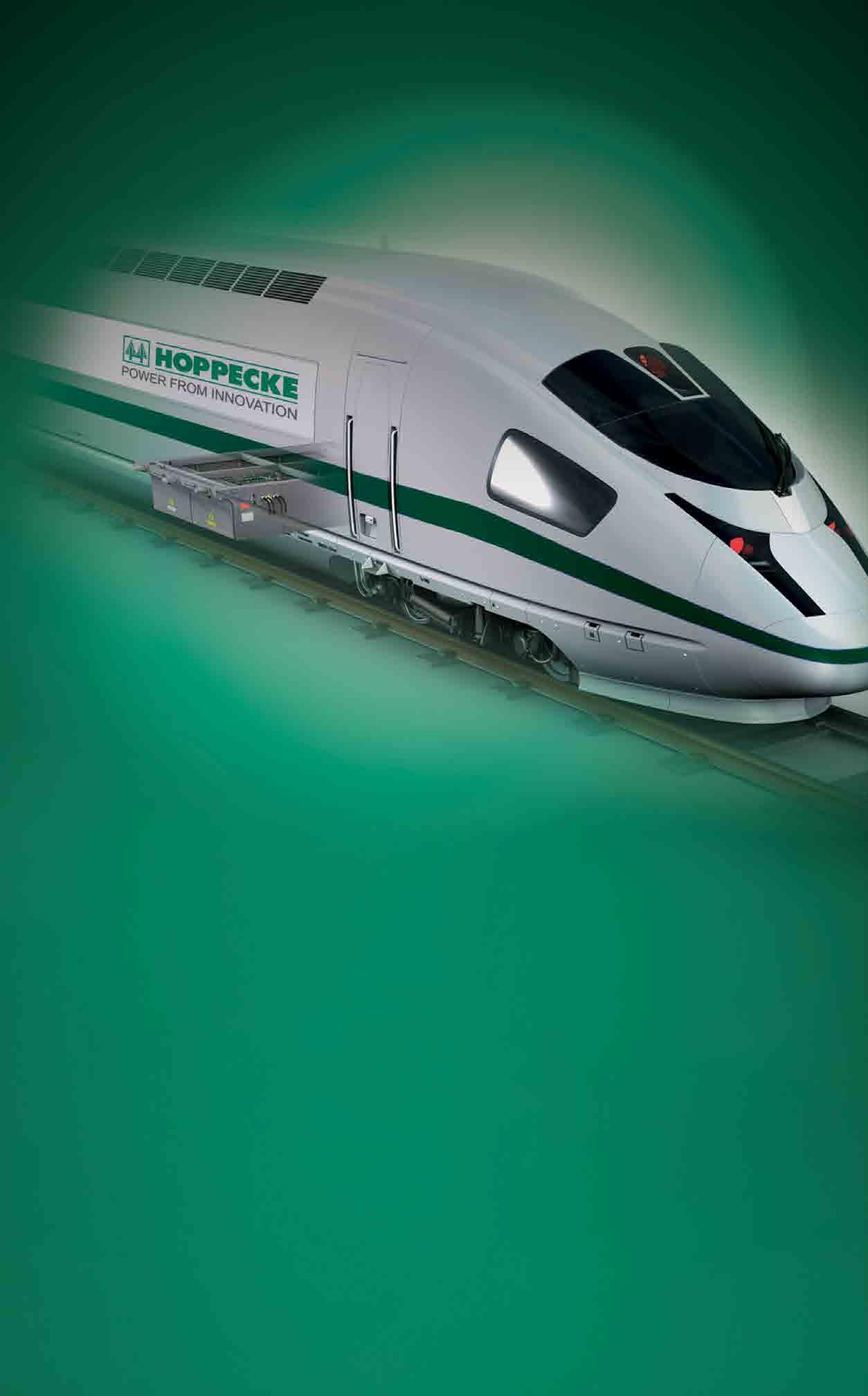
5 minute read
Rail power supply systems Hoppecke
RAIL POWER SUPPLY SYSTEMS
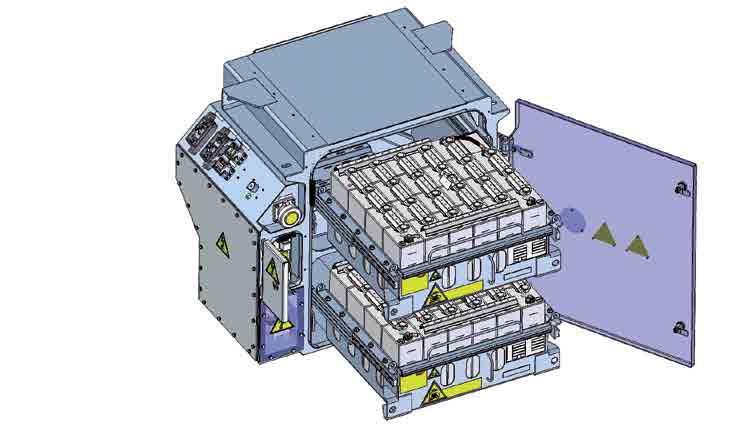

Hoppecke Batteries’ Rail Power is part of the company’s Special Power Systems division. Rail Power develops and produces power supply systems for trains. Marco Siebel spoke with Hans Peter Czernietzki, sales director of the company’s business unit Rail Power, about the company’s €10 Million investments in the USA, the company’s new three-story office building in Germany, and the latest market developments.
HOPPECKE Batterien GmbH & Co. KG was founded in 1927 by Carl Zoellner, who named the company after the nearby river Hoppecke, in central Germany. The company is still family run by the fourth generation owner Marc Zoellner. Turnover in 2014 was €340 million, generated by 1980 employees.
Hans Peter Czernietzki begins: “About 40–45 per cent of turnover is generated in Europe, 50 per cent in Asia and Africa, and between 5–10 per cent in the USA. We expect to reach the €500 million turnover mark within the next five years. We currently have one production facility in the USA, two in China, and three in Germany. As planned, we expanded our production facility in the USA in 2014; instead of renting we now own a new production facility.”
Hoppecke has six production facilities in Germany, and one in the USA. It was in Brilon where Hoppecke first produced special alkaline batteries on a fibre-structured basis, in a joint enterprise with two major German car makers. In 2011 Hoppecke opened its technology centre in Zwickau, between Munich and Berlin.
Mr Czernietzki adds: “In 2015 we inaugurated a new three-story office building at our headquarters in Brilon, where we have now concentrated our sales and production management. Our research department is still based in Zwickau.”
Hybrid trains in Germany
Germany is operating the first hybrid shunting locomotive fleet throughout Europe. The Hoppecke powered vehicles are less noisy compared to conventional diesel shunting locomotives and save about 40 per cent on fuel and 60 per cent on emissions. The hybrid vehicles contribute to the Deutsche Bahn’s climate protection programme 2020. Hoppecke’s 6.5-tonne batteries deliver the clean power the European Union’s environmental CO2 targets demand: Germany voted for a law aiming at reducing CO2 emissions by 50 per cent from 1990 base level by 2020.
Mr Czernietzki says: “We are obviously happy with the trend of hybridisation of outdated diesel run rolling equipment. The first testing agreement with Deutsche Bahn was signed in 2010 within the frame

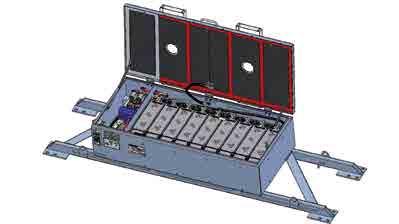
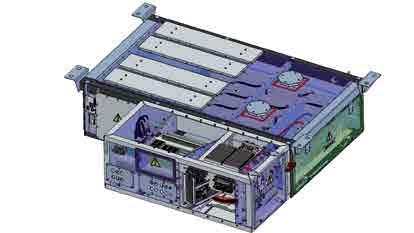


of the Deutsche Bahn Green Logistic Programme. The aim was to fully replace the conventional shunting locomotives fleet with hybrid locomotives. Today we live in an era of converting old rolling equipment to hybrid technology, and we are in an excellent market position to provide rail services with complete battery systems using our unique lightweight FNC® technology.”
Fibre Nickel Cadmium technology
The Hoppecke Fibre Nickel Cadmium battery, FNC®, has been on the market for more than 30 years. The unique FNC® technology is based on metallised polypropylene fibre-structured mat, originally developed for very demanding applications such as aerospace as well as electric and hybrid vehicles. The carrier material for the active material is not a heavy and rigid metal, but instead a very lightweight, flexible mat. The highly dense, three-dimensional structure of the metallised fibre mat is so porous that 90 per cent of the volume of the fibre electrodes remains free for filling with active material.
Mr Czernietzki continues: “Hoppecke’s FNC® technology has the advantage of being lightweight and yet able to produce high to very high currents during discharge and charging at a low nominal capacity.”
The fibre-structured electrodes have a conductive nickel matrix into which the active material is filled using a specially developed process, without the use of additives such as graphite or iron, meaning that there is no oxidation possible. Consequently, no change of electrolyte is necessary throughout the operating life of the battery, in contrast to conventional NiCd batteries.
Hoppecke has supplied more than one million FNC® cells to its railway customers throughout the world. This success is based on
the many advantages offered by FNC® technology as compared with other energy storage systems. All Hoppecke FNC® cells for rail vehicles are manufactured at the Brilon site in Germany, which is certified to ISO 9001, ISO 14001 and DIN 6700 C5 standards. Today, Hoppecke continues developing special power products that allow high to very high currents, for the railway industry and the aviation and aerospace industries.
Complete solutions
Since 2001 Hoppecke has seen a ten-fold increase in turnover, and expects to increase its growth by selling complete power supply systems comprising FNC® cells with its crates or trays, battery boxes, and all the electrical components such as fuses, switches and diodes. In addition, for rail transport vehicles, Hoppecke offers battery chargers which may be installed inside or outside the battery box as desired.
Today, Hoppecke is the number one provider of complete battery systems in China. In the USA, Hoppecke batteries operate the subway trains of Miami and Honolulu. In terms of turnover, the European market provided the lion’s share of the €340 million generated in 2014, followed by China and then the USA.
Mr Czernietzki: “We see a bright future in both the hybridisation of rolling rail equipment and the development of complete battery systems. We are the only supplier in the world capable of equipping our battery systems with either lead-acid or NiCd batteries at our own production sites.”
Hoppecke’s other divisions are Motive Power Systems, covering the market for industrial trucks and driver-less transport systems, and Reserve Power Systems, protecting life and goods, and securing data around the clock.
Mr Czernietzki concludes: “Hoppecke is the only battery producer that has all four technologies in-house: lead, FNC® nickel-cadmium, NiMH and Li-Ion. This means that customers do not need to look for different power system providers; they find every technology they need to use at Hoppecke.” n
ULTRATEX
Nonwoven fabrics have a wide range of characteristics, many-sided functions and enormous potential! For over 30 years, ULTRATEX has been the preferred specialist in processing nonwovens.
Flexible production technologies, ultra-modern machines and innovative finishing characterise our enterprise. Heat and ultrasonic welding and sewing, punching, cutting, calendering, laminating, gluing and printing offer a wide spectrum for realising and implementing new ideas.
This gives rise to products for industrial packaging, filter applications, advertising materials, pillow cover, products for medical applications such as nonwoven covers for cold-warm compresses, disposable products for clothing in cosmetics and food packaging industries and other applications with demanding hygiene requirements.
As a medium-sized enterprise, ULTRATEX operates to an uncompromising standard of organisation and flexibility, enabling it to respond dynamically to market changes.
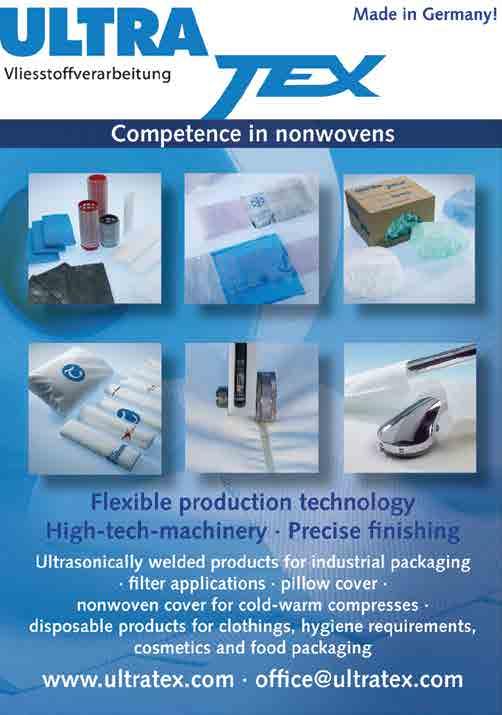