
4 minute read
Combined strengths KCM 2000 Group
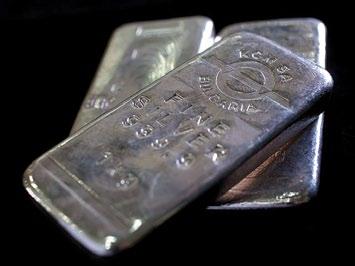


COMBINED STRENGTHS
The KCM 2000 Group manages a wide portfolio of companies across a number of fields such as nonferrous metals production, trade and engineering, and includes Europe’s largest producer of lead and zinc alloys, KCM AD. Industry Europe looks at the group’s activities and how the synergies between each of its companies have enabled it to grow in strength in the years since its establishment.
Privatised in 2000, the joint-stock company KCM 2000 AD manages a diverse portfolio of companies, employing over 3000 people across the fields of nonferrous metals production trade, industrial engineering and industrial service. It is the role of the parent company to assist each of its subsidiaries in the management and control of their various activities when it comes to innovation, production, trade and marketing.
KCM AD is the main production unit of the group and the leader in nonferrous metals production in south-eastern Europe and the Black Sea region. The company remains at the cutting edge of metallurgical development and works actively to promote the sustainable credentials of its materials. The group also holds a 49 per cent share in Luki Invest Plc, a producer of lead and zinc ore. Meanwhile VARBA-BATANTSI, established in 2011, is focused on the mining and processing of ore
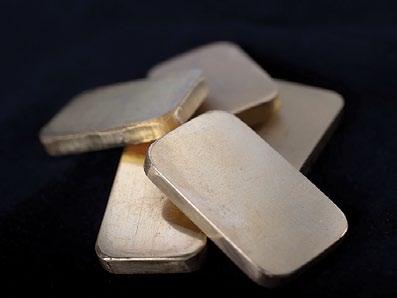

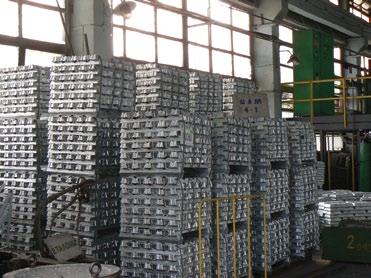
mineral resources and is managed by two owners – KCM 2000 AD and MINSTROY Holding AD.
The KCM 2000 Group’s trading activities are carried out by KCM TRADE EOOD and BLZ METALIKON Ltd, while KCM TECHNOLOGY EOOD is an independent company within the structure of the group which provides engineering and technical services according to exact customer specifications. Other wholly-owned group companies, concerned with industrial service provision, include KCM Industrial Service EOOD and Stroyservice EOOD.
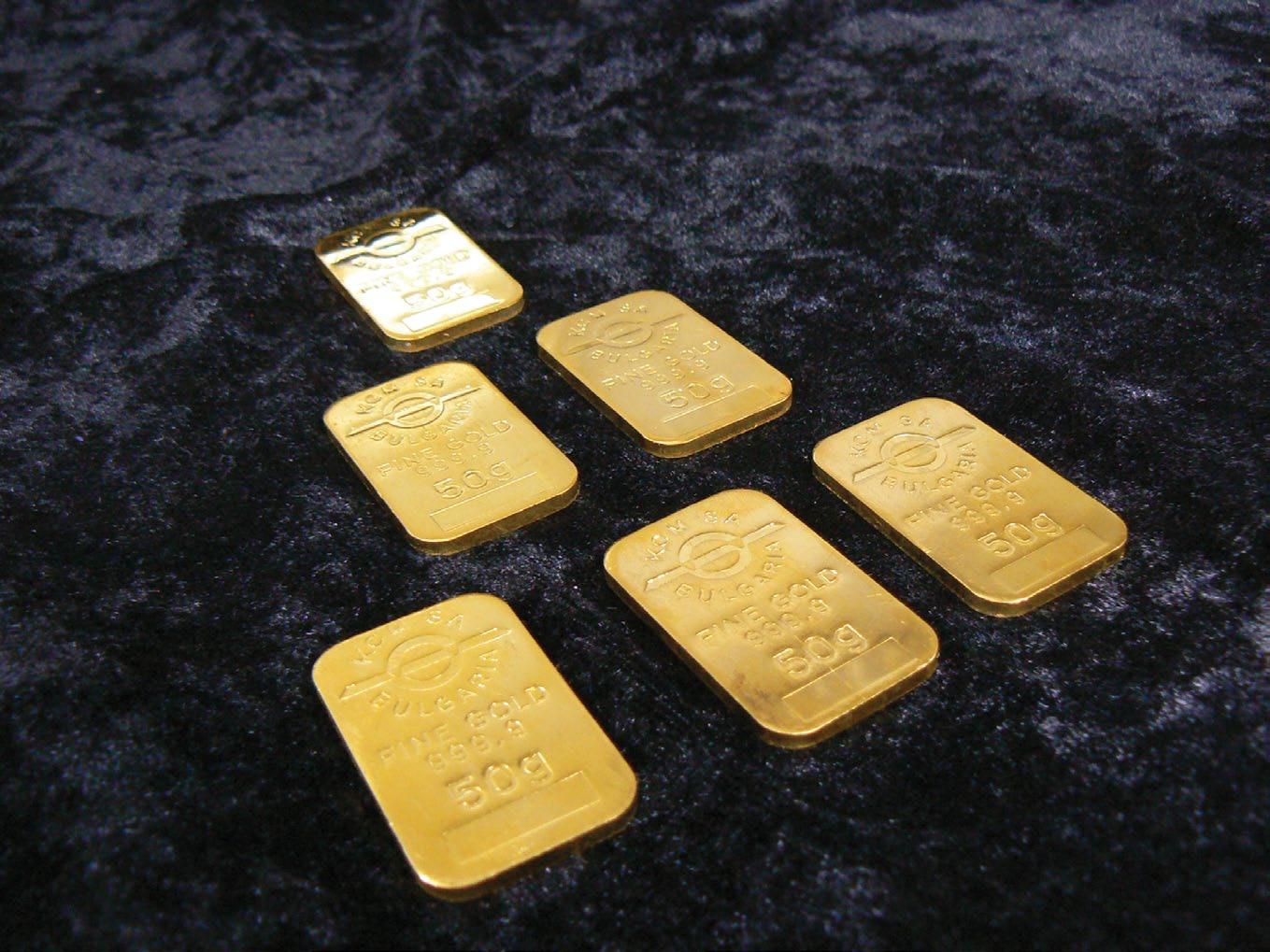
Continuous investment
KCM AD manages its own extensive zinc-lead mining facility near Plodiv as well as a large engineering and industrial service company, and is a major shareholder in the country’s largest industrial and commercial zone complex.
KCM has made significant investments in a number of key facilities over the past decade. These have included a state-of-the-art battery recycling facility, a wastewater termination plant and a zinc roasting and sulphuric acid facility – all of which have made a significant contribution to reducing the company’s carbon footprint.


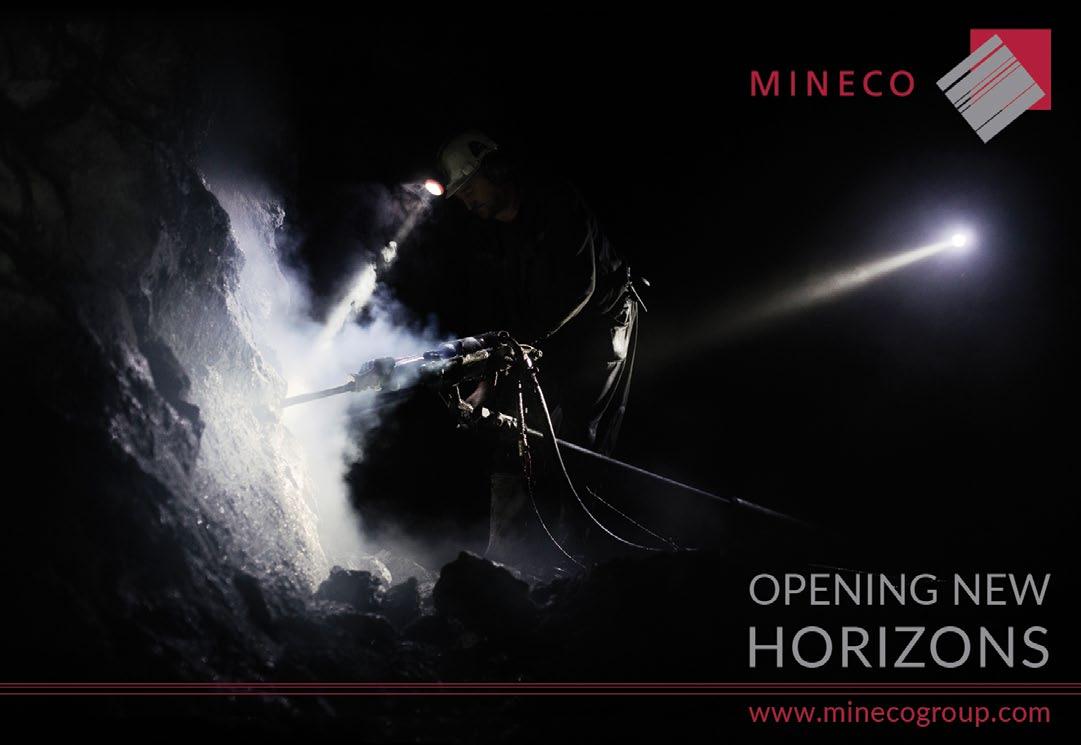
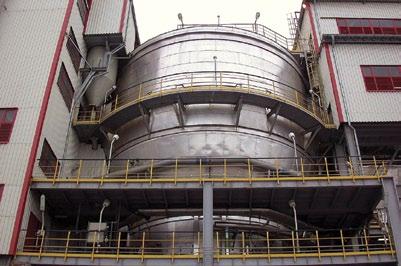

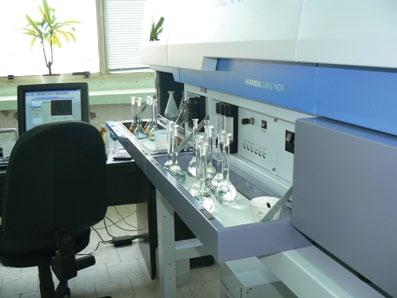
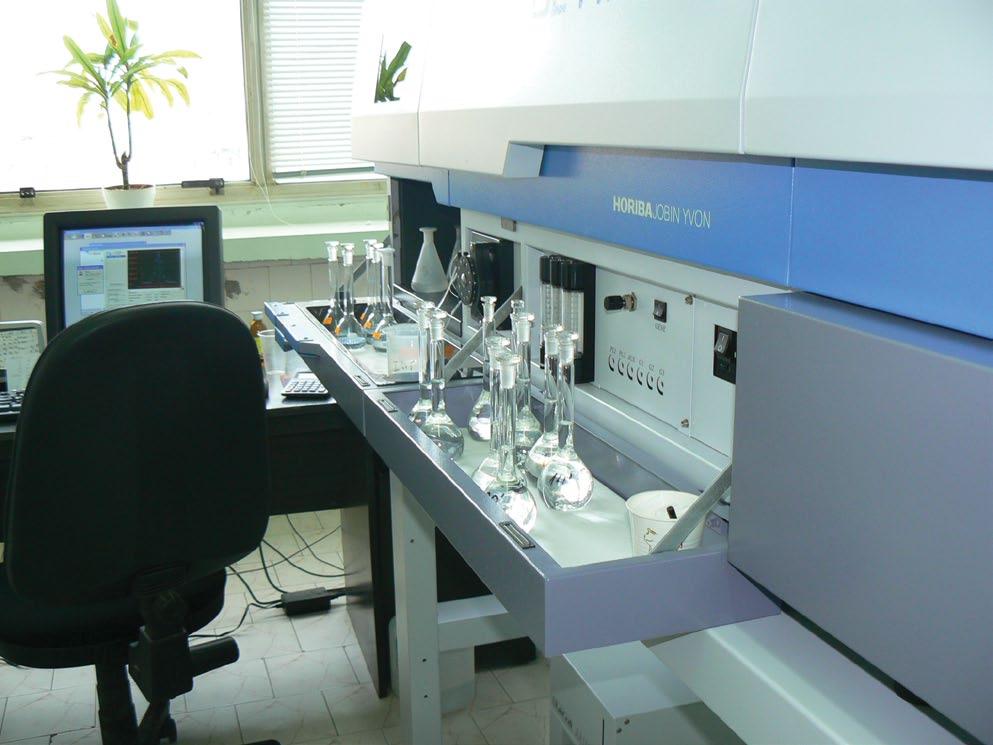
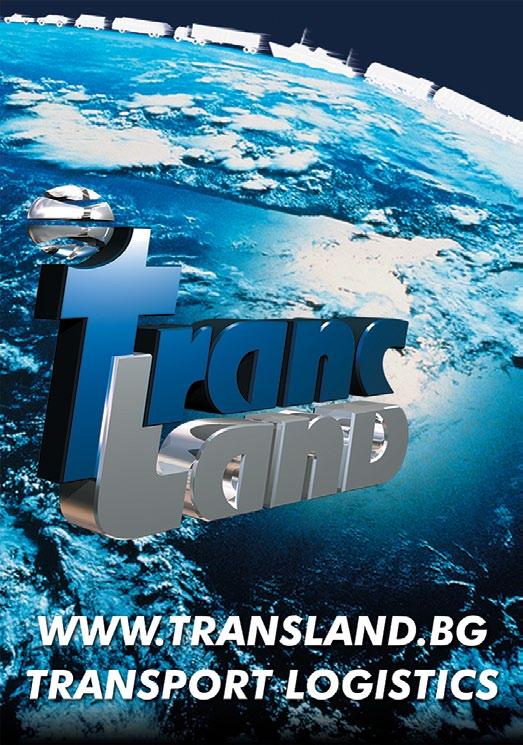
In 2014, the group launched the second stage of a 400 million lev (€204.5 million) investment project. The first stage of the project – investing in facilities for recycling, diversifying the raw material base and installing a new zinc plant – was completed in 2014. The next stage of the ambitious project is ongoing, but when it is completed it should see the plant’s capacity increase to increase from 75,000 tonnes to 115,000 tonnes of zinc per year.
KCM’s domestic market for its smelter products is around 10 per cent of total production, with the majority of the products exported to Turkey, Greece and other Mediterranean countries. However, the company has been increasingly moving into western European markets for the sale of its zinc alloys.
The company has also been developing a wider range of alloys for a variety of applications including those for protection against corrosion. In addition, all types of precious metals are manufactured through KCM’s smelter, including alloys for coins as well as for gold and silver specially treated for banks and ‘rolled’ precious metals for industry.
Building on its substantial experience gained during the company’s restructuring process and the implementation of new plant and technology, KCM is also able to offer a wider range of technological consultancy services. These include conceptual, technical and economic research, specialised high-tech and laboratory testing procedures, the design of new systems and installations using AutoCAD and inventor professional 2010 software and the licensed monitoring of equipment.
Additional solutions and production know-how are also available in fields such as continuous lead slag fuming, zinc dust production, the production of zinc and lead alloys, the processing of fluids and the recycling of waste water cooling as well as the recovery of gold from gravity concentrate.
Sustainable commitment
All KCM 2000 Group companies are committed to sustainability and continuous quality improvement and it holds the ISO 9001, ISO 14001 and BS OHAS 18001 certifications.
In 2008, for example, KCM implemented the ‘Process Innovation and Production Increase Project (PIPIP), which was finalised in 2012. The PIPIP’s main objective was to achieve environmentally appropriate and competitive production of non-ferrous and precious metals, alloys and chemical products. The concept included energy saving processes and options for the processing of recyclable materials, as well as for the reduction of green house gases and emissions. n