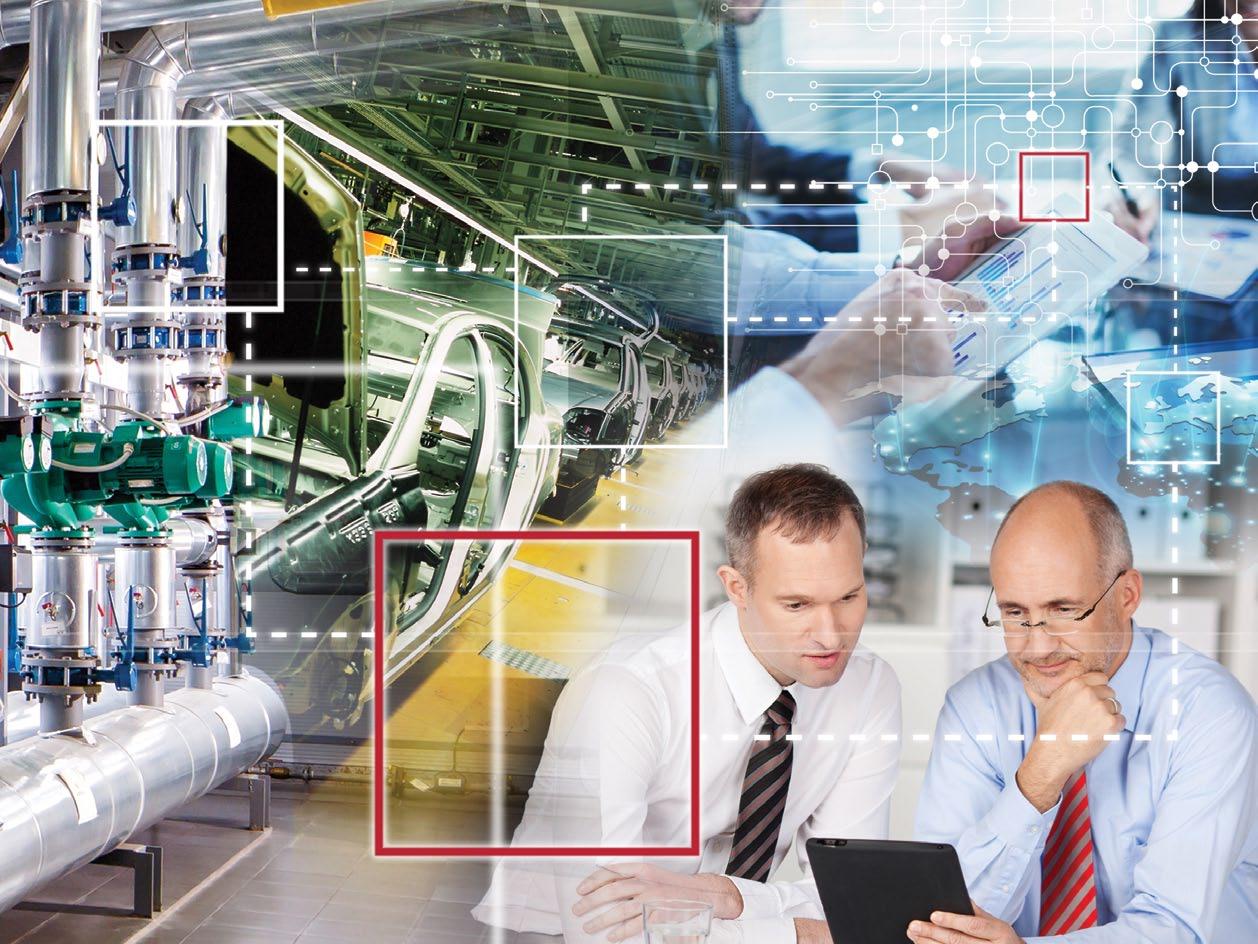
9 minute read
Smart solutions A look at how Rockwell Automation is embracing Industry 4.0
sMart solutions
Thomas Donato, Rockwell Automation EMEA President, explains to Peter Mercer how the fourth industrial revolution is transforming manufacturing efficiency.
IN the summer of 2017 Rockwell Automation, the global leader in industrial automation and information, opened its first EMEA (Europe, Middle East and Africa) Customer Centre in Karlsruhe, Germany. The new facility is designed as a one-stop source for customers seeking personalised advice on the right digital strategies that will help them develop their own ‘smart’ factory – in which the interlinking of production and IT systems can reduce costs, improve quality, save resources and enable a faster response to market changes.
Rockwell Automation started its own journey to what it now calls ‘The Connected Enterprise’ around ten years ago with the introduction of intelligent monitoring of production data across its own manufacturing facilities. Its customers can now use the new Centre to leverage Rockwell Automation expertise and experience the benefits of digitalisation live on site. In theory, of course, most enterprises understand the potential of the smart factory but the Customer Centre is designed to bring these advantages to life though interactive demos, application examples and advice from Rockwell Automation specialists on how the smart factory precepts may be implemented to meet the specific needs of each company.
“When we began the process of connecting production and IT systems across our own manufacturing operations – connecting assets across multiple locations – we were able to achieve up to 5 per cent gains in productivity,” explains Thomas Donato, Rockwell Automation President for the EMEA region. ‘Now we can help our customers to realise similar benefits through reducing inventories, optimising supply chains, improving product quality and unlocking cash resources.
“Essentially the Customer Centre enables us to show customers how we have done it ourselves and where they themselves can start. We can offer them an Execution Model, that we have developed as part of our Connected Enterprise concept and which we can use to help them tackle each of the stages in their own realisation of the smart factory. We start by reviewing their current situation and clarify their expectations. Then we define the goals together, decide on the scope and create a concept that will meet exactly their individual needs.”
The new Customer Centre also hosts staff, PartnerNetwork members and customer training sessions as well as seminars on smart factories, big data and the Internet of Things.
The Connected Enterprise is the foundation of the Rockwell Automation approach to

Industry 4.0 – the fourth industrial revolution (after steam, electricity and computer-driven automation) that is bringing together computers and automation in systems of data exchange that monitor the physical systems of the ‘smart factory’ and make it possible to control the operational technologies in real time. These connected technologies hugely improve information transparency and visibility into manufacturing processes, making it possible to transform operational productivity, efficiency and asset reliability as well as dealing with quality issues before they arise.
The Connected Enterprise approach is already delivering huge boosts to performance, flexibility and connectivity throughout industry, from automotive, chemicals and food processing to fibres and textiles and even entertainment.
Designing-in productivity
Rockwell Automation is working with Jaguar Land Rover to deliver flexible and productive solutions. JLR is also building a new £1 billion plant in Nitra, Slovakia, which will have an annual capacity of 150,000 vehicles, will feature many advances in auto production technology, including an ultra-fast carrier system (from Kuka) and a highly automated paint shop process that will minimise the impact on the environment.
Thomas Donato explains that one of the things that has changed in recent years is the ways in which productivity can be ‘designedin’ to new plants. “For example, our Independent Cart Technologies help move parts and products around the plant more efficiently and with less maintenance than traditional methods. This is a real gain in operations such as that of JLR where the manufacturing process has to cope with a very high degree of variation in product specification – to meet vehicle customisation demands – so it’s vital to get the right parts to the right places and to error-proof the systems.
“In fact these systems can be programmed and re-programmed to perform different functions at different times or for different throughput. These functions can themselves be altered at a touch of a screen and new functions can be added with new product lines or capabilities. This means a huge reduction in change-over times and a built-in ability to adapt to future change too.
Furthermore, when flexible new motion technologies such as these are operating in a fully connected enterprise, plant managers gain unprecedented visibility into the performance of equipment on the shop floor. This data can thus be analysed and transformed into actionable business intelligence. And bringing new levels of business intelligence from the machine level into the MES and ERP levels of the enterprise means that manufacture can become a seamless part of the whole supply chain.”
Connecting up food processing machines
Unprecedented levels of connectivity and remote management were also key requirements for Hiperbaric, the Spanish manufacturer of high pressure food processing equipment for the worldwide food industry. It was looking for a solution that would integrate all the components that shape its machines to provide higher reliability and productivity and greater energy efficiency as well as managing the equipment easily – and even remotely.
Hiperbaric met these challenges by implementing a Rockwell Automation Integrated Architecture control and information system which could interface with a plant-wide Connected Enterprise solution. Thanks to the enhanced operational intelligence delivered by the Rockwell Automation systems Hiper-
baric its customers can now access, analyse and act on production data in real time while also benefiting from the enhanced productivity made possible by the integration of all the interconnected systems.
This connectivity also allows remote management to be performed from Hiperbaric’s offices. “We can connect from any PC to all the machines we have distributed worldwide,” explains Carole Tonello, the company’s Applications Manager. “Since all key elements are in the network, we can access any of them for diagnostics, see configurations and enter changes. For us this is undoubtedly a very powerful tool.”
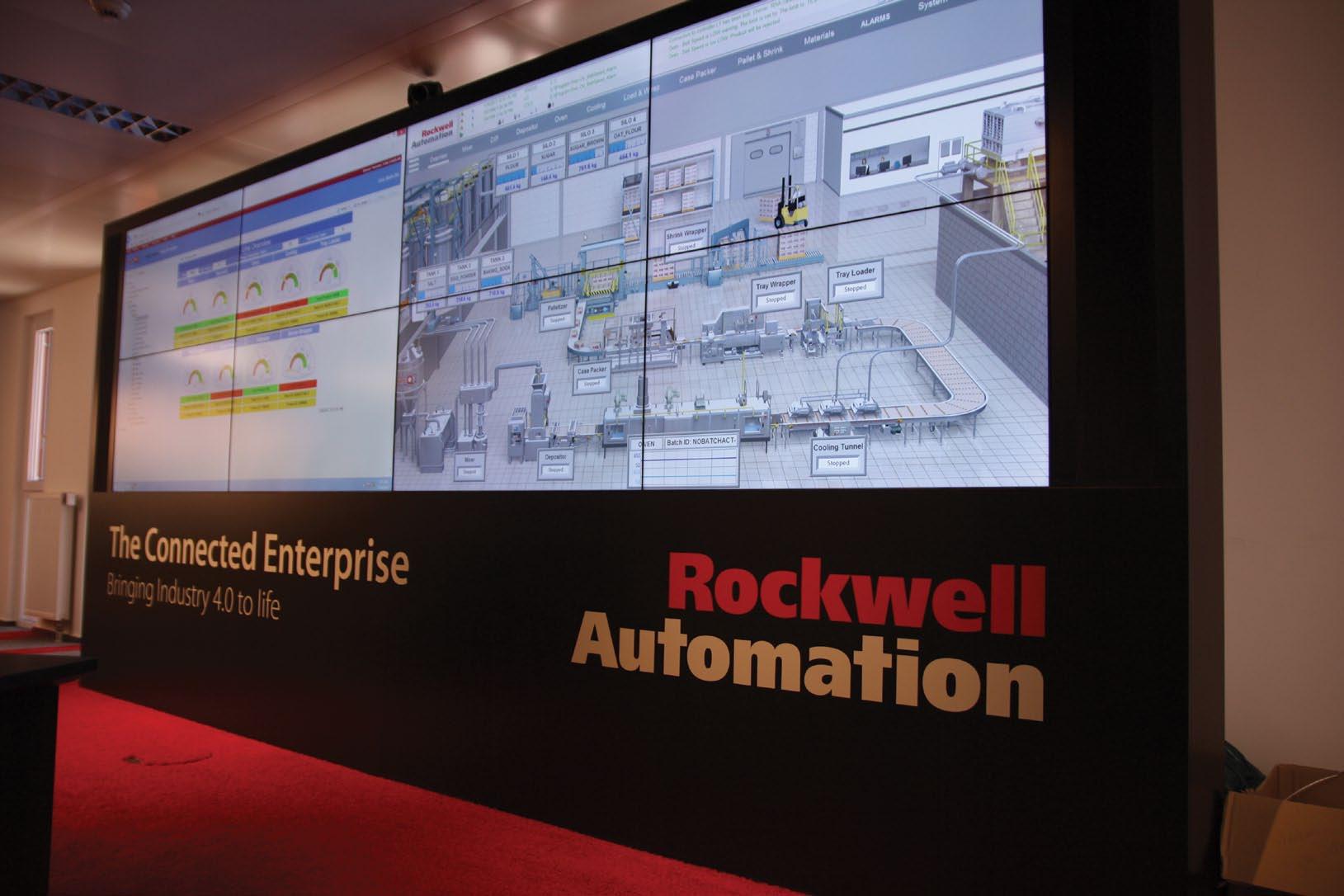
The next step – IoT
Throughout manufacturing industry in both the US and Europe, the consensus is that the next major step in the journey to smart manufacturing and the truly connected enterprise is going to be the adoption of the technologies of the Industrial Internet of Things (IoT). Rockwell Automation is currently developing new products and systems that will help organisations worldwide progress from pilot or proof-of-concept IoT projects to scalable IoT deployments.
“Manufacturers and industrial operators are discovering practical ways to apply IoT across their operations,” says Thomas Donato. “Combining IoT technology and expertise in specific industrial applications enables better collaboration, faster problemsolving and increased productivity.”
Rockwell Automation had the early chance to show how effective its IoT solutions could be when it was asked by Metso, the Finnish industrial equipment group, to develop a global industrial IoT platform that would connect, monitor and perform analytics for its mining and aggregates equipment and services.
“Metso equipment is used by mining operations in multiple locations in all parts of the world so its customers need to have the most effective possible monitoring of everything from current and projected market demand to current mine capacity and local production costs,” explains Thomas Donato. “Only complete transparency can give them the information they need to respond swiftly to changing circumstances, by, for example, expanding or reducing production levels or increasing investment.”
Metso began working with Rockwell Automation on a pilot programme in 2015, remotely monitoring an African-based mining crusher from a location in Wisconsin. The IoT solution it developed was built on its FactoryTalk Cloud platform powered by Microsoft Azure and the data collected immediately enabled Metso to identify opportunities for improvements in machine performance.
Jani Puroranta, Metso’s Chief Digital Officer, explains why the results confirmed the company’s commitment to the implementation of the industrial IoT platform on a global scale: “For our mining and aggregates customers, access to real-time data enables higher uptime, faster and safer shutdowns and ultimately more tonnage processed at lower cost. Thanks to Rockwell’s IoT platform we can now deliver analysed equipment data into the hands of our customers anywhere in the world for advanced decision-making.”
Scalable solutions
“The availability of data on an unprecedented scale is revolutionising how companies solve issues and adapt to changes,” says Thomas Donato, “but producers are now faced with

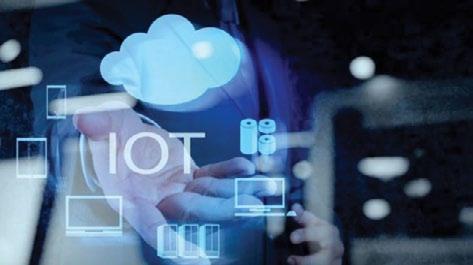
the complexity of making data useful at the right place and the right time, especially when often they lack in-house expertise in data management. So Rockwell Automation has developed very simple-to-operate scalable computing offerings that can deliver IoT data at three levels, from individual devices to the entire plant to the entire enterprise.”
At the device level ‘Shelby’ is a personal chatbot assistant that can help users to monitor performance and maintenance issues on the plant floor. It can tell you everything from the number of drives on-line to which devices have faulted. Whether you are interacting from your phone or your computer, Shelby keeps you informed on the overall health of your system and warns you when something goes wrong.
At the system level the Rockwell Automation ‘Scio’ platform opens access to ad-hoc analytics and performs advanced analysis by pulling both structured and unstructured data from virtually any existing source in the enterprise, enabling managers to make decisions when and where they matter most. It can intelligently fuse related data to deliver analytics in intuitive dashboards – called storyboards – that users can share and view.
“Scio puts analytics to work for everyone across the plant, giving users personal access to all data sources,” says Thomas Donato. “Indeed, its easy-to-use interface means that all users can effectively become self-serving data scientists – they don’t need PhDs to become expert problem solvers.”
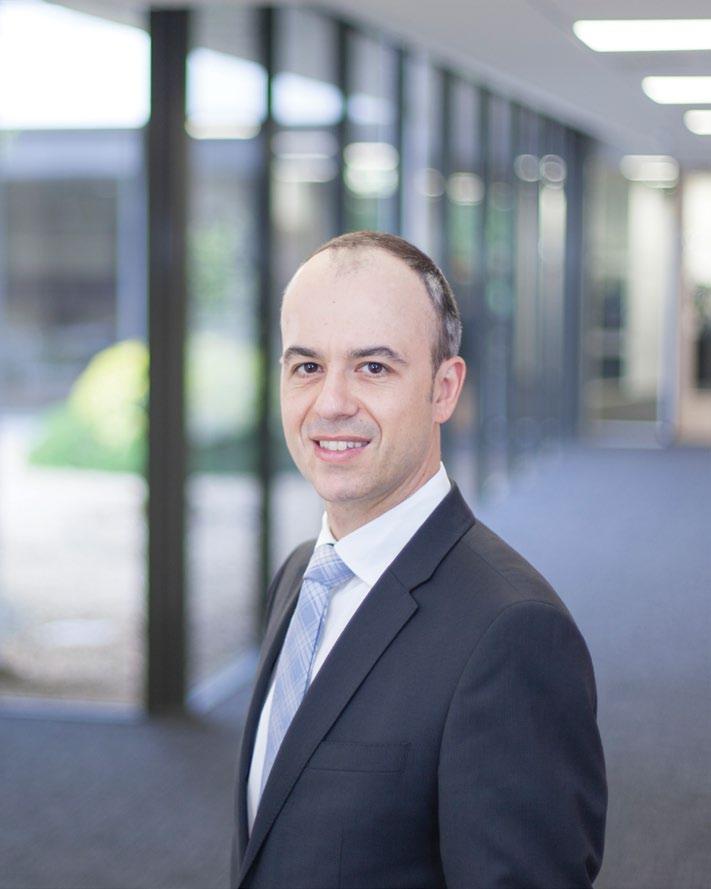
Putting AI to work
In fact, the expertise of all those data scientists that used to be needed to create diagnostic analytics solutions has now been ‘boxed’ in an artificial intelligence (AI) module that was unveiled by Rockwell Automation at last November’s Automation Fair in Houston. Once installed in a controller, the Project Sherlock AI module leverages novel physics-based modelling to ‘learn’ the application that the controller manages and build a model from the stream of data – in a matter of minutes. Sherlock then continuously watches the operation, looking for anomalies and triggering an alarm if its spots a problem. Future iterations will go beyond diagnostics to direct users on how to fix the problem or automatically adjust system parameters without any human intervention.
“Shelby, Scio and now Sherlock make smart analytics available to industrial producers in packages that are really easy to implement,” explains Thomas Donato. “As they embark on their digital transformation voyages our customers can’t wait on expertdriven analytics – there just aren’t enough industrial data scientists available and even if there were, most companies have neither the time nor the resources to employ them.
“What we are therefore developing is an expanding system of analytic offerings that run across the plant floor for devices, machines and systems and enable our customers to easily monitor and model their industrial operations. Rockwell Automation’s smart scalable analytics means that plantfloor data can be fully integrated at every level into business intelligence strategies, making The Connected Enterprise a reality for industry worldwide.” n
Thomas Donato, Rockwell Automation emeA President