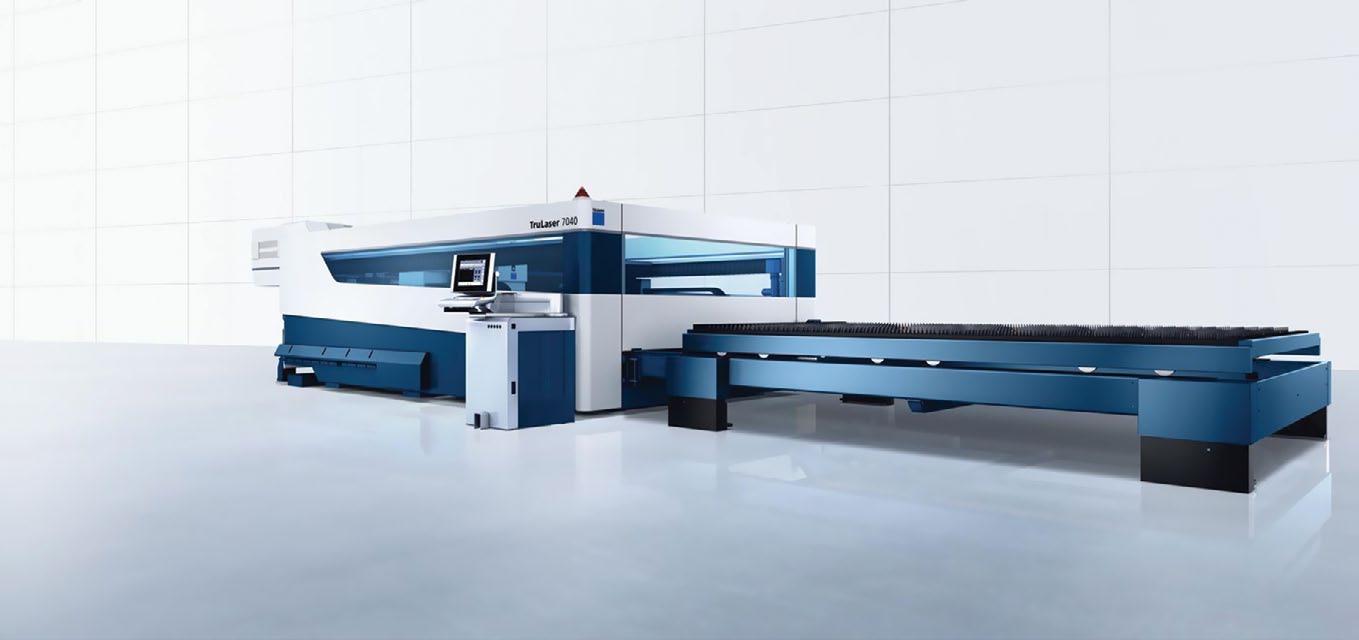
5 minute read
3D technology revolutionises denture production
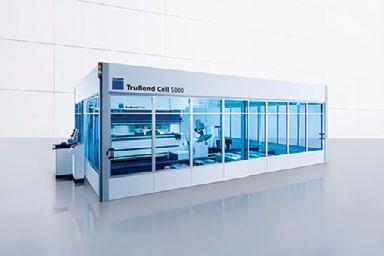
The Trumpf Group is a global leader in the design and manufacture of high-tech laser products and machine tools for industrial applications. Its diverse product portfolio ranges from 3D dental printers to e-mobility solutions, electrical storage technologies and smart software. Philip Yorke reports on one of the world’s most progressive and innovative electrical engineering companies.
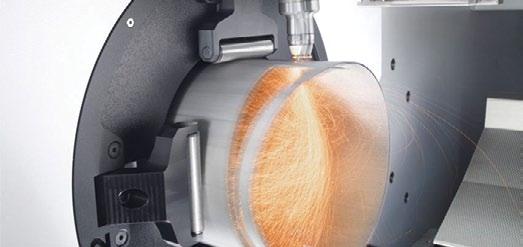
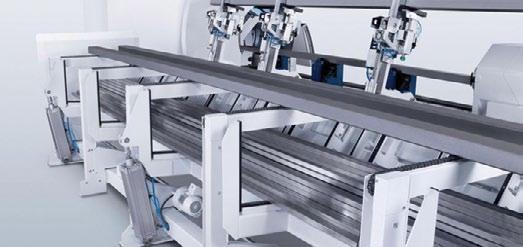
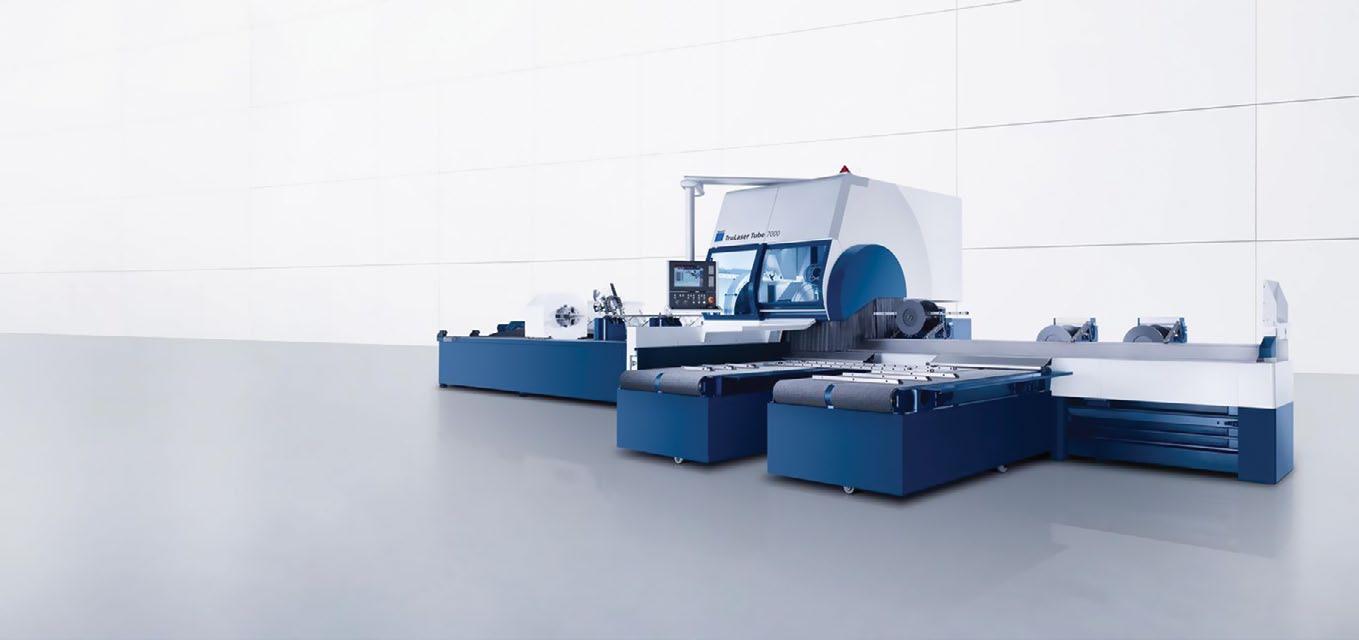
The Trumpf Group is an independent, family-owned company that was founded in Germany in 1923, at which time it operated a series of mechanical workshops. It has since evolved to become one of the world’s most successful and respected electrical engineering companies. Trumpf leads the field in its many diverse disciplines which range from machine tools, to laser technologies and advanced electronic solutions for industry.
Today the company’s innovative software solutions have paved the way for the development of a “Smart Factory”, thus enabling it to implement the most advanced technical processes in industrial electronics. With a highly skilled workforce numbering around 13,500 people, last year the Trumpf Group generated revenues of more than €3.6 billion.
Pioneering 3D laser technology
The Trumpf Group is present in almost every sector of the manufacturing industry and its diverse portfolio of products and services is unparalleled. As a leading pioneer of industrial laser technology it came as no surprise to the market that in February this year Trumpf announced it had developed the world’s fastest dental 3D printer. Trumpf’s ‘TruPrint 1000’ utilises multiple lasers to make dental prostheses ten times faster than by conventional methods.
In addition, wireless digital connectivity links the Trumpf system to machines, which in turn opens the door to the manufacture of entirely new dental products. This latest ground-breaking technology from Trumpf was unveiled recently at IDS, the world’s leading international dental technology trade show. This is where the company showcased its revolutionary TruPrint 1000. This is the world’s only small-format system that works with multiple lasers. This format enables it to manufacture dental products ten times faster than existing dental milling machines.
This latest small format 3D printer from Trumpf boasts another innovative feature: connectivity. With its direct wireless link to milling machines, the TruPrint 1000 is able to print teeth that are designed to be mounted on implants. This implant-supported denture not only replaces the original tooth, but also the root to anchor it. This latest revolutionary product is helping to industrialise dental 3D printing. With the new TruPrint 1000, it takes just three minutes to print a tooth.
Reinhard Stroka, head of the Dental Products Division at the Trumpf Group said, “More and more dentures are being mass-produced, particularly in Asia, which is why it is crucial to support the digital workflow. The ability to connect to the milling machine is a key milestone step towards fully automated mass production”.
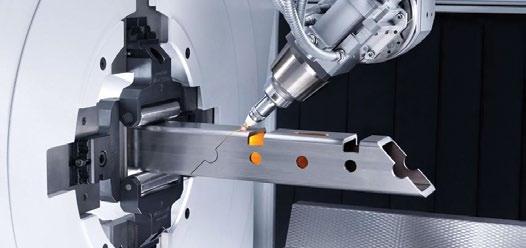
Futuristic e-mobility solutions
The Trumpf Group is already benefiting from the automotive industries’ shift towards e-mobility with its advanced battery storage solutions and laser welding technologies. These ground-breaking products were unveiled recently at the International Automotive Photonics Technology Conference, held in Ditzingen, Germany. Here auto-industry innovators presented their very latest e-mobility technologies and manufacturing processes.
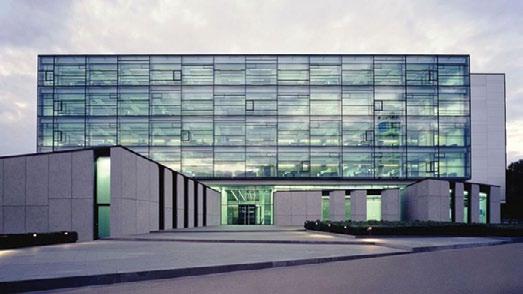
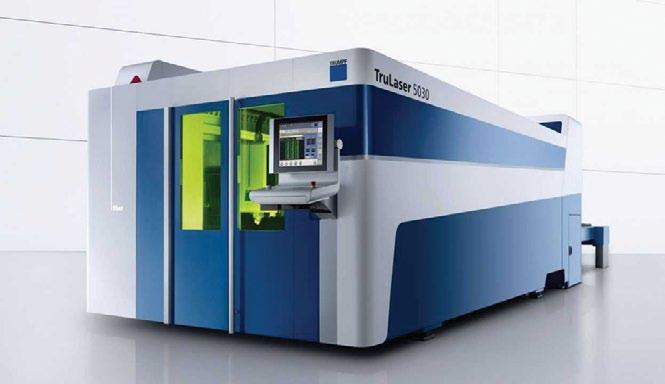
One of the Trumpf Group’s key contributions is a new laser that is specially designed for welding copper. This is acknowledged as being superior to any other laser welding product on the market and represents a major breakthrough in efficiency and precision. It is a significant development created by Trumpf’s laser specialists as part of its e-mobility growth strategy. Considered as the most important material for conducting electricity, copper plays an essential role in the e-mobility manufacturing sector. The new tailor-made laser offers a faster and more efficient means of welding copper for applications such as those found in high-power electronic systems used in today’s electric cars.
“The transition towards e-mobility offers some major opportunities for German industry” said Christian Schmitz, head of the Laser Technology Division at Trumpf. “The important thing now is to rapidly address the new areas of opportunity for business and technology that are emerging from this global structural transformation”.
The Trumpf Group expects further growth as a direct result of the fundamental changes in the automotive industry. The company’s sales of products and solutions which are channelled straight into the e-mobility sector have doubled compared to the sales figures for the previous year. “Twenty per cent of our order intake from the auto industry is now coming from e-mobility, which is twice as much as last year” Schmitz commented.
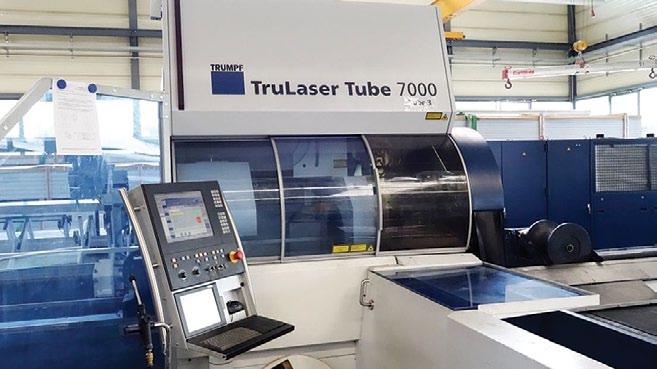
Boosting productivity
A new machine drive concept that significantly boosts productivity and makes tool changes up to 70 per cent faster has just been launched by the Trumpf Group. This new ‘TruBend Centre 7030 concept, not only offers high-speed panel-bending, but it is also able to load and unload the machine automatically. The latest TruBend Centre 7030 is particularly adept when it comes to fabricating complex parts with various radius bends, short side lengths and narrow profiles.
This alternative bending technology is much faster than any of those relying on existing die-bending machines. The Trumpf engineers have also added a feature that allows it to change multiple small tools at the same time. The new TruBend Centre 7030 also features an offline TecZone fold-programming solution that enables operators to programme many parts with just a few clicks of the mouse.
The Trumpf Group has focussed on making its new TruBend Centre 7030 faster than ever before and its engineers have achieved this by splitting the machine’s drive unit into two parts. As a result, instead of equipping the machine with just one central hydraulic cylinder, the new design features one on the left and another on the right. This configuration increases its axis velocity and significantly boosts the machine’s productivity. The new on-demand servo drive also saves energy by running the motor only when the machine actually needs it.
For further details of the Trump Group’s latest innovative products and services visit: www.trumpf.com
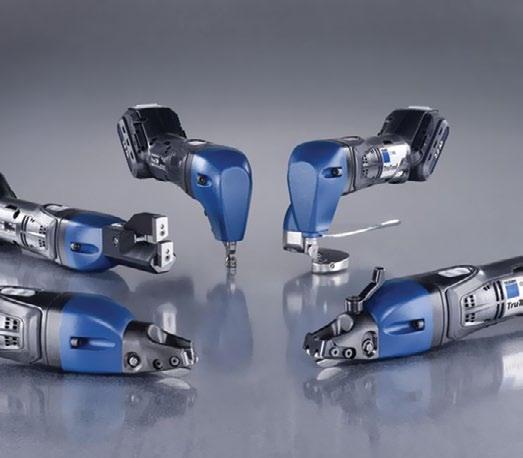
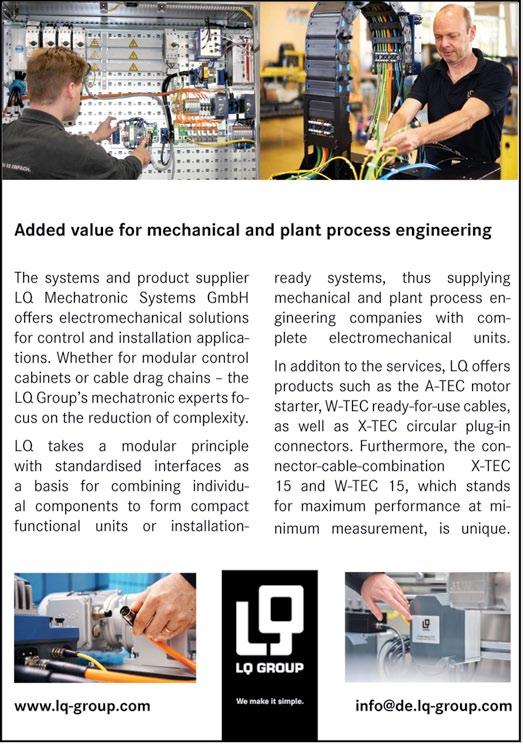