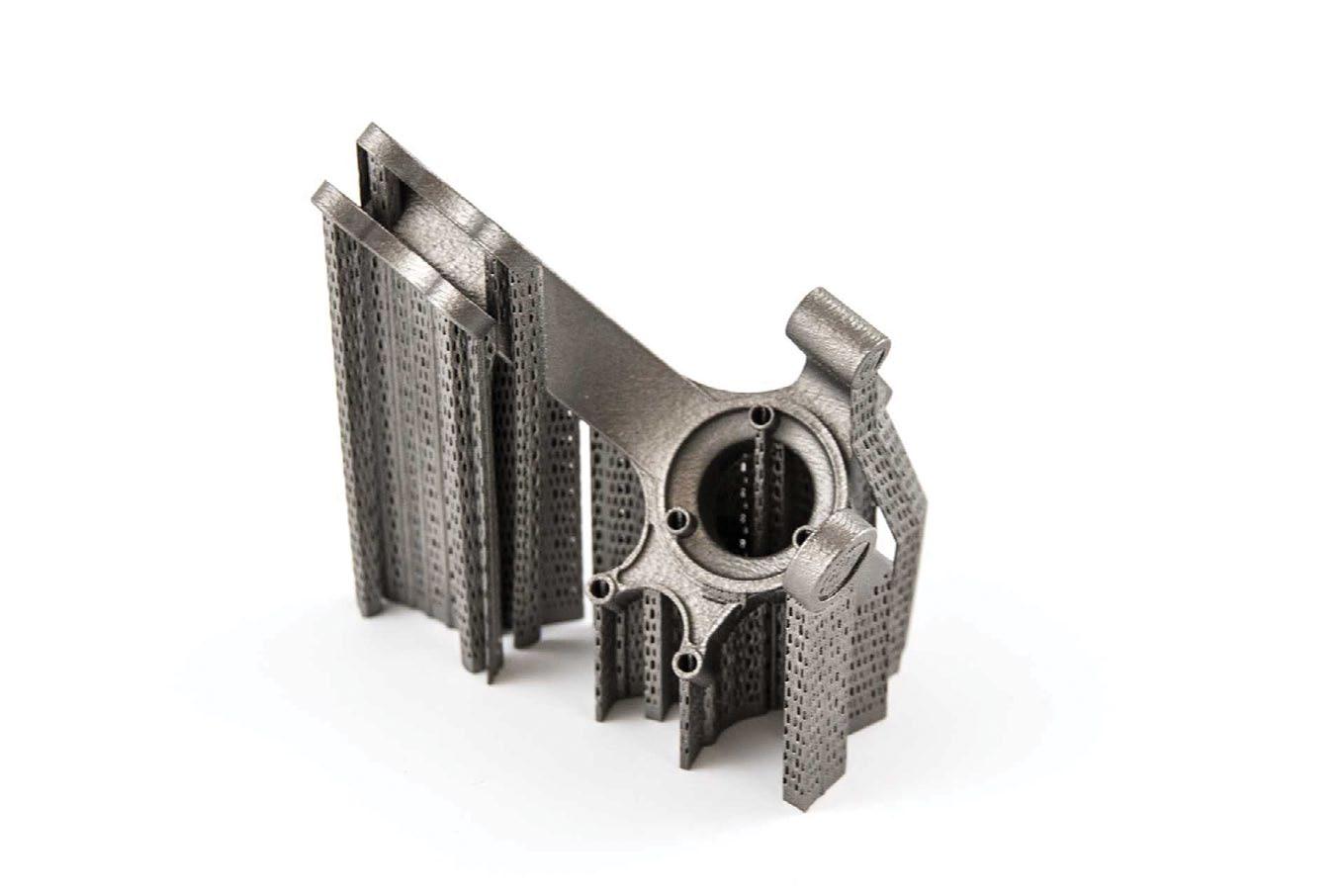
4 minute read
3D patient-specific care Materialise


3D PATIENT-SPECIFIC CARE
Materialise is a Belgian company that leads the field in the development of 3D printing software for a broad range of applications from healthcare and automotive to avionics and consumer goods. Philip Yorke reports.
Materialise incorporates almost 30 years of 3D printing expertise and software development, which today forms the backbone of the 3D printing industry. The company’s open and flexible dedicated solutions enable players in a broad variety of industries to build innovative 3D printing applications that are designed to make the world a better and healthier place.
Headquartered in Belgium, with a global network of offices, Materialise has pioneered many of the world’s leading medical, automotive and aerospace three-dimensional solutions. Fast expanding IP portfolio
Recently, Materialise strengthened its unique position in the healthcare industry with its expanding implant (IP) portfolio of personalised solutions. A new patent has been accepted for Materialise’s 3D planning technologies and 3D-printed guides that enable the desired fixing of personalised implant products.
Materialise’s latest patent enables the design of screw replacements for the fit and fixation of customised implants. With the recent expansion of its portfolio of medical patents, the company continues to strengthen its unique position in the healthcare industry. At the same time, this supports its commitment to help patients worldwide through technological innovation.
With almost 30 years of experience in medical 3D printing and planning and an impressive IP portfolio of 160 medical patents granted, Materialise is in a unique position to support surgeons with advanced planning tools and personalised medical devices for complex patient cases.

This latest patent strengthens further the company’s 3D planning technologies and 3D printed guides that allow accurate planning and design of screw placements for customised implants, ensuring the desired fixation and optimal bone preservation.
All-in-one platform
Earlier this year Materialise launched its latest personalised solution, the TRUMATCH® Personalised Shoulder system. With its expanded collaboration with DePuy Synthes, its US distributor, the new online platform and 3D printed guides for shoulder surgery was unveiled recently at the AAOS annual meeting in New Orleans.
The unique TRUMATCH® Personalised Solutions Shoulder System will help orthopaedic surgeons prepare for shoulder arthroplasty surgery, specifically addressing Reverse Shoulder Arthroplasty (RSA) and Anatomic Shoulder Arthroplasty (TSA) operations. It offers surgeons an all-in-one, web-based platform that allows them to better plan and prepare for these operations as well as to order patientspecific 3D-printed surgical guides.
RSA and TSA operations present unique challenges to surgeons with limited visibility as the result of the small incision, the Glenoid cavity being sited deep in the surgical window and the lack of reliable landmarks. However precise alignment is necessary, not just because of limited bone stock, but because of its impact on overall screw length and fixation (with RSA) and the occurrence of peg perforation (with TSA).
“3D planning is gaining popularity with orthopaedic surgeons performing shoulder operations,” said Wilfred Vancraen, founder and CEO of Materialise. “Together with our strategic partners like DePuy Synthes, we are continually working to improve surgical planning processes for a range of hospital operations.”

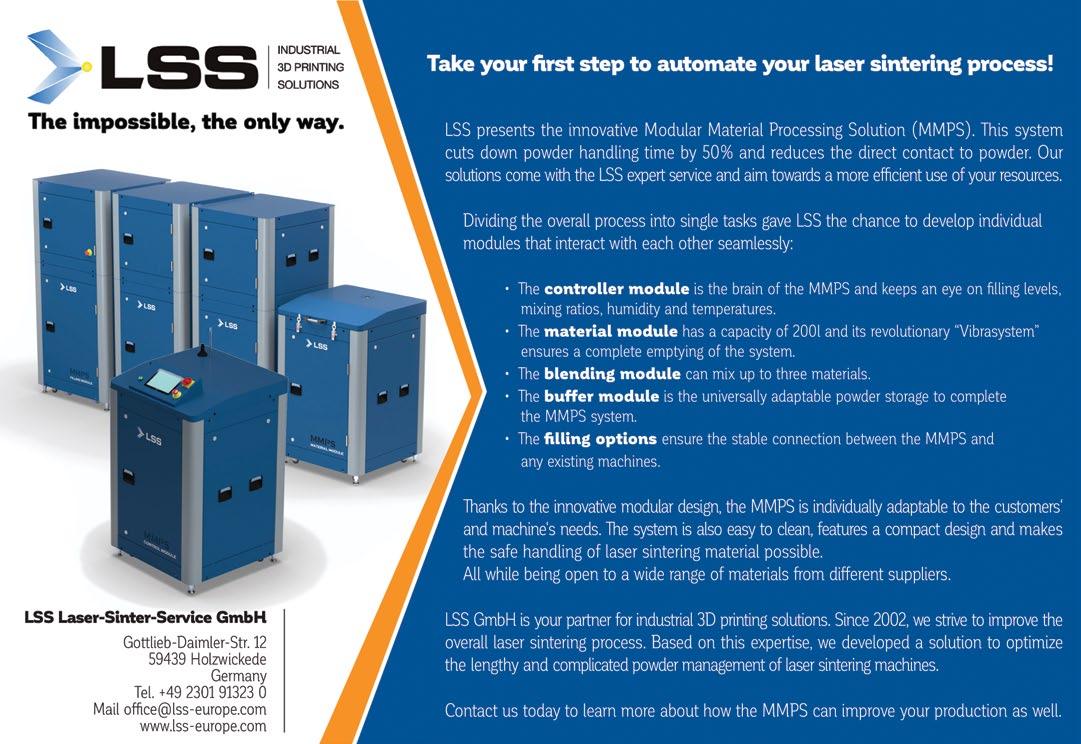
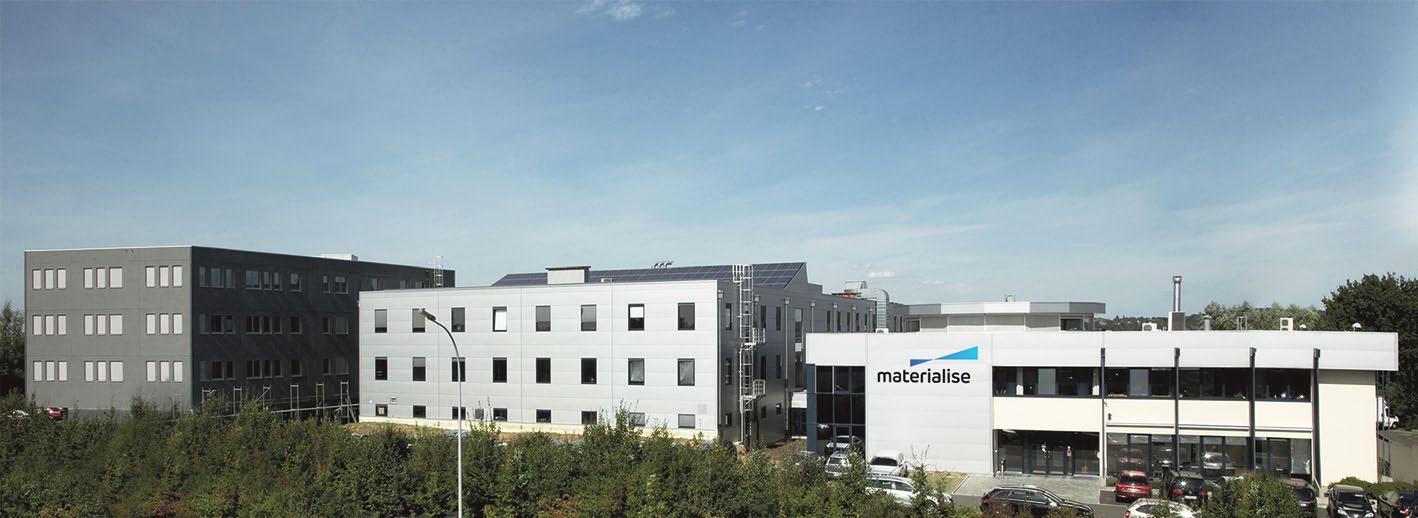
Validated software solutions
Materialise is working closely with its partners and providers to remove uncertainty and confusion for hospitals and physicians who are incorporating 3D printing into their diagnostic and surgical planning processes. In Chicago in November 2018, Materialise launched its certification programme that allows printer manufacturers that partner with the company, to have products tested and validated as being fully compatible with ‘Materialise mimics inPrint’ software.
This is the first and only software to gain clearance from the FDA to develop 3D anatomical models for diagnostic and surgical planning uses. The inPrint software is both printer and material-agnostic, thus allowing Materialise to develop partnerships and solutions to meet a wide range of hospital and clinician requirements.
Stratasys and Ultimaker are the first two 3D printing hardware partners to participate in this programme and to have their products tested by Materialise to certify compatibility. “These partnerships offer healthcare providers the benefits of our open and flexible 3D printing solutions, whilst eliminating potential compatibility challenges with third party hardware providers,” said Bryan Churchfield, VicePresident and General Manager of Materialise North America.
“Hospitals and physicians want the benefits of flexible software tools that are material and printer ‘agnostic’, but they also require the certainty that flexibility won’t create compatibility challenges at deployment or in the future. We’re ensuring they can focus on patient care and improving people’s livers by providing compatible point-of-care solutions that meet their individual needs,” Churchfield added. For further details of Materialise’s latest innovative products and services visit: www.materialise.com
