
4 minute read
A single supplier for end-to-end ceramic production SITI B&T Group
A sIngLE suPPLIER foR EnDTo-EnD CERAMIC PRoDuCTIon
With its new patented technology Supera®, SITI B&T Group is amongst the world leaders in the production of turnkey plants for the ceramic industry, focusing on innovation, quality, flexibility and energy efficiency. Daniele Garavaglia reports.
Aleading global player in the production of fully-fledged systems for the ceramic industry, from clay preparation to the final product, and with a presence in all markets, SITI B&T Group, a company from Sassuolo – the heart of the world’s ceramic district – is a leading player at every stage of the production process. The company offers technological excellence and innovative service solutions, with a focus on energy efficiency and reduced manufacturing costs. The Italian group moved into the segment of large ceramic sheets through its innovative Supera® technology, designed using the most progressive techniques in the sector, through advanced and intelligent automation and patented systems.
“Supera® is a technology devoid of moulds and foundations, and it does not require special transport. It allows for the creation of large sheets with a wide variety of thickness (5–30mm) and size,” explains Cinzia Gervasi, marketing manager. It has a production capacity of up to 13,000m2/day (44,000 tonnes), considering a raw thickness of 10mm. The possibility of making raw or fired cuts of the sheets in different subformats allows for high manufacturing and material storage flexibility. “Basically, we reproduced the typical benefits of traditional pressing on a discontinuous tape press. The innovative movable plate system for dust containment can overcome the scraps constraints. The system consists of a mobile partitions-forming device, hydraulically fed during the ‘pressing’, while the breathable system of the press enables the correct de-aeration through a semi-porous membrane. The result is higher production efficiency.”
Supera® is characterised by a significant aesthetic versatility: you can have up to 10 surface structures simultaneously. It is also possible to quickly change the structure in less than 15 minutes, thanks to a fast buffer / format release system. The initial research and development for the Supera® line resulted in the evolution of the Start-Stop system: launched in 2014 for the Evo 3.0 presses, it features an engine system equipped with inverter pumps, capable of powering the press on demand, “a device that reduces the energy requirement of the forming system by about 30 per cent.”

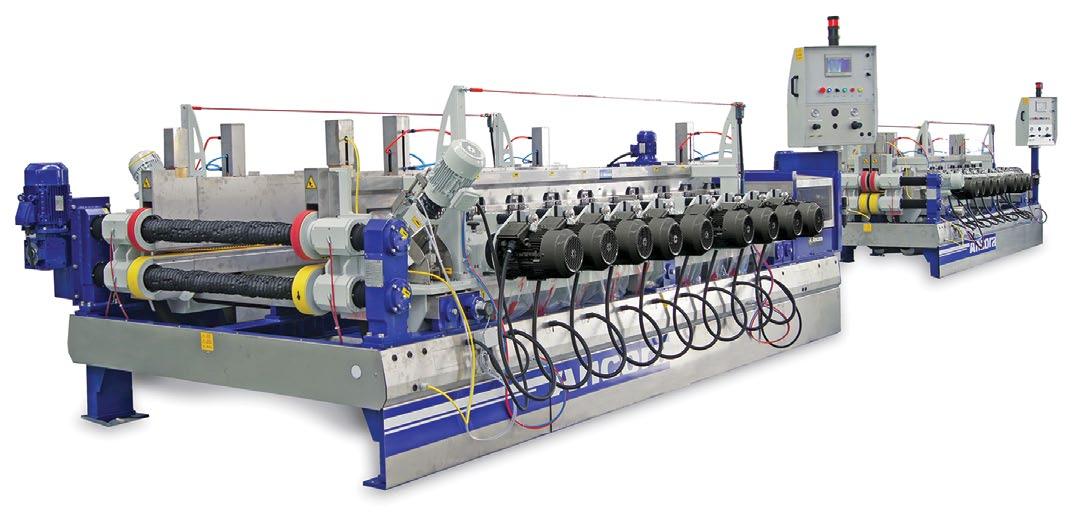
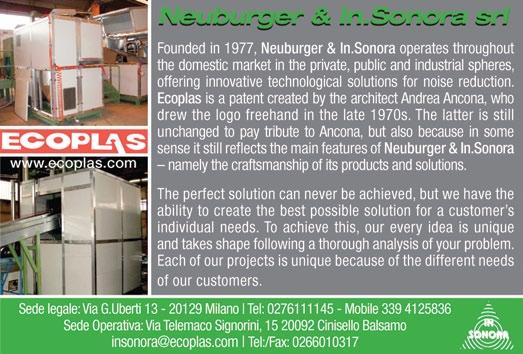
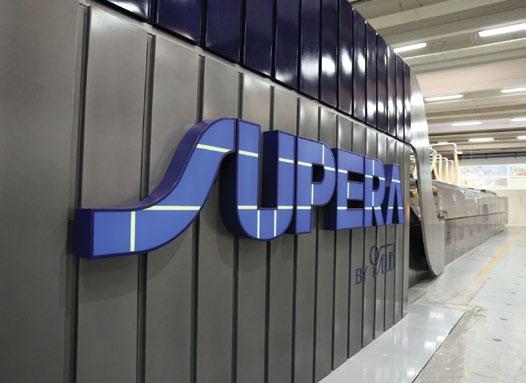
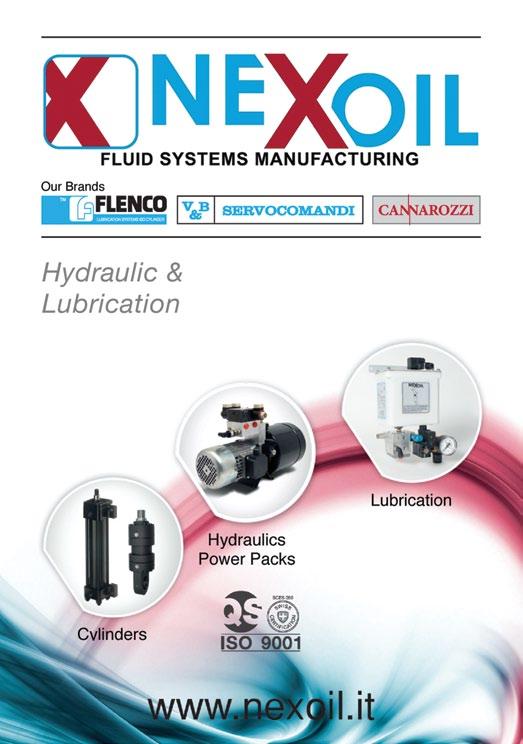
Comprehensive services
Today SITI B&T Group is the only supplier able to offer integrated and innovative technology solutions for the entire production line of large ceramic sheets, from the preparation and characterisation of mixtures (made by the advanced technology centre in Formigine) to pressing, drying, glazing, firing, handling and storage; all supervised by a single integrated system, which ensures remote control of all stages and manufacturing process benchmarks.
“In our technology centre, we provide many services to customers: starting from the study of raw material to testing, implementation and prototyping of new products, thanks to the possibility of implementing laboratory tests and harnessing the entire Supera® full line technology,” adds Cinzia Gervasi. For clay preparation, SITI B&T can provide integrated solutions for both wet and dry grinding. The Dryfast® mills range for the dry grinding of ceramic mixtures, available in different sizes, has many interesting features: a series of rollers treated to resist wearand-tear; high efficiency classifiers; differentiated treatments according to clay abrasiveness and output granulometry constancy. The granulating machine Grainmix is an extremely versatile solution: depending on requirements, it allows for the creation of moistened or granulated powders. The production process is completed by Evo 3.0, presses featuring cutting-edge technology for better pressing and with a reduction in tile casting defects; and by Titanium®, the innovative kilns for the firing of ceramic sheets that, thanks to their exclusive burners, are at the absolute leading edge of energy efficiency, reducing fuel consumption by over 30 per cent.
Digital decoration is guaranteed by the partner Projecta Engineering, in association with Digital Design, which offers a combination of different technical capabilities, extremely flexible for perfect synchronisation between digital graphics, structure and dry (or wet) application of substances. The G5 modular printer, a combination of the main winning features of Evolve range, is a paradigm of total flexibility. The end of the line is guaranteed by Ancora finishing technologies, ensuring maximum efficiency, productivity and quality: technologies such as Dry Squaring, a saw intended for the dry working for all types of ceramics, including porcelain tiles, with exceptional energy- and cost-savings. n

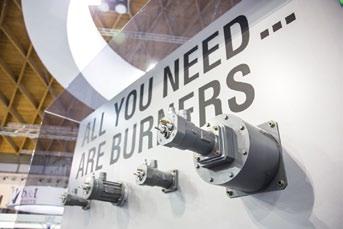
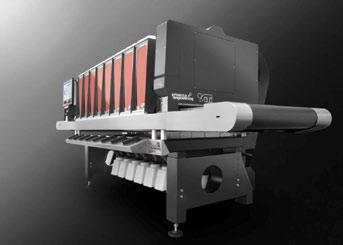