
9 minute read
Global ambitions TWE Group
GLOBAL AMBITIONS
With a longlasting experience, the TWE Group is one of the world leaders in the development and production of nonwovens for a wide range of industry applications. Victoria Hattersley spoke to Hugo Christiaen, member of the management team of the TWE Group, to find out about the company’s production profile, a recent major acquisition and its plans for future global expansion.
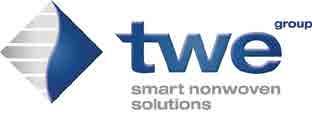
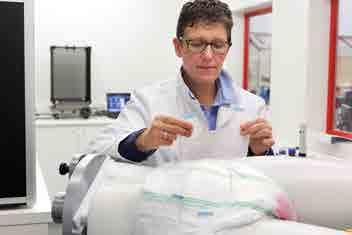
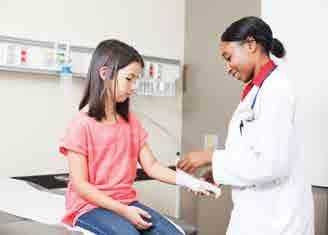
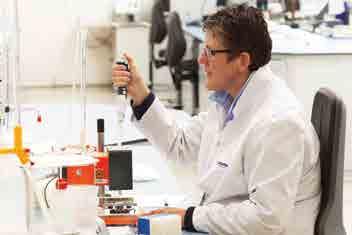
This year saw one of the most significant milestones in the TWE Group’s recent history, and a major step forward in its international expansion strategy, when it acquired the US company Vita Nonwovens (effective retrospectively from 1 January 2015). Vita Nonwovens LLC is a recognised manufacturer of nonwoven materials previously belonging to a private equity investor. It has sites in Fort Wayne (Indiana), High Point (North Carolina) and Schertz (Texas), with whose help it will expand the TWE Group’s expertise in the North American market.
According to Mr Christiaen, “Vita Nonwovens LLC’s core competencies – the development and manufacture of functional nonwovens always tailored to our customers’ requirements and produced individually – and the geographical locations of the three sites make the company a perfect member of the TWE Group. This will allow us to meet customer requirements even more efficiently in the future and set new standards for the quality of the TWE Group products. More than 1300 staff are now working hard together to make use of the development capacity and turn innovations into reality.”
Background and structure
Before going on to look at the products and innovations TWE offers to its customers throughout the world, it’s worth pausing to take a look at its current structure. Originally established in 1912, it has seen its most significant growth since the late 1990s. After the acquisition of various companies in Germany in this decade, a production facility was set up in China in 2007.
This was followed, in 2012, by the acquisition of the Belgium-based nonwovens producer Libeltex. Mr Christiaen tells us: “This was especially important because before this point TWE was only really present in Germany, but after this it had a broader European presence. And now, with the acquisition of Vita Nonwovens, it has gone all the way from being a smaller German group to an international player.”
Today, the group has a total of 12 plants across Germany, Belgium, France, Sweden the US and China. Its total revenue amounts to around €400 million and it employs more than1300 people (including the 200 recently added from the US acquisition).
Production technology
The world of textile production is divided into both traditional textiles and nonwovens, the latter of which has only been in existence for around 30 years. Today TWE focuses solely on nonwovens and continues to lead the field when it comes to pioneering, innovative products and technologies.
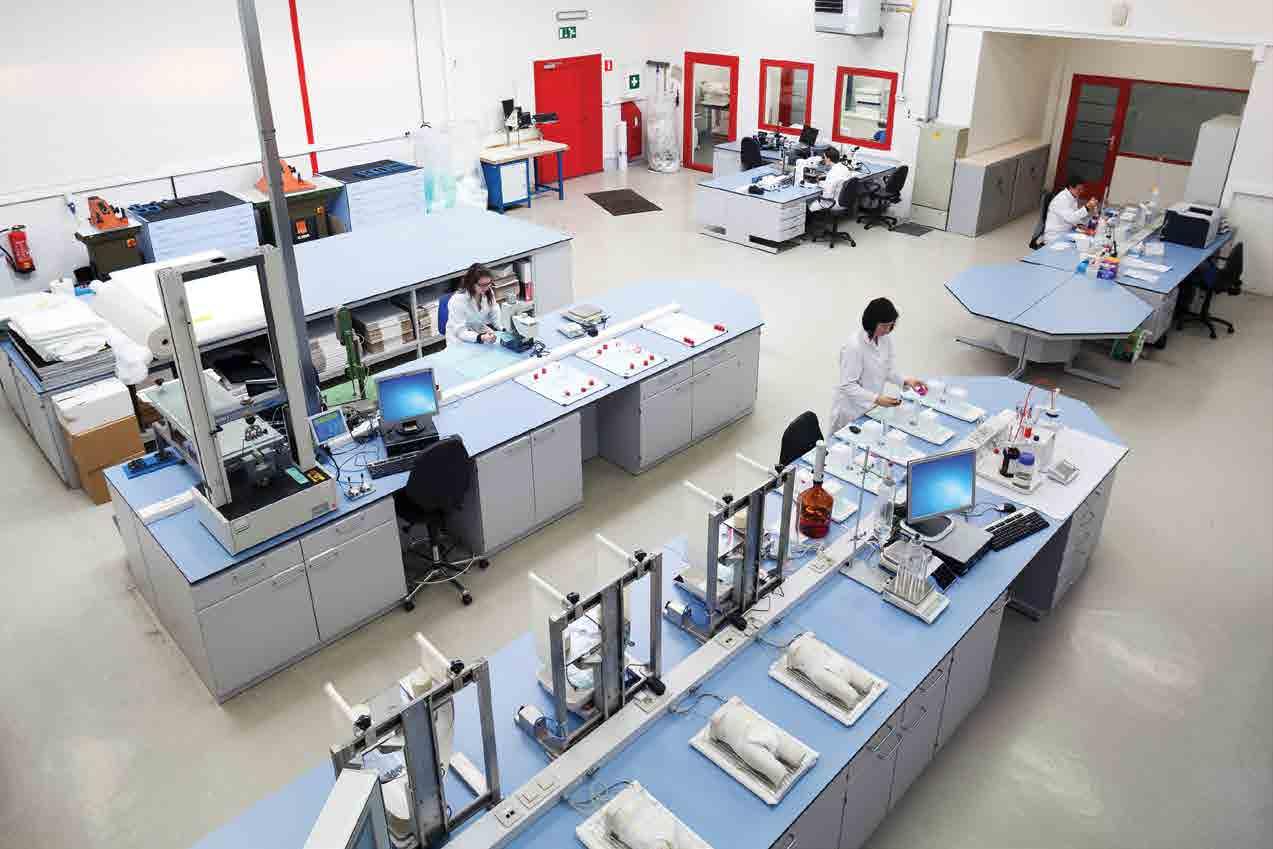
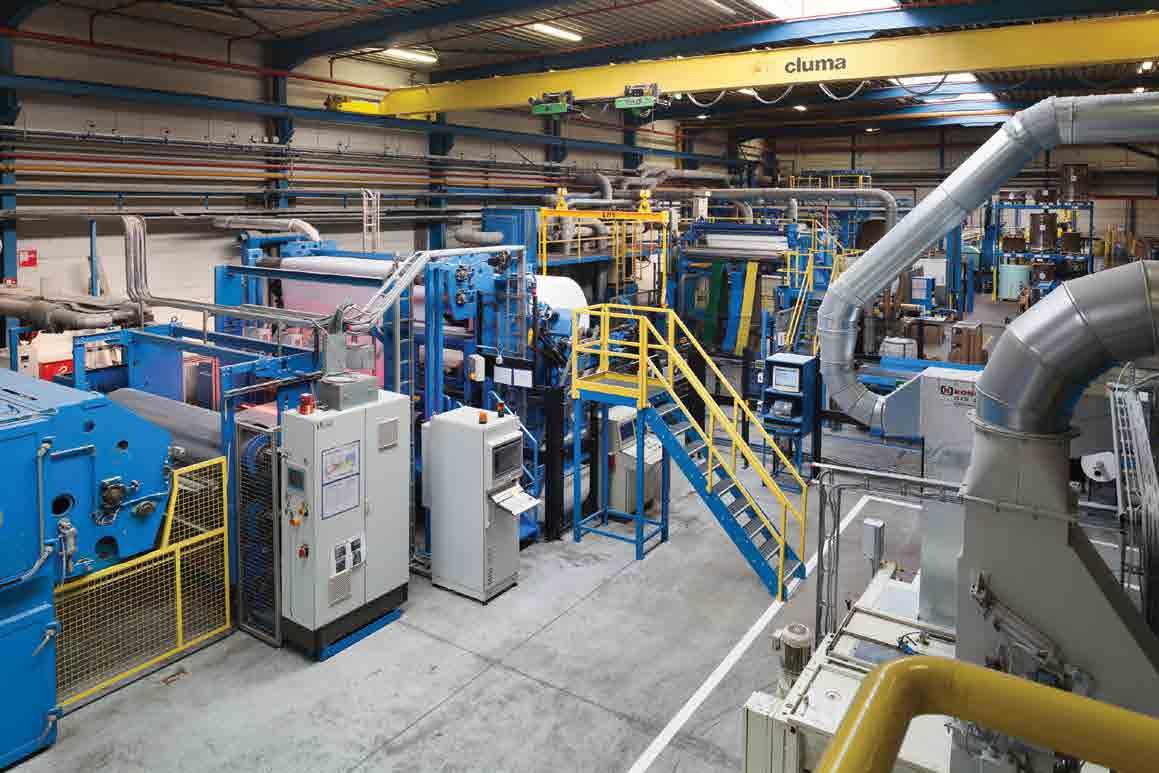
The production of nonwovens takes place in three basic stages: web formation, web bonding and finishing treatments. Within these there are three different web formation methods – drylaid, spunmelt and wetlaid – although TWE only focuses on drylaid. There are many different bonding methods, including chemical, thermal and mechanical. According to Mr Christiaen: “We use all of these bonding methods at various points but not all of them are used at every one of our plants.”
Production profile
The TWE Group’s nonwoven products fall into seven distinct application groups: Hygiene, Medical, Mobiltech, Filtration, Building & Construction, Wipes and Comfort. For the first of these, Hygiene, the company produces mainly unique three-layer ‘Slimcore’ ADL (Acquisition Distribution Layers) as well as top sheets and back sheets for baby, femcare and adult incontinence products. Its products enable customers to produce considerably thinner diaper layers, reducing transportation costs and providing a competitive edge.
For its Medical nonwovens, TWE focuses on three areas: OCP (Orthopaedic Cast Padding) bandages, wound care products and disposable gloves for hospital use. It is, for example, one of the European leaders in wash clothes, with highly advanced needlepunched nonwoven production facilities.
When it comes to its Mobiltech division, TWE mainly serves the automotive industry where its products find hundreds of applications. As technical components its nonwovens (produced under brand names including Caliweb, QuietWeb and AeroFil) can soundproof, seal and filter. They can be placed in car boots, used for seat heating products and much, much more besides.
The Filtration division has two main enduse areas: air filtration and liquid filtration. Products can provide secure filter action and durable performance in spray booths, vacuum cleaner bags and filters, kitchen hoods and so on. Meanwhile, in the Wipes division, TWE produces a wide variety of household cleaning wipes in many colours. The group is able to meet even the most stringent customer demands when it comes to anti-bacterial features, coating and refining processes.
Building & Construction is playing an increasingly important role in the TWE Group’s overall production portfolio. When it comes to this, it would probably be quicker to list the areas of the home in which its nonwovens aren’t used, so many and varied are its applications. To put it as succinctly as possible, the group offers solutions for effective thermal and acoustic insulation in all areas of the house, both interior and exterior. To give just one example, Mr Christiaen tells us: “In swimming pools in France it is common not to use tiles but PVC. But in
TWE Group Management, Jörg Ortmeier (COO) and Ralf Berens (CCO) Hugo Christiaen, member of the management team of the TWE Group
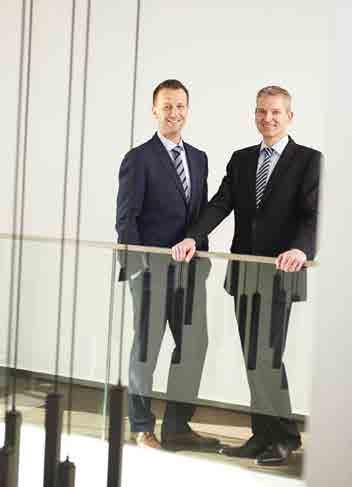
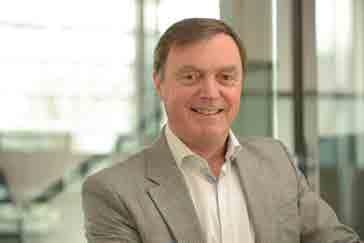
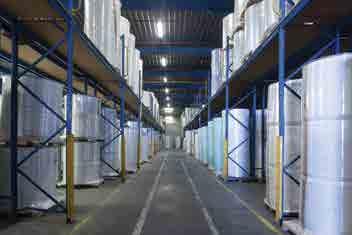
order to protect the PVC foil you have to put a protection layer in-between that and the ground. That is where we come in.”
The final division is Comfort. Here TWE makes nonwovens for three separate application areas: furniture, bedding and apparel. Under its Isosoft label, the company offers a broad spectrum of durable and sustainable insulation with high performance when it comes to weight, coating, layer structure and fibre strength. As an example, it might make the layer that sits between the leather and foam cushion on a sofa.
Within each of these units, Mr Christiaen tells us that “we can do both standard and customised products but more and more we are finding we have to customise them. R&D is therefore very important for us if we want to remain successful for years to come. We need to be inventive and come up with new solutions so we work very closely with both our customers and suppliers to come up with the right products.”
All TWE’s production plants are certified according to the ISO 9001 standard. In addition, its German plants hold 50001 energy management certification and the group is working on rolling this out across all its global sites in the near future. The emphasis the company places on quality can be seen from the fact that it regularly receives prestigious awards: For example, in 2014 it won a coveted Ontex Award for ‘Excellence in Customer Service’.
The group regularly attends some of the world’s leading trade shows in order to showcase its products and solutions. For example, in March this year it was present at Filtech and also exhibited at the Bau building & construction show in Munich. Later this year it can be found at Techtextil in Frankfurt, where it will be concentrating mainly on its Mobiltech and Construction business areas. The week after they will exhibit at the Anex fair in Shanghai.
Continued leadership and quality
As a leading global player, TWE is aware of the need to continue expanding its footprint in order to offer a better service to its clients. The above-mentioned US acquisition will allow it to do just that, by increasing the number of products it is able to offer this market.
Mr Christiaen explains the reason for this: “For some of our products, logistics costs are an important factor. For example, when it comes to our Hygiene and Mobiltech products, which are very lightweight, we can supply anywhere in the world – even as far away as New Zealand. But for areas such as our Comfort products, the logistics costs are much higher which restricts us in terms of where we can sell them. Establishing production bases in strategic locations is the obvious solution. We want to strengthen our presence in Asia and the US and at the same time we will continue to streamline our operations and look for synergies. It’s a two-pronged approach.”
He concludes by describing the current business ethos of the group: “In recent years we have moved firmly away from purchasing raw materials based on price alone and are now focusing only on higher added-value products. We’re not a ‘bread and butter’-type business, as innovation and meeting customer demands is more important to us than price. We build on strategic partnerships: that is how we will continue to survive and indeed thrive in this environment.” n
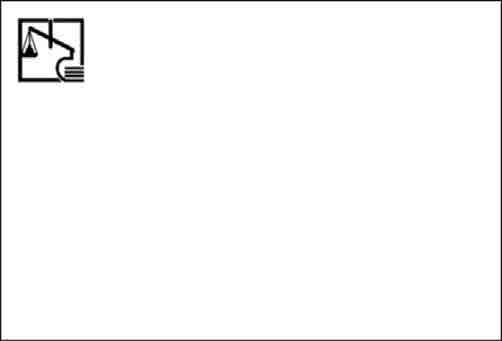


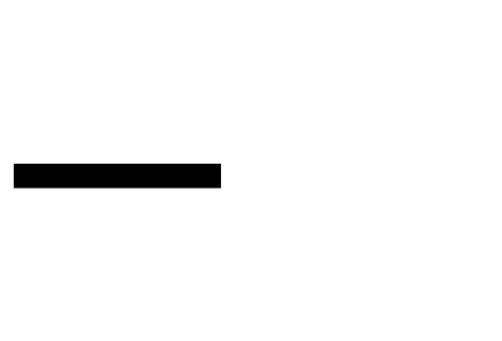
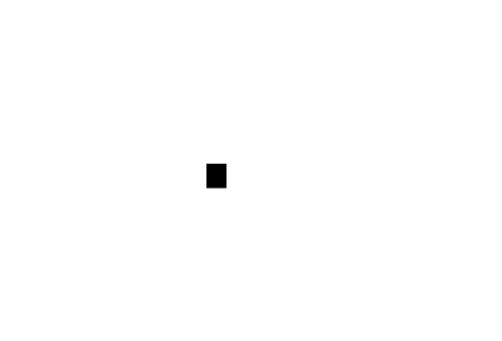
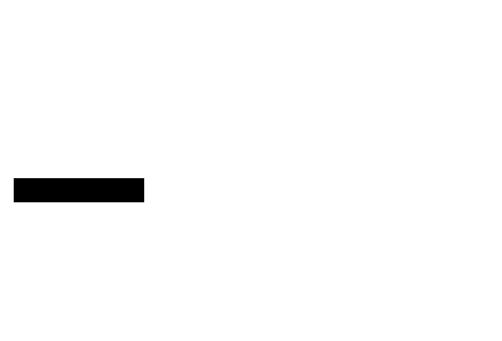

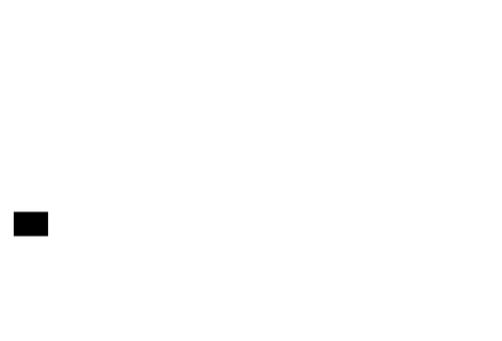
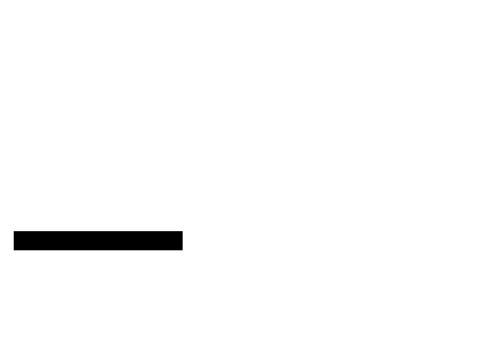
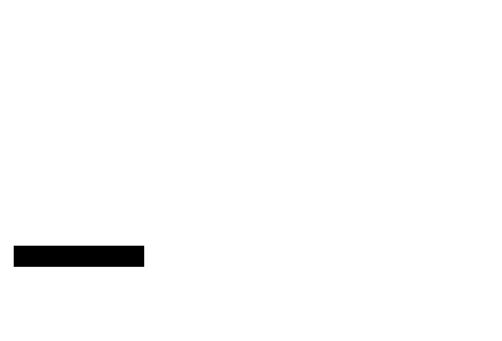
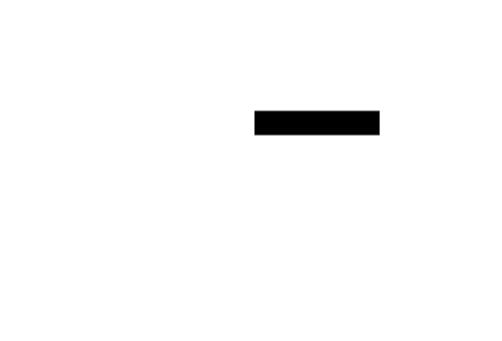


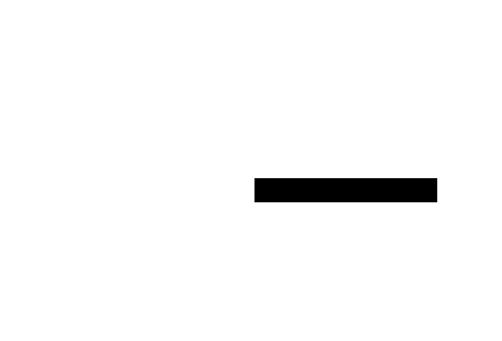
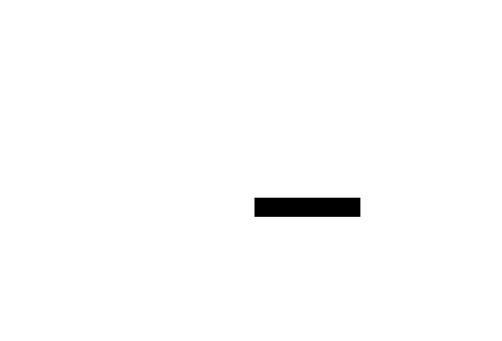

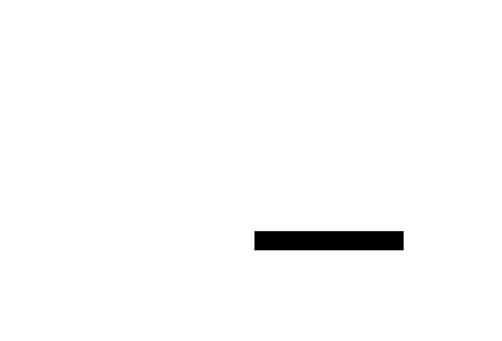
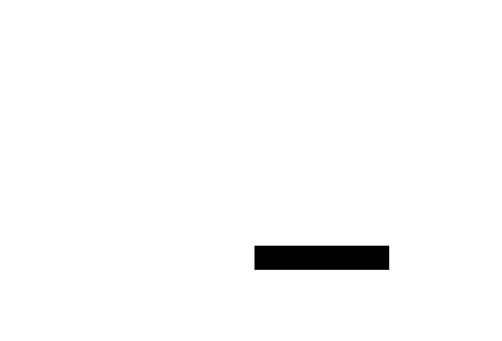
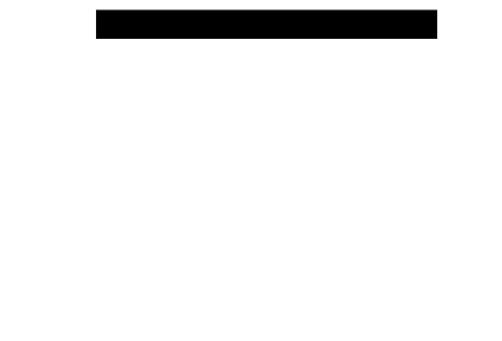


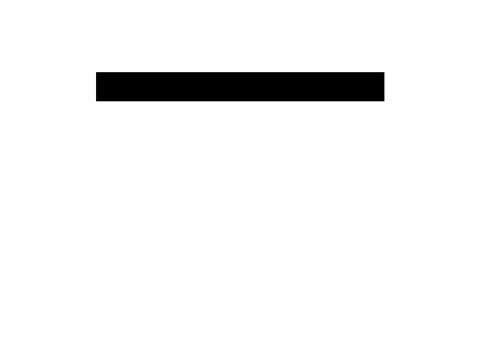
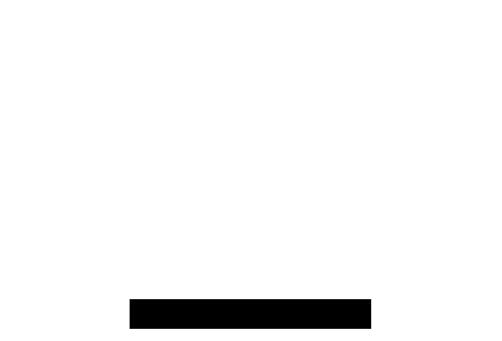
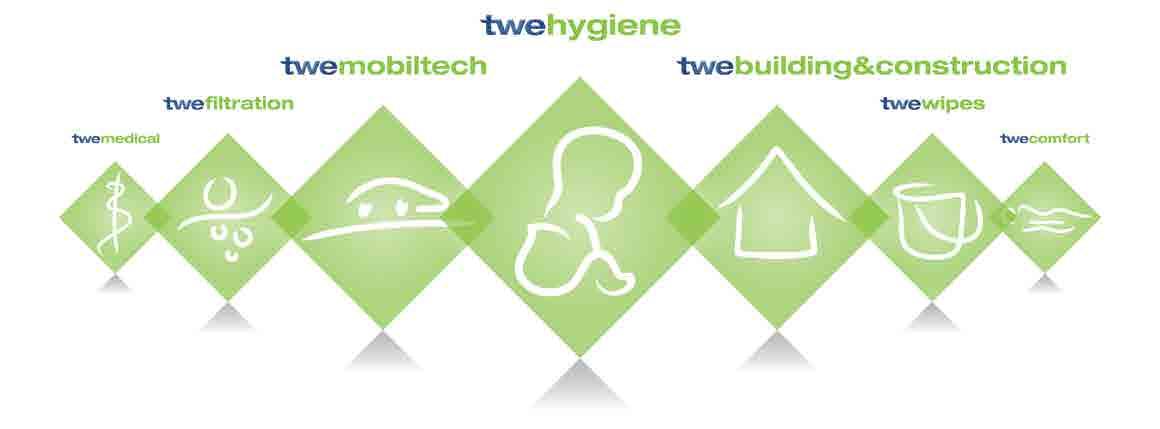