
5 minute read
Advanced technology for container production
STRUMET, a company from Strumien, Poland, is one of the leading European manufacturers of steel containers used in transportation and storage systems.
STRUMET was founded in 1995, following the privatisation process of the state-owned company that faced a crash at that time. “Our first task was to get the company out of debt,” Wojciech Szczypka, the STRUMET vice-president and production director, recalls. “Since then, we have continued to grow. We have invested more than 90 per cent of our return into the company’s development. The long path we’ve been through for 23 years can be illustrated by the increase in the company’s employment. In the 1990s, our team was only 45–50 people, now we employ 520 people, have 60 external workers and 500 subcontractors. In total, 1100 people work for us.”
In 2005, STRUMET received the certificate of the Quality Management System to the ISO 9001 standard. The company also has the certificate forFactory Production Inspection according to EN 1090 and the quality certificate of welding works according to EN ISO 3834-2. The Galvanising Institute in Gliwice has classified STRUMET to the 1st Large Plants Group pursuant to the requirements of PN-M-69009.
In March 2008, the company opened its Hot Dip Zink Plant, which is one of the largest plants of this kind in Poland. It is equipped with state-of-the-art devices and machines that make it possible to obtain high zinc-coat quality combined with high efficiency. In 2015–2017, the fire galvanising line was modernised and extended. A new chamber with pickling kettles was also commissioned and a kettle for liquid zinc was replaced with a larger one.
Since 2012, many investments have been made in new technologies, galvanising, warehouses, CNC hall and powder coatings. The indoor production space increased to 45,000m², while the company’s total area covers 10 ha. STRUMET’s annual sales in 2016 were estimated as PLN 220 million (€52.4 million), including PLN 175 million (more than €41.6 million) from export sales. STRUMET sells its products all over Europe as well as to Turkey, Mexico and the USA. In September 2017 STRUMET received Environmental Management System certification according to the ISO 14001:2015 standard.
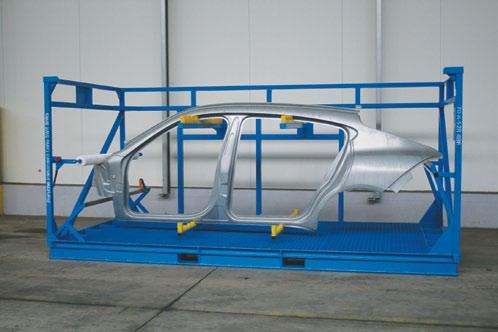
Delivering know-how and comprehensive service
The company’s production volumes in 2016 amounted to 36 thousand tonnes of steel processed into metal containers and 22 thousand tonnes of galvanised parts. The automotive industry accounts for 95 per cent of STRUMET’s total sales. It works in close cooperation with such big names in the automotive sector as the Volkswagen Group, Daimler Group, Jaguar Land Rover, Pirelli and Continental. The company’s products are also used by the metal industry, the chemical industry, the construction industry and many more.
“Most of our products constitute containers made to special orders, tailored to the client’s individual needs,” explains Mr Szczpka. However, we are not limited to selling our products, we offer our clients our knowhow and comprehensive service, including assistance in choosing a proper type of container matched to the customer’s specific needs. We can implement designs from scratch; we prepare technical documentation, and manufacture the container prototypes, which may be tested by a client before the series production. We can make almost every kind of construction according to the customer’s requirements. Nothing is impossible. We have our own design office equipped with modern CATIA V5, Autodesk Inventor and NX Siemens software, tool room and prototype room, thanks to which we can draw up a design virtually for every container type. Modern and cost-efficient machines as well as high technology production lines enable us to complete orders fast and on time.”
The basic materials for container production are semi-finished steel products, including: sheets, flat and round bars, squares, round and rectangular pipes, and so on. STRUMET has close relationships with reliable suppliers. Each delivery is certified and inspected by the Factory Production Inspection. All materials are stored in roofed warehouses.
Since welding is the company’s basic technology, it uses highquality welders, and the process is supervised by qualified controllers as well as scientific research institutions. In 2014, STRUMET initiated the robotisation of welding processes with the installation of three robotised Comau welding posts.
“We rely on the latest technologies and cost-efficient machines to ensure the high quality and competitiveness of our products. In recent years, we have considerably extended the department of computer operated machines (CNC). We have numerically controlled automatic machines for cutting pipes, numerical presses, CNC machining centres, laser pipe cutting machines, laser metal sheet cutting plotters, pipe bending CNC posts and many more modern machines,” says Mr Szczypka.
The containers are produced in powder-painted or hot galvanised versions. STRUMET owns two powder shops – an automated line and a large size powder shop. The galvanising process is carried out on a hot galvanising line. The company can also produce containers in cold-galvanised versions and is about to open a new department for plastics processing.
experts in zinc coating
Zinc is a metallic chemical element that is present in the natural environment and is not harmful to the environment; it is even a necessary element for living organisms. Moreover, zinc can be recycled. The hot-dip zinc coating (plating) process known as zinc coating by
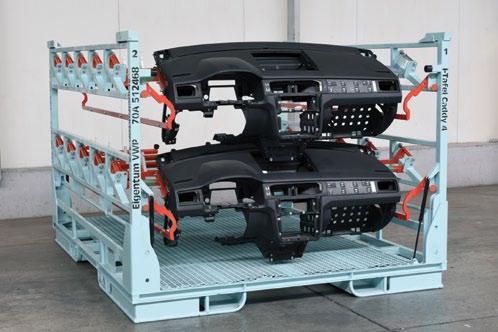

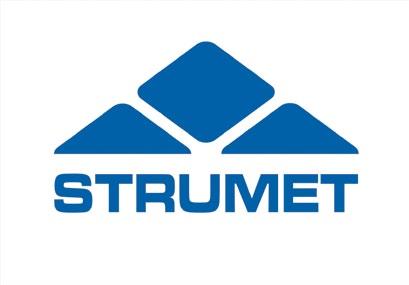
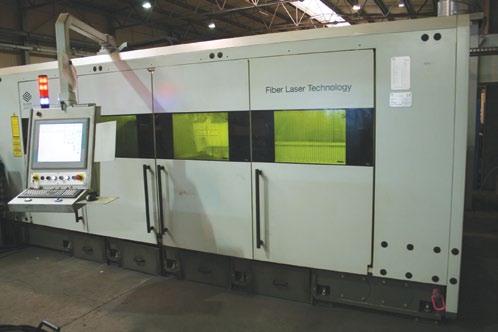
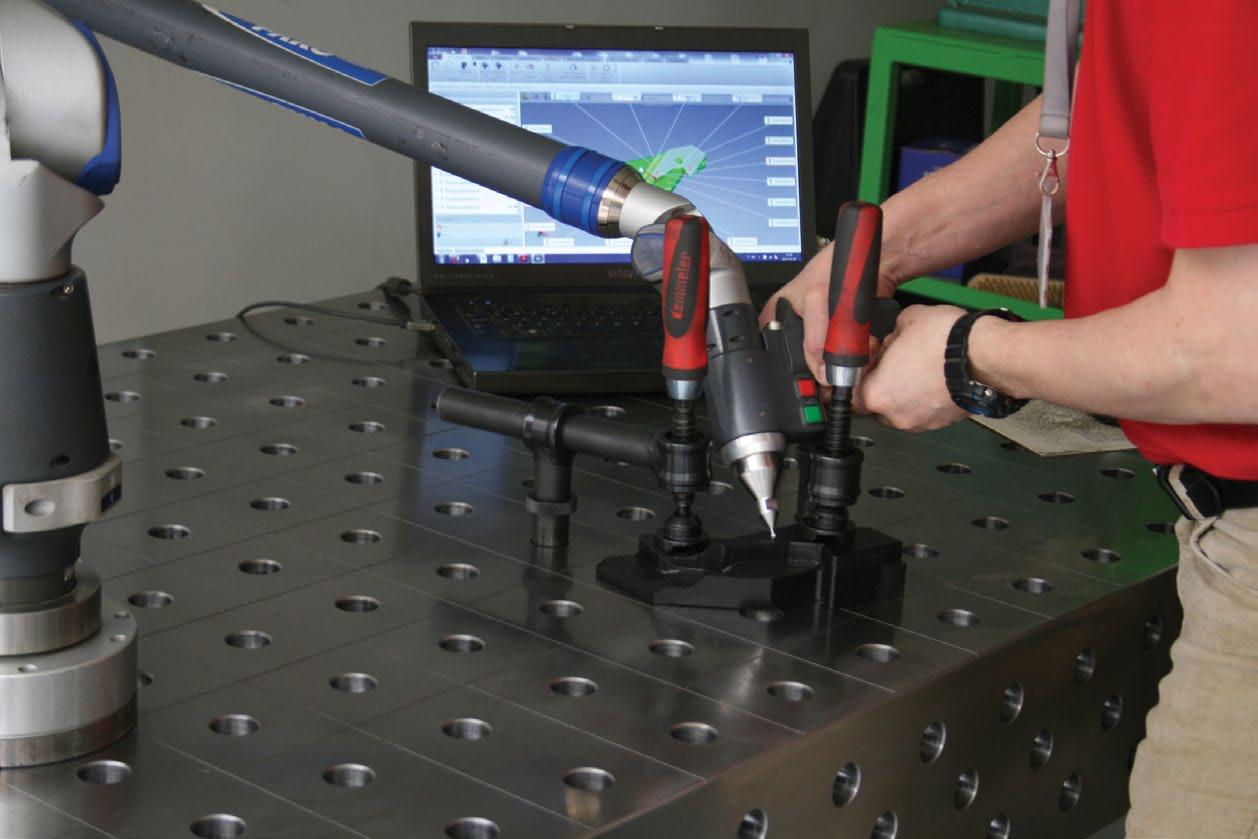
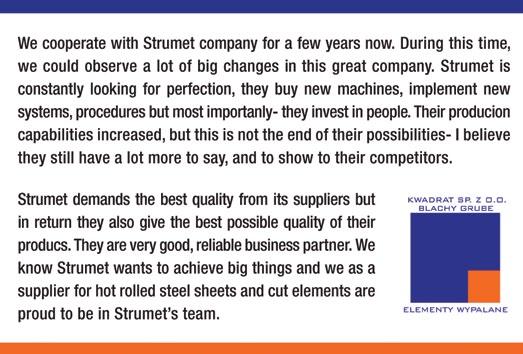
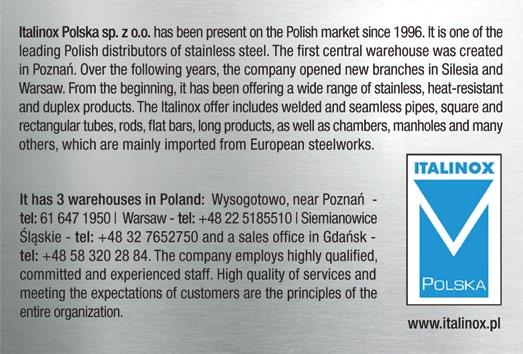
immersion, currently used by STRUMET, is one of the most efficient methods of steel structure rust-proofing. The coat features high mechanical resistance and aesthetic appearance. Average zinc loss in a structure in use ranges from 1–2 µm per year (for use under nonaggressive conditions). Therefore, the average working life of zinc coats is 30 years, but it can reach even 100 years.
The STRUMET Zinc Coating Plant is equipped with modern environmental protection devices. All process tanks are closed tight and equipped with extractors. They are provided with a chemical leakage protection system fitted with pumps and buffer tanks that can cope with simultaneous tightness loss in a few tanks. Tank extractors are connected to an absorber to prevent chemical vapours from being released into the environment. The Zinc Coating Plant releases no liquid waste, because process solutions operate within a closed circuit.
Visit: www.strumet.pl
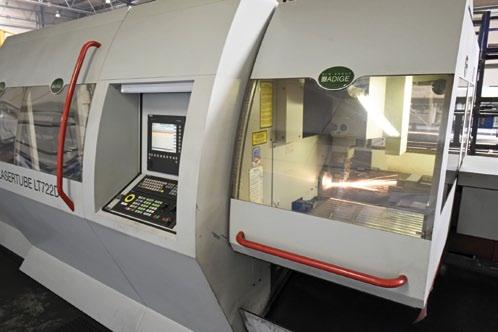

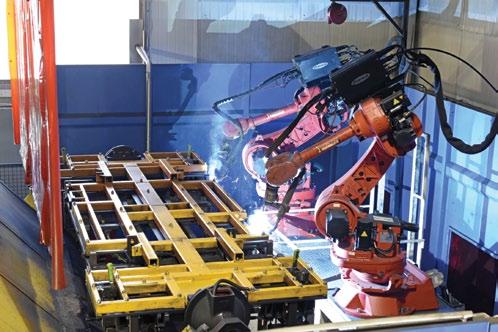