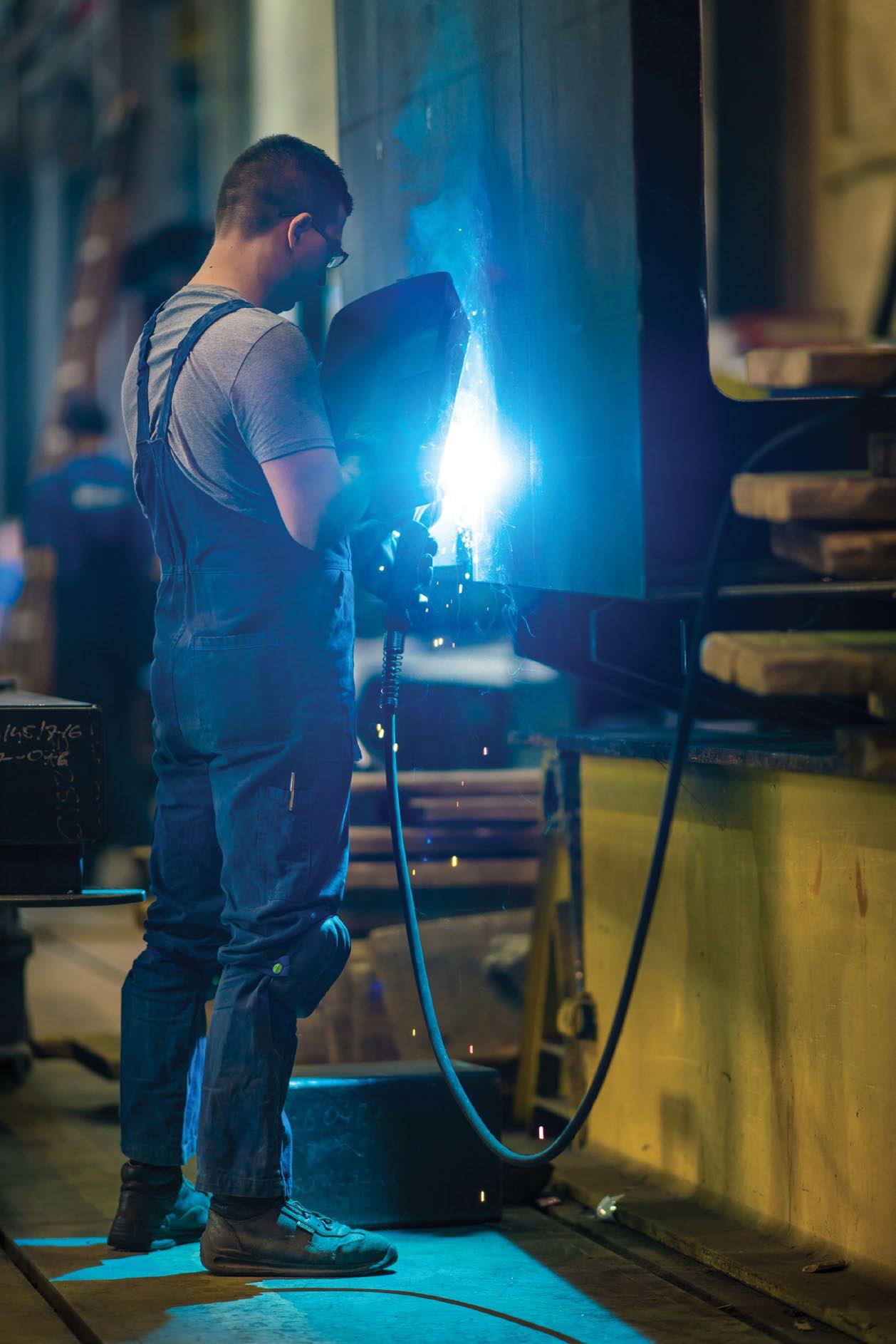
4 minute read
metal specialist Primabiro
Welding process
montage hall
Metal sPecialist
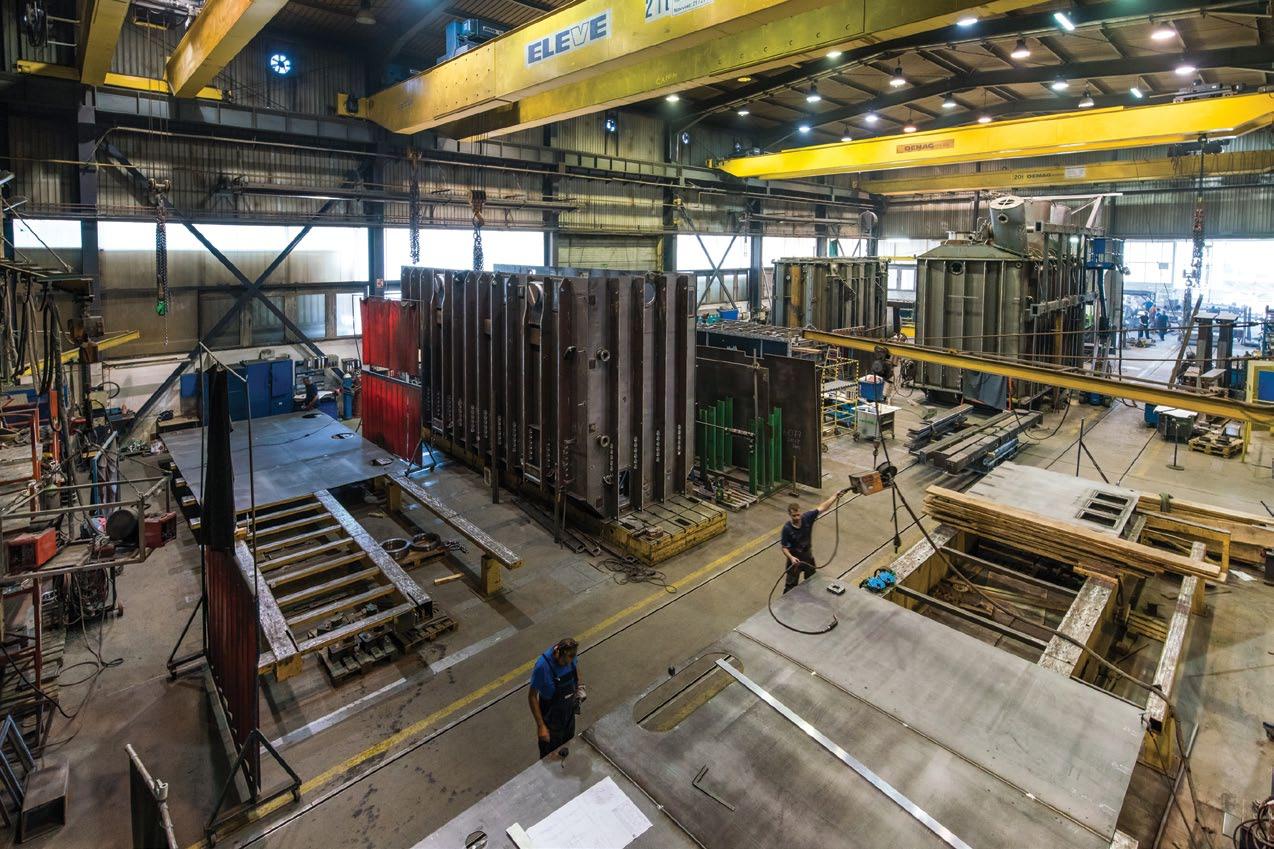
Metallurgy is not the word that instantaneously comes to one’s mind with reference to Croatia. However, the country has a sound manufacturing base and Primabiro, a manufacturer of high voltage transformer casing and other heavy metal structures, is one of the companies that have managed to capitalise on thenew opportunities of the last two decades and win a reputation as a reliable partner to European producers.

Primabiro directors mr. Željko mezga and mr. Stjepan Pongrac
Primabiro, based in northern Croatia near the Hungarian and Slovenian border, is a family-owned enterprise managed by two partners, Željko Mezga and Stjepan Pongrac. The company, today employing 340 people, was founded in 1992 and this year commemorates its 25th anniversary as a successful operation in European metallurgy markets.
In the early 2000s, the business was carried on in four separate locations but in 2004 the company bought a manufacturing plant and consolidated all activities into the new premises. In 2005 the modernisation of production halls was completed, providing the company with 3350 square meters of covered manufacturing areas and 750 square meters of offices. In 2006 the company focused on incorporating welding technologies into the portfolio and achieved the DIN 17700 part 8 welding requirements, an important prerequisite for increasing its European market share. Today they are holders of EN ISO 3834-2 Comprehensive quality requirements and EN 15085-2 - Welding of railway vehicles and components.
“We are a metal processing company and our core business includes all kinds of heavy metal structures, “says CEO Željko Mezga. Our primary products, reflecting our knowledge and experience, are metal casings for high voltage transformers for customers including Kolektor Etra d.o.o. Ljubljana/Slovenia, Starkstrom-Gerätebau GmbH Regensburg/Germany, Royal SMIT Transformers B.V. Nijmegen/Netherlands, Siemens Europe, CG Power Systems Belgium NV Mechelen/Belgium, Preis&Co. Ges.m.b.H. Pernitz/Austria and others. They account for 90 per cent of our current production, representing around 330 tons of finished product per month.”
Investment - key to the future
He further explains that the production process includes technical drafting, metal sheet, profile and pipe cutting, machining, welding, metal part assembly and anti-corrosion surface treatment. “The production flow is structured to ensure a line production process from raw material input to
Inspection
the finished product output,” he says, adding that continuous investment is an integral part of the company’s strategy, aiming to secure further growth and development of new production processes and capacities, deploying new modern machines and technologies. “We pay particular attention to education and training of our employees as well as safe working conditions,” he affirms.
Since moving into the new premises 15 years ago, large sums have been invested in capacity extension as well as technology modernisation. The latest major investment has been spent on the installation of a new technology for incoming material shot blasting. “In 2018, we plan to complete the investment in increasing production capacity to ultimately have 10,000 square meters of roofed aria, housing a line process production of metal casings for high voltage transformers. This will further boost our capability to fully meet customer requirements both in terms of product quality and delivery terms. After this, we will further invest in technology upgrade and modernisation, safer working conditions and professional staff training,” explains Mr Mezga.
The design and structure of the new halls meet all applicable environmental regulations. As the technological process involves production of metal structures, it has no negative impact on the environment.
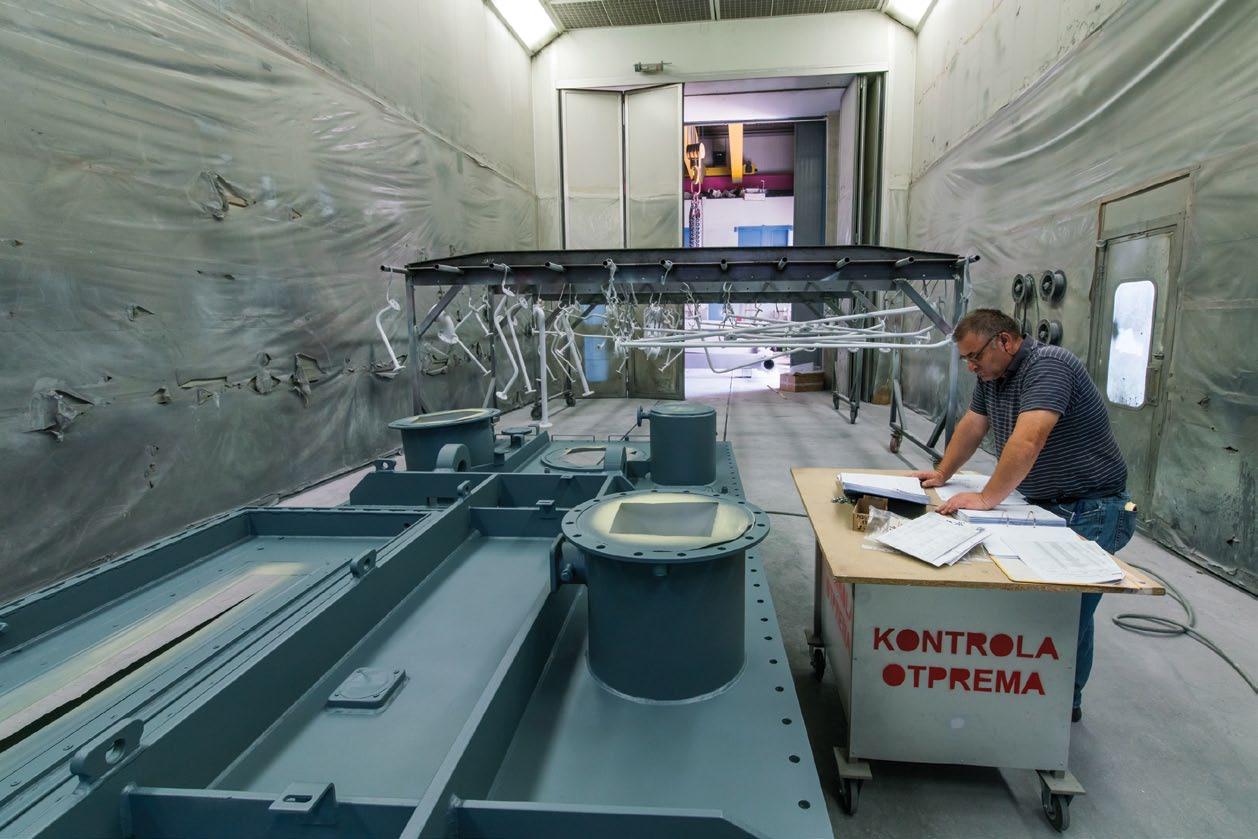
Challenges and opportunities
Asked about the key competitive advantage that has enabled the company to penetrate and successfully operate in the sophisticated and highly competitive West European markets, Mr Mezga says: “We guarantee the quality of our products to customers with all required fea-
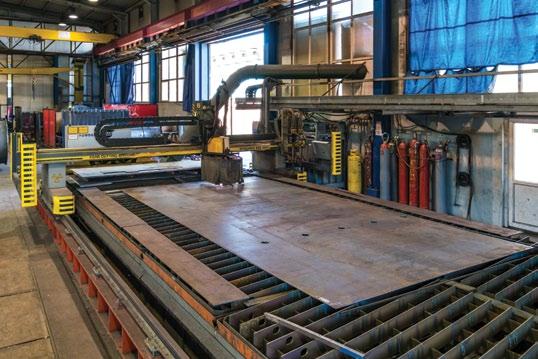

tures duly in place, reflecting the quality of construction and welding and including the appropriate anti-corrosion protection of the final product.”
“The biggest challenge we are currently facing is the outflow of labour due to unfavourable labour conditions in Croatia on the one hand, and the opening of the European labour market on the other. The number of people attracted to better working conditions aboard is rising, resulting in a shortage of quality workforce at home. Nevertheless, we strive to provide our workers with adequate salaries, professional training and other benefits in order to retain skilled workforce. To offset the continuing requirements from customers to reduce the product prices against the ever-increasing labour cost as well as other work-related expenses, such as in the improvement of the work environment, is quite a challenge.”
However, despite the challenges, Mr Mezga confirms that the company is well on track towards its mission - to continue to be a reliable and trustworthy partner for its customers. “We remain committed to providing high-quality products and services to our customers in the demanding world energy market.” n
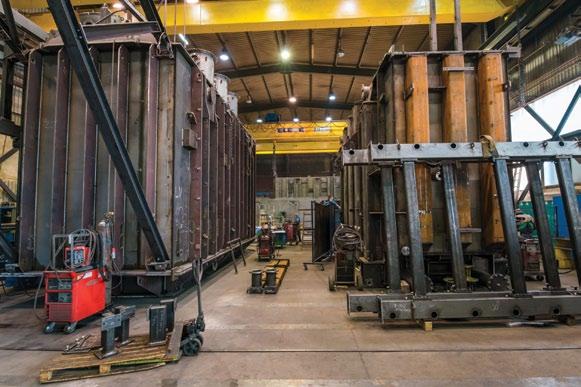
Probing installation (Trial installation of trafotank )
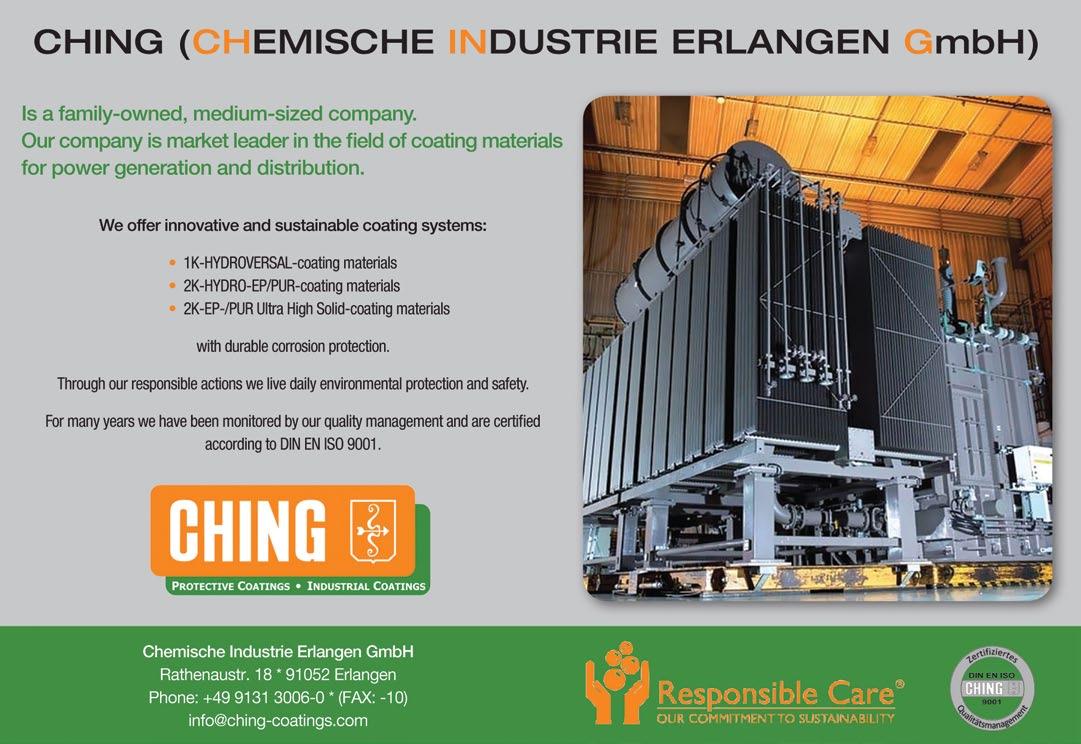