
5 minute read
Metal tube processing experts BLM Group
METAL TUBE PROCESSING EXPERTS
The BLM Group is an undisputed leader in metal tube processing. Giovanni Zacco, market development manager, talks to Barbara Rossi about this fast growing group and its plans for the future.
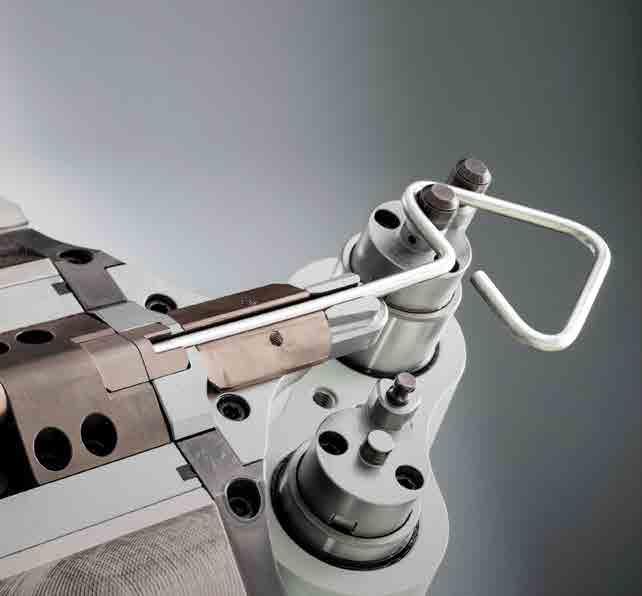
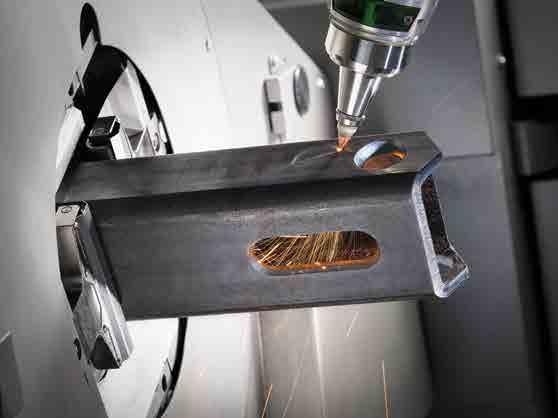
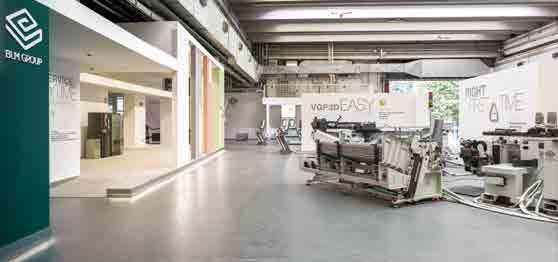
The BLM Group offers an extremely comprehensive range of products for metal tube processing, which include laser cutting (lasertube), sawing, bending and end forming solutions, as well as machines for sheet metal cutting. The only group in the world able to offer all the existing metal tube processing technologies and to integrate them into complex manufacturing systems, BLM is based in northern Italy, with facilities in Cantù (Como) and Levico Terme (Trento). All products are made in Italy. The 2015 turnover was €240 million and in the period 2013–2015 annual growth has been at 17 per cent.
The group comprises three companies: BLM SpA, Adige SpA and Adige Sys SpA. BLM SpA operates from the Cantù site and is specialised in the production of tube bending machines, end forming machines and one particular lasertube model. The two Levico facilities (Adige SpA and Adige Sys) manufacture all the other cutters and laser systems for both tubes and metal sheets.
“Some products we have developed in the past few years are LTFree, LC5 and LT8.10 for lasertube (laser cutting systems), 4-Runner for bending and E-Shape for end forming. LT-Free is a five-axis laser cutting system ideal for three-dimensional parts, bent, hydro-formed or pre-assembled tubes, or flat and pressed sheets. It allows traditional cutting operations – usually carried out in sequencing – to be performed in a single cycle on the same machine. The system is equipped with a fibre laser capable of processing any type of metallic components at high speed with excellent quality. LC5 is a combined system for laser cutting sheet and tube and we are the only ones to manufacture it. The combination of two systems into one offers clear advantages in terms of cost effectiveness. The new LT8.10 offers processing flexibility and is the best performing laser tube cutting system for processing any metal, with a quality which has until now been unattainable.
“4-Runner is particularly suited to processing small and medium size tubes, even in very complex shapes, which are typically used in automotive, air conditioning, heating or cooling system applications. Starting from a coil, it performs straightening, end-forming (up to six passes), facing, rolling, bending, cutting and controlled unloading of the finished part all in one. It can be configured and used with various modules for specific jobs or complete processes. E-Shape is the new all-electric tube forming machine for end forming and integrated stock removal (cutting and facing) jobs, employing VGP2D programming software.”
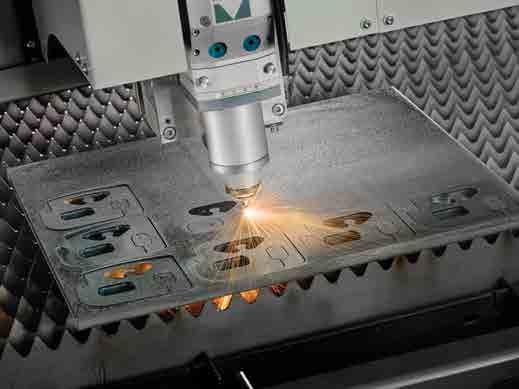

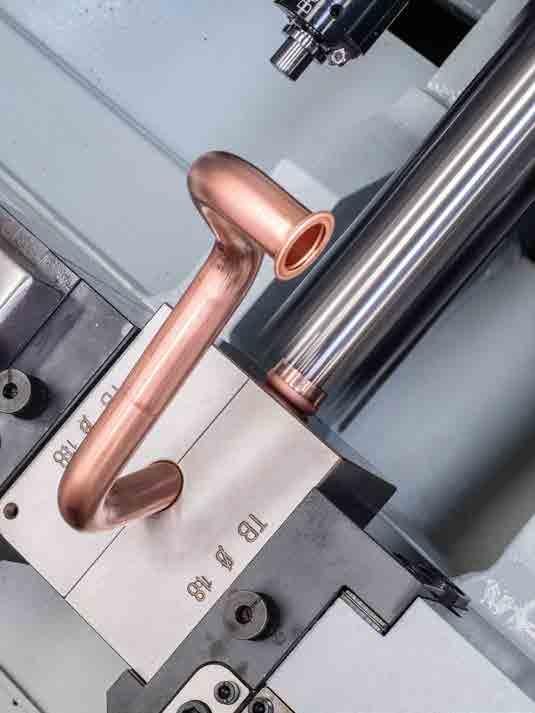
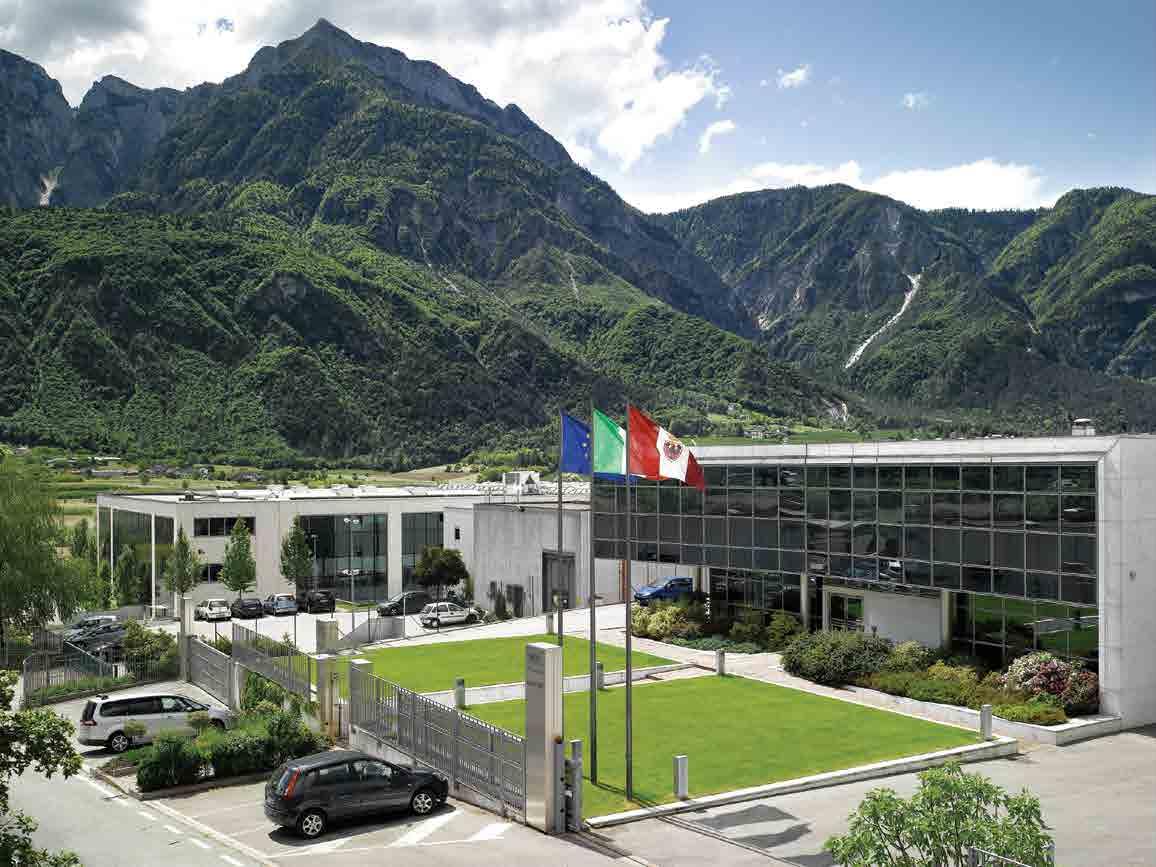
Development through innovation
“In order to keep up with our growth, in the past few years we have expanded our production facilities both in Cantù and in Levico. We have one facility in Cantù – which occupies a 15,000m2 covered area – and two in Levico Terme – respectively covering 25,000 m2 and 27,000m2. All our sites are ISO 9001 certified and obviously this expansion has required significant investments. Furthermore, we regularly invest in R&D. In fact, every year 7.2 per cent of our turnover is channelled into research, which we conduct both internally and in collaboration with Italian and international research institutes and universities, such as the Politecnico di Milano, Politecnico di Torino and the Fraunhofer Institute.”
The company supplies its solutions to OEMs from various sectors – automotive, furniture, agricultural machinery, transport and construction – but also to contractors, therefore its products end up serving an extremely wide range of sectors and are used in a wide spectrum of applications. Automotive and furniture (indoor and urban) are the two main sectors served and will remain central to the group’s work in the future, but the construction sector might also offer significant growth opportunities. Laser cutting has enabled BLM to develop machines for tubes of large dimensions, such as those employed in construction.
“Geographically we are truly global, as we serve all industrialised markets. As a geographical area the EU is our main market, while as a single country the US ranks at the top. About 85 per cent of our turnover derives from exports, although in the last couple of years the Italian market has been recovering quite well. We offer technical support services in all the geographical markets we supply.
“In the next few years we expect strong growth in Mexico and further expansion in South East Asia and the Middle East (Iran in particular). Lasertube is widening its boundaries in terms of future
potential applications and we always pay attention to the new horizons that open up in science and technology, particularly with regard to laser sources, so we might offer new solutions in the future. We really believe that development comes from innovation and that this is the path to follow to maintain our current growth trend. We are very interested in developing solutions for new applications close to our current field of expertise.”
Suppliers are important to BLM’s success. “All our suppliers are highly selected and qualified. They all have to comply with a particular set of requirements that we set. We have a very close relationship with our critical suppliers, which I would define as being a partnership, especially with regard to mechanical processing where we collaborate closely with high quality Italian companies. We use all certified materials and our policy is that of purchasing production and non-production materials and products of the utmost quality. Among the suppliers that we work with are Rofins Sinar for laser sources and Siemens for electronic equipment.” n
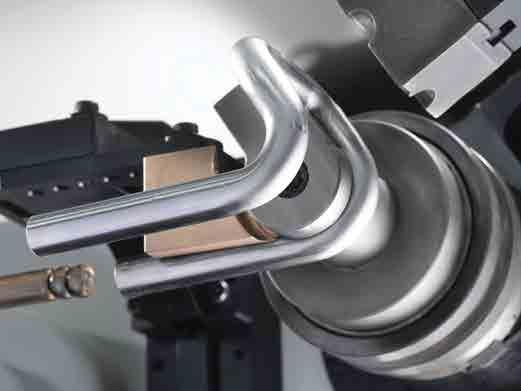

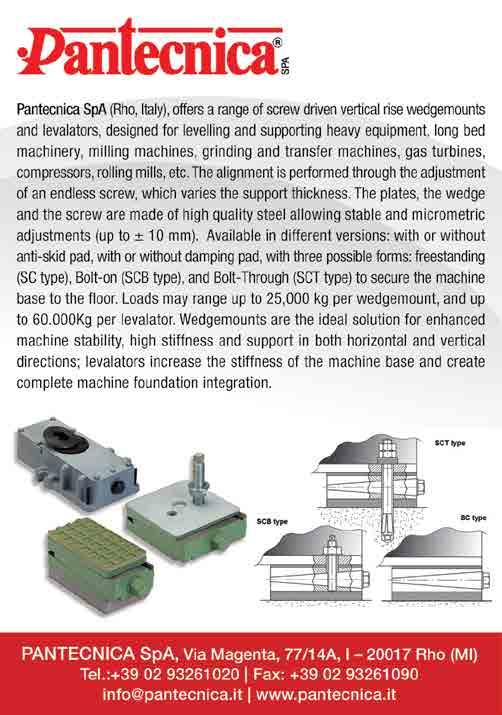