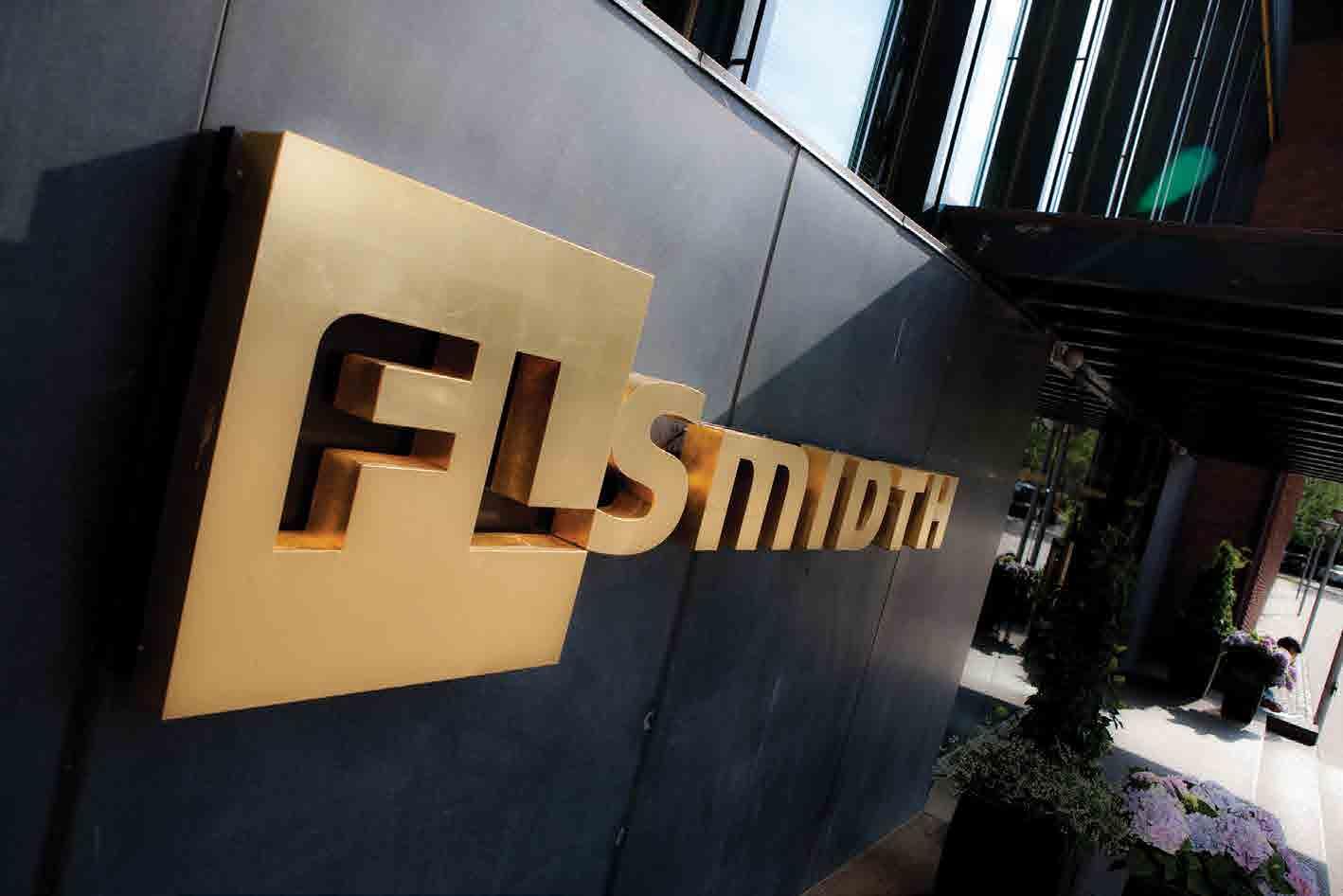
8 minute read
A one-stop solutions provider FLSmidth
A ONE-STOP SOLUTIONS PROVIDER
FLSmidth is a leader in the supply of equipment and services to the global cement and minerals industries. Industry Europe reports on the company’s core expertise and recent contract wins.

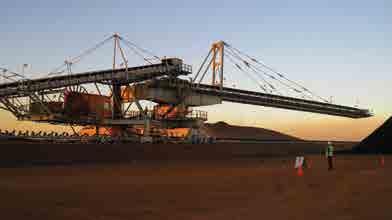
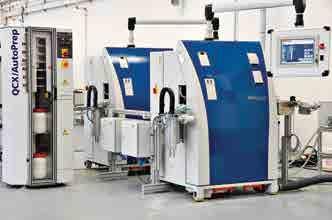
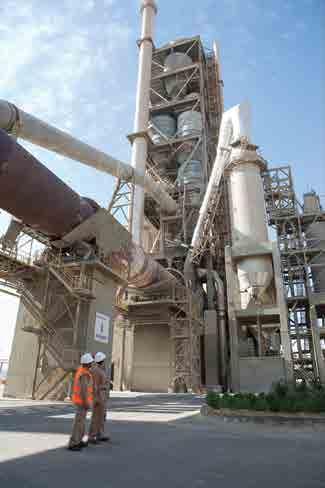
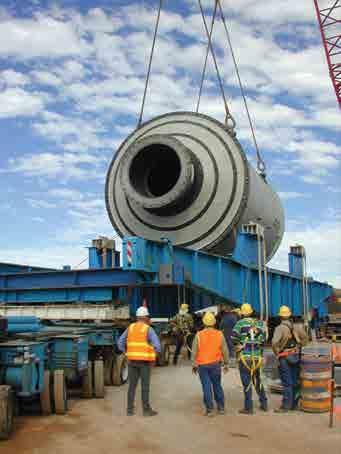
FLSmidth won its first contract for a cement plant, near Limhamm in Sweden, in 1887. Today the Danish company supplies the cement and minerals industries globally with engineering, single machines and complete processing plants as well as comprehensive maintenance and support services that range up to the complete operation of customers’ processing facilities. FLSmidth currently offers its full service solutions in six core focus industries: cement, coal, iron ore, copper, gold and fertilisers; its technologies and services range from material handling in the quarry through the entire processing operations of the end product.
Headquartered at Valby, near Copenhagen, a site it moved to in 1956, FLSmidth today employs more than 15,000 people all over the world.
Until the later part of the 20th century the company was focused on designing and producing machinery for the cement industry. It introduced the coal-fired rotary kiln to the European market at the end of the 19th century – an innovation from the USA that revolutionised cement production – and by the 1950s FLSmidth machinery was used in 40 per cent of all cement production in the entire world. In the following years the company continued to introduce new machines and processes that reinforced its position as a technology leader in the industry, including the ATOX vertical mill, which combined the grinding, separation and drying processes into a single unit. Since the 1980s FLSmidth has sold more than 300 ATOX mills.
Refocusing and expansion
Then, following the economic recession of the 1980s, FLSmidth began to diversify into a number of other businesses until it had grown into a group of some 125 companies in which two thirds of sales were in non-core activities. However at the beginning of the 21st century it was decided to dispose of the group’s nonstrategic interests and refocus on the development and production of equipment, production plants, systems and services for the global cement and minerals industries. This return to the company’s roots was marked in 2006 when it was awarded a contract by Holcim to supply the world’s biggest cement production line at Ste Genevieve, Missouri, in the USA.
At the same time the company began a series of strategic acquisitions that would enable it to expand its services into the minerals industries. Perhaps the most important of these was the acquisition in 2007 of the process division of the Canadian company GL&V, consisting of Dorr-Oliver Eimco and Krebs Engineers. The expertise in separation equipment for the metals and minerals industries that this purchase brought to the group enabled FLSmidth to offer customers the entire flow sheet of a typical minerals plant, from raw material extraction to the final end product.
As an example of its work in this area, in March this year (2015) FLSmidth received a contract worth approximately €30 million from the Moroccan phosphate and fertiliser producer Office Chérifien des Phosphates (OCP) for the supply of material handling equipment to a port facility and mine site in Morocco.
The order covers supply of equipment, supervision of erection as well as commissioning. The equipment to be supplied includes three bucket wheel reclaimers, each with a capacity of 2000 tonnes per hour, two stackers with a capacity of 2000 tonnes per hour, two stackers with a capacity of 1000 tonnes per hour and finally associated yard conveyors.
“Our strategy is to be the leading single-source supplier in all the industries we serve,” explains a company spokesperson. “We have built up this position in the cement industry over many years and, thanks to our strategy of key acquisitions, we can now offer the minerals industry the same complete service. In fact today around one third of our business is in the cement industry and two thirds in industries such as copper, gold, iron ore and coal.
“Our continued expansion has been reinforced by the global branding strategy that we adopted in 2009 – ‘One Company – One
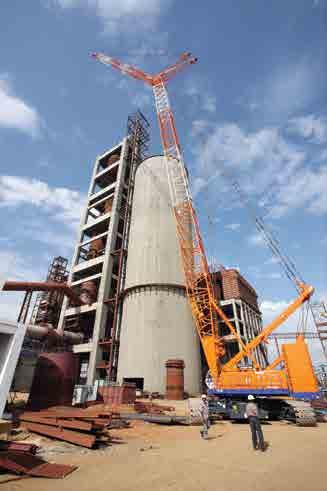



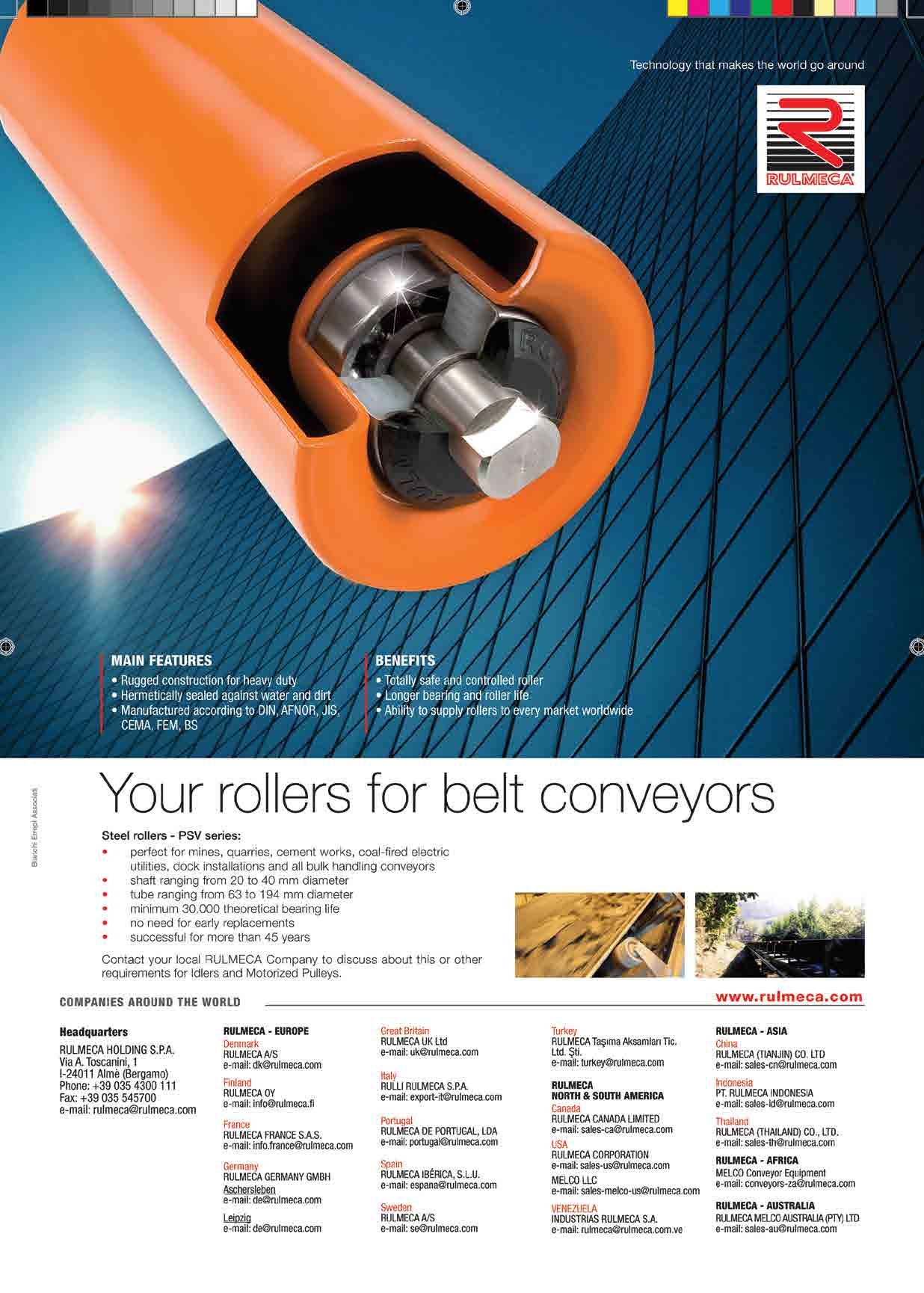
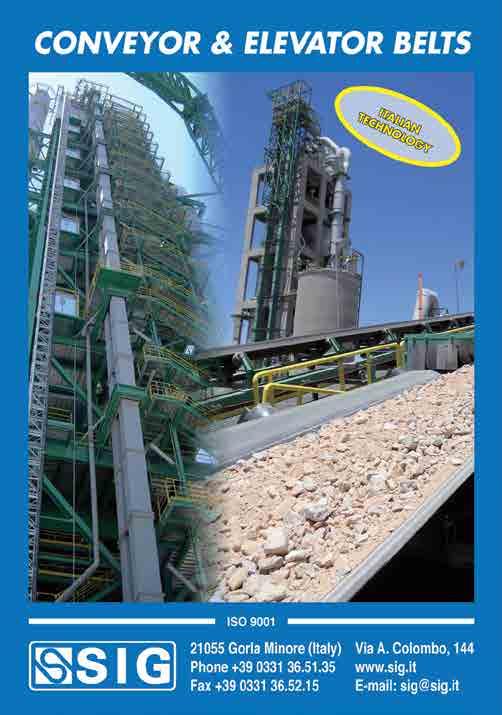
Name – One Source’ – highlighting our position as a supplier of the whole value chain to both the cement and the minerals processing industries. So customers in the copper industry, for example, can now source from us everything they need for the complete processing operation – equipment for crushing, grinding, filtration, flotation, material handling, screening, thickening and even for sampling and on-line analysis.”
Global leader in cement
FLSmidth’s has over 130 years of experience in guiding large and small cement plant design and construction around the world. Its ‘one source’ strategy enables it to offer customers everything from process design and project management to equipment supply and commissioning, even including training for the operators who will run the plant.
A recent example of a project for the cement industry, announced in November 2014, was an EPC (Engineering, Procurement and Construction) contract which the company signed with one of the world’s largest cement producers, CEMEX, for the supply of a new cement production line to be installed at CEMEX’s Odessa cement plant in western Texas, USA. Once the installation is finished, the cement line is expected to have a capacity of around 2540 metric tonnes per day.
The expansion will utilise state-of-the-art production technology resulting in higher fuel efficiency and improved productivity. The equipment scope includes a 5-stage ILC preheater with a Low NOx Calciner, 3-pier kiln, FLSmidth® Cross-Bar® cooler, Duoflex® burner, Pfister® weighing and dosing systems, gas analysers and three Fuller-Kinyon® pumps. Furthermore, an FLSmidth control system will ensure the most efficient operation.
We are located in Romania, Resita, a city with an old industrial history, and many manufacturing possibilities.
We manufacture: • Welded assemblies • Steel structures • Rubber and metallic rubber vulcanised parts • Machined parts
We have the following certifications: ISO 9001:2008, DIN EN 15085-2, EN3834-2, and we are approved by the Romanian Railway Authority for the manufacture of vulcanised parts.
We can be reached at telephone 004.0255.213.817 and e-mail plastomet@plastomet.ro
Proud to be Flsmidth suppliers.
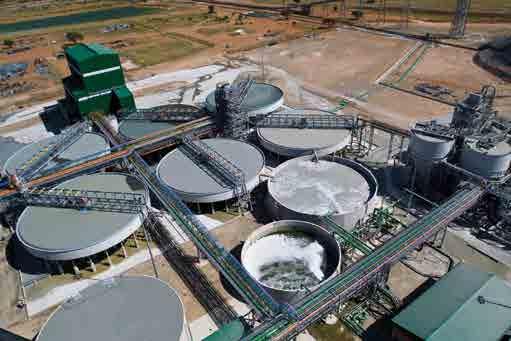
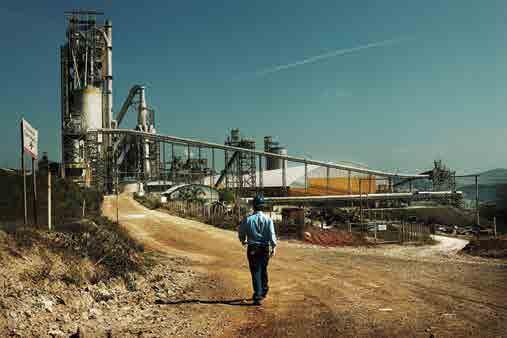
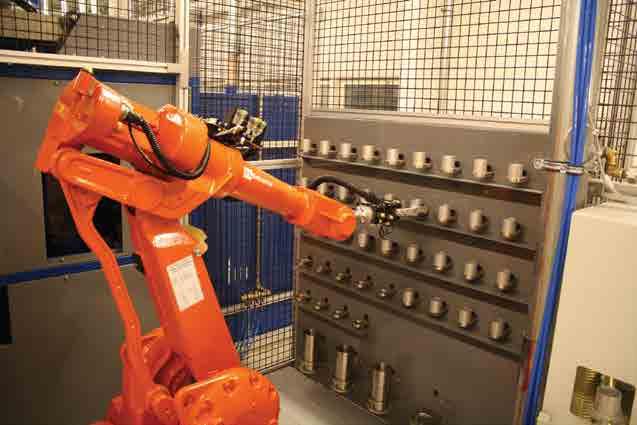
WEAR RESISTANCE
The Delhi Iron pillar stands rust free for more than 3000 years. Exceptional wear protection technology of ancient India.
The ancient Indian blacksmiths mastered the art of wear protection to protect the Delhi Iron pillar and other such monuments from the hazard of nature for over 3000 years.
At Reitz India, we continue this age-old tradition of expert wear - protection. We protect our fans from their highly abrasive and corrosive environment with the use of wear plates made from alloys of Chromium, Nickel, Molybdenum, Vanadium, Manganese and Tungsten Carbide to protect the surfaces and increase the lifespan of the Fans.
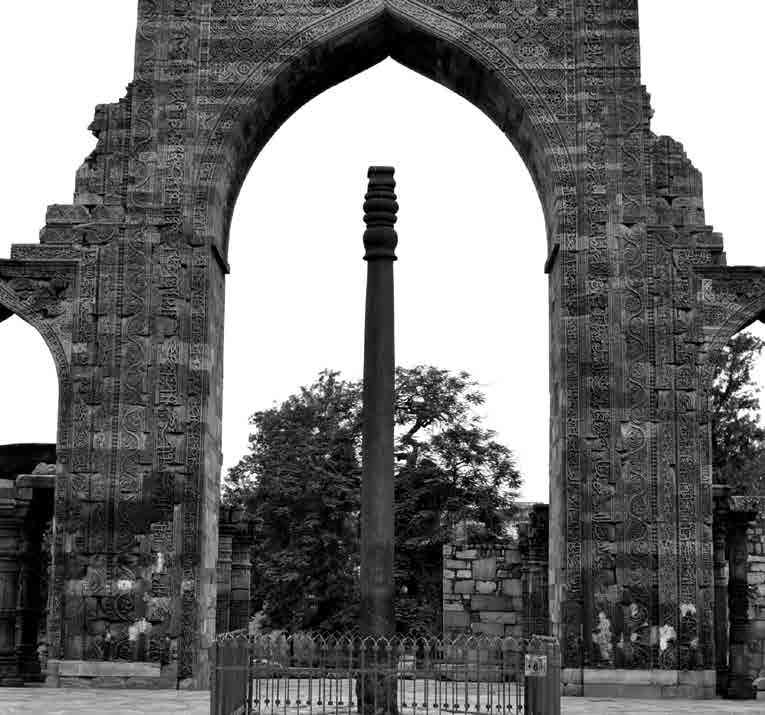
Reitz India Limited VII Floor, Block - A, Q City, Gachibowli, Nanakramguda, Hyderabad - 500046, India. Phone: +91-40-4488 1888 Fax: +91-40-4488 1899 E-mail: info@reitzindia.com
www.reitzindia.com
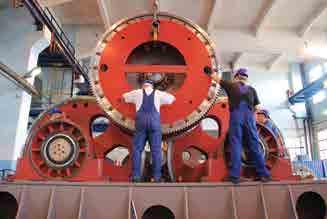

This contract was followed the next month by another contract from CEMEX to supply a 2800 tonnes per day cement production line to be installed at their new Cementera del Magdalena Medio S.A.S. cement plant. The plant is located in the department of Antioquia, approximately 135 km from the capital of Antioquia, Medellin.
The line will use the latest production technologies and achieve high environmental and quality standards. The department of Antioquia is a region in Colombia that is expected to see an increase in cement demand resulting from continued economic growth as well as planned investments in infrastructure.
Cutting edge technology
In all its business areas FLSmidth leads the way in improving environmental protection through cutting edge technology and optimised product manufacturing, fabrication and installation.
“Our R&D activity is a huge part of the business we carry out inhouse and our Dania R&D Centre in Denmark is the largest facility of its kind in the industry,” says the company spokesperson. “Cement production is, of course, extremely energy intensive so a lot of our work in recent years has been in improving energy efficiency but we are also putting a lot of effort into reducing emissions. Our HOTDISC combustion system was introduced 15 years ago but it remains a highly effective process for burning alternative fuels in a controlled and environmentally-friendly manner. It can burn all forms of solid waste, from sludge or grains to huge used tyres or large pieces of timber such as old telephone poles and so turns otherwise useless and environmentally challenging solid waste into useful energy in a completely a safe and economical way. Most new cement plants today are equipped with this technology.”
FLSmidth is also an industry leader in the development of air pollution technology and offers a wide range of solutions to reduce particulate matter and gaseous emissions. With more than 8000 systems installed worldwide, the company is a one-stop source for helping customers comply with environmental regulations all the way through from project development to after-sale services. FLSmidth is also leading the way in waste heat recovery systems. Its Kalina Cycle technology is a unique system that uses a binary working fluid of ammonia and water to achieve improved heat transfer and higher efficiency. The system is ideally suited to the waste gas streams of the pre-heater and clinker cooler vent of a cement plant. n
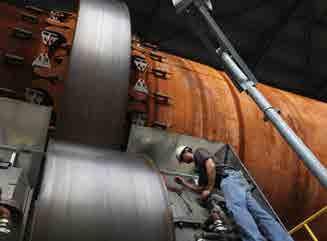