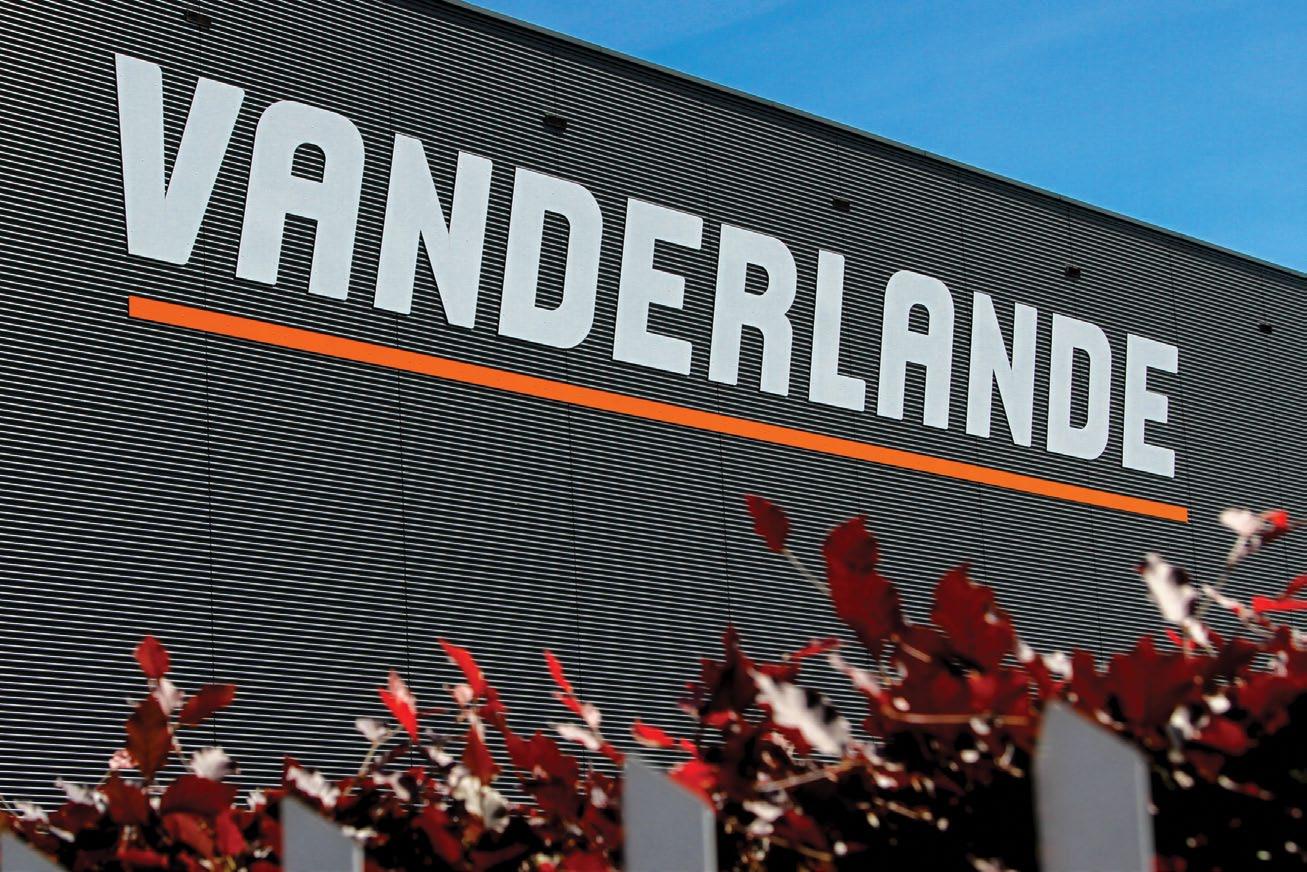
6 minute read
Flying high in airport handling systems
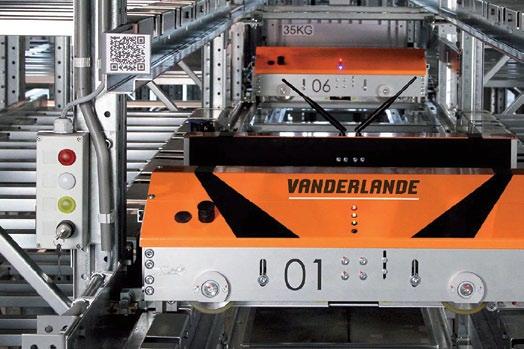
Vanderlande Industries is a global leader in the design and manufacture of airport baggage handling and security systems. The company has been successful in moving into new markets with its latest generation of Scannojet® passenger checkpoints and high-tech handling systems, including its Automated Guided Vehicle® technology (AGV) which avoids the need for conveyors and sorting systems. Philip Yorke looks at a company that continues to outperform its competitors and extend its global reach.
Vanderlande Industries was founded in Veghel, Netherlands in 1949 and began by manufacturing conveyer systems for the loading of agricultural produce onto ships, which were moored in the nearby waterways. Today the company is a global leader in automated handling technology and one of the largest and most advanced in the world. Its core businesses provide a wide range of fully automated material handling systems for baggage handling at airports, as well as for automation systems for warehouses and government postal distribution services.
Vanderlande designs and installs material handling systems of all sizes, from local sorting depots to some of the world’s largest and most sophisticated distribution centres. All the company’s tailor-made systems and services are designed to improve its customers’ logistics processes, from the initial concept right through to total life-cycle support.
Vanderlande’s services range from logistics concept and design, to engineering, software development, supply chain management and manufacturing. In recent years the company has extended its specialised service concepts to customers worldwide. This offers an important growth area as it includes pro-active maintenance, remote monitoring and diagnostics with a clear focus on end-to-end process performance.
Today Vanderlande is also able to transfer its diverse technologies to other operations, thus making it possible to excel in its three main areas of operation: baggage handling, warehouse automation and postal sorting systems.
Integrated solutions
In July this year, Croatia’s main international airport at Split selected Vanderlande’s integrated solutions to provide it with new baggage handling systems, which will include the company’s advanced Vibe Software and life-cycle service packages. The unique, highly efficient system will be installed at the airport’s new terminal building with delivery planned for April 2018.
Following its entry into the European Union in 2013, Croatia has seen a significant increase in tourism and last year Split Airport welcomed over 2.3 million travellers. In April this year volumes rose by more than 60 per cent compared to the same month last year. In order to be able to handle such dramatic growth, Split Airport decided to build a new terminal. It selected Vanderlande due to the company’s unrivalled industrial expertise and innovative handling solutions, which are ideally suited to match the airport’s future requirements.
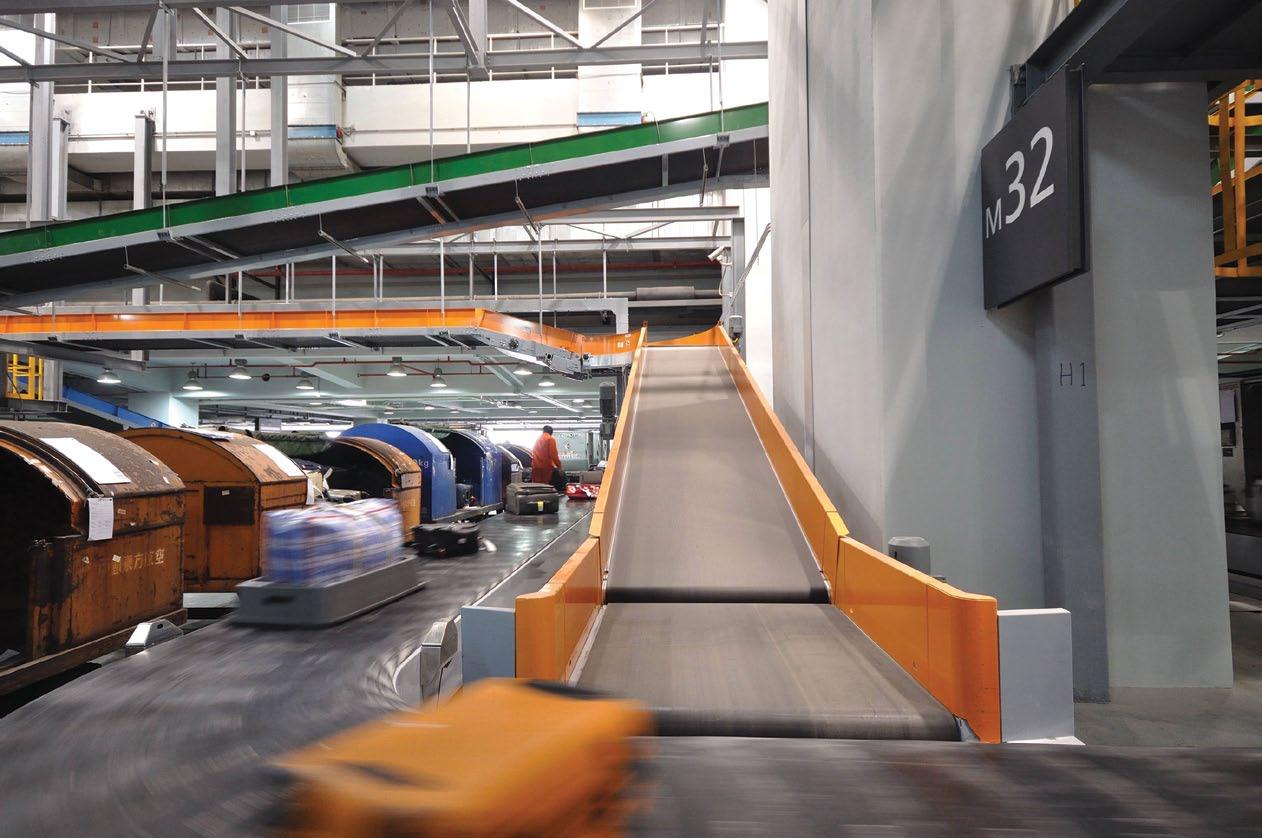
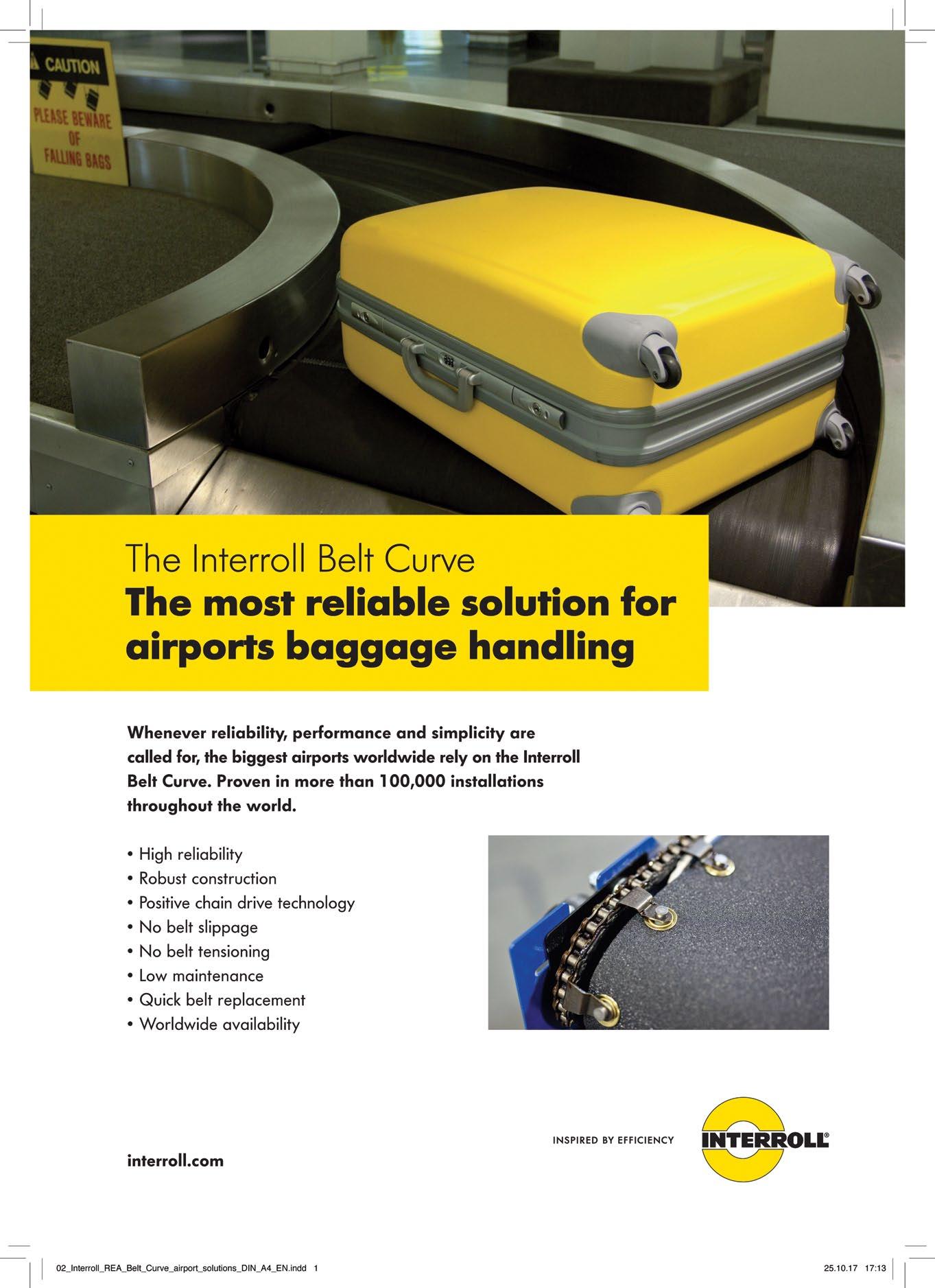
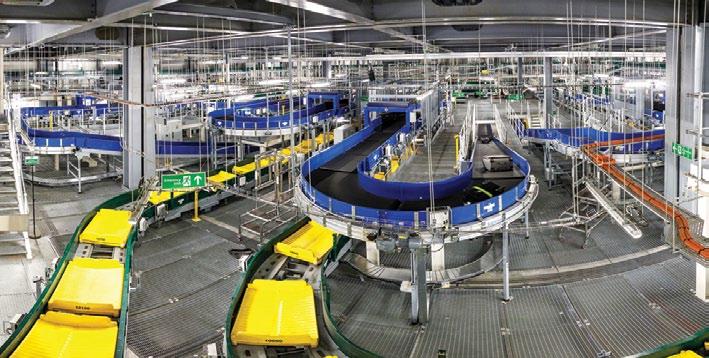
Another major contract was awarded to the company recently when Tallinn airport in Lithuania chose Vanderlande to supply its latest generation of Scannojet® passenger checkpoints for its new security screening area. The company was ‘pre-selected’ for the contract based upon its reputation and expertise as a systems integrator offering the most cost-effective and efficient solutions. All of the airport’s five ‘Scannojet®’ lanes have been designed according to the latest operational insights and field experience.
The new lanes will be equipped either with three or four parallel divestment stations, each with indicator lighting to guide passengers swiftly through the checkpoint in an intuitive manner. Each divestment station is configured in such a way that people can use two trays beside each other, while divesting their belongings. This feature guarantees a constant flow of passengers and also provides peace of mind for travellers. Furthermore, operators are able to maintain a good overview of the complete passenger divestment process.
unique solutions
In September this year Vanderlande signed a contract to implement its new solutions for the baggage handling area at Lelystad Airport, which is part of the Schiphol Group. This unique system will utilise the company’s acclaimed Automated Guided Vehicle (AGV) technology and includes a new self-drop system, as well as optimising the travel experience for passengers. The announcement comes at an important time in the history of Lelystad airport, which is located near Amsterdam and has been required to undergo a major phased upgrade in order to provide additional capacity and enhance its growing commercial activities. The new facilities must be completed by 2019.
The all-new solution from Vanderlande will guarantee shorter project lead times and will consume up to 50 per cent less energy compared to traditional baggage handling systems. The special design will also mean that the equipment can be easily recycled, thus contributing to a circular economy.
“We are delighted to have signed this agreement with our partner Viggo, who was rewarded with the contract for completion of the shellstate terminal and the provision for ten years of all related services at Lelystad airport,” said Vanderlande’s CTO Vincent Kwaks.

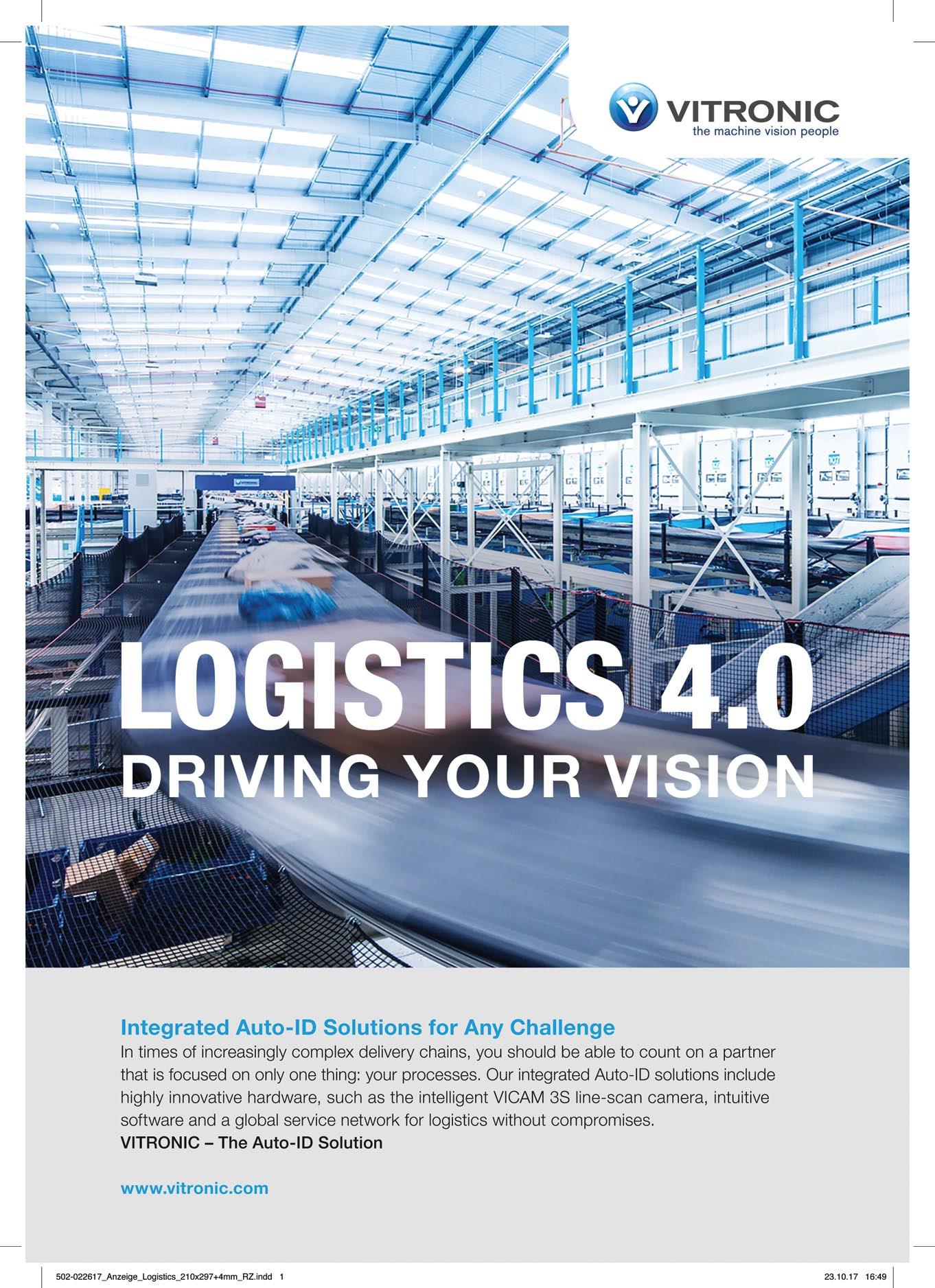
Vitronic
logistics companies have high demands on the degree of automation for their processes. No matter which application - sorting, incoming and out-going inspection, material flow, storage, order picking or optimal utilization of transport capacities: The basis for optimizing logistical processes is the automated capture and processing of product-, package-, and customer-related data – easily, efficiently and transparently.
VITRoNIC Auto-ID systems capture and analyze all relevant information such as bar codes, 2D-codes, customer-specific codes and plain text (oCR) – even several different code types in one image – on up to six sides of different packages. The orientation of the package makes no difference, text and codes are captured even behind foil. Parallel, the volume and weight of the consignment is captured.
Flexible operation according to your needs. Depending on individual requirements, data on packaging can be captured in a variety of camera-based methods and then utilized efficiently for downstream processes
• Manual data capture – camera to goods • Semi-automatic data capture – goods to camera • Fully automatic data capture – inline
VIPAC systems can be installed at any position along the entire process chain – including volume measurement, recognition of deformations and weighing – and guarantee maximum read rates.
“This is an excellent example of how Vanderlande is able to adapt its existing technology to create an entirely new solution. We’re confident that our innovative equipment, combined with new intelligent software applications, will provide maximum efficiencies to Lelystad and the wider aviation industry.”
Vanderlande will also be presenting yet another new innovation, called ‘Fleet’, at the Inter Airport Europe 2017 exhibition in Munich, Germany in October, where live demonstrations will be available.
expanding product portfolio
In a move that will significantly enhance Vanderlande’s high-tech product portfolio, the company announced that it had acquired the leading Canadian software company, ‘Optosecurity’, in June this year. The acquisition strengthens Vanderlande’s integrated portfolio of solutions and its position as market leader for value-added logistic process automation at airports.
Optosecurity’s software is unique and offers a market-leading platform for remote screening and data integration. The combination of this intelligent software and Vanderlande’s automated passenger checkpoint solutions presents the opportunity for the new partnership to become the leading integrator of passenger screening processes at airports worldwide.
For further details of Vanderlande’s innovative integrated handling systems, visit: www.vandelande.com
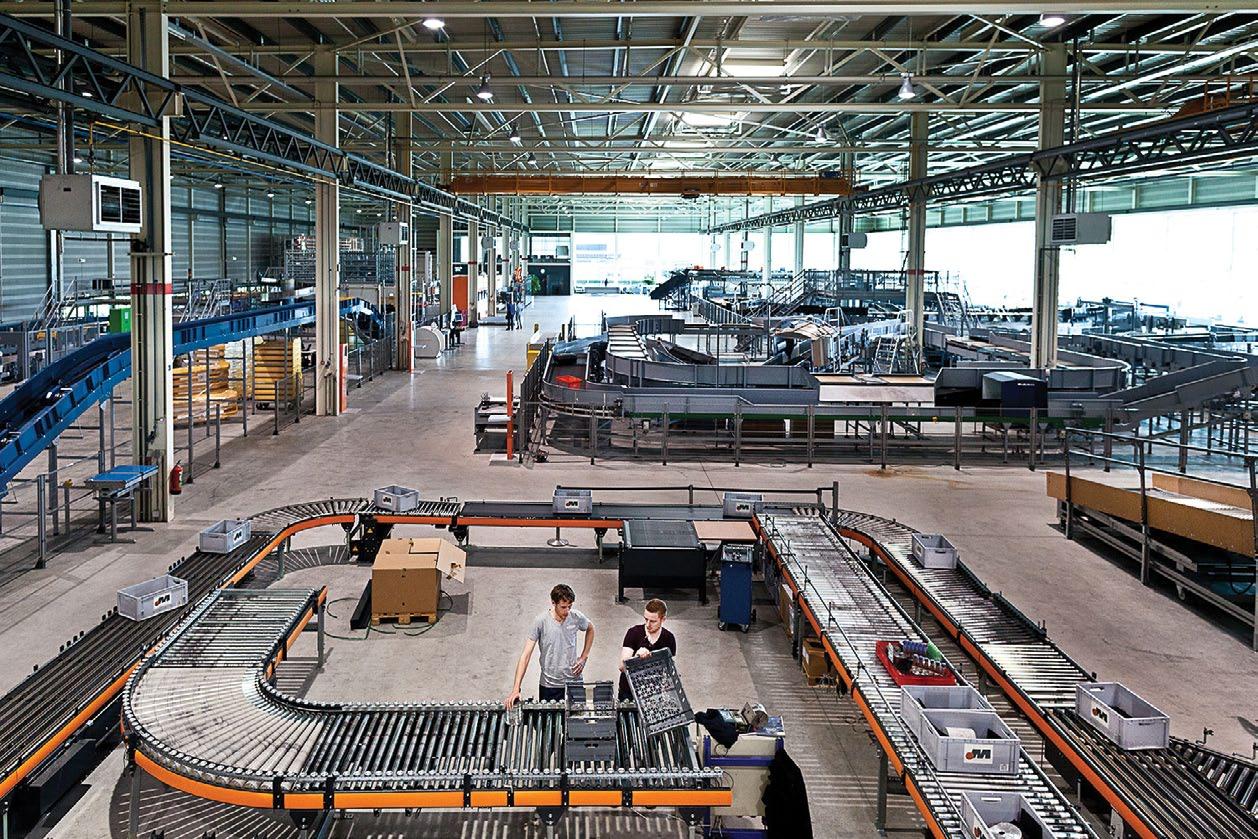