
4 minute read
Your chosen partner in sheet metal manufacturing

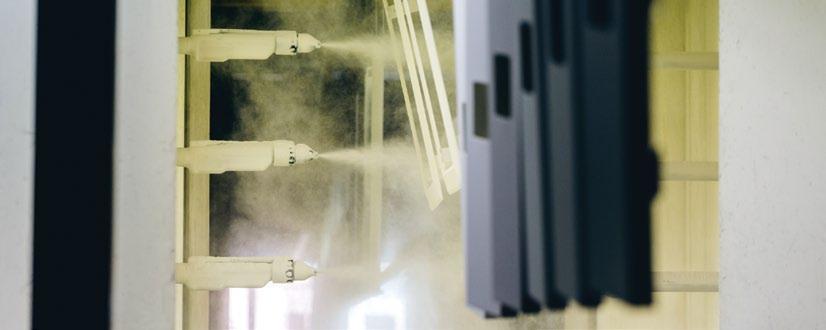
Stansefabrikken has gone through many phases and events during its 30 years in the sheet metal industry. The company has experienced its up and downs following national and international economic cycles. However, it has mainly been on a steady path of growth and profitability driven by hard work and ambition on the part of its enthusiastic employees and owners.
Stansefabrikken was established in 1985 with one operating company, 9.1 MNOK in turnover and 27 employees. Today the group consist of several subsidiaries, has an annual turnover above 300 MNOK (2016) and up to 370 employees coming from Norway, Sweden and Lithuania.
Stansefabrikken decided to establish production abroad in the summer of 2002. Its choice was Ukmergė, a middle sized industrial city in central Lithuania. Today the leading provider of sheet metal processing companies in Lithuania, Stansefabrikken UAB – a subsidiary of a Norwegian Stafa Industrier AS – is currently operating in four market segments: sub-supply of sheet metal products; automotive stamping; development and sale of fuse cabinets and post-boxes; and rental services in the industrial park.
The Stafa Industrier group is a financially solid, modern, wellstructured organisation. The Stafa Group companies are primarily offering services and products within the sheet metal manufacturing business, with a vision of building long-term relationships and providing customers with highly cost-efficient solutions to meet the most challenging requirements. Quality and delivery precision is considered a prerequisite. Group companies are certified according to ISO 9001, ISO 14001 and TS/ISO 16949.
Partner for oem companies, aerospace and automotive
Stansefabrikken is one of the three group companies located in Lithuania. It is capable of producing almost any kind of sheet metal product made to specifications in high and medium volumes. The
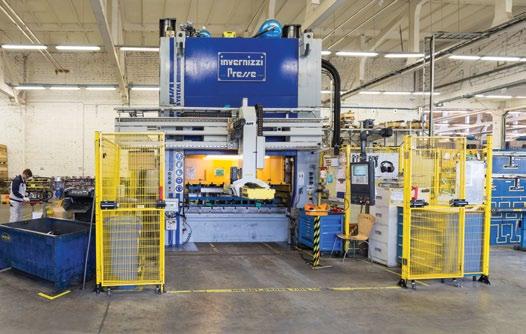
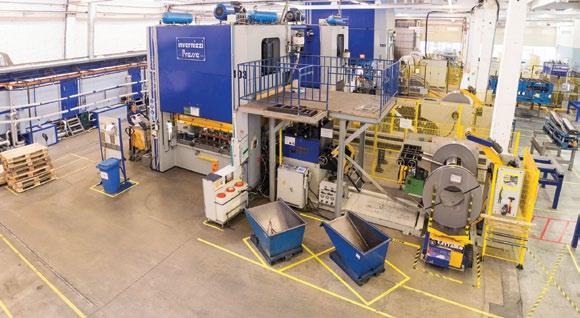

company supplies products in all stages, from design to the finished item, using modern CNC laser cutting, punching, bending, welding and robot welding equipment.
Its manufacturing facilities also include two automated powder-coating lines. A fully automated process of pre-treatment with oxilan ensures consistent and high-quality coating results. In addition, the company offers comprehensive assembly and packing-to-shop services. As a sheet metal parts producer and supplier, Stansefabrikken makes sure its products are professionally assembled and packaged. In addition, it can offer engineering, design and prototyping services via its subsidiary in Fredrikstad (Norway) – Stansefabrikken Fredrikstad AS. A young and dynamic team of Norwegian and Lithuanian designers, engineers, project leaders and managers has been involved in a variety of projects that enable its customers and partners to develop new products and achieve the desired results.
Stafa Industrier has decided to put a greater focus on its products for the automotive industry. Therefore, in 2007 it opened a new factory to produce stamped metal automotive parts: Stansefabrikken Automotive UAB. Investments were made in modern equipment and one of the most powerful presses in the Baltic States. The company is compliant with the highest standards and strictest requirements within the automotive industry.
Stansefabrikken Automotive operates the biggest punching line with a 1300-tonne press accommodating punches of up to 30 tonnes and parts measuring up to 4500 x 1800mm. The company is manufacturing car parts from soft steel of up to 12mm in thickness and 1600mm in width. Another advantage is that the 1300-tonne press is technologically linked with a degreasing line. This ensures short production leads and effective cost control.
Consistent work and attention to detail has helped the Stafa Group companies build a reputation as reliable partners, allowing them to win the trust of such famous companies as ABB, Bang & Olufsen, CENIKA, BICO, GKN Aerospace and others. The sheet metal products are mainly used as components of safety-critical systems such as steering columns, breaking control systems, instrumental panels and tow bars for car manufacturers such as Opel, Nissan, Renault, Mercedes-Benz, VW and Audi.
Industrial facilities for modern production
The modern industrial park Ukmergės Pramonės Parkas UAB is located in Lithuania, in the grounds of a former gear factory, and occupies an area of more than 5.3 ha. It houses the Stafa group companies mentioned above, as well as external companies. The vision behind the group’s creation of the park was to offer industrial premises with common facilities and services, which are well-suited to modern production. Currently the fully developed industrial park can offer 22,000m2 of renovated office and production space. A total of seven enterprises currently operate in the industrial park.
“Our goal is to become a top-level service provider in the sheet metal industry, supplying customers with top-quality products. To achieve this, we continuously expand our expertise by developing our staff, investing into the upgrading of equipment and introducing the latest technologies, as well as focusing on being more efficient,” says Nerijus Mašalas, managing director of Stansefabrikken UAB.
Focus on efficiency
Stansefabrikken is constantly updating its operations to achieve greater efficiency. The greatest improvements in efficiency have been down to the efforts of its internal ‘S-TEAM’ which consists of heads of production departments, as well as to its implementation of the ‘Stop’ analysis.
A Norwegian parent company ‘Stafa Industrier’ has been assisting the group in the implementation of its efficiency improvement project. “We had to change the process flow in the factory, as well as the working principals, and this proved to be the right decision – and not just because of the increase in the available space. We rearranged the manufacturing process itself and increased the output – now the operator is working on the manufacturing of the product, while another set-up operator is adjusting the machine tools,” explained Mr Mašalas. n