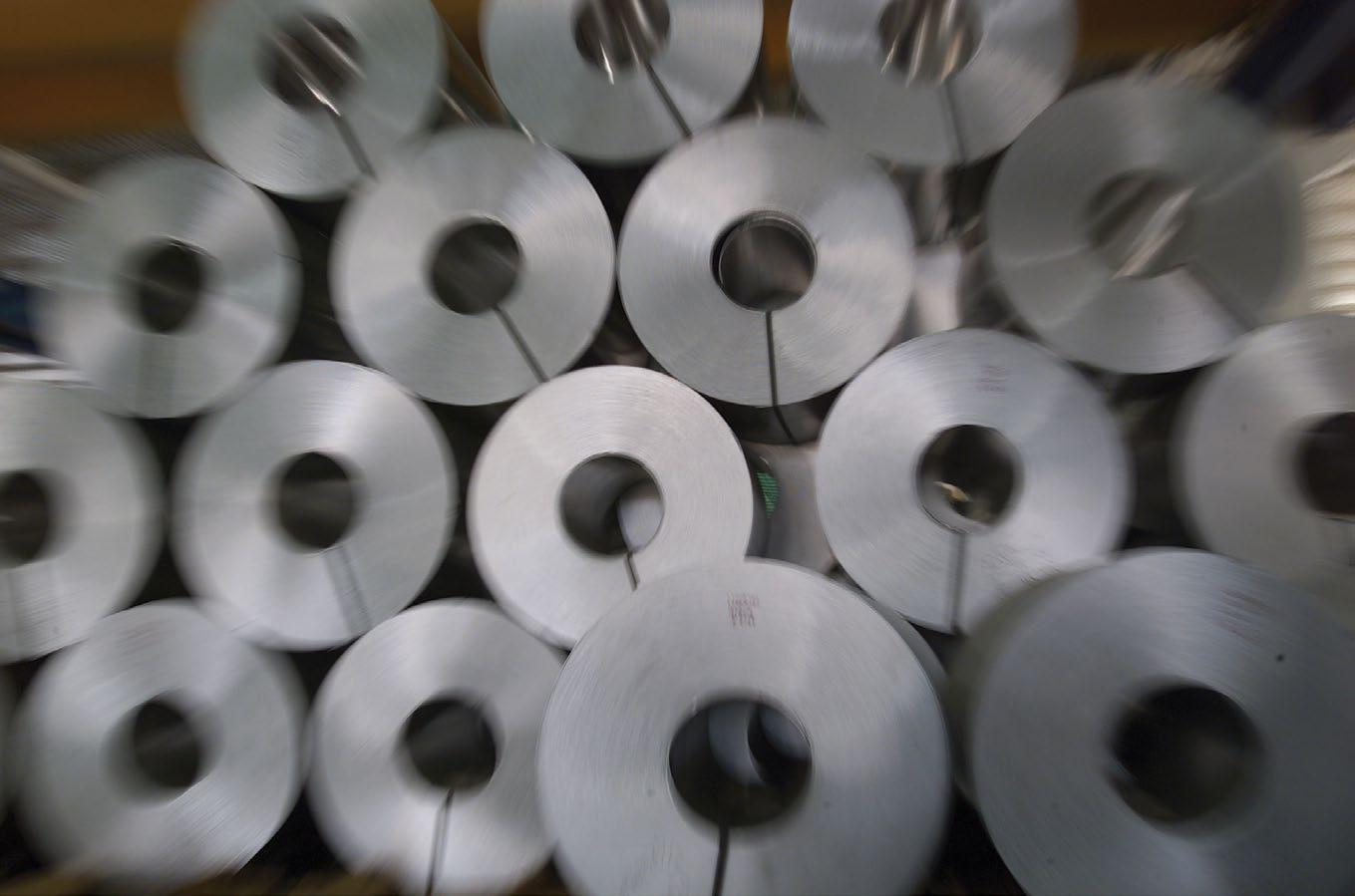
4 minute read
Profile of sustainable success Profilglass
PROFILE OF SUSTAINABLE SUCCESS
The Profilglass Group of Italy is a global leader in the manufacture of aluminium spacer and decorative bars for insulating glass (IG) units. It recently acquired Lamial, a leading Italian company in alloy laminates, offering greater synergy and expertise to Profilglass’ automotive and transport sectors, as Philip Yorke reports.

Profilglass has led the way in aluminium machining and profiles since 1982, when two brothers Giancarlo and Stephano Paci began to produce decorative profile spacers for the fast growing double glazing industry. Rapid growth over the years has resulted in a highly efficient organisation that produces more than 180,000 tons of aluminium products per year, with exports delivered to over 90 countries worldwide.
Profilglass started out as a family business and continues to be driven by the same Paci family today. The company operates from its original production site in Bellocchi di Fano, on the Adriatic coast, which now extends to over 250,000 square metres and employs around 700 people.
The state-of-the-art facility is comprised of four of the latest cold and hot rolling mills, an extensive cast-house for slabs and six continuous casting lines. In addition it operates modern machinery for the production of aluminium sheets and coils, as well as over twenty machines for the production of aluminium profiles. Profilglass also operates its own powder coating plant and plastic moulding facility. In 2017, the Profilglass Group recorded sales exceeding €500 million.
Technological advantage
Staying ahead of the competition in a crowded market place such as the double glazing industry requires major on-going investments in technology and customer services. More than 10 per cent of Profilglass’s revenues are dedicated to research and the acquisition of the latest manufacturing process technologies. Working with its long-term partners the company develops and implements cuttingedge technologies that keep it one step ahead of the competition.
Today Pofilglass is the fastest growing Italian company in the aluminium-strip production sector and much of this success can be attributed to its close working partnerships with other specialists in the industry. Companies such as Mino of Italy, with whom Profilglass has developed a close working relationship since 2001. Mino has supplied Profilglass with high-tech cold rolling mills as well as the latest hot rolling lines. Recently Profilglass also contracted Mino to supply a new Continuous Annealing & Heat Treatment line, where the floating furnace and quenching sections were supplied by Otto Junker of Germany.
In terms of its dedicated customer services, Profilglass strives to provide assistance 24/7 with optimal, just-in-time deliveries based upon a 3-4 week turnaround. This exceptionally short turnaround is only possible thanks to its high volume warehouse storage facilities. Profilglass is also proud of its unrivalled product portfolio, which ranges from 0.10mm to 8mm in thickness, and from 10mm to 1,550mm in width. Superior service comes as standard at the company and is endorsed by its vision, “You can only be successful, if you offer superior service and can fulfil the needs of your clients”.
Focus on the environment
From the outset, Profilglass has recognised the importance of sustainability and the protection of the environment. Its raw materials are 100 per cent recyclable and it has developed an increasing
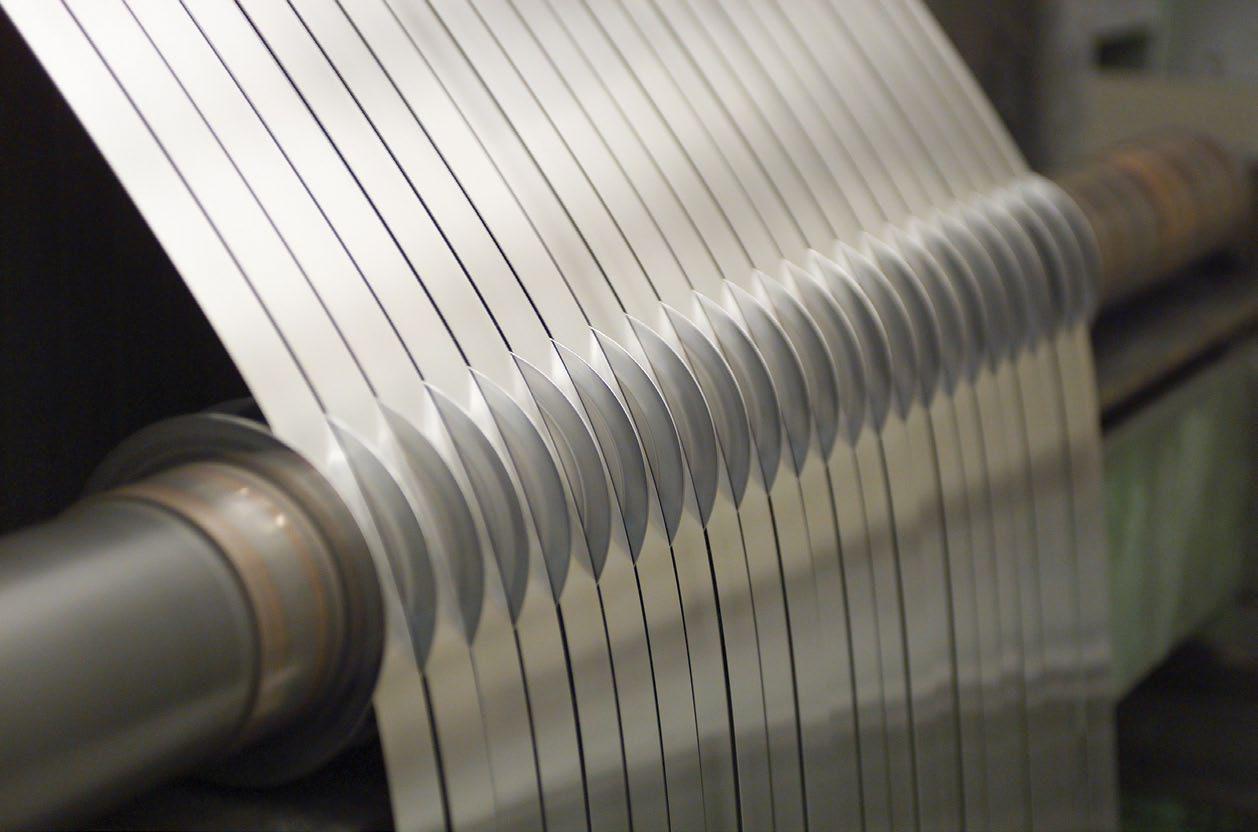
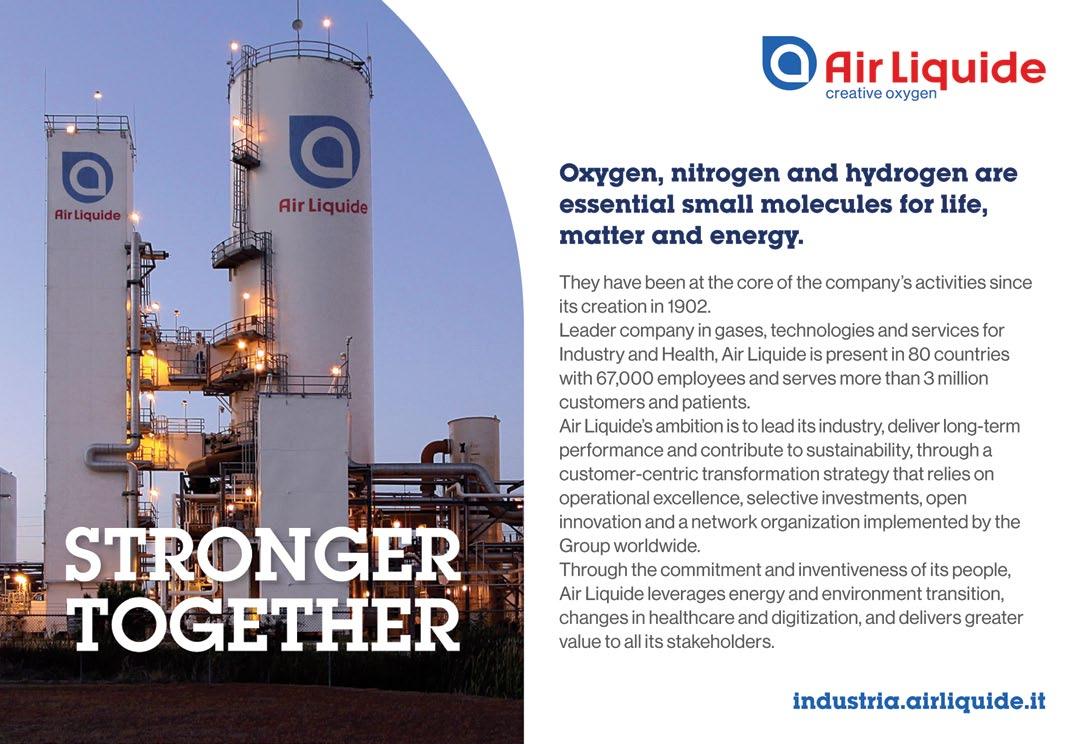
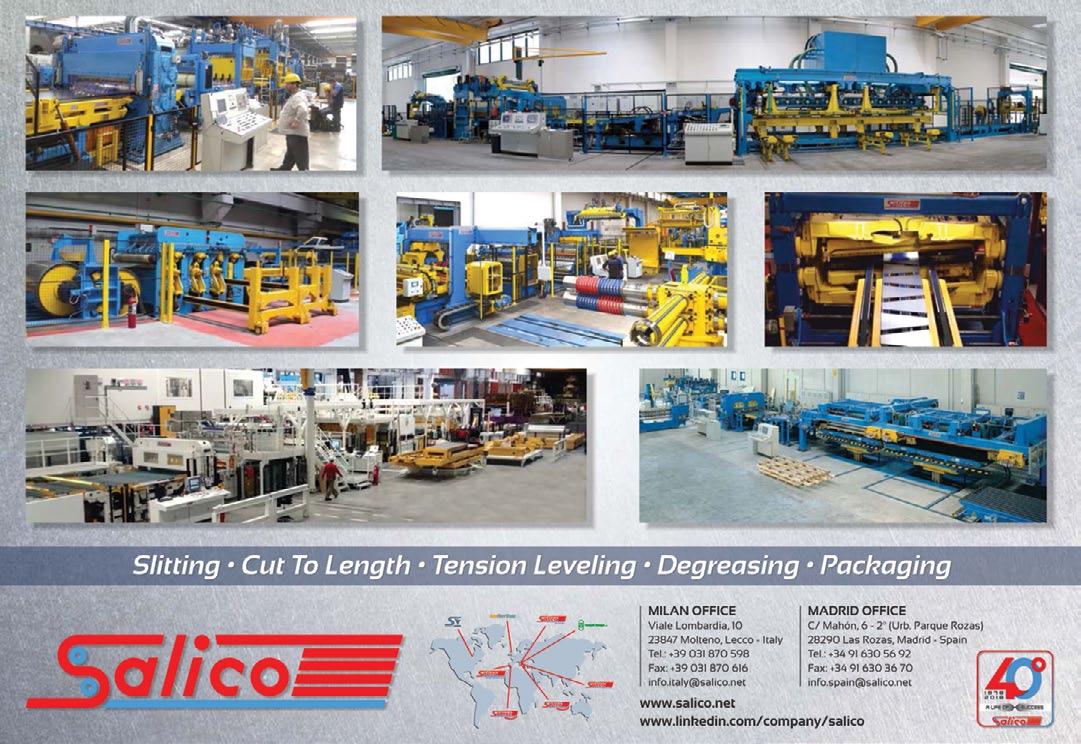
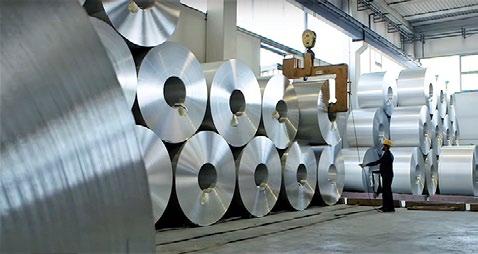
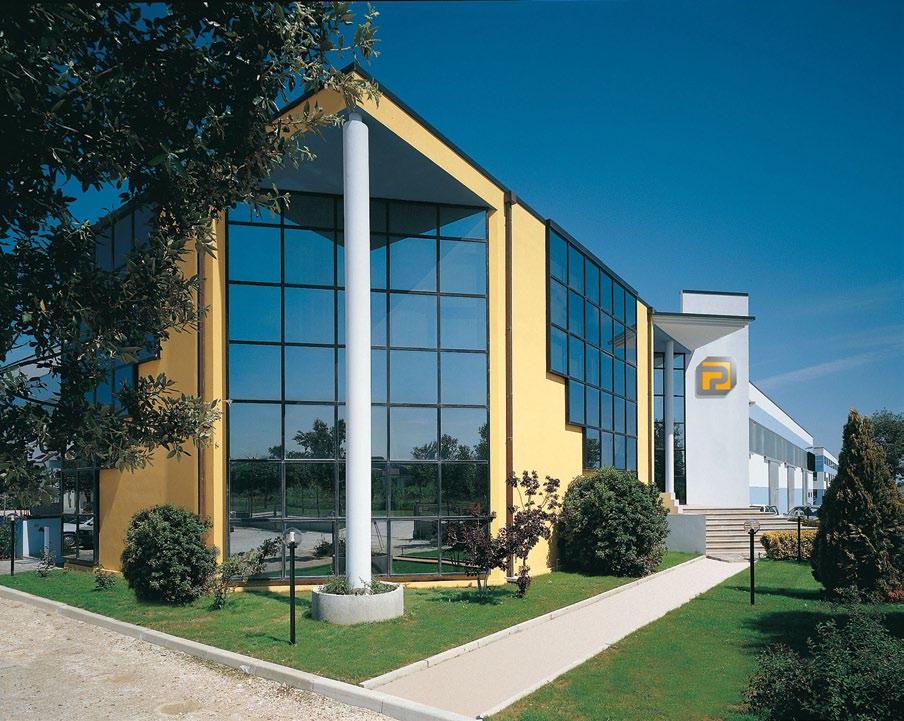
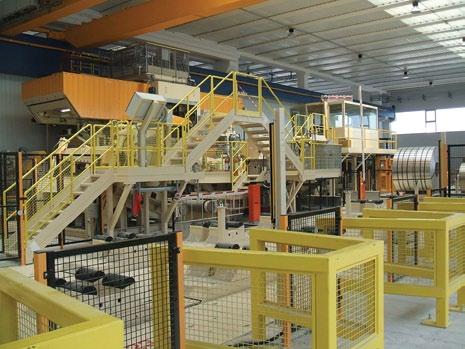
number of sustainability policies over the years, with a strong commitment to managing its resources in a responsible way.
“We are firmly convinced that development and innovation should go hand-in-hand with a deep-rooted respect for health and safety for everyone involved, as well as for the environment. This is why we take all necessary measures aimed at optimising working conditions and enhancing human resources, by investing in equipment, organisational improvements and other actions with a view to fostering a positive corporate climate that encourages growth and cooperation” Profilglass told Industry Europe.
“At the same time we have chosen to make our facilities as environmentally-friendly as possible, by installing a large-scale photovoltaic system, which is one of the biggest solar-parks in Italy, and is installed on our factory roofs. This was constructed by the Bellariva Group in collaboration with Opera Energisa and is owned by the Chinese specialist company Jiangsu Zongyi Co. Ltd,. This vast installation has a power capacity of 16.2MWp and is able to meet the energy requirements of more than 4,500 households.” World-beating efficiency
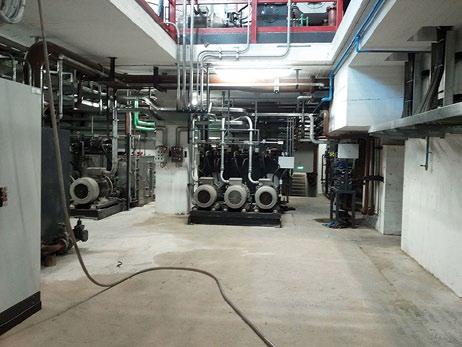
Profilglass currently has an annual production capability of more than 500 million metres of aluminium profiles, 90 per cent of which are destined for global markets. Such large-scale production is achieved with the employment of the latest, internally-built roll-forming machines that use the induction welding process. These high quality aluminium profiles are available in standard, bendable, clear anodised and painted versions.
Since its founding, Profilglass has conducted a constant policy of investment and improvement, which has culminated in the construction of four state-of-the-art continuous-casting plants and two modern rolling mills. These allow the realisation of finished products from non-processed raw material. The latest specialised plant developed in-house by Profilglass is its coil degreasing plant which eliminates completely the rolling mill lubricant remains, which is executed online during the roll-forming process. n
For further details of the Profilglass Group’s innovative products and customer services visit: www.profilglass.it
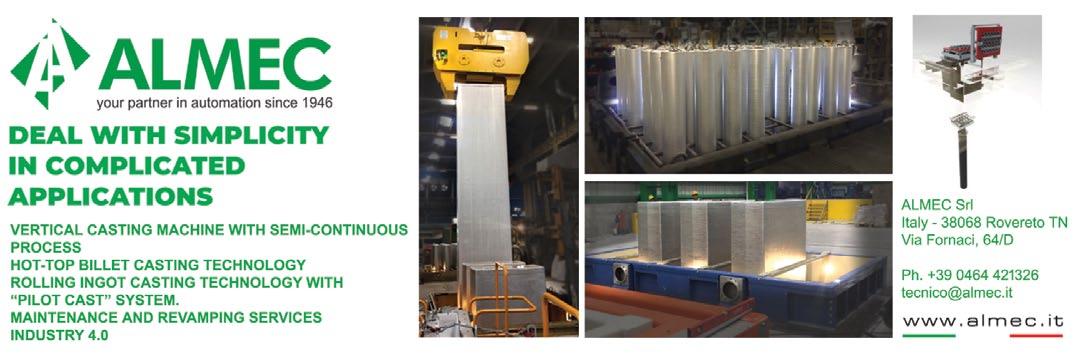