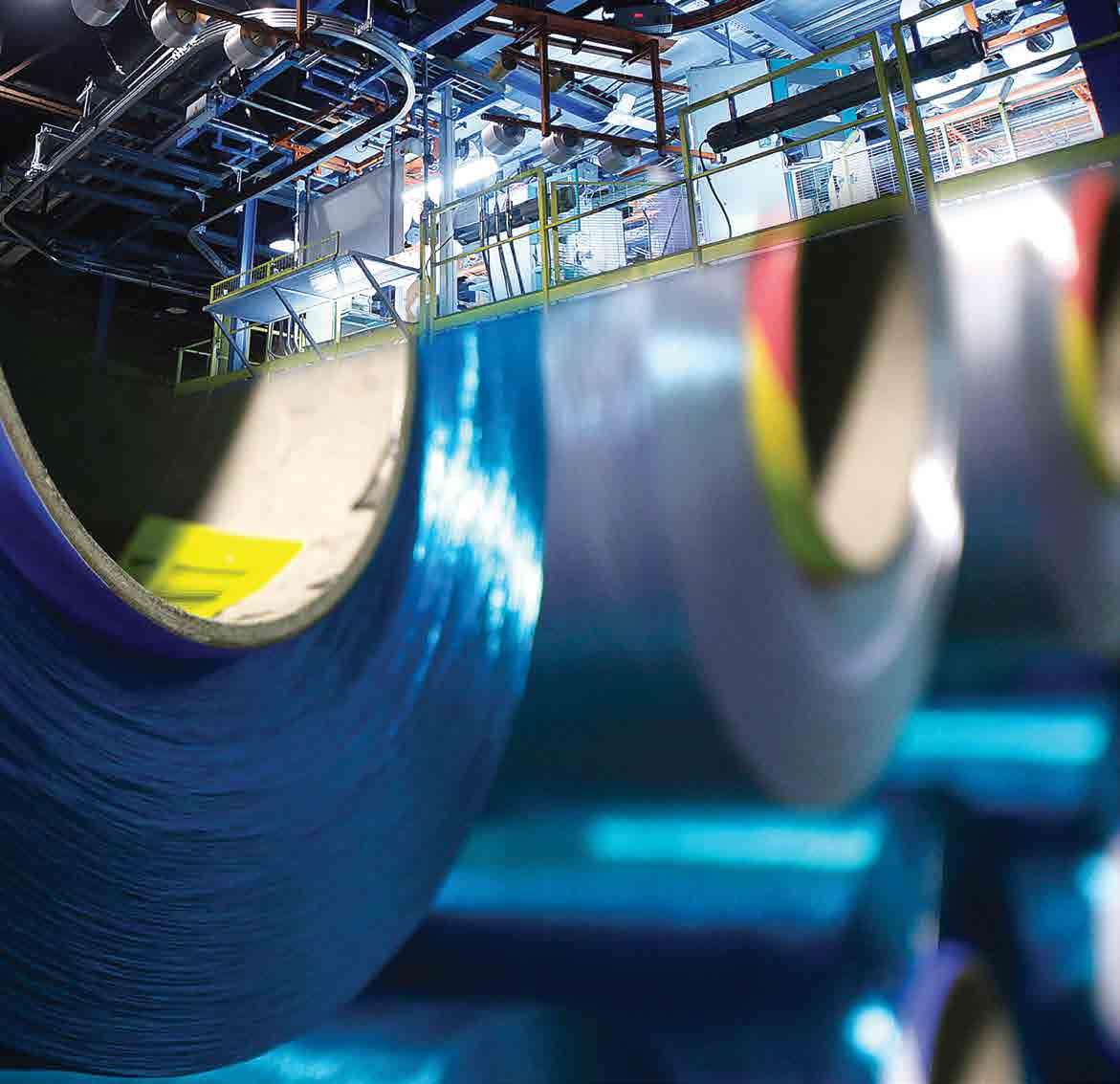
6 minute read
Sustainable innovation RadiciGroup
SUSTAINABLE INNOVATION
RadiciGroup is an Italian multinational with a long history and a strong focus on innovation and sustainability. Two of its companies – Noyfil SA and Noyfil SpA – are clear examples of this, as Barbara Rossi discovers.
RadiciGroup belongs to a wider industrial group, which also includes companies operating in chemicals, plastics, synthetic fibres and nonwovens sectors. RadiciGroup, whose establishment dates back to the 1941, has created a solid organisation on a worldwide scale, and has developed the highest possible degree of product technology. RadiciGroup’s strength is its vertically integrated nylon production. The Group is also a European leader in the production and processing of a wide range of polyester yarns. Here, its production control starts with the spinning process and reaches all the way down the chain through the various yarn processing stages.
Its products are the starting point for developments in the apparel, furnishings, automotive, consumer goods, construction, electrical and electronics, household appliances and sport sectors. In 2014 the Group consolidated sales revenue was €1025 million.
Innovative and green
Today innovation and sustainability must truly go hand in hand in a symbiotic relationship. For this reason, the group is totally focused on these issues. Indeed, it incorporated these concepts into its companies long ago and has cultivated them ever since. As mentioned, the group is an Italian multinational with diversified businesses focused on chemicals, plastics, synthetic fibres and nonwovens; and a strong global presence in Italy, the rest of Europe, North America, South America and Asia. “In all the businesses in which we operate,” said Filippo Servalli, marketing director of RadiciGroup, “we have adopted an approach to sustainability based on system-wide, rigorous measurements of the environmental, economic, human rights, labour practices and decent work performance, society and product responsibility indicators, as per the Global Reporting Initiative guidelines. The premise is that we can manage only what we can measure.”
He continued: “The strategy we have adopted for sustainable product development is three-pronged: biopolymers, particularly bio-polyamides, partially or totally obtained from renewable source materials; post-industrial recycling; and eco-design, a new approach to product design that takes into account the environmental impact of a product throughout its entire life cycle.”
Noyfil SA and Noyfil SpA
Two RadiciGroup companies, Noyfil SA and Noyfil SpA, respectively located in Switzerland and Italy, offer two clear examples of this sustainability practice. Their know-how and total control of their production chain, from spinning to downstream processes, make the Noyfil production and processing sites capable of optimising and customising the performance of their yarn to customer specifications or target market requests. They cover everything from outdoor furnishings to marine, medical, industrial, apparel, automotive and geotextiles. All these are market sectors in which sustainability is becoming more and more essential. “During the past few years, our reduced environmental impact yarns have shown a positive growth trend,” said Daniele Dossi, site quality manager of Noyfil SA. “This holds true for our r-Radyarn® and r-Starlight® yarns, 100 per cent made from post-consumer recycled PET bottles; and CornLeaf yarn, made from polylactic acid biopolymer – a 100 per cent natural material made from renewable vegetable resources. CornLeaf is biodegradable and will decompose into mature compost.”
He continued: “After measuring and calculating the environmental performance indicators for all our polyester yarns using the Life Cycle Assessment method, in September 2014 we chose
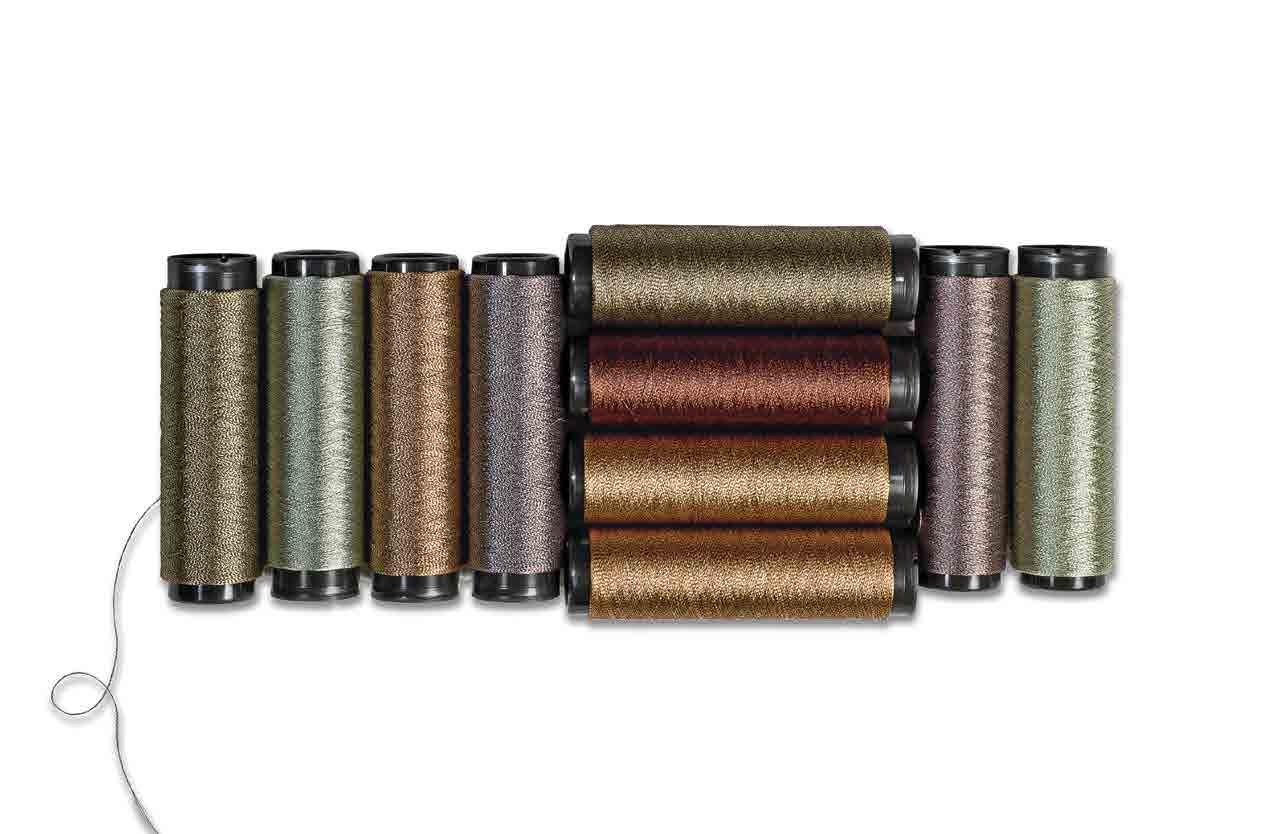
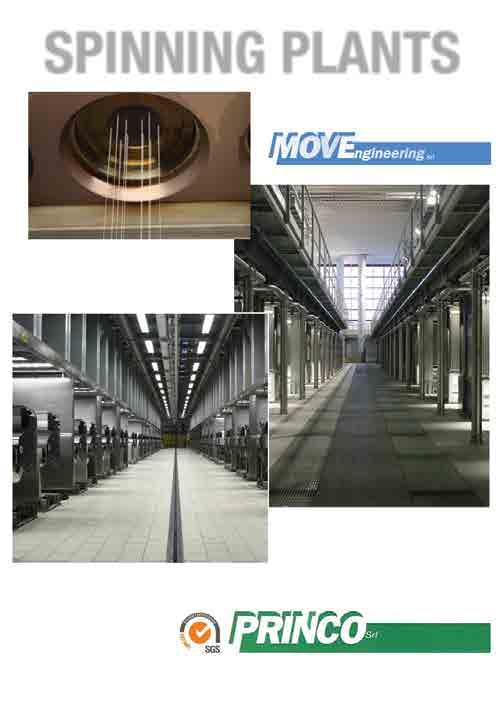
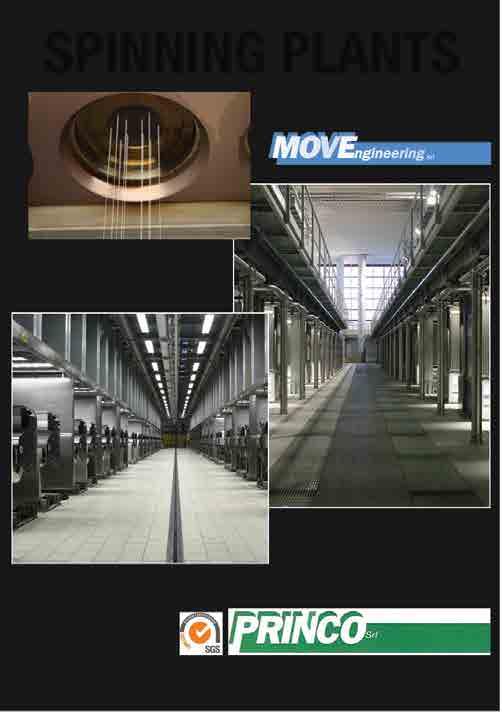
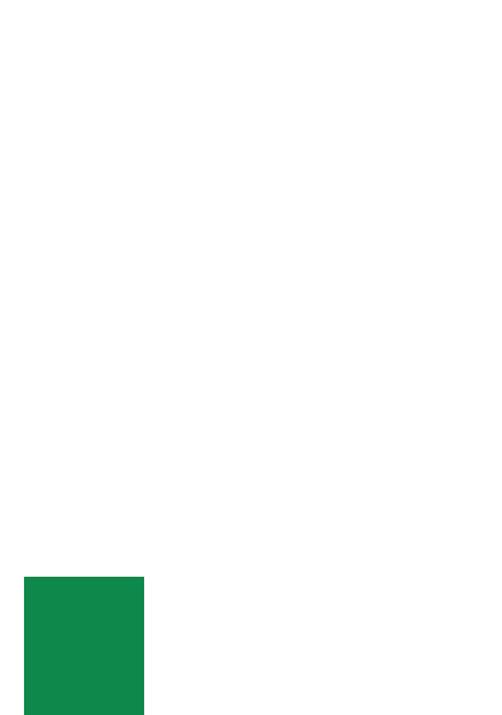


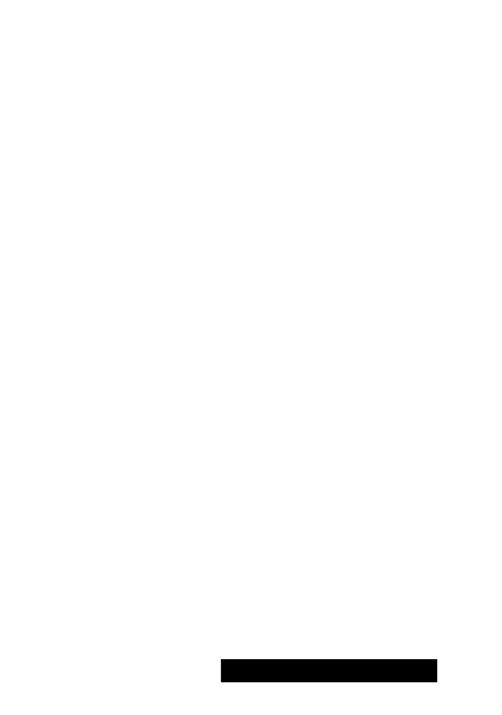
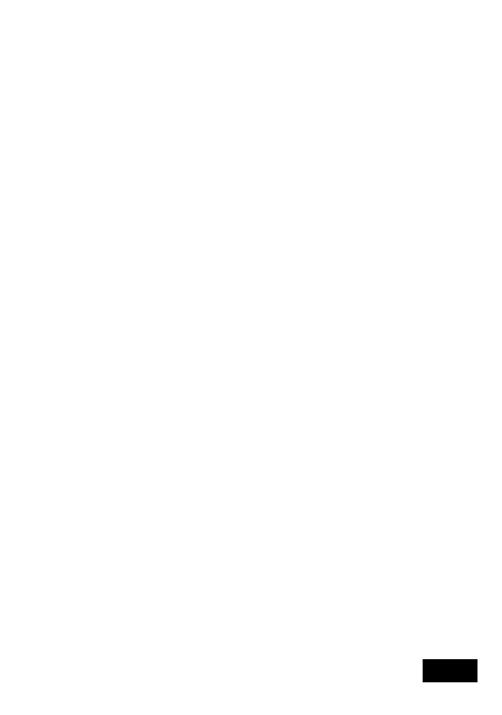
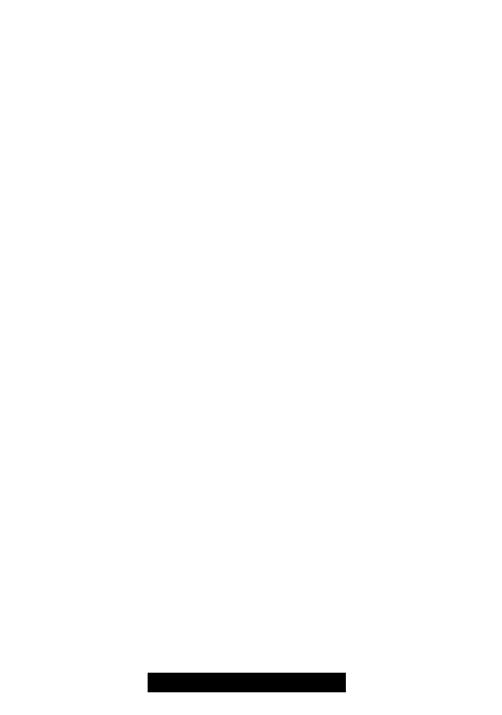
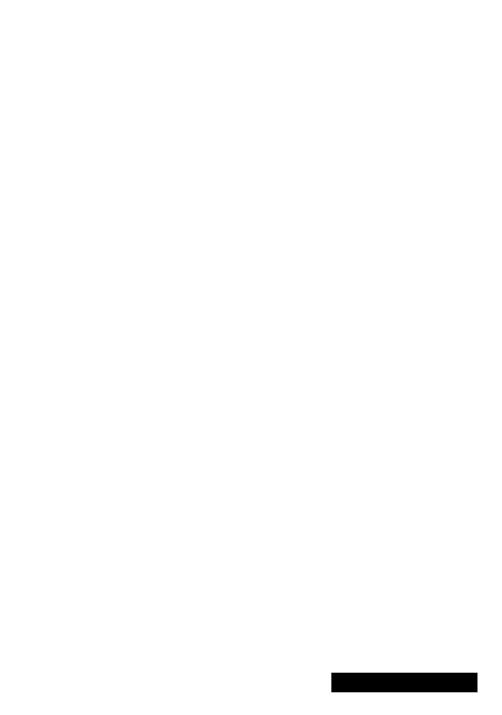

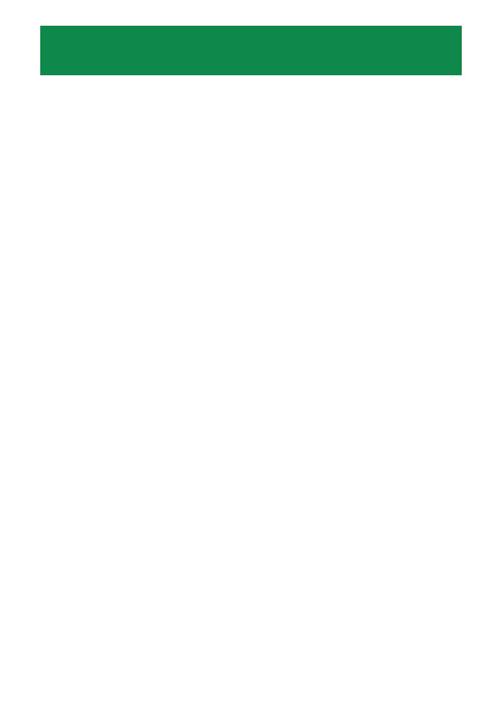
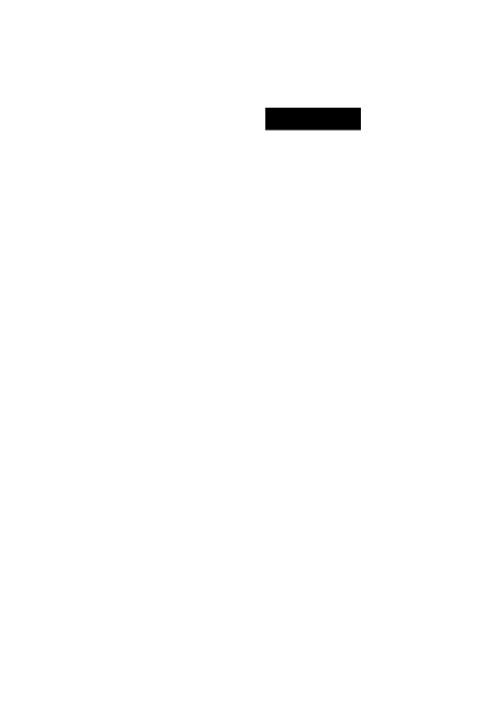

PRINCO SRL
PRINCO SRL, in cooperation with its sister company MOVEngineering, supplies engineering services and equipment for man-made spinning factories suitable to produce “no touch quality yarn” (production without any manual handling of the bobbins) through POY, FOY and FDY processes.
In the production of PA6 and PA6.6 PRINCO has realized important and big projects both in Italy and foreign countries. In the last years we have focused our attention also in the PET and PBT yarn production.
In the field of polymer filtration PRINCO produces Hypox® Filter, a continuous polymer filter with cleaning in situ.
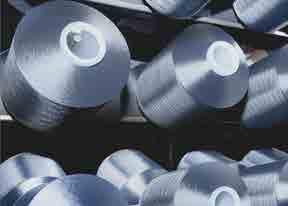
www.leitsu.com
The LEI TSU group is one of the European leaders in continuous yarn processing. All of its production takes place in Italy, in two plants based in Lombardy.
For over 30 years the company has specialised in continuous polyester processing, fi rst only as a twister and then also as an air texturizer, as well as a kdk and fancy yarn manufacturer.
LEI TSU produces and distributes over 500 different continuous polyester products (raw-white, yarn-dyed or mass-dyed) which it sells all over Europe, Turkey and the Maghreb.
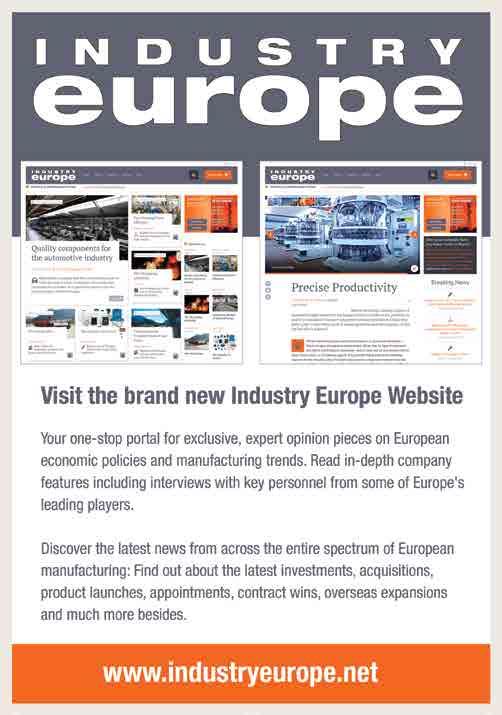

the highest level of transparency and clarity by adopting the UNI 11505:2013 standard for measuring and declaring the recycled material content in r-Radyarn® and r Starlight® yarns. UNI 11505:2013 is the standard that establishes the requirements for the disclosure of recycled material content in man-made fibres. Disclosing the precise content of recycled material in fibres means providing users with all the elements needed to calculate the exact composition of their own finished products and giving end consumers more information, which can be found directly on the label. This certification was an important step for us and our commitment to sustainability.”
The r-Radyarn® and r-Starlight® yarns, which are 100 per cent made from post-consumer recycled PET bottles, are sustainable in several tangible ways. They add value to waste, cut down on plastics disposal in landfills, make people aware of the importance of separate waste collection and decrease the energy used in production processes, thus reducing emissions of CO2 gas. Furthermore, the solution-dyed versions of these yarns allow for a significant savings in water consumption compared to traditional dyeing processes. Another yarn produced by Noyfil is CornLeaf, which is made from polylactic acid (PLA) biopolymer and ensures full eco-compatibility in terms of reduction of CO2 emissions and water and energy savings. CornLeaf is available in a wide range of solution-dyed lightfast, wash-resistant colours. It combines the advantages of natural fibres with those of synthetics: light weight, tenacity, comfort, UV resistance and safety.
Water is a natural resource that needs to be preserved: Noyfil can colour its yarn by solution dyeing, a technique that reduces the amount of water used, thus saving this precious resource. The yarn is dyed and functionalised during the initial extrusion stage and does not require further conventional downstream dyeing and finishing processes. This allows for significant savings in water consumption and a reduction in the pollution load. But that is not all. Solution dyeing and solution functionalisation also allow for substantial energy savings. n
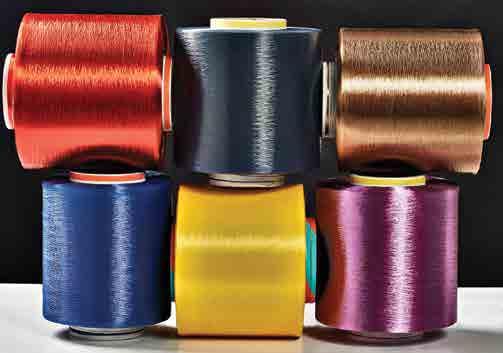
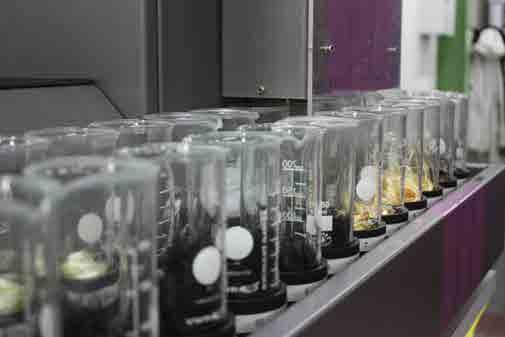