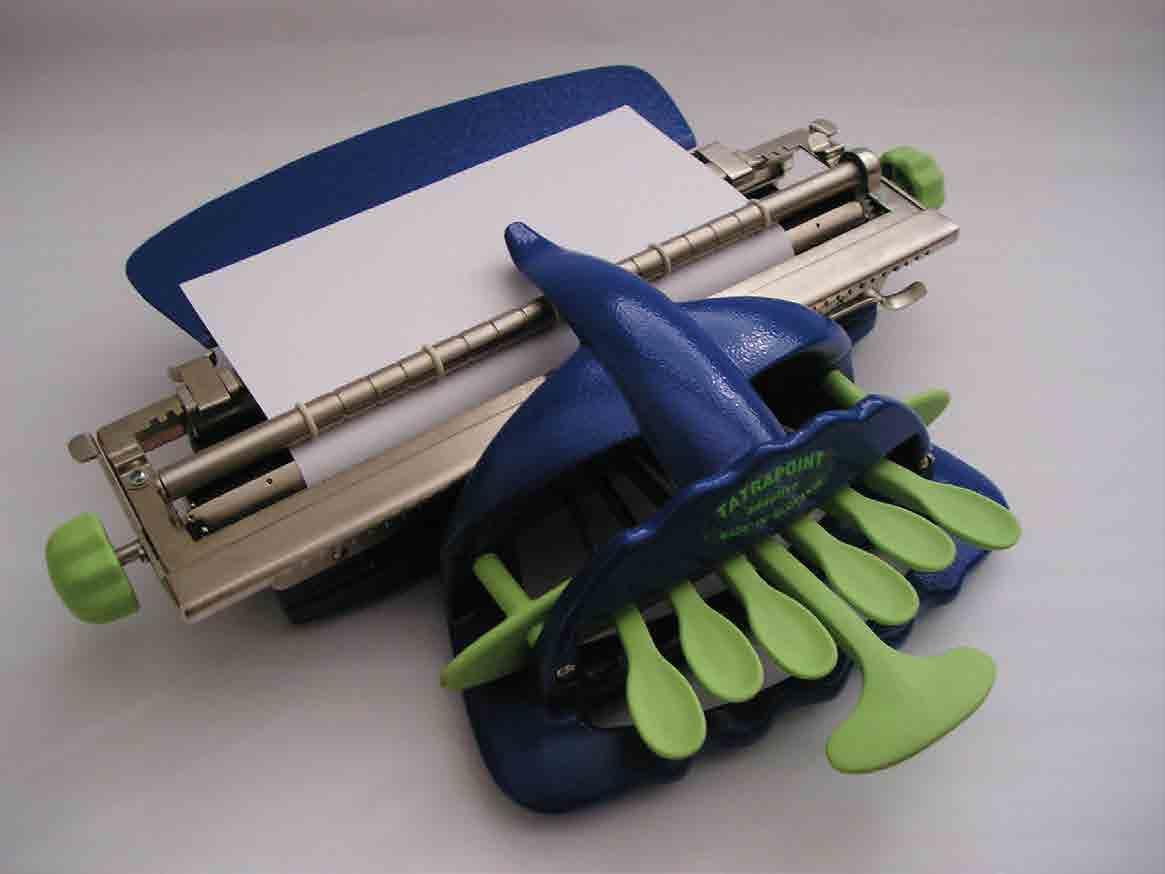
4 minute read
Sheet metal specialist ŠVEC A SPOL
SHEET METAL SPECIALIST
Slovak ŠVEC A SPOL is a modern engineering company offering bespoke production of sheet metal parts and assemblies, diversified into several industry sectors. Romana Moares spoke to managing director Lubomír Švec about the company’s evolving core business and what makes it strong in this fiercely competitive market environment.
The Slovak company ŠVEC A SPOL s.r.o. was established two decades ago in order to design and manufacture stamping tools for metal piece pressing. A turning point came in 1998 when it became a supplier to the automotive sector, and subsequently set up two more divisions for the manufacture of metal assemblies, and for steel, aluminium and stainless steel components.
In the past few years the company has undergone another wave of rapid growth, resulting in the establishment of a new division for the manufacture of steel structures, based in Nitra, and the achievement of the ISO 14001 a ISO 3834_2 certificate for the welding of steel structures, protective rails and machine parts and equipment. “We have become a specialist in stainless steel and aluminium processing,” says Mr Švec.
Total turnover for the group (including its sister companies) reached nearly €20 million in 2015 and its financial performance is further improving. “In the near future, we want to further extend our comprehensive services in the area of ultrasonic cleaning and stainless steel processing,” explains Mr Švec. He adds that the company’s core competitive advantage is its diverse portfolio and ability to offer customers not only part and sub-assembly deliveries, but also comprehensive product solutions. Trusted partner
“Our key products are stamping tools and pressed pieces for the automotive industry, comprehensive assemblies for the food and construction sectors and ultrasonic cleaning devices for various industry applications,” explains Mr Švec.
The development of stamping technology for metal parts is supported by PamStamp 2G simulation software. The stamping tools are designed in CATIA V5 R24, ProENGINEER, PowerSHAPE, Mechanical Desktop (3D) and AutoCAD (2D) software.
The company is currently organised into five production divisions, located in Nitra and Vrable, each applying the principles of lean manufacturing. The divisions are equipped with first class machines including over 20 presses from 100 to 800 tonnes capacity and universal machines for sheet metal processing, including laser cutting, punching, bending and folding machines and robotic welding equipment.
In the past two years the company has invested over €7.5 million in new technologies. The latest additions include Trumf Fiber, a high-performance automated laser, a Salvagnini CNC panel bender, a Trimill portal five-axis milling machine and the Arisa transfer press – a

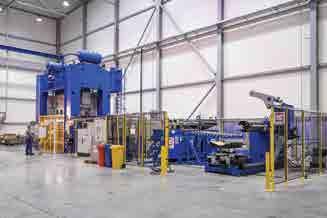
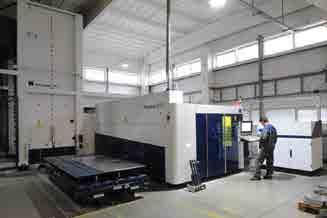
modern standard for automotive suppliers. “We plan to further upgrade our production technologies and include the latest machines so we can further improve our productivity, quality and flexibility,” says Mr Švec.
For European car makers
The engineering sector seems to be booming at the moment, but generally speaking only those companies that can offer timely deliveries to the desired level of quality at a highly competitive price can expect to really benefit from this boom.
“The products from our tooling and pressing shops, which are delivered to Tier 1 suppliers, may be found in the vehicles of nearly all European brands,” says Mr Švec, adding that the automotive sector is not the only industry in which ŠVEC A SPOL has achieved success. “Our ultrasonic cleaning line will be installed in Thailand in early 2017 and our ‘ambassador’ on literally all continents has been our typewriter for the blind – a product design and developed entirely in-house which has cemented our reputation ever since it was first launched decades ago. And this year, we have used the Amazon sales channel to promote our (so far) small product range of in-house designed stainless steel products.”
Ambitious plans
Mr Švec points out that one of the pillars of the company’s success is its partnerships with suppliers, highlighting in particular its technology suppliers Trumpf, Trimill, Hermle and Doosan, tool suppliers Semaco and Asinell and raw material suppliers Raven, Klimex and Ferona.
“While in 2015 we invested massively in technologies, in 2016 investment was focused on staff training and development so our new modern technologies can be utilised in the most effective manner. We will continue this process and have ambitious plans for the next few years: we want to purchase further new technologies, invest in product design and extend our prototype capacity so that we are in a position to meet even more comprehensive customer requirements in a fast and flexible manner.”
In concluding, he stresses the company’s mission for years to come – to develop a modern, highly efficient business which offers its customers a comprehensive range of products and services using the latest technologies, while remaining a trusted partner and a good employer. n
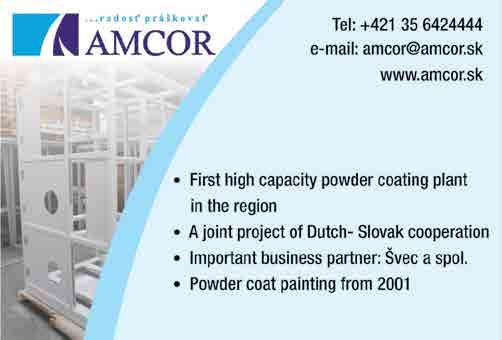
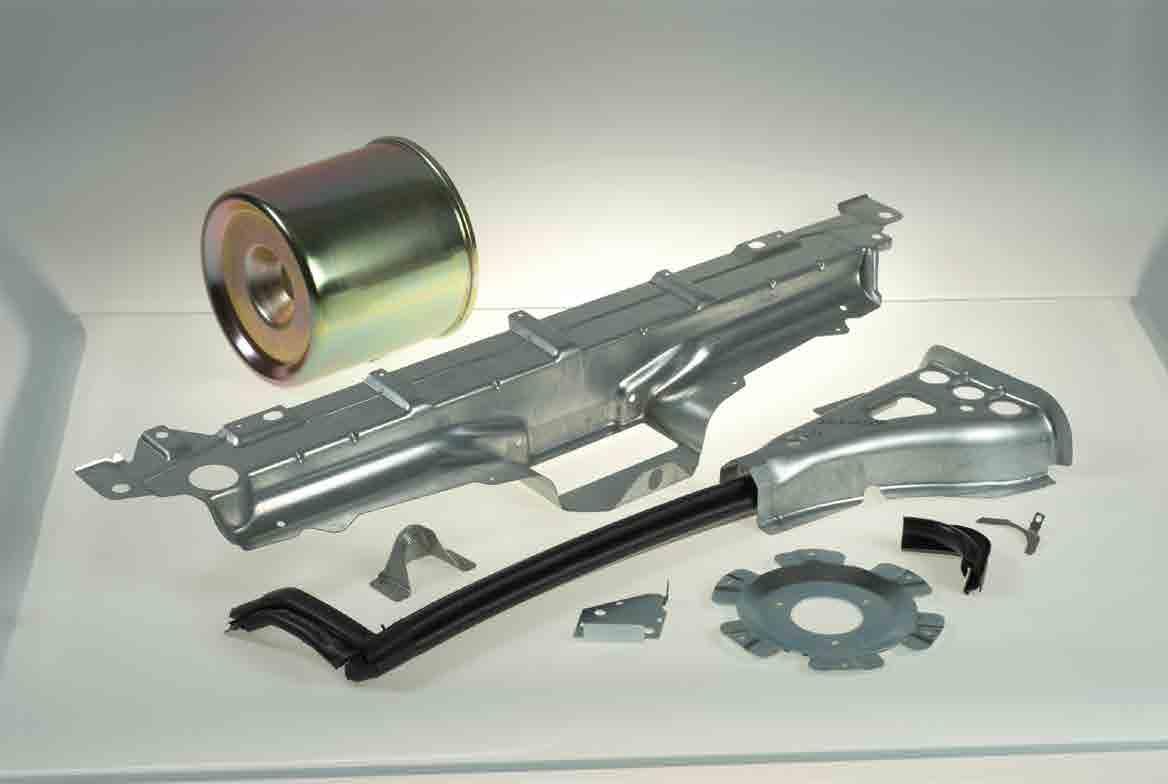