
4 minute read
Sustainability tubed Linhardt
SUSTAINABILITy TUBED
Linhardt is a global market leader in the design and manufacture of aluminium and plastic tubes for the packaging industry. Its dedication to sustainability and all that entails is well known within its business sector, as Philip Yorke reports.
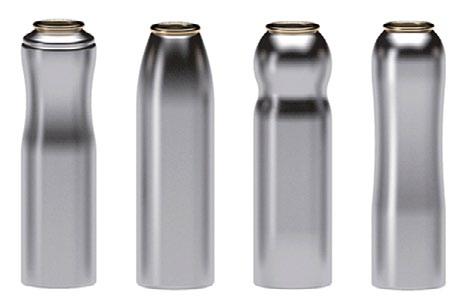
Linhardt was founded by Christian Linhardt in Viechtach, Germany, in 1943. The company’s first plant in Hambrucken began production in 1947. A second facility was opened in Viechtach in 1958. The company continued to see consistent growth and in 1992 it acquired the leading Italian tube maker, Tubettificio Tubex of Milan. The success of this strategic acquisition provided the springboard for several other key acquisitions, completed in 1997 and in 1999. Another milestone was reached in the year 2000 when it opened its first state-of-the-art ‘clean factory’ facility in Viechtach, which was dedicated to the production of specialised packaging for the pharmaceutical industry.
Today the company is a major global player serving leading multinational brands in the fields of pharmaceuticals, cosmetics, consumer goods and healthcare. Linhardt’s diverse product portfolio extends to Multi-flex tubes, aluminium cans and rigid tubes, as well as collapsible aluminium and plastic tubes and formed aluminium parts for individual packaging solutions. Currently Linhardt employs more than 1300 people and in 2017 recorded sales of over €150 million.
Antimicrobial advance
From the outset, Linhardt has demonstrated its commitment to innovative product development and sustainability, which has become the hallmark of all Linhardt packaging. This year the company unveiled another ground-breaking product which achieved the goal of extending a product’s shelf life without the need for preservatives. As a result,
Linhardt was awarded the title ‘Tube of the year 2018’ by the European Tube Manufacturers Association (ETMA) for its latest innovative packaging concept, the third such accolade this year.
Whether it is sensitive ointments for the pharmaceutical industry, high priced cosmetics or foodstuffs such as tomato paste, there are countless items in daily life that rely on the packaging expertise of Linhardt. However, it is not always enough to keep valuable fillings fresh for a sufficient length of time. Today many manufacturers rely on preservatives or complex sterilisation processes to provide longer shelf lives for their products.
The challenge was therefore to develop a film composite that offered antimicrobial properties and then process it into a tube for serial production. This became a challenge that Linhardt was determined to master, and which resulted in its unique ‘Antimicobial Tube’. The highly efficient composites involved kill resistant germs, viruses, fungi and other harmful organisms with their broadband antimicrobial effect.
The advantage of the Linhardt antimicrobial tube is obvious. It offers significantly higher shelf life for any product without the traditional need for preservatives. Furthermore, it also eliminates the need for energy-intensive processes such as radiation sterilisation.
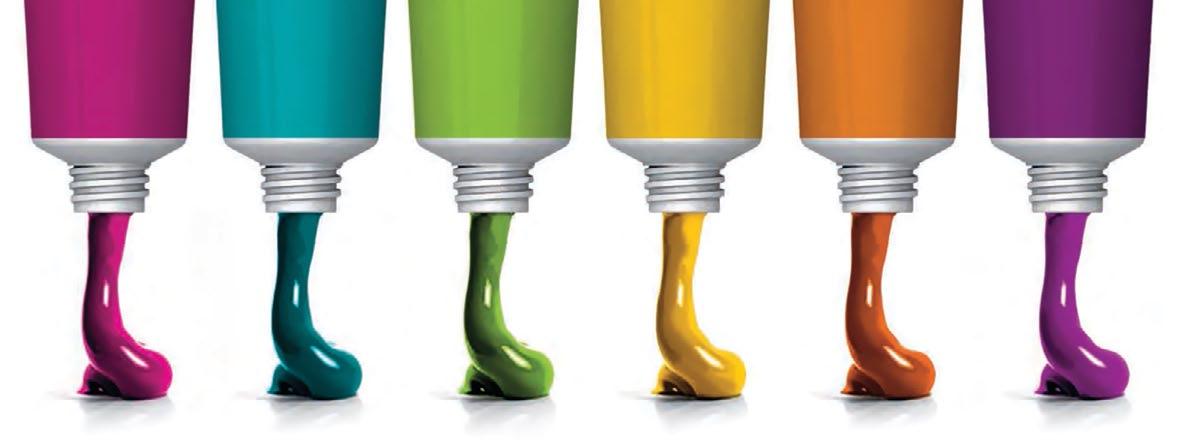
Systemic sustainability
At Linhardt, systemic energy management practices reduce consumption and pave the way for other eco-friendly processes.
Sustainability and a pioneering spirit, combined with integrity, are set in the DNA of a family business that has led the packaging field for over 75 years. This re-investment programme is not just limited to the development of new innovative packaging concepts and the equipment pool, it also includes society and the environment of the planet. “We want to do more than simply hand a healthy company on to the next generation; we want them to grow up in a world that is worth living in. This vision extends beyond tomorrow and defines the philosophy of everyone here at Linhardt.
“In the near future Linhardt’s production processes will be entirely CO2 neutral and its combined heat and power systems will continue to dramatically improve our energy efficiency. One of the biggest-scale individual measures to reduce energy consumption is the installation of energy-efficient co-generation plants at our facilities in Viechtach and Hambrucken. These plants use natural gas to produce most of the electricity that we need, whilst at the same time converting the thermal energy produced in the process to heat production facilities in winter and to cool them in the summer,” a Linhardt spokesman added.
It is impossible to imagine life without some form of packaging, which is why Linhardt feels responsible for guiding its packaging towards a more sustainable future. The company therefore adopts the widest range of approaches for the reduction of resource consumption and for the protection of the environment.
multi-flexible
Linhardt’s Multiflex tubes clearly demonstrate what the next generation of composite material packaging is able to offer. The wall of the company’s latest Multiflex tube is not overlapped and welded as in the past, but joined edge-to-edge. An extra-thin tape seals the butted joint, thus making the joint virtually invisible.
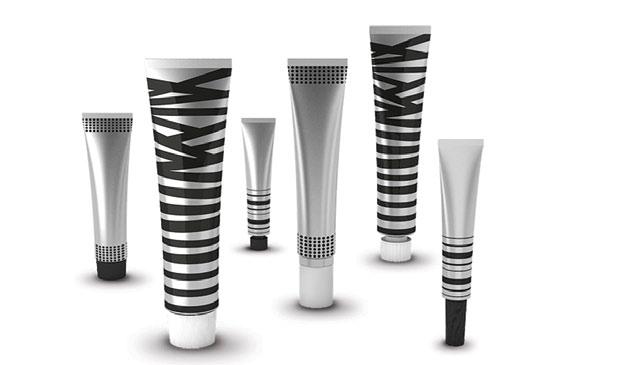

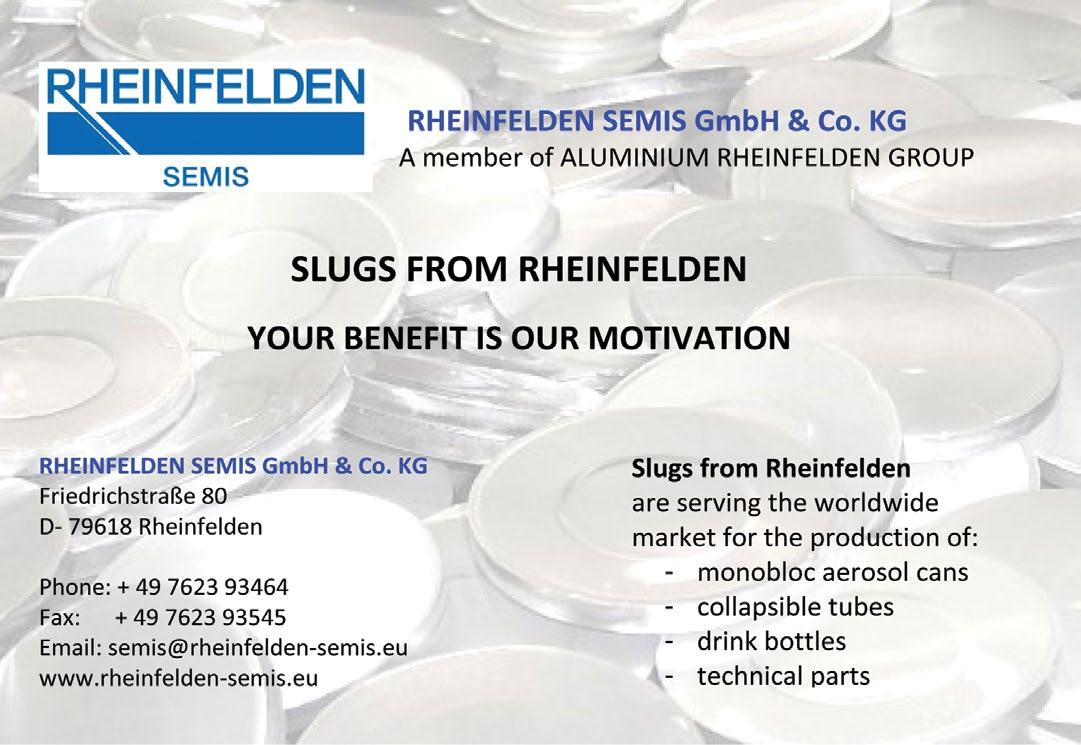
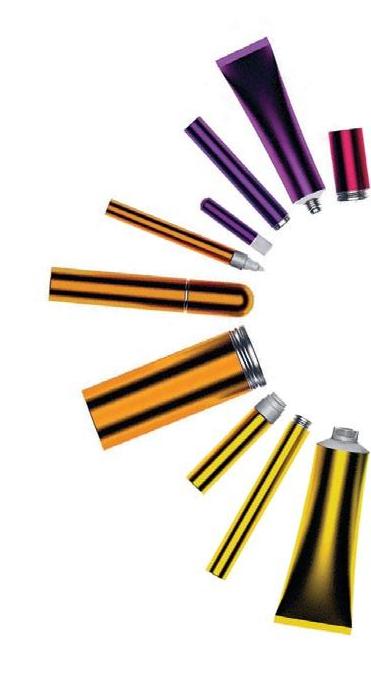

The Multiflex tube’s advantages include a 360-degree printing surface that is capable of photographic print quality, as well as offering a variable reset force and the provision of constant shape stability. In addition, it offers asymmetrical layering, particularly valuable for items requiring a combination of high-gloss decorative films with functional films inside the tube. These functional films can interact directly with the product, which also provides clearly definable barrier properties.
The company’s latest Paperflex tubes benefit from up to 50 per cent paper content and offer a very natural look. The tubes’ inner layer is food-grade compliant and its PET intermediate layer gives it a strong, pleasing and high-quality feel. n
For more details of Linhardt’s latest innovative packaging products and services visit: www.linhardt.com
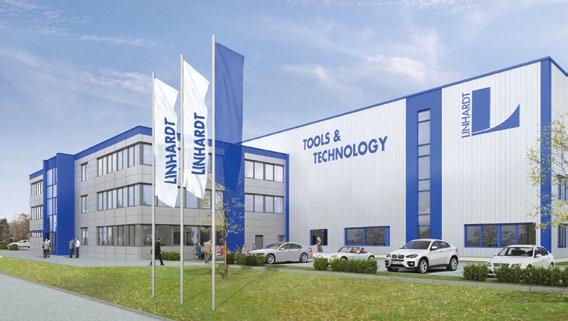