
4 minute read
At full speed Cooper Standard
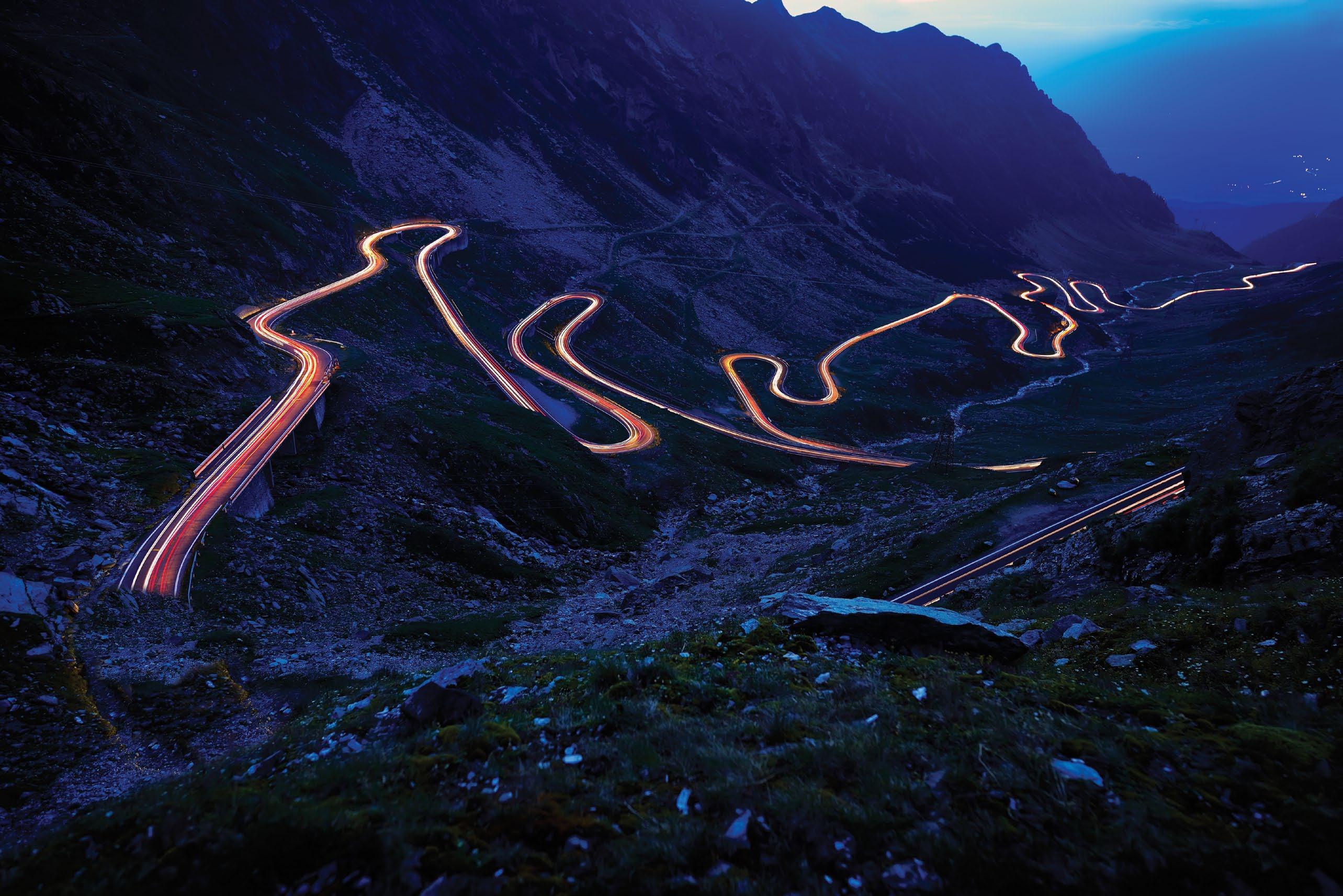
at full sPeeD
Cooper Standard, a leading global supplier of systems and components for the automotive industry, is accelerating game-changing advancements in material science to produce environmentally conscious solutions and automotive components that reduce weight, lower emissions and improve vehicle performance. At the same time, the company is increasing its research and manufacturing capabilities worldwide. Romana Moares reports.
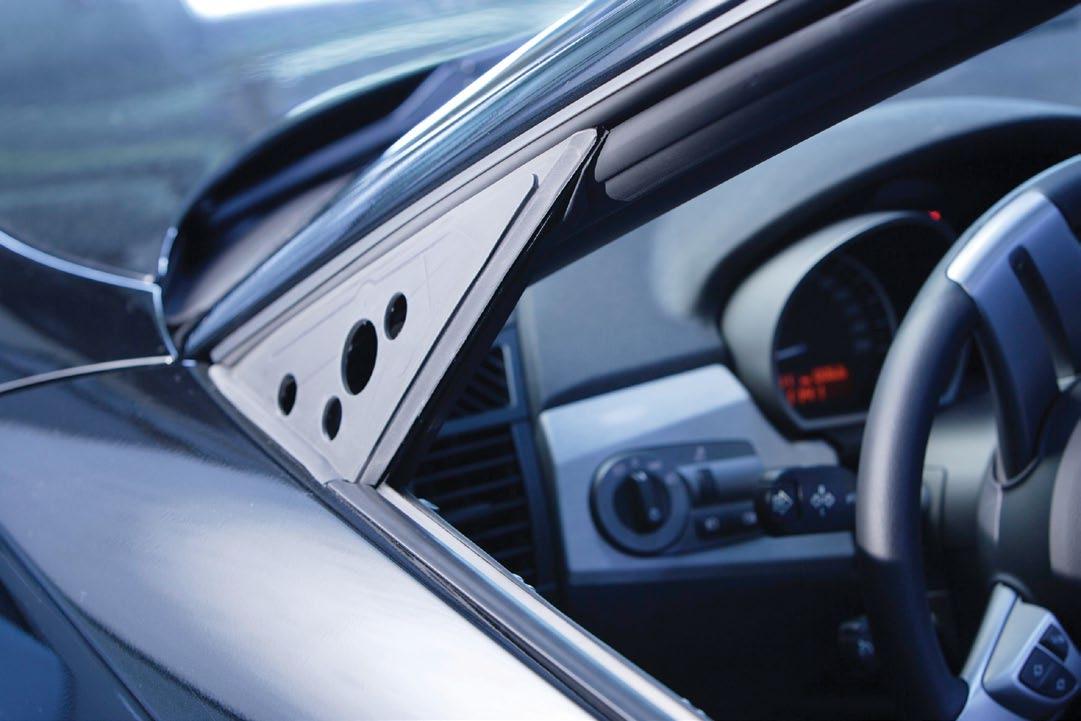
Cooper Standard has a long tradition of providing customers with the highest quality and most innovative solutions in sealing systems, fuel and brake delivery systems, fluid transfer systems and anti-vibration systems. Headquartered in Novi, Mich. USA, the group employs more than 30,000 people globally and operates in 20 countries around the world. Products include rubber and plastic seals, fuel and brake lines, fluid transfer hoses and anti-vibration systems.
Cooper Standard’s customer base includes the world’s biggest automotive OEMs. The company provides advanced engineering solutions to mitigate vehicle noise vibration and harshness (NVH), and to enhance ride and handling characteristics. It is a top five global supplier of vibration control products for powertrain, chassis and suspension components. Specialising in complete powertrain and body mount systems, its reputation is backed by extensive engineering, analysis and world-class test capabilities to meet the most demanding applications for cost, mass and performance. All the company’s anti-vibration products are developed using a costeffective, technology-focused approach, with a focus on providing system solutions to meet the most demanding customer requirements and vehicle specific characteristics. At the forefront
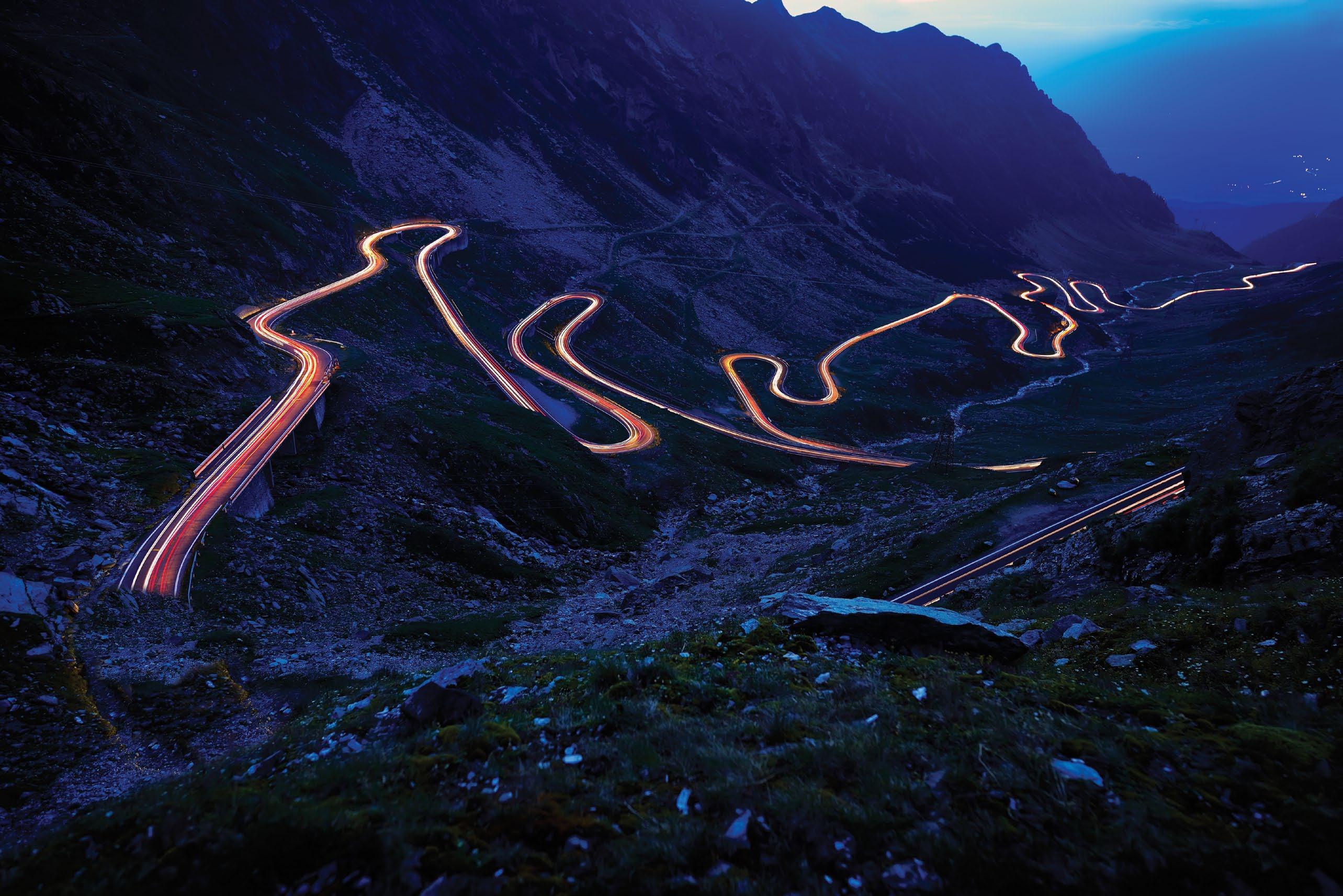
Its focus on innovation has been one of the factors that has hoisted the company to its position and remains an utmost priority today. To help customers meet the demands of the evolving auto industry and non-automotive adjacent markets, Cooper Standard recently opened a new Global Technology Centre in Livonia, Michigan. The new facility offers capabilities in material science, tooling, development, production and validation, consolidating the company’s innovation and development teams under one roof with the expertise to take products from material development to production reality.
Cooper’s innovative contribution was awarded in October last year when the company was named as a finalist in the 2018 Automotive News PACE Awards for its Fortrex™ lightweight elastomeric material. The new class of material is providing game-changing advances in weight reduction and enhanced performance in automotive sealing, an area that until now has not experienced significant material innovation in decades.
The Fortrex™ material combines the best attributes of EPDM (ethylene propylene diene monomer) and TPV (thermoplastic vulcanizate) materials, which are typically used in sealing, while eliminating

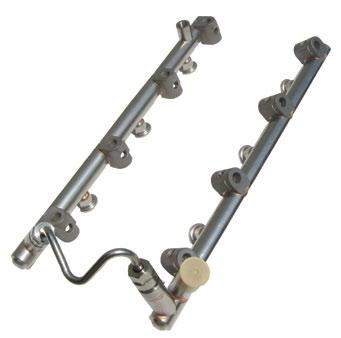
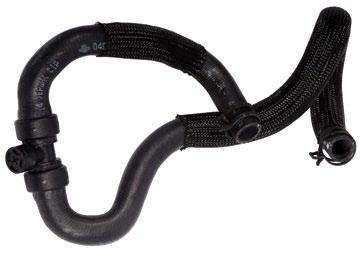
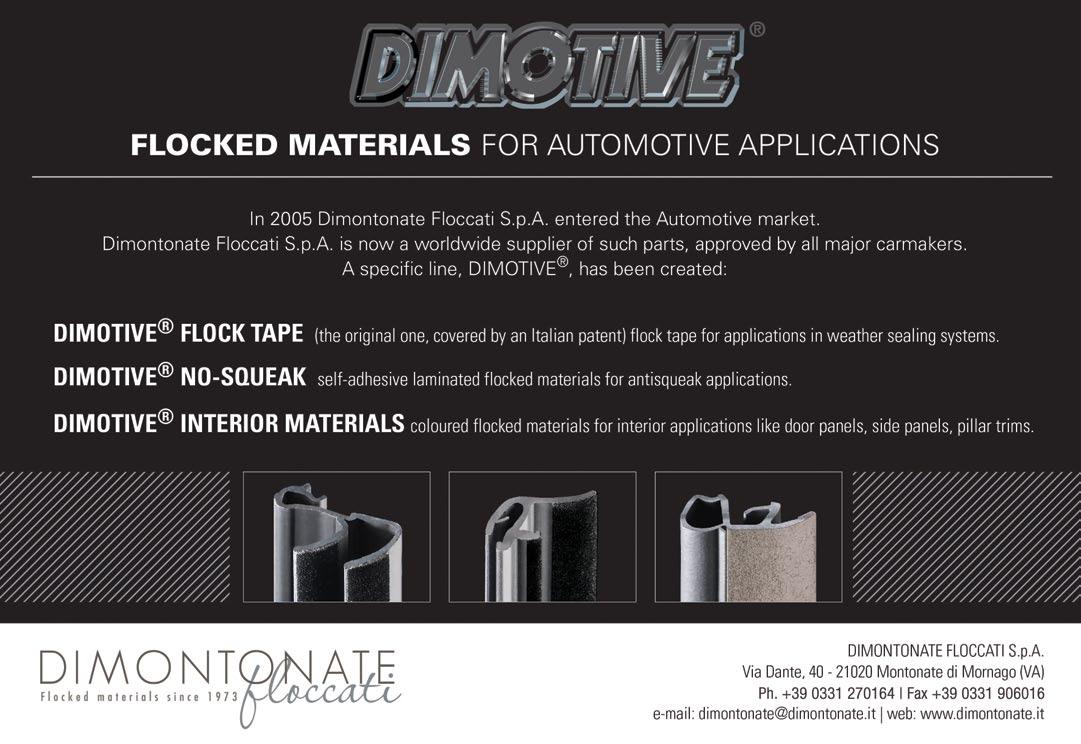

their negative aspects. Fortrex™ offers weight savings of up to 30 per cent versus traditional EPDM, while avoiding the compression set issues associated with TPV, resulting in superior sealing systems and reduced cabin noise. It does not weather or bloom like EPDM and can be accurately colour-matched. Fortrex™ is non-conductive and has a remarkably low carbon footprint across the entire material and production chain. In addition, Fortrex™ is a dynamic material platform that can be modified for an endless list of applications and performance solutions within automotive and related markets.
In addition to technological innovation, Cooper Standard is committed to ecological and environmental improvement and its continuous research programme is designed to improve the company’s overall carbon footprint. Cooper Standard’s extensive research and development department is clearly focused on research that is directed towards improving products in ecological terms, as well as in terms of better performance and more competitive pricing.
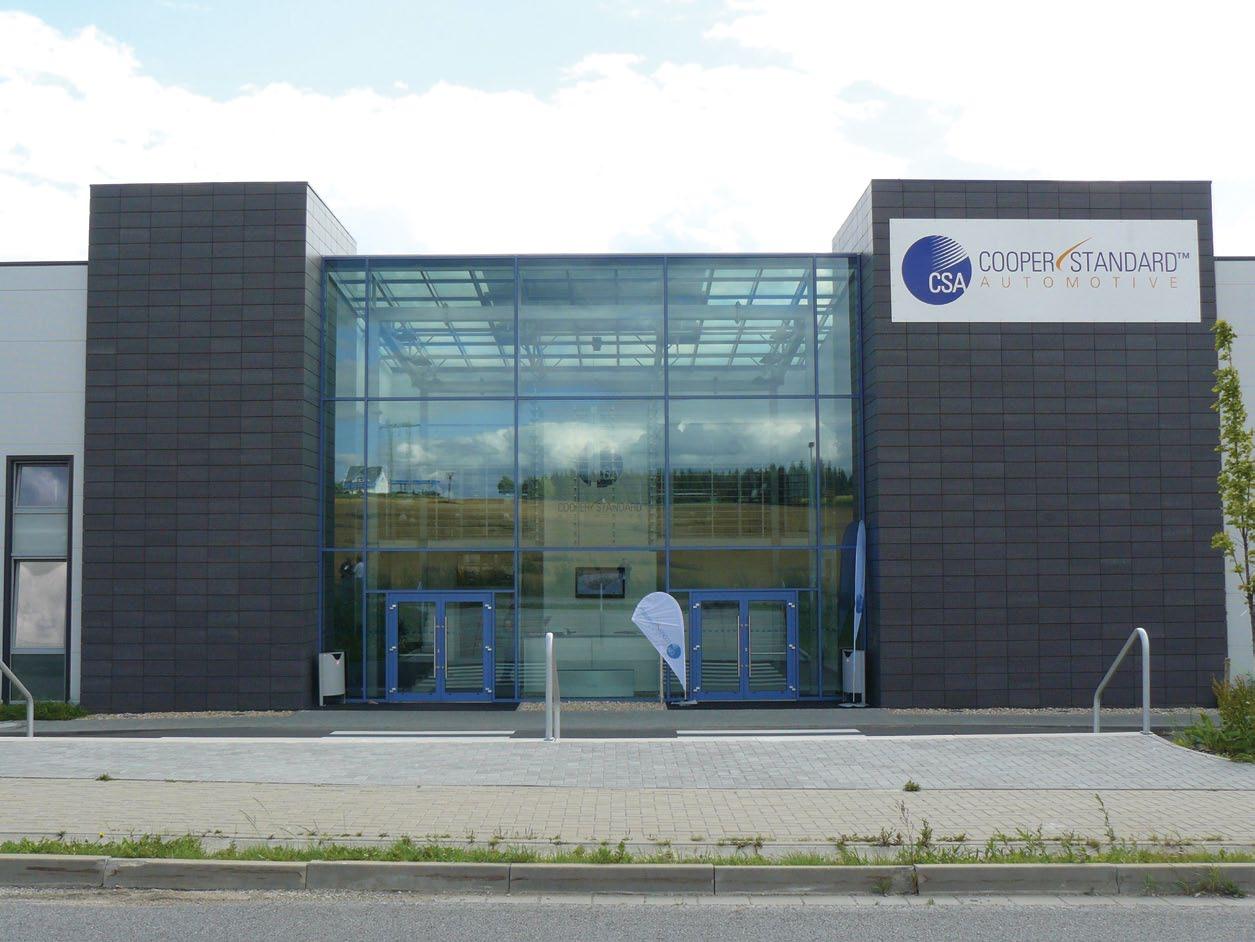
Committed to growth
In the last few years, the Cooper Standard has been significantly increasing its global technical capabilities as well as its manufacturing presence. In addition to its new innovation centre in Livonia, it is investing $1 million to expand its manufacturing facility for coolant tube and hose assemblies, transmission cooling lines, and fuel and brake lines at Surgoinsville, Tennessee, in response to customer growth.
Focusing on China, Cooper Standard has accelerated its business development programme in the Asia Pacific area in recent years. In a bid to further boost its presence in Asia, currently consisting of 17 plants with nearly $600 million in revenue and about 5300 employees, the company recently opened test and prototype centres in Shanghai. The test and prototype centres are located about 30 miles from the firm’s regional headquarters in Shanghai, also the home of its regional technical centre. Currently, the two centres combined employ about 50 engineers, but that number is expected to increase. The prototype centre focuses on material science development and prototyping new technologies. The test centre will concentrate on validation and testing, both designed to support the regional research and development centre.
The recent investment demonstrates Cooper’s commitment to further strengthening its position. Technological leadership, combined with broad product expertise and capabilities, high quality global resources, as well as its customized set of global best practices designed for quality and lean initiatives, are solid foundations on which Cooper can build as a top global automotive supplier. n
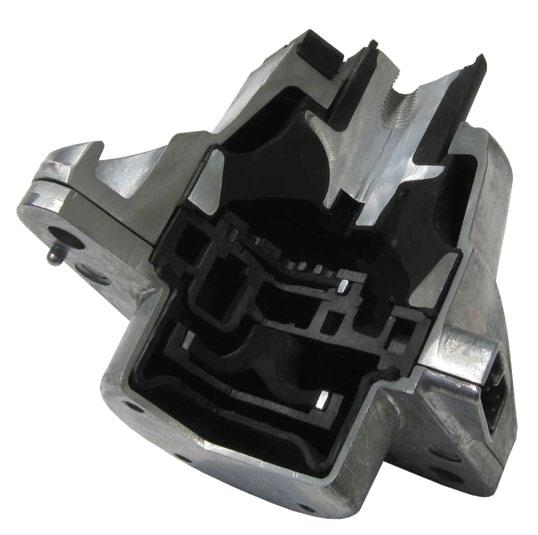