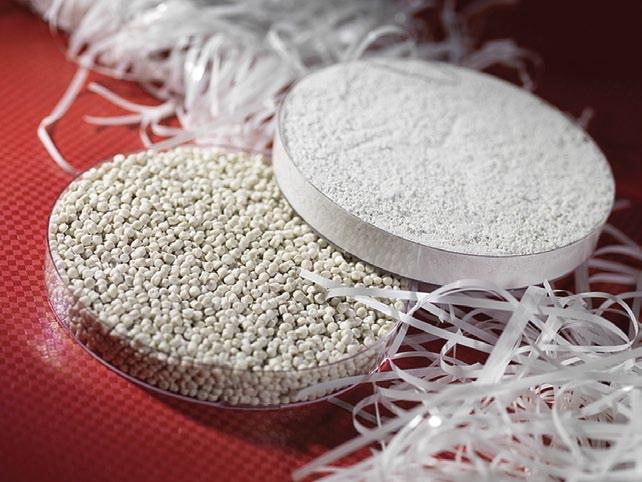
5 minute read
Star performer Starlinger
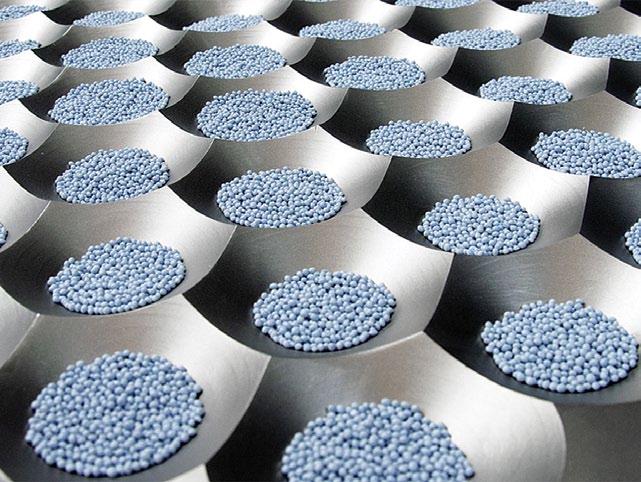
star performer
Starlinger Recycling is a global leader in the design and production of machinery for the recycling and refining of an infinite range of modern plastics. The company’s advanced Reco-Star systems are unique, world-class products. Starlinger is also a global leader in the manufacture of woven plastic sacks. Philip Yorke reports.
Starlinger was founded in Austria over 25 years ago and from the outset has been a globally orientated company. Today, plastics are recycled worldwide and many countries operate collection and re-use programmes for production and post-consumer waste.
The company’s dedicated customer orientation helps it to develop innovative, tailor-made production facilities, which are designed to meet the needs of widely varying regional requirements. These can include broad differences in the recipes of polymers, additives and production processes, as well as in throughput quantities and the many types of individual manufacturing industries.
The company’s worldwide sales and service-support network and technical consulting services help its customers to achieve optimum results throughout many different manufacturing processes. In addition, as a truly multinational company, Starlinger employs multi-lingual teams that are able to communicate directly with customers in their own language.
Innovation by design
Innovation has been at the heart of Starlinger’s culture from the outset and today, at a time when raw material prices are soaring, high quality granulate has become a significant cost-saving alternative to that of virgin plastic material. Developing solutions to meet the ongoing challenges involved in the recycling of production and postconsumer waste means that the company is constantly adapting its technologies in order to meet continuous changes in the nature of incoming materials. Starlinger must also take into account the potential uses of the final recycled product. This means not only providing solutions for the optimisation of precision engineered recycling lines, but also for the big consumer brand manufacturers that rely on Starlinger for high levels of recycled product purity and flexibility.
For example, Starlinger’s well-known RecoSTAR direct series has been specifically designed for the recycling of medium and large quantities of heavy ‘regrind’ materials such as PE, PS, PA and PC. With the Reco-Star
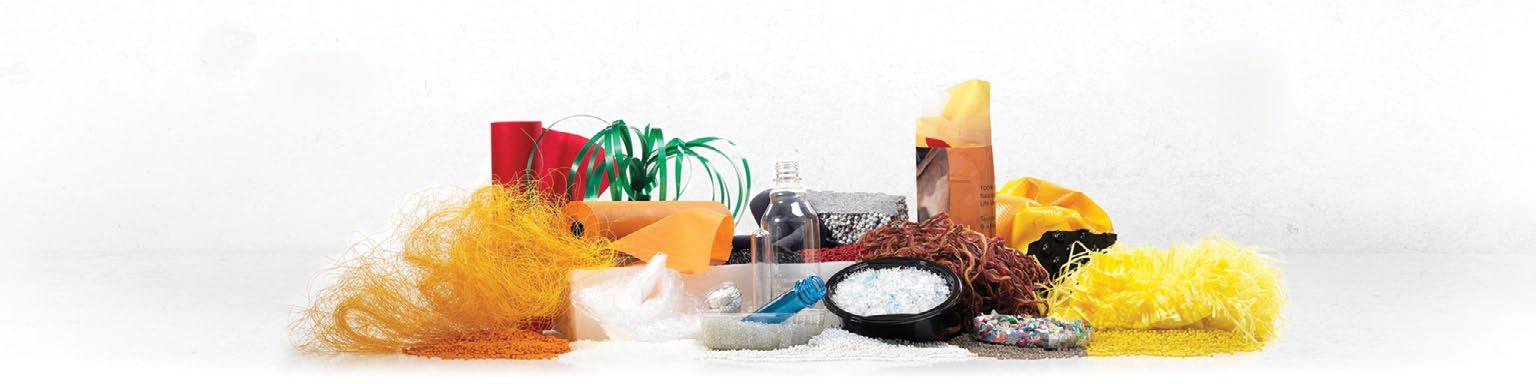
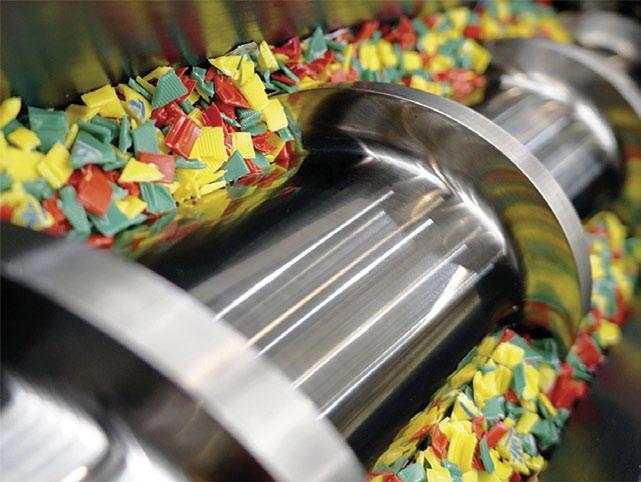

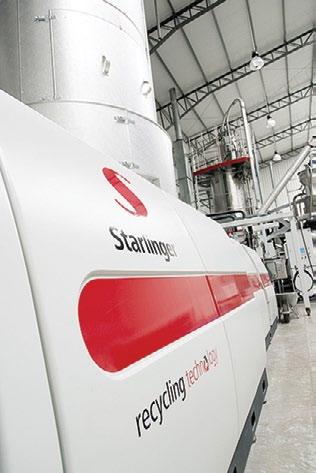
direct series, a feeding hopper delivers material directly to the extruder without the need for being pre-cut or compressed. The rate of feeding is controlled automatically and the entire innovative system is designed to ensure that any problems of over- or under-loading are eliminated.
Solid foreign substances are easily filtered with the RecoStar direct machines by a continuous melt-filter that is available with or without a back-flushing system. Another key advantage of the system is that no heating or other treatment of the material is necessary before entering the extrusion process. A clear and easy-to-use touch-screen monitor ensures a comfortable starting and stopping process throughout the continuous operation of the recycling line.
Starlinger’s RecoSTAR direct series is comprised of five machine sizes which together can cover an output range of between 130 and 1200kg/h. Each machine can also be equipped with degassing, high vacuum and a back-flushing filter as well as any one of three different pelletising systems. unrivalled service
Outstanding after sales service is an important facet of Starlinger’s success story. From the initial offer to the project planning and order handling phase, and on to the installation and commissioning of each recycling line, in addition to operator training and ‘lifetime’ after sales service, Starlinger offers these services as standard. The company also offers engineering consultancy, financing and assistance in obtaining certifications and much more.
As a supplier of high-tech industrial plants and customer-specific solutions, Starlinger recognises the value of individual customer care from the moment of first contact, until the recycling line is operational and beyond. Unrivalled after-sales service from its Customer Care Centre is an important part of Starlinger’s customer offering and a USP. This means not only a well-stocked spare parts warehouse, but above all the availability of qualified staff with in-depth and comprehensive expertise that can offer high problem-solving capabilities.

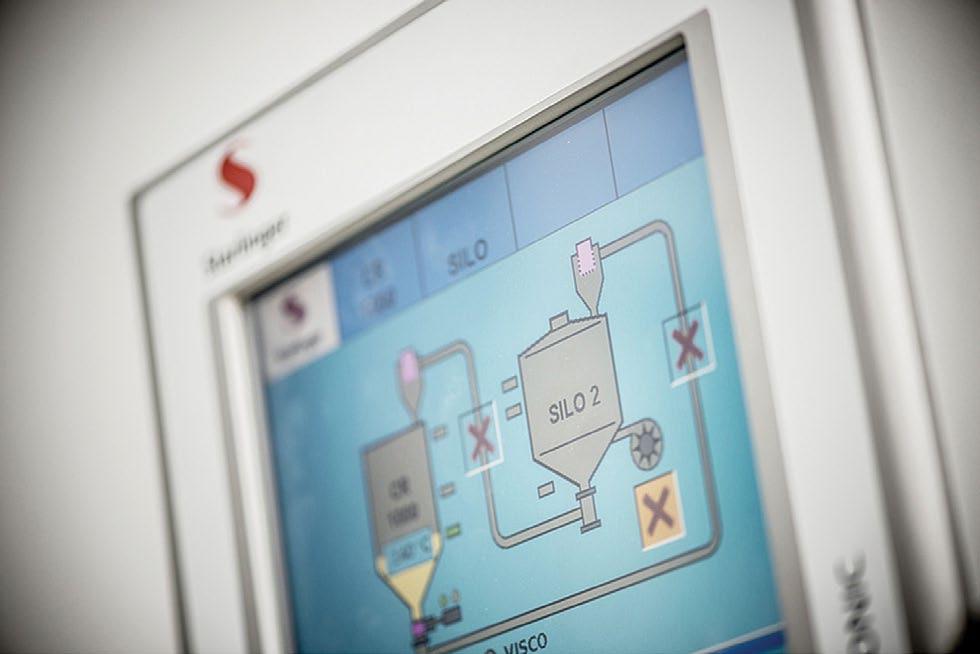
Flexible, modular design
The unique RecoStar PET, non-food recycling series offers stateof-the-art technology for the in-house recycling of PET flakes from bottles, preforms, strapping brands and sheets, as well as for the recycling of post-consumer bottle flakes after the washing process. The end product is a melt-filtrated, uniform granulate that can be used for a wide range of applications including containers, sheets, fibres and non-wovens.
Here the main product features include flexible modular design, with high levels of automation and user-friendliness, as well as direct material flow, uniform treatment of the input material, adjustable pelletising systems and increased energy efficiency. The optional inline crystallisation after underwater pelletising also ensures optimised energy efficiency and high crystallinity.
Some technical aspects of the RecoSTAR direct series include the heating of PET flakes, which are dried in a two-stage process by means of hot air and optional dry air, or under vacuum conditions. The special design of the dryer outlet results in centre-flow prevention, consistent residence time and FIFO processing. This ensures ideal preparation for the extrusion process with constantly maintained IV levels or with an IV increase level if required. Once installed, the unit can be equipped with an SSP reactor before or after extrusion in order to increase viscosity and efficiency. n
For further details of Starlinger’s innovative recycling products and services visit: www.starlinger.com
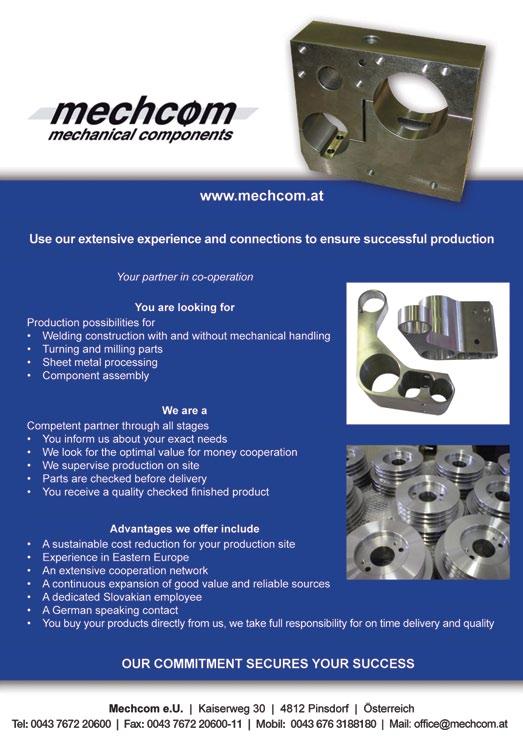
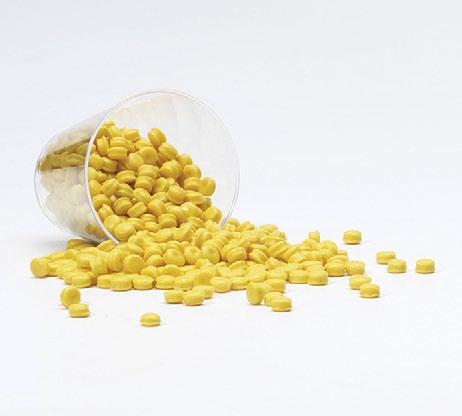
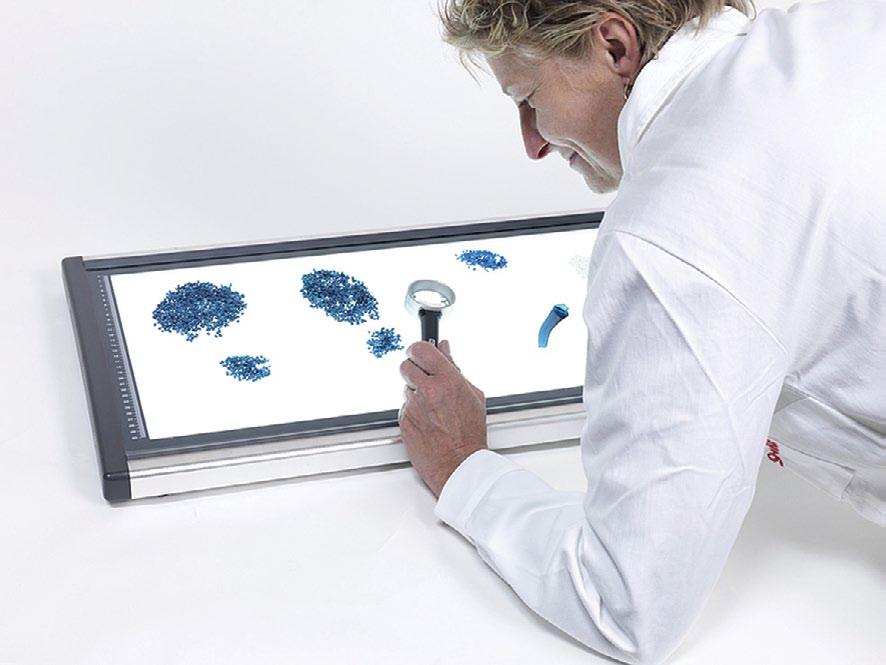
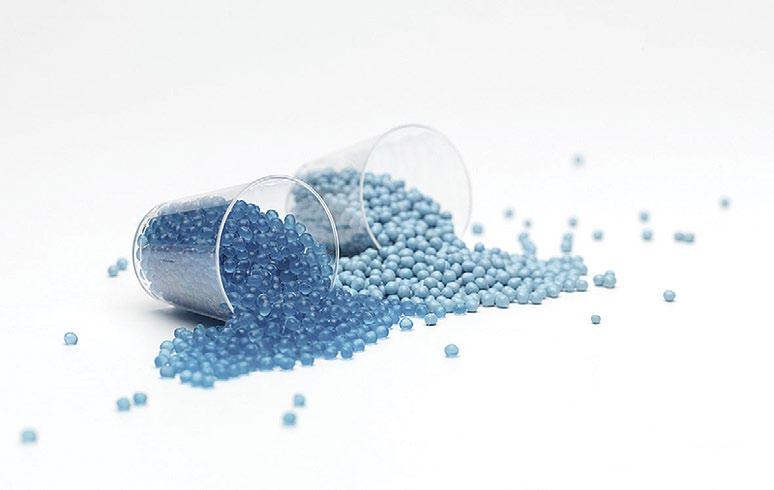