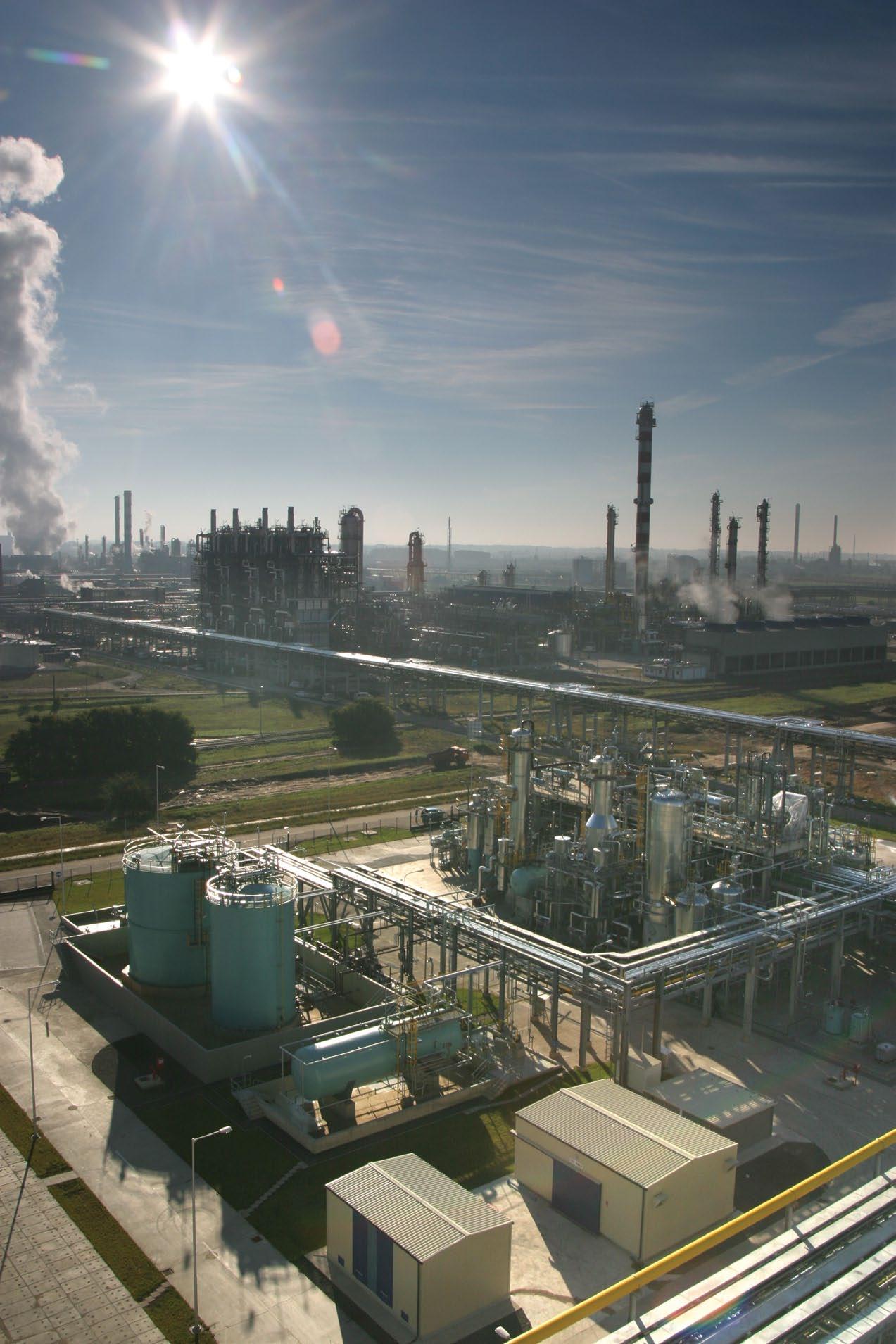
6 minute read
Ambition for success MOL Petrochemicals
aMBITIoN FoR SuCCESS
The MOL group in Hungary is preparing for a giant investment to extend the petrochemical activities at MOL Petrochemical Ltd’s Tiszaújváros plant in Hungary. The new industrial facility will introduce polyol production while creating hundreds of jobs in Hungary’s most deprived region. Edina Beale reports on the details of this new project.

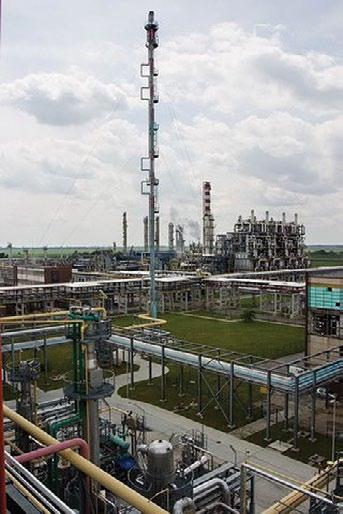

Headquartered in Budapest, Hungary, MOL Group is a leading integrated oil and gas corporation with operations in over 33 countries and 26,000 staff worldwide. MOL’s exploration and production activities are supported by more than 80 years’ experience in the hydrocarbon field. The group operates four refineries and two petrochemical plants in Hungary, Slovakia and Croatia, while its retail network consists of more than 2000 filling stations in 10 countries across central and south-east Europe.
From crude oil to plastics
As part of the integrated Downstream Division of MOL Group, MOL Petrochemicals Ltd, along with the petrochemical unit of SLOVNAFT in Bratislava, develops optimised refinery and petrochemical production processes in accordance with the group’s philosophy ‘from crude oil to plastics’.
Established in 1951, MOL Petrochemicals Ltd, formerly known as Tisza Chemical Group plc, holds a leading position in the petrochemical sector in central-eastern Europe. The company engages in the production and wholesale distribution of olefins, petrochemical products and polymer products. It produces and supplies ethylene, propylene and other olefin co-products to chemical and oil companies. It also produces and supplies a range of polymer products, including low-density polyethylene, unimodal and bimodal highdensity polyethylene, polypropylene copolymers, and homogeneous polymer primarily to plastic processing companies. It exports its products to Italy, Poland, Germany, Slovakia, Romania, Austria and the Czech Republic.
Aid granted for gigantic investment
The European Commission has recently found Hungary’s €131 million investment aid to MOL Petrochemical Ltd’s Tiszaújváros plant to be in line with EU State aid rules. This support will contribute to the development of the northern Hungary region, while enabling the group to remain competitive in the single market.
Among other things, the investment aid granted by Hungary will support MOL’s plans to invest a total of €874 million to introduce the production of polyols and propylene glycols in its existing plant in Tiszaújváros. Polyol is the main component of polyurethanes, which are used for the production of foams for car seats, dashboards, coatings, adhesives and sealants – amongst many other things. Propylene glycol is primarily used in the production of polymers, but is also used in food processing, personal care products and pharmaceuticals.
This new industrial facility will produce an annual total of 200,000 tonnes of propylene oxide, which will be used by MOL to create polyol



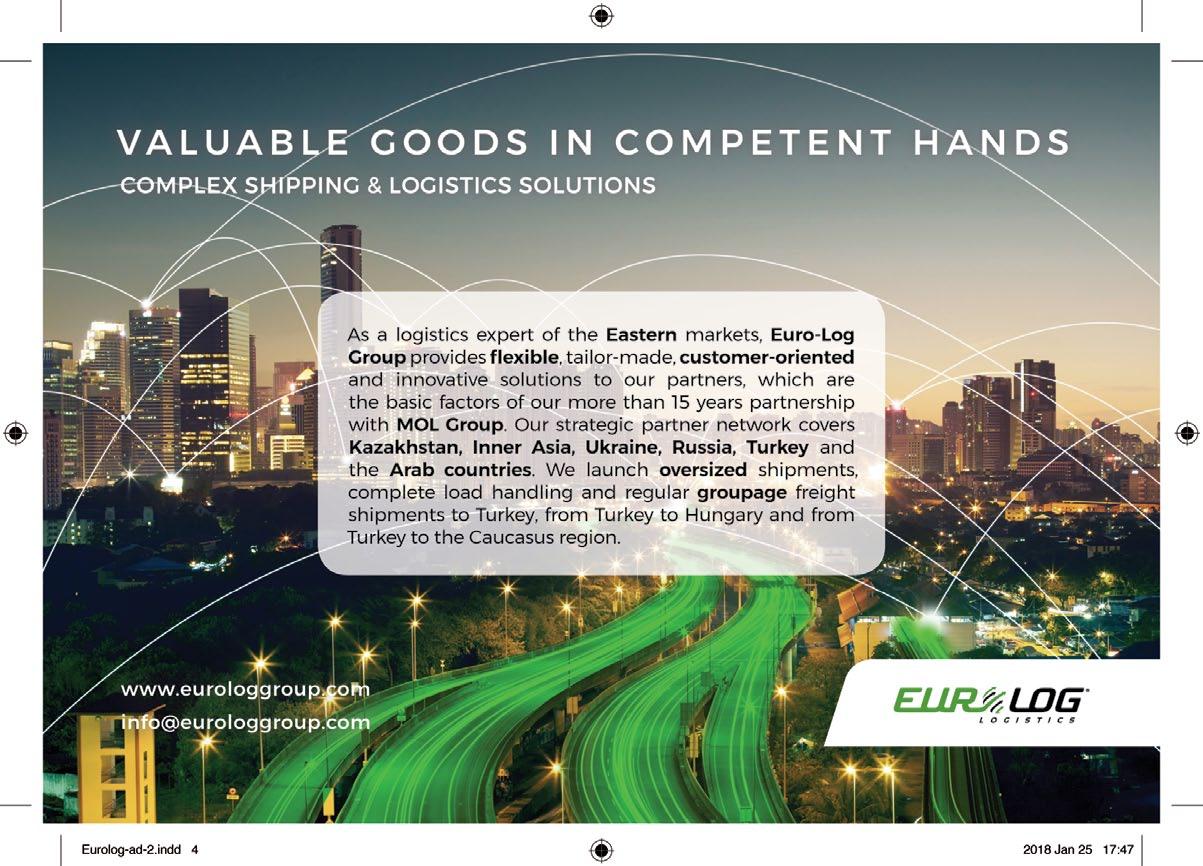

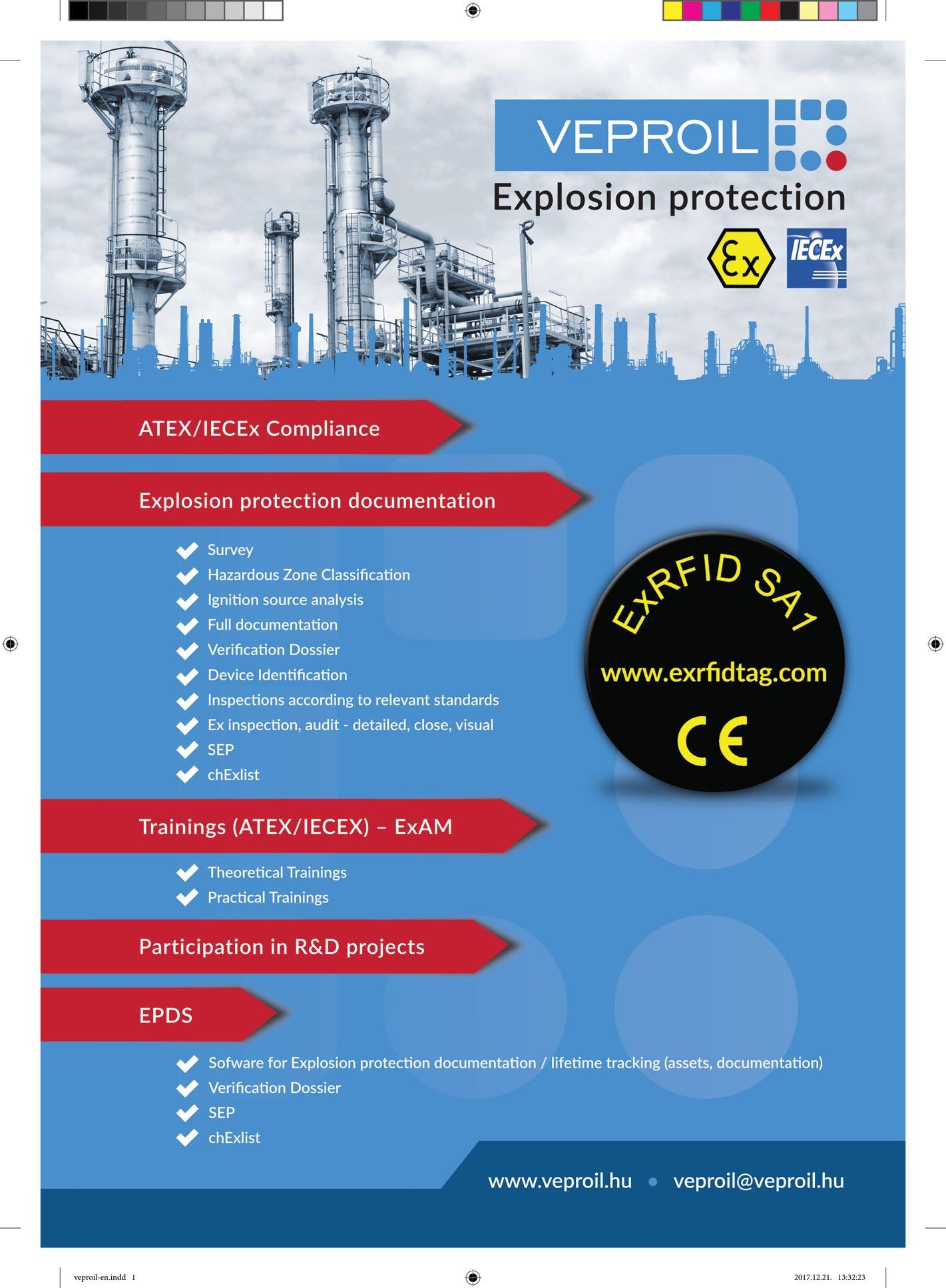
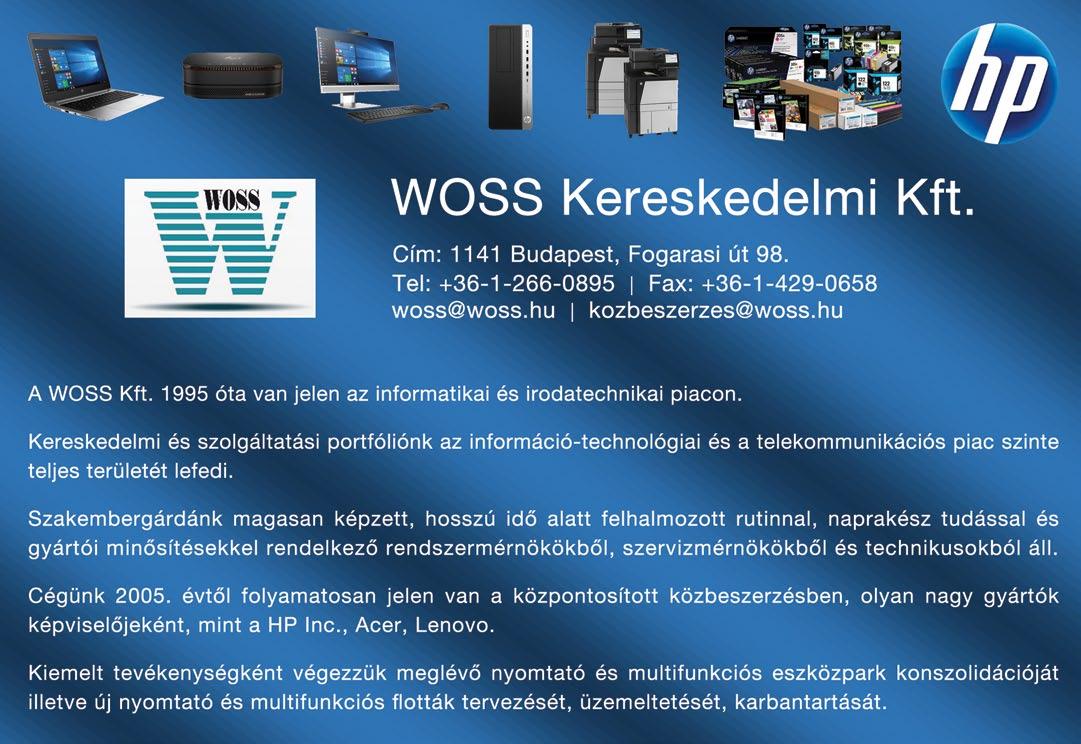

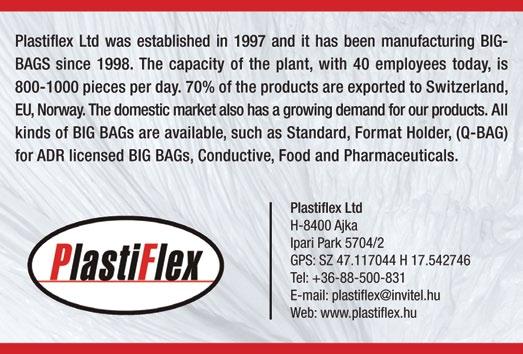
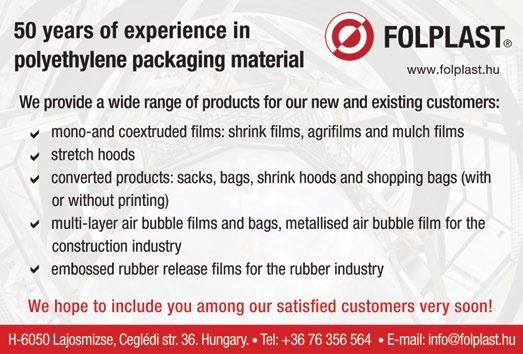
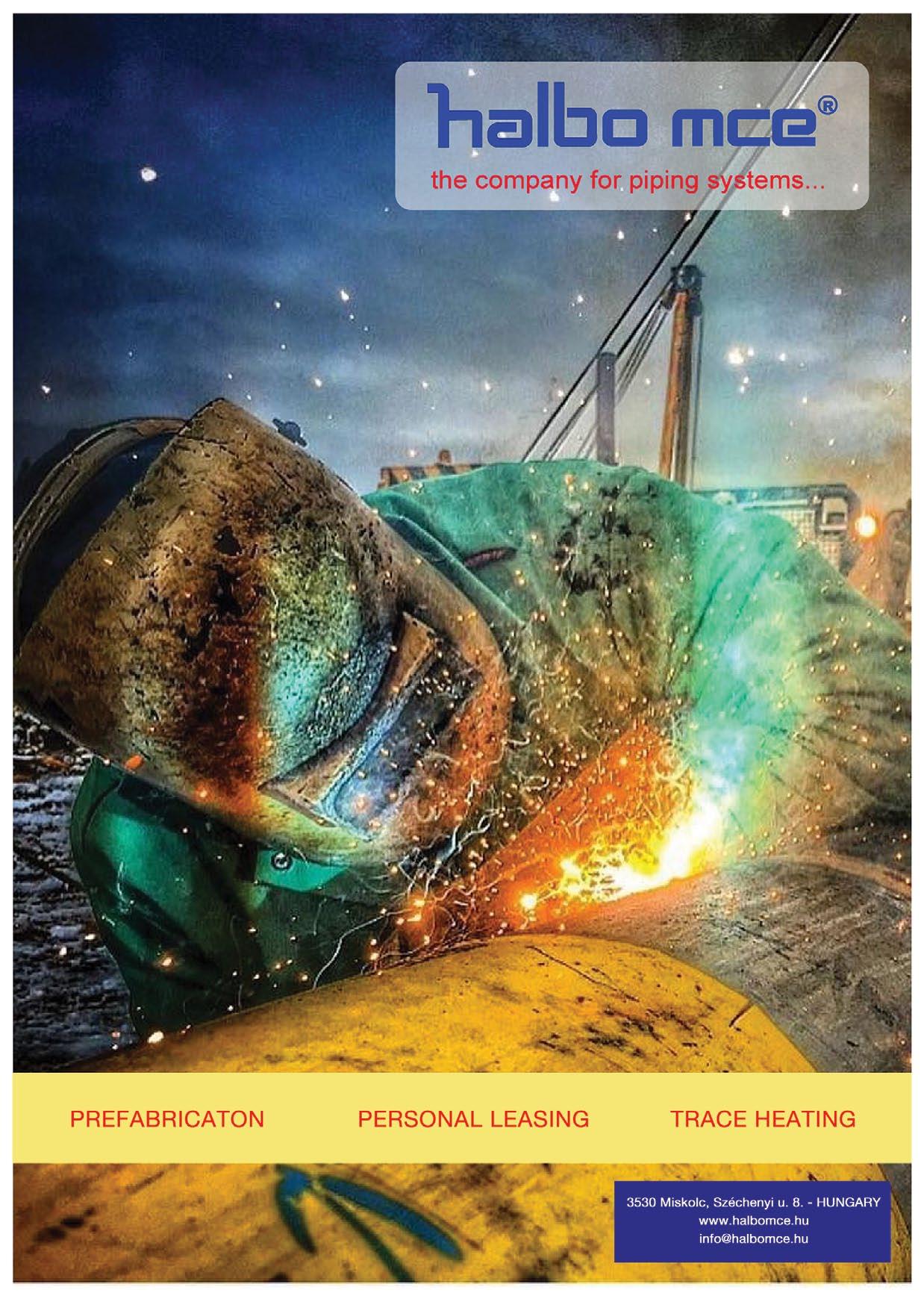
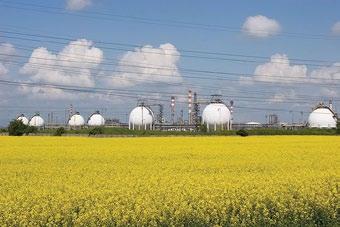
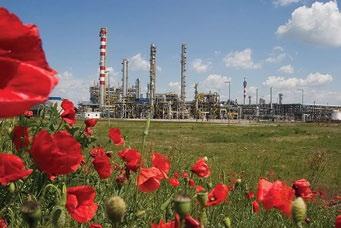

products. The facility will consist of many different units: besides the propylene oxide plant there will be several polyol production lines. Polyurethane plastics made from polyol are used worldwide in the construction, automotive, packaging and furniture industries.
organic and industrial investment
According to the plans outlined in MOL’s 2030 long-term strategy, the group intends to invest around 4.5 billion dollars into the petrochemical segment between 2017 and 2030. The new modern complex of facilities will be built in Tiszaújváros and it will be the largest organic investment project, both for MOL and for the region as a whole, in the next five years.
According to Zsolt Hernádi, MOL chairman and CEO, this will not only be a special investment for the chemical industry but also for Hungarian manufacturing as a whole. He said: “The new petrochemical plant will produce 15 per cent of the European polyol production with zero emissions, and its production could increase the Hungarian GDP by 70 billion forint per annum. We spend on average 100 billion forint a year on investments. Tiszaújváros plays an important role in the MOL Group, as we have world-class plants here. Thanks to the petrochemical investment we will be able to create the region’s largest chemical conglomerate, and the MOL Group will be the only company in central and eastern Europeto carry our integrated production of this product.”
Plans for new Budapest headquarters
In accordance with its ambitious strategy plans for the next 15 years, the MOL group has made the decision to establish a brand-new headquarters that will provide the required working conditions for a multinational group. The new headquarters will be constructed in a new quarter of the XI District in Budapest, and will be named ‘MOL Campus’. The 28-storey building, due to be completed by 2021, will be 120m high.

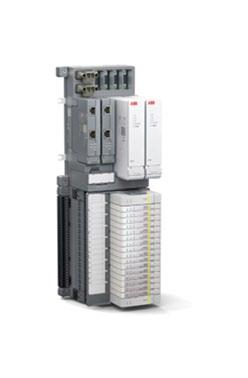
systeM 800xa’s select i/o funDaMentally changes
autoMation Project execution
For decades, automation projects have used controller-centric distributed control system (DCS) architectures. Such architectures create a significant number of interdependencies between project tasks that can easily lead to considerable cost overruns and delays should any change orders be implemented. ABB has developed a new I/O family – complete with engineering tools and methodologies – that eliminates this scenario and takes project efficiency to the next level, making over-budget or late automation projects a thing of the past.
One example of project interdependency is when a “design freeze” is declared before hardware purchase, which, in turn, has to precede application engineering, and so on.
Any changes to the design, like changing I/O types, adding I/O, moving I/O to a different controller, etc., require potentially costly change orders due to the amount of work needed to make changes after design freeze.
In response, ABB has developed an extension to the System 800xA family of I/O solutions called Select I/O. Select I/O is a single channel I/O solution for both process and safety applications that commun cates with the system via a redundant industrial Ethernet I/O network.
The Select I/O terminations can be installed and wired in the field early in the project phase, obvia ing the need for space-consuming marshalling cab nets. The signal types can be defined much later by adding individual signal conditioning modules, which reduces the financial impact of any late changes.
With the multiple clusters of Select I/O commun cating on a redundant Ethernet network, the I/O can be automatically scanned, configured, and checked in the field in parallel with the application enginee ing being done in the ABB project factory. This paralleling is called “xStream” engineering and includes soft marshalling capabilities that automatically converge the two workstream deliverables – ie, the application engineering project and field I/O configuration – just before final commissioning.
The result is that automation is removed from the overall project critical path. Fewer surprises, fewer change orders, earlier commissioning of projects and happier owner-operators is the result. n
