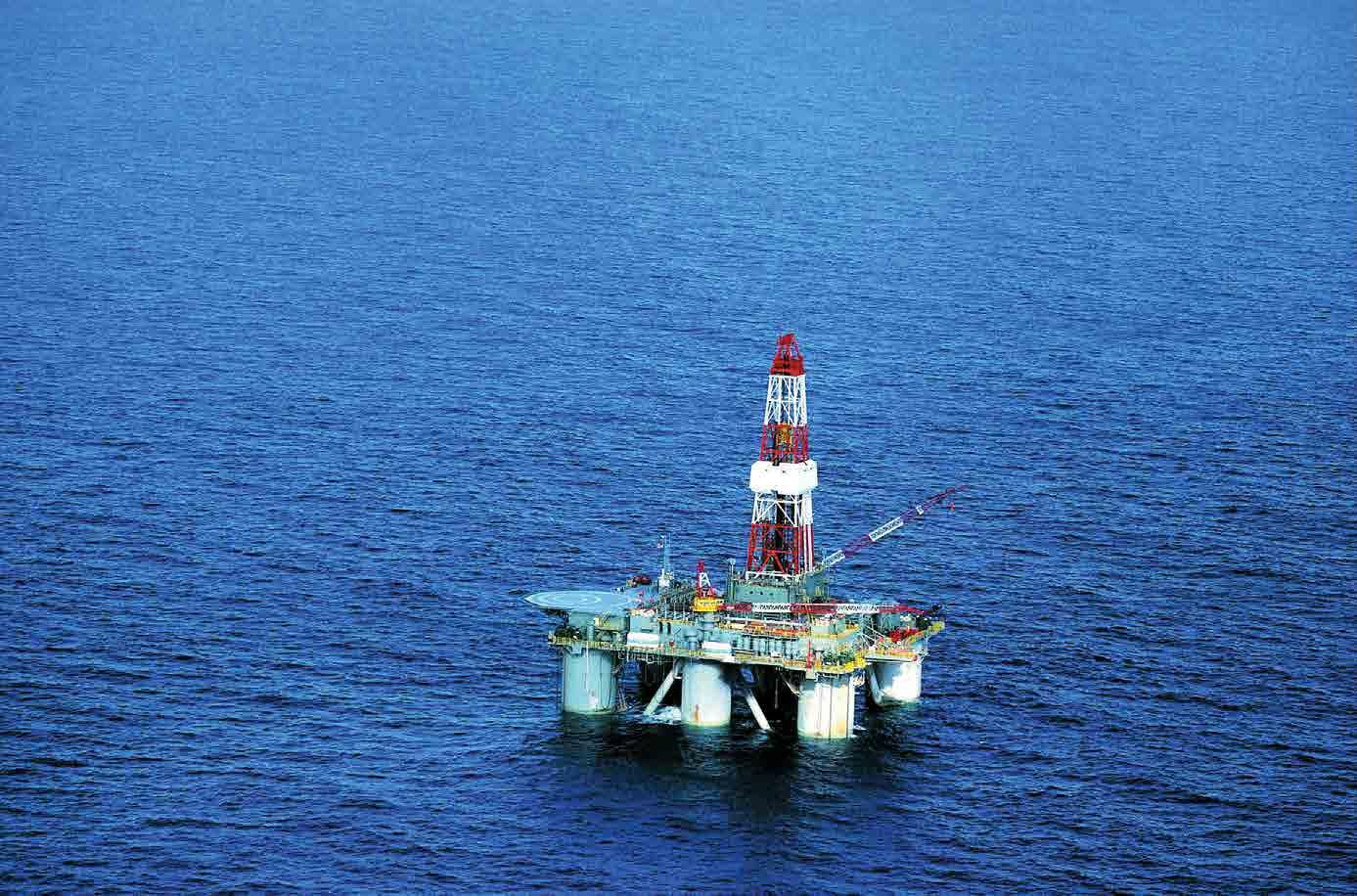
WORLD LEADER IN CARBON FIBRE PRODUCTION
Zoltek Zrt, based in Nyergesújfalu in Hungary, is a wholly-owned subsidiary of the US-based Zoltek Companies Inc. This successful arm of the global corporation has the biggest carbon fibre production capacity in the world. Industry Europe looks at the company’s history and recent activities.
AS part of Zoltek Companies Inc., Zoltek Zrt has long been a major European player in the field of carbon fibre production. In March this year (2015) it further consolidated its position when it signed formal strategic cooperation agreement with Hungary’s Minister of Foreign Affairs and Trade. This agreement outlined a plan to expand production capacity and employment at the company’s main plant in Nyergesújfalu, which is already the largest carbon fibre factory in the world and manufactures a wide range of materials for use in the wind energy, aerospace and automotive industries. This expansion is set to create 100 additional jobs immediately and another 200–300 over the next few years.
Company history
It is in part the company’s long-term experience that has enables it to maintain its leading position. Magyar Viscosa, the predecessor of Zoltek Zrt, was established in Hungary in 1941 as a manufacturer of basic commodities for the textile industry. Ten years later it began the production of carboxy methyl cellulose (CMC) under its own licence, and during the next few years it began producing Poliamid 6-based staple fibre and filament under the brand name DAMAMID, and acrylic fibre under the brand name CRUMERON. Its product range continued to expand, and by the 1980s it was coping with the production of plastic nets and mesh, engineering plastic and polyamid compounds.
In 1993 the company became a state-owned company under the name Magyar Viscosa Rt. Two years later the American company Zoltek bought the shares owned by the Hungarian Privatisation and State Holding Company and Magyar Viscosa Rt. became a subsidiary of Zoltek Companies Inc, operating under the name Zoltek Zrt. Carbon fibre production and carbon fibre textile processing began in Hungary in 1997.
In 2004 Zoltek Zrt went through a significant transformation: It ceased the production of viscose staple fibre and launched a number of new production lines. Capacity increased as a result of new capital expenditure and the profile of R & D was also raised. One outcome of this was the establishment of a domestic base for membrane ultra-filtration production and research.
Production profile
Zoltek Zrt’s carbon fibre business unit manufactures carbon fibre as a reinforcing material for composites in the automotive, plastic and building industries. In addition, it produces oxidised PAN fibre for carbon-carbon composites and flame retardant materials for the aerospace and automotive industries. The company uses two different manufacturing technologies: PANEX 35 carbon fibre tow and PYRON (oxidised PAN) tow, which has less carbon content. The two types of carbon fibre differ according to their end uses.
Panex 35 is a low-cost commercial carbon fibre manufactured in a proprietary high-throughput process that allows it to be the lowest cost commercial carbon fibre on the market. Panex 35 is the dominant carbon fibre in the wind turbine industry and is at the forefront of many other applications including infrastructure, automotive, pressure vessels, offshore drilling, and other industrial applications.
In electrical applications, carbon fibres can be used to tailor the electrical properties of injection moulding compounds, paints and
Megawatt Kft was established in December 1989 and is owned by Hungarian private individuals. The company established two sites: a sales department in Nyergesújfalu and a construction department in Lábatlan.
The sales department distributes products of prominent manufacturers to partners including companies and private persons.
The construction department primarily provides services including the design and implementation of strong/weak current industrial facilities and of the strong current construction and process control of industrial technologies. In addition we take part in design and construction of offi ce buildings, public buildings and private fl ats.
Megawatt Kft applies ISO 9001 quality management system.
Design/Implementation/Production: 2541 Lábatlan, Rákóczi F. u. 262. Tel: +36 33 463 223 Fax: +36 33 361 169 E-mail: kivitelezes@megawatt.hu Sales: 2536 Nyergesújfalu, Kossuth L. u. 129. Tel: +36 33 454 000 Fax: +36 33 454 494 E-mail: megawatt@megawatt.hu Web: www.megawatt.hu We are able to offer the following services from our factory that complies with the MSZ EN ISO 3834-2 quality assurance standards: • Production of stainless steel tanks referring to the 97/23/EG, G Modul, IV. category pressure equipment directive • Design and production of unique industrial equipment from rust- and acid-proof steel • Assembly and implementation of complete technological systems • Production of AQUAREX INOX hydraulic pressure control vales in
DN50-200 sizes • Design and production of interior decor and household items and handrails
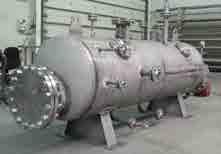
GYGV Kanizsa Kft. 8800 Nagykanizsa Egerszegi u. 2/F, Hungary Phone: +36-93/313-283 - E-mail: info@gygv.hu - www.gygv.hu
adhesives. The resulting products provide the benefits of plastics with the conductivity and electrical shielding capabilities of metals. When used in adhesives, the electrical conductivity of carbon can be used to enhance cure times in RF environments by an order of magnitude. The electrical properties of carbon fibre and the ability to configure the material into a semi-permeable membrane with defined mass transport properties make carbon an ideal choice for Next Generation fuel cell engines.
In friction applications, carbon fibre is used to create materials that can withstand extremely high temperatures coupled with brutal abrasive wear. Small amounts of carbon can even be used to control the explosive burn of airbag propellants, resulting in the safer deployment of airbags in automotive applications.
PYRON Oxidised PAN Fibres are ideally suited for chemically resistant and thermally stable applications. The fibre is made by continuously oxidising pan precursor to a carbon level of 62 per cent. PYRON carbon fibres are generally used to replace asbestos in low-cost friction applications such as automotive or industrial clutches and brakes. Other applications include protective fabrics and chemically resistant packings for pumps and valves.
Zoltek products at JEC
Some of Zoltek’s latest carbon fibre developments in wind energy and automotive were showcased at this year’s JEC Europe trade show. For example, the automotive section of the company’s booth showcased its intermediate carbon fibre products specifically formulated for use in automotive, and a variety of commercially-ready surface and structural carbon fibre automotive parts. These included a carbon fibre roof panel with a premium and paintable surface manufactured via a new process called ‘Surface RTM’. This process is the result of a year-long industry partnership with using the latest KraussMaffei RTM technology, Henkel PU chemistry, Chomarat C-Ply fabrics, Ruhl PU coatings and Zoltek’s specially-sized Panex 35 50K carbon fibre. The partnership resulted in an impressive carbon fibre roof panel for the Roding Roadster that is ready to paint directly out of the moulds and is suitable for structural and semistructural parts.
In the area of wind energy, Zoltek showcased its pultruded profiles, including segments of wind blade spar caps built with pultruded profiles. They can also view spar caps built with Panex 35 prepegs and fabrics. In fact, many other markets besides the wind energy sector are beginning to open up for Zoltek now that its pultruded products are fully commercialised. The high strength and stiffness, as well as lightweight and corrosion resistant properties of carbon fibre pultruded profiles, are performing and testing well in offshore drilling, infrastructure and other industrial markets.
Finally, Zoltek displayed its newly formulated Panex 35 prepegs with specific resin formulations available for wind energy, automotive, marine, medical and consumer electronics. Its recent expansion into a new 12,500m2 prepeg manufacturing facility has given the company the manufacturing capacity required for large scale projects, specifically in the wind energy and automotive sectors. n

