
4 minute read
Focus on high performance filtration

Haver & Boecker is a global leader in the design and manufacture of high-performance wire mesh filtration solutions. Constant investment in new technology and R&D has resulted in the development of ground-breaking weave types as well as innovative automation solutions. These latest high-tech products will be showcased in March at the International Filtech Trade Fair in Cologne, Germany. Philip Yorke reports.

Haver & Boecker is an independent, family owned company with its headquarters in Oelde, Westphalia, Germany. Founded in 1887, it operates two diverse and distinct product divisions. The company’s wire weaving division produces woven wire cloth and processes it into finely engineered woven wire products. These are used for the screening and filtration of chemicals, plastics, automotive components, in aviation and aerospace, electronics, industrial and analysis screening, in the food industry as well as for architectural applications.
Haver & Boecker’s machinery division is specialised in industrial processing, transport and storage, as well as in the filling and palletising of bulk materials. The Machinery Division’s product range includes single machines and complete turnkey systems for the handling of powder-based and granulated materials, as well as for liquid and pasty products for food and animal feedstuffs. Sophisticated ship-loading and -unloading equipment is also manufactured by the company’s fast growing machine division.
Together with over 50 subsidiaries and a network in excess of 150 dealers across five continents, Haver & Boecker is a truly global player with more than 3000 employees. In 2017, the Haver & Boecker Group recorded consolidated revenues of around half a billion euros.
Taking filtration further
At Filtech in March this year, Haver & Boecker are planning to showcase their latest range of innovative filtration systems that offer advanced three-dimensional solutions. Where conventional filter cloths have reached their limits, the company’s Minimesh RPD HiFlo-S uses a revolutionary weaving technology that features highly efficient, three-dimensional pore geometry. This development provides new solutions for manufacturing industries that in turn makes specialised filter processes more efficient, more economical and more eco-friendly than ever before.
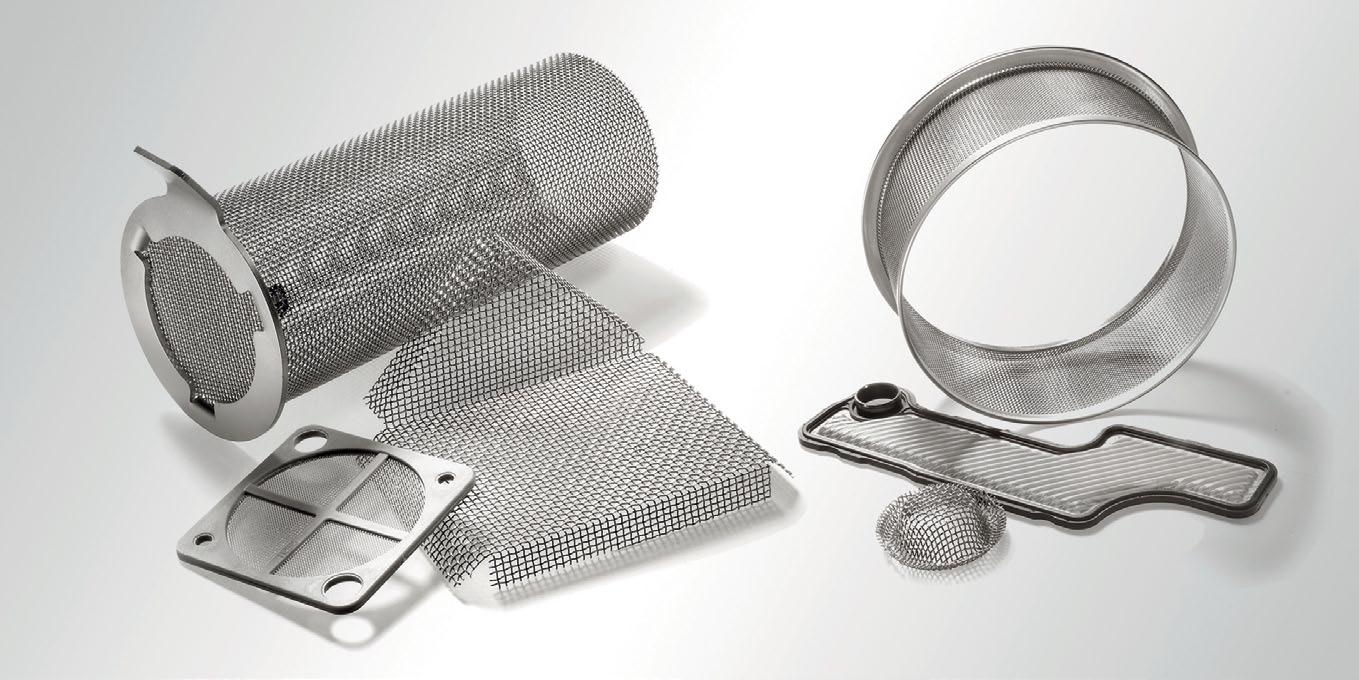
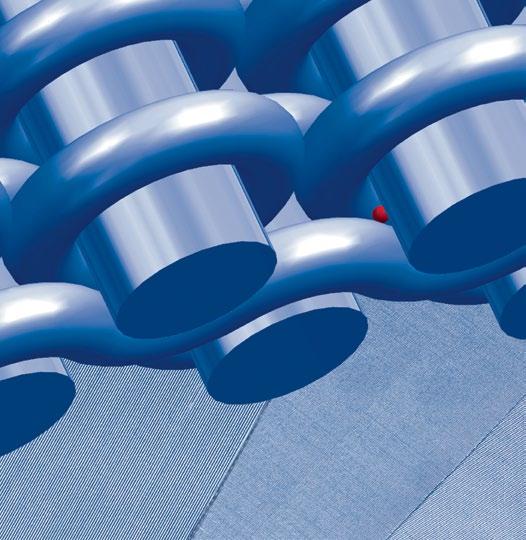
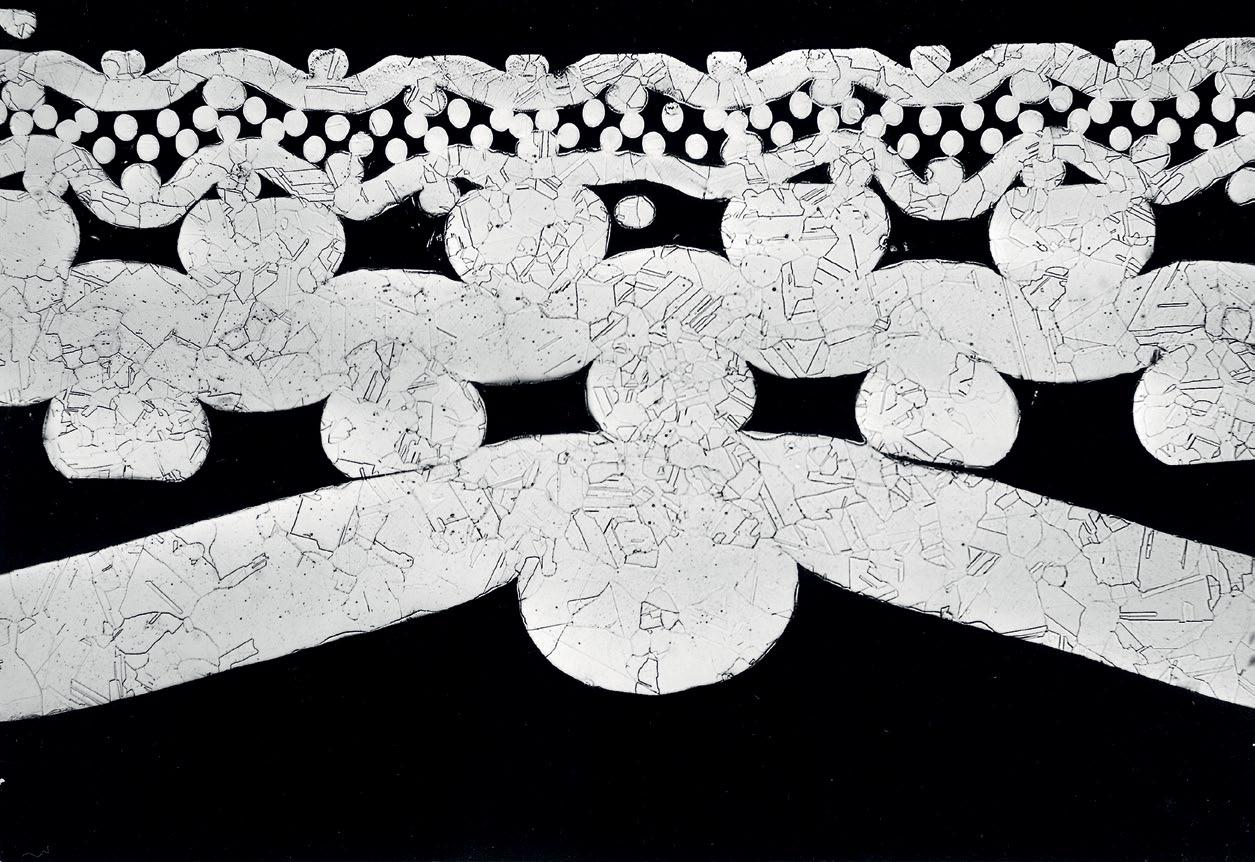
Haver & Boecker told Industry Europe, “Woven wire mesh solutions for filtration and separation make up an important part of our product range. The Filtech Trade Fair is an international platform in this field. Haver & Boecker will not only be present with a comprehensive booth, but will also be taking an active part within the conference programme itself by presenting two very informative lectures.”
The latest weaving technology from Haver & Boecker is unrivalled and means that the open surface over any given area is significantly increased due to the special weaving structure of the company’s new Minimesh® RPD HIFLO-S. The medium’s flow-through rate can easily be doubled when compared to conventional filter cloths that have the same pore size, for example the Minimesh® DTW-S.
In addition, the flow conditions are optimised and turbulence around the filter cloth effectively avoided. The unit’s pore size can also be calibrated as required, from 5um to 40um. As a result, it is now possible to weave special materials such as Avesta, Titanium, Hastelloy and Inconel in the small pore size range, which previously had not been possible. Hence, for the very first time, the RPD Hi-Flo-S offers corrosion and temperature resistant filter cloth with pore sizes below 40um.
Judith Ahlke, marketing manager of Haver & Boecker’s Wire Weaving Division, said, “Our customers’ requirements for new end products inspire our engineers, technicians and product designers to develop bespoke solutions for new product applications and developments.
These include new weave types, automation solutions and conceptualising the optimum production and testing process.”
Ahlke added, “We are constantly pushing boundaries in order to produce the ultimate solution for innovative products. This includes combining wire mesh of various designs with injection moulding for edge protection, sealing, joining, support or assembly elements, or for forming shapes. In cooperation with scientific institutes Haver & Boecker considered the design in single- and multi-layered woven wire mesh combinations for solid-liquid separation.”
New design considerations
When it comes to solid-liquid separation, Haver & Boecker thinks differently and looks beyond the standard to innovative design considerations in wire mesh combinations.
In cooperation with the Institute of Mechanical Process Engineering (IMVT) in Stuttgart, Haver & Boecker has investigated and evaluated different offline measurement techniques when using woven wire mesh in solid-liquid separation. Particle systems were also evaluated and their influence on the result of load-dependent fractional separation efficiencies and the dirt-hold capacity revealed.
The effects of different gradient structures and layer configuration in single- and multi-layered woven wire mesh combinations have been subject to extensive research. The outcomes of the research clearly demonstrated the reduction of the tendency to blocking and pressure loss, as well as improved separation efficiency and dirt-hold capacity, with optimised through-put characteristics. n
For further details of Haver & Boecker’s latest innovative products and services visit: www.haverboecker.com or attend the company’s booth at Filtech 2018 in Cologne, Germany, between the 13th and 15th March.