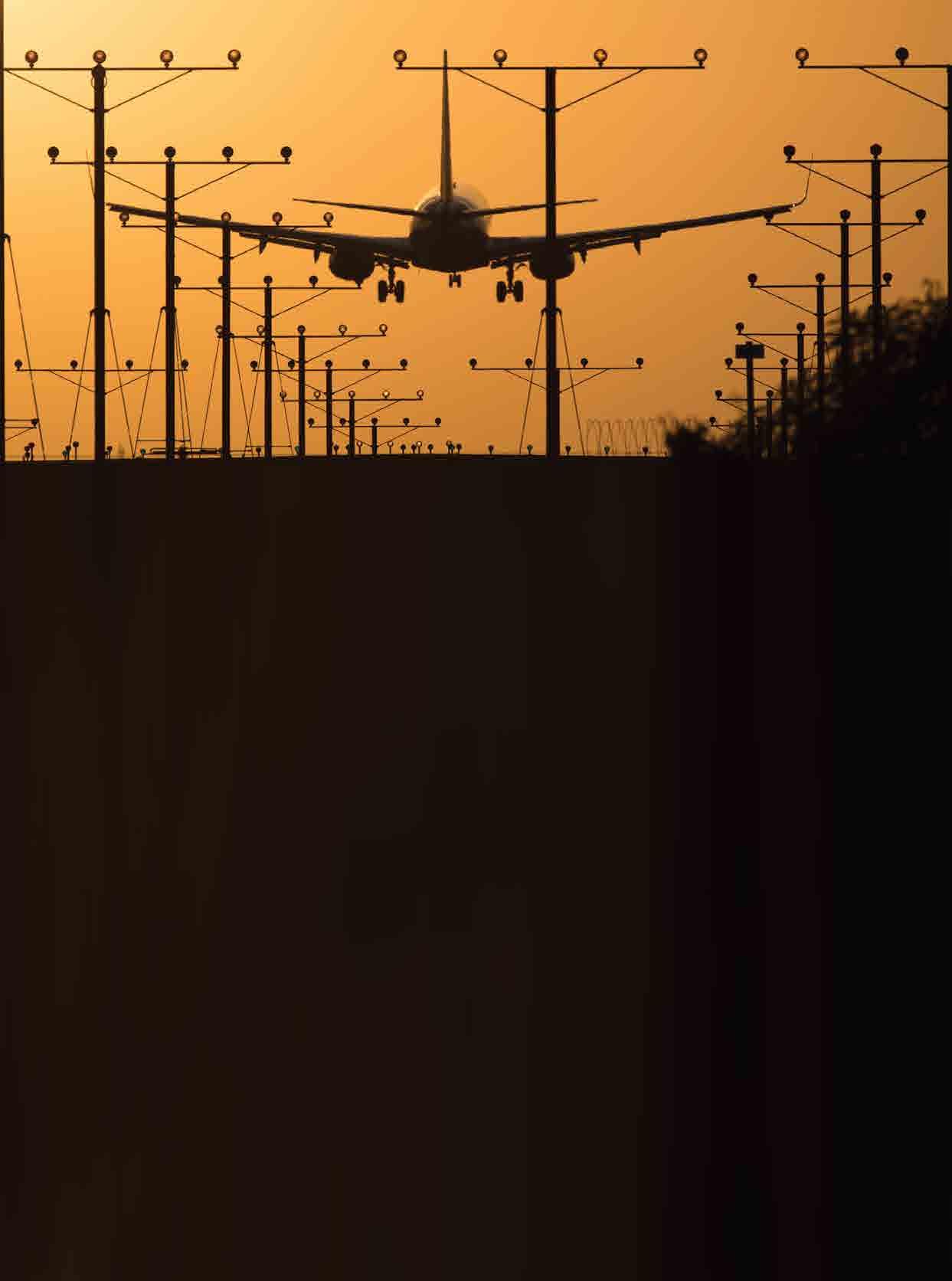
4 minute read
Flying high Asco
FLYING HIGH
Asco is a leading world-class designer and manufacturer of high-lift structures, complex mechanical assemblies and major structural components for the aerospace industry. Philip Yorke looks at a company that provides some of the world’s most innovative avionics solutions and continues to expand its product portfolio and technological capabilities.
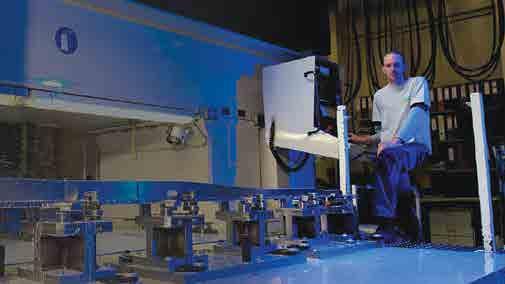
ASCO Industries NV is a global leader in the development, manufacture, treatment and assembly of steel and titanium high-precision components for the aerospace industry. The company’s product portfolio includes wing-flap actuation systems, engine mounts and landing gear components. Asco Industries was founded in 1954 and is headquartered in Zaventum, Belgium
Today the company operates from four key locations – Belgium, Canada, the USA and Germany – with over 1300 employees and a turnover exceeding €250 million. Asco also produces more than 2500 assemblies each month and is dedicated to becoming the world leader in the design and manufacture of high lift devices for the aerospace industry.
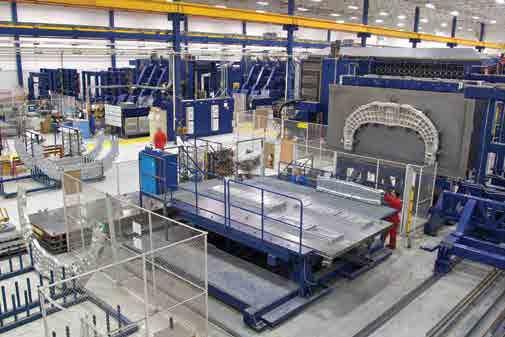
A passion for precision
Asco is constantly seeking new and innovative technological solutions in order to support its customers’ individual requirements. A continuous programme of research and development and long-term partnerships with clients and academia, as well as its own award

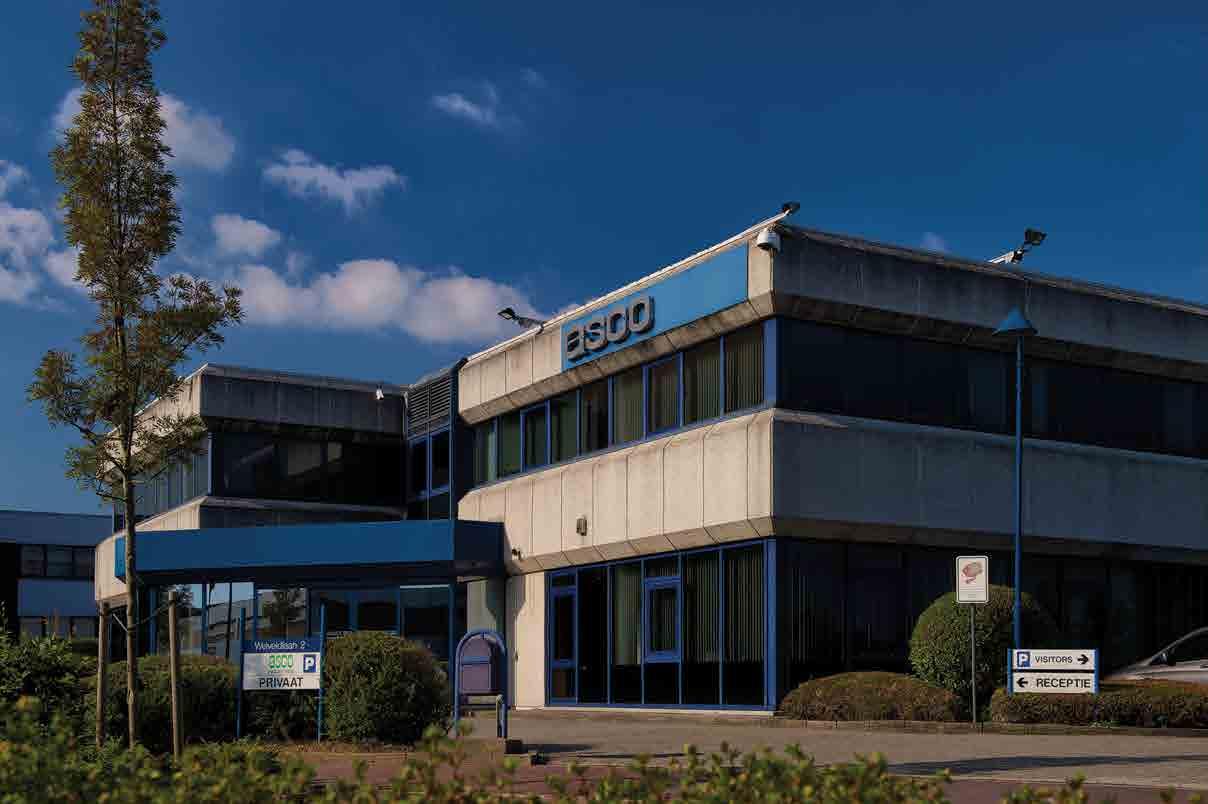
winning products, have helped to secure Asco’s place as a major global player within the international aerospace community. Asco firmly believes that precision in the aerospace industry is all about a continuous focus on detail, while keeping the big picture in mind. This is why it places a high priority on driving its quality management systems and procedures to meet the highest levels of international standards and legislation.
Asco’s engineers continuously enhance the excellence of their products, which are designed to meet cutting-edge applications for high lift devices and complex structural assemblies, while at the same time working towards achieving greater sustainability and an ever greener environment.
As a result of over 60 years of engineering excellence, Asco is known throughout the aerospace industry as a world-class designer and manufacturer of high technology operating systems for the slats and flaps on aircraft wings, as well as for many other complex assemblies and structural components. The company’s passion for precision keeps it ahead of its competitors and can be found throughout its manufacturing processes.
Building on success
Asco is always working to build upon its enviable market position as the global leader for ‘high-lift devices’. These include deployment mechanisms and support systems for a wing’s movable leadingedge slats and trailing edge flaps. The company works continuously to improve the aerodynamics of an aircraft, resulting in improved fuel economy and a reduced overall ecological footprint. This is why Asco is the industry’s preferred partner for the design and supply of enhanced lift and landing solutions for the majority of the world’s commercial aircraft fleets.
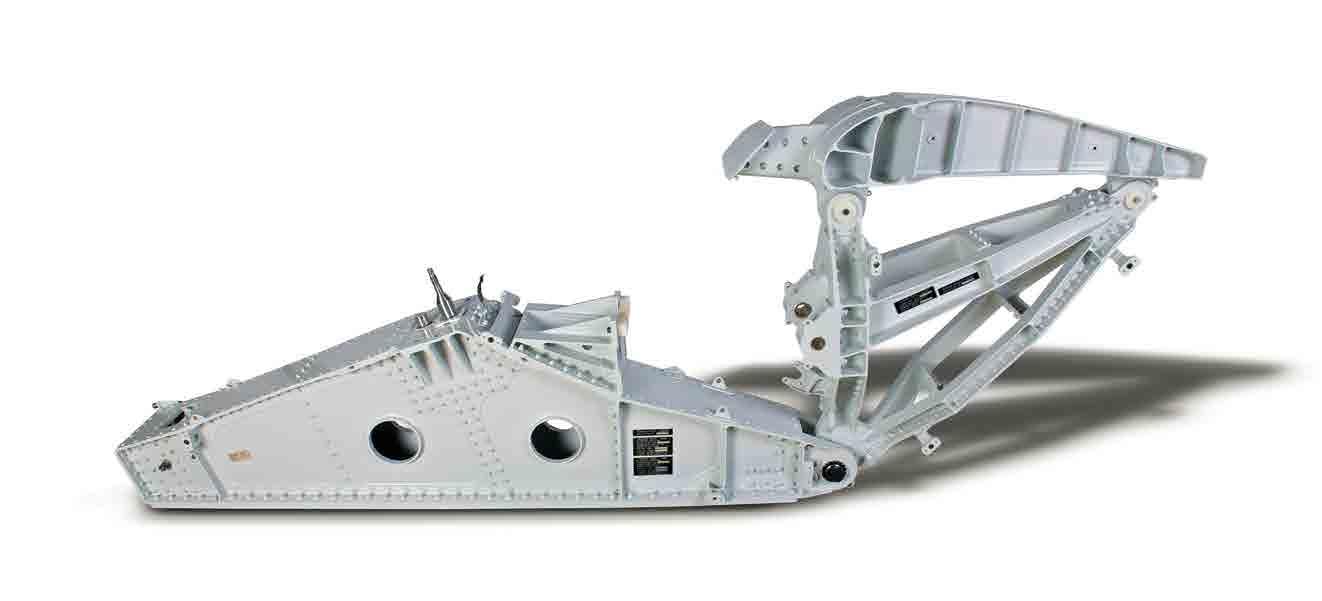
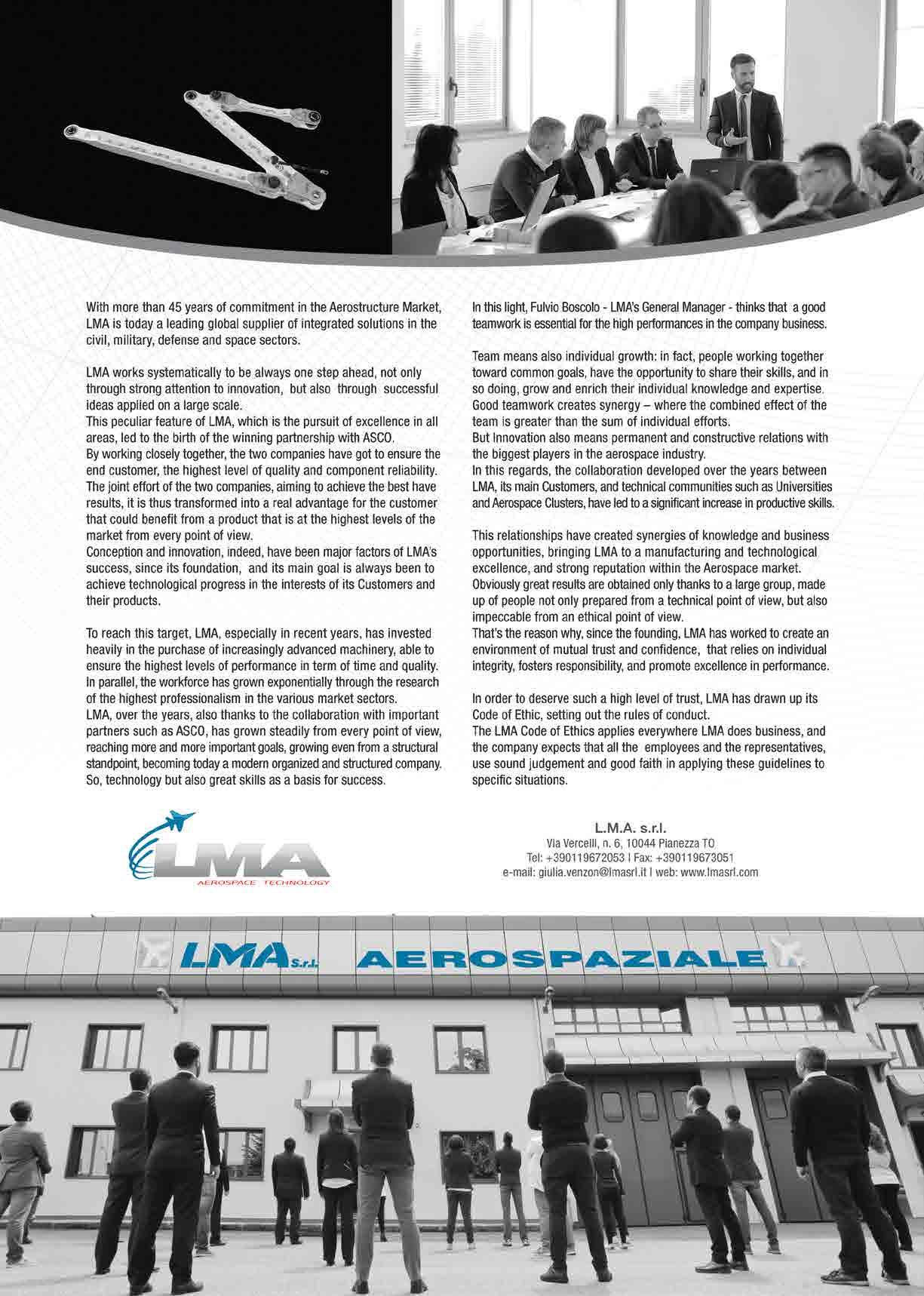
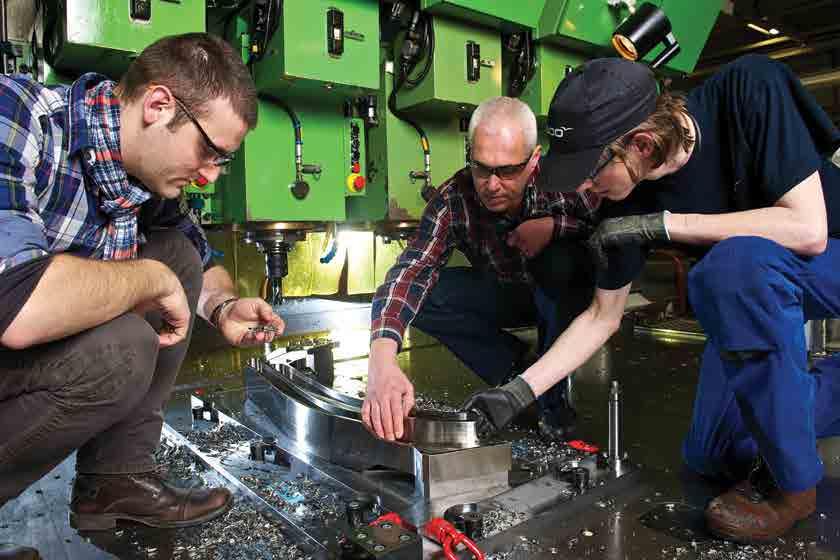
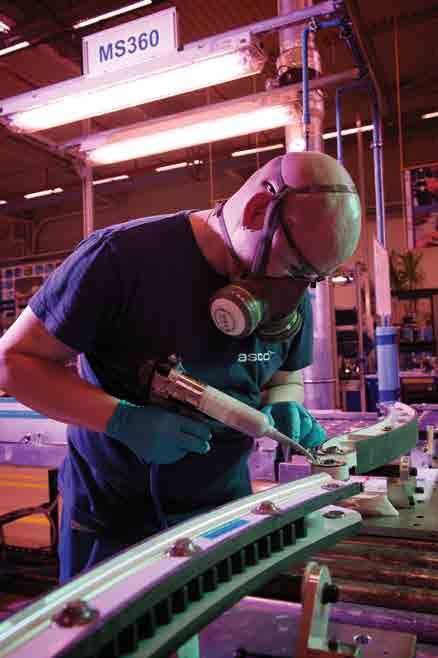
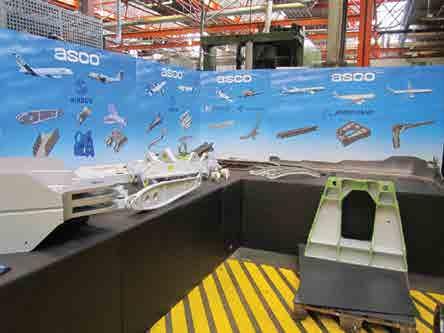
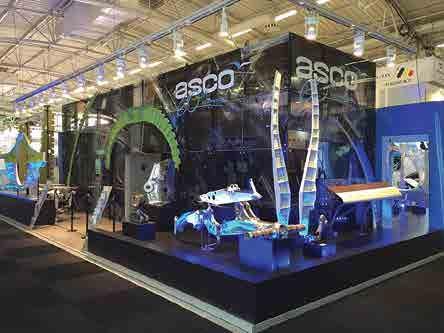

Until recently Asco worked exclusively on commercial aircraft programmes. However, building on its commercial success, the company has become a primary supplier for the manufacture of several modern military aircraft programmes.
Strong partnerships
Being a third generation family business, Asco understands the importance of its partnerships and close relationships with its customers. The company looks for professionals who prize a culture based upon close collaboration and new, innovative ideas while seeking personal challenges to help them fulfil their individual potential and goals.
From the outset, Asco developed strong working partnerships and relationships, being aware that supplying the aircraft industry with even the smallest part was a business like no other so it needed to stay true to its motto, ‘Do it right from the start’. On one occasion it had only a weekend to draft its offer for the A310 slat track contract. It won the contract; however, even when it had acquired the latest machine tools from Germany, it still took nine months from receiving the raw materials to delivering the final product. Things are very different today. Asco can supply parts for an airbus A330 in just five days, and for a complete set for the massive Airbus A380, it must take into consideration that it requires a total of more than 2500 individual components.
Since then Asco has been involved in all the various airbus programmes, including the A330, A340, A380, and now the A350. In fact since the mid 1990’s Asco has supplied key parts for every western aircraft model in the 50-seat plus range. Asco is also playing a major role in the current 787 Dreamliner programme, supplying slat tracks and the crown and lower frames of the fuselage section that supports the aircraft’s vertical fin. Through its close industry partnerships, Asco also supplies the regional aircraft market, with components for both Bombardier and Brazil’s Embraer’s executive jets.
In addition, from its state-of-the-art facility in Canada Asco also supplies the Boeing Everett assembly plant in Seattle, where it produces complex titanium and aluminium components for Lockheed Martin’s F35 joint Strike fighter. n
For further details of Asco’s cutting edge, high-tech product solutions and services visit: www.asco.be
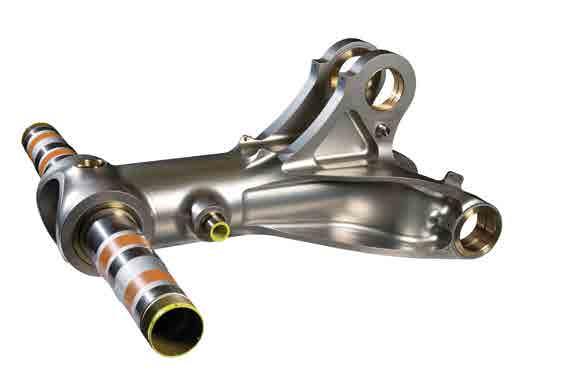