
4 minute read
Bespoke cabin design Agrikon Kam
BESPokE CABiN dESiGN
The Hungarian company Agrikon Kam has over 40 year’s experience in driver’s cab production. Its ability to manufacture bespoke cabins that are produced by the most advanced production systems has attracted the largest European machine manufacturers in many industries and resulted in continued growth. Edina Beale reports.
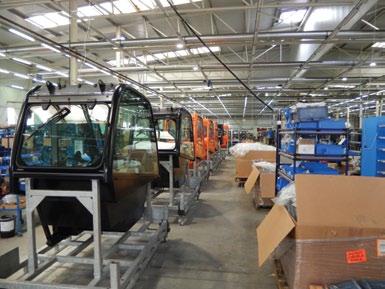
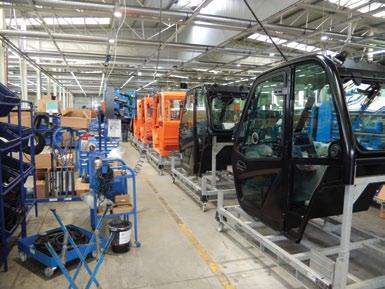
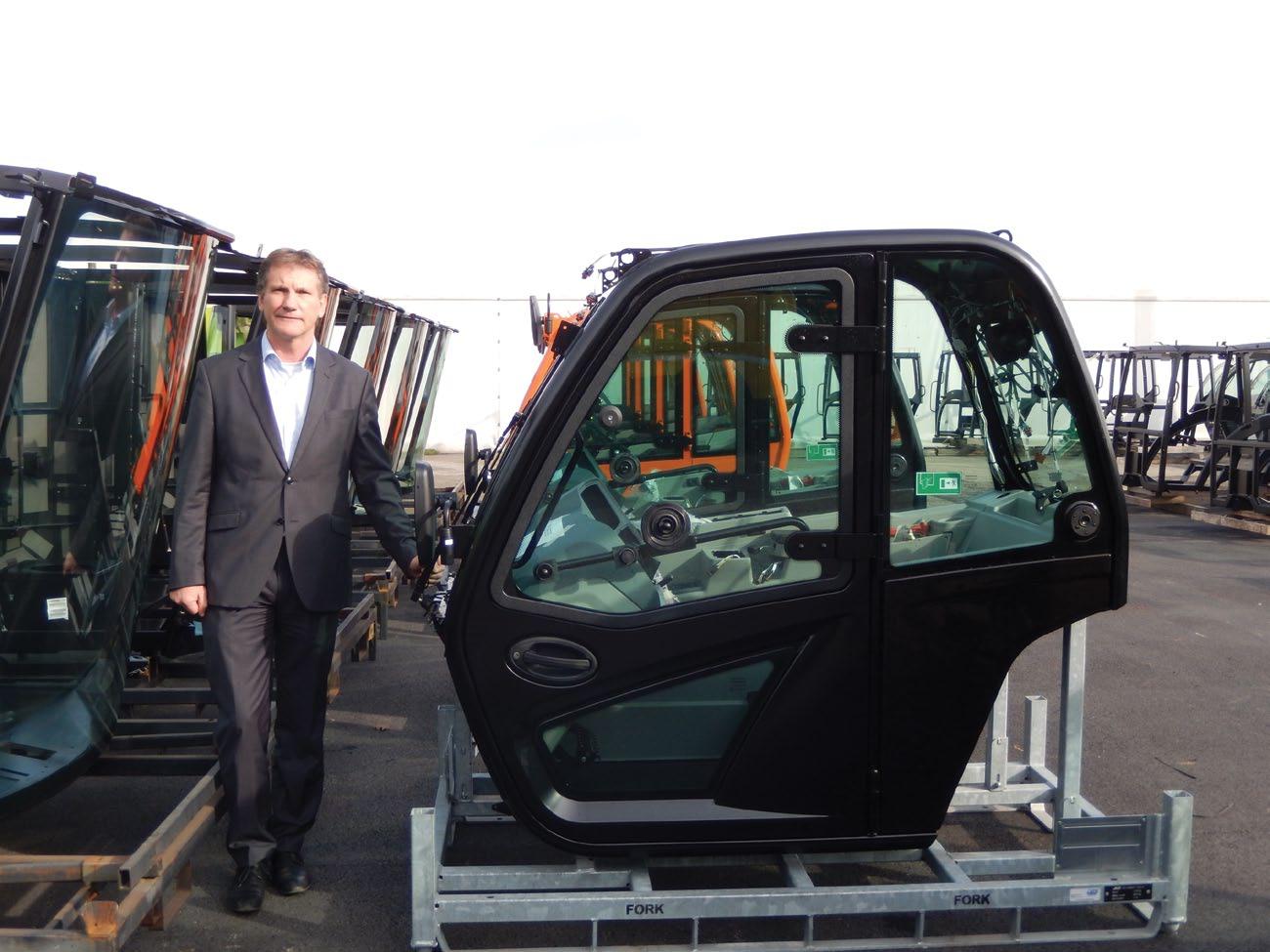
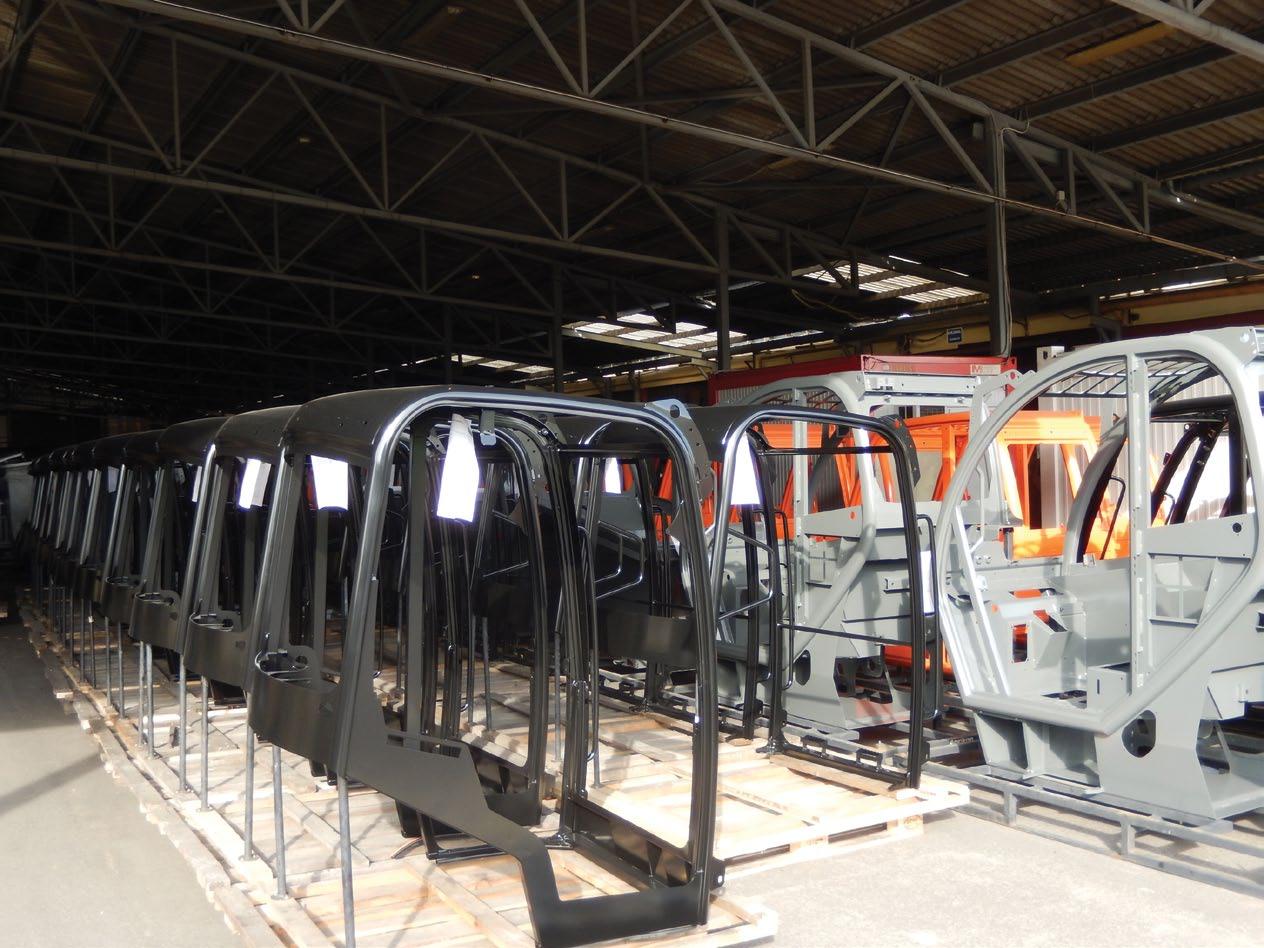
Following the Second World War the need for new agricultural machinery led, in 1946, to the Hungarian state establishing a new factory in Kiskunmajsa. As a state-owned industry, the factory continued to produce agricultural machinery as required. In 1968, the company diversified and began to produce driver’s cabs for lorries. This development led to the first contract with the factory’s current major partner, Claas, as the new order required the factory to produce driver’s cabs for combine harvesters.
The name Agrikon Kam was first used in 1987 and in 1993 Agrikon Kam was privatised, with two thirds of the company being bought by managers and staff, whilst the remaining third was bought by a foreign investment company. The antecedents of the management team have ensured that no dramatic changes were required to ensure the smooth transition to a privately owned company.
extensive Portfolio Prominent partners
Today Agrikon Kam is the leading manufacturer of driver’s cabs in Hungary. The enterprise currently employs over 500 people and last year turnover reached €34 million.
Agrikon has been supplying the leading combine harvester manufacturer, Claas since 1975. This relationship was strengthened in 2015 when Agrikon began to deliver products to the group’s French operations as well as to the Hungarian and German Claas manufacturing units. Whilst successfully maintaining long term partnerships, Agrikon has also acquired many new partners in this segment and found opportunities in new markets. The company now supplies driver’s cabs for WackerNeuson and it has been regularly manufacturing Kramer, Hako and Terex driver’s cabs as well as receiving orders from the American/Belgian JLG. After exporting welded components to Liebherr for many years, Agrikon had also been selected to manufacture driver’s cabs for them.
Whilst first focusing mainly on requirements in the agricultural sector, as part of their strategic direction the factory successfully diversified its product range in 2011 and began to target the construction industry. Today the range of cabs is extensive with units developed for tractors, combine harvesters and construction machines. Agrikon is able to provide a full cab, which includes the roof, window screens and windows, lighting, climate control, seat and electronics. Alternatively, there is the ability to meet bespoke orders where one or more of the standard elements are not required. Due to its extensive industry experience and expert knowledge Agrikon is able to take part in the design and development process and work together with its large European manufacturing clients to meet their specific needs. Diverse technologies
To meet the highest European standards, in recent years Agrikon has invested nearly €10 million to replace outdated technology with the latest available. Cabins are manufactured from steel sheets and other steel base materials and the factory uses a diverse cutting edge technology throughout the production process. For component production five modern laser cutting facilities are implemented to cut the steel sheets in 2D and 3D to the required size. These laser cutting technologies are now also used to cut all other steel base materials which enable the firm to improve on quality and efficiency. Their state-of-the-art bending machines are equipped with an
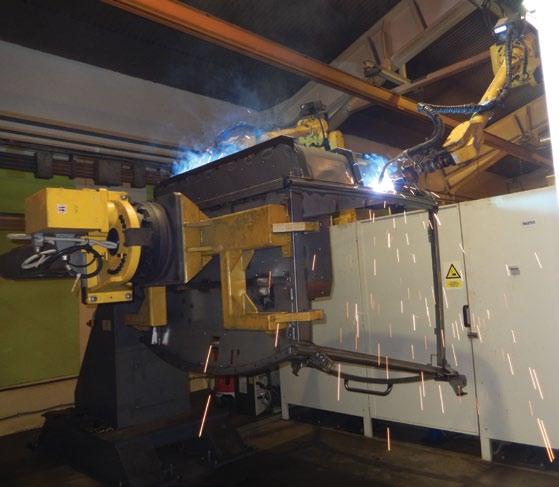
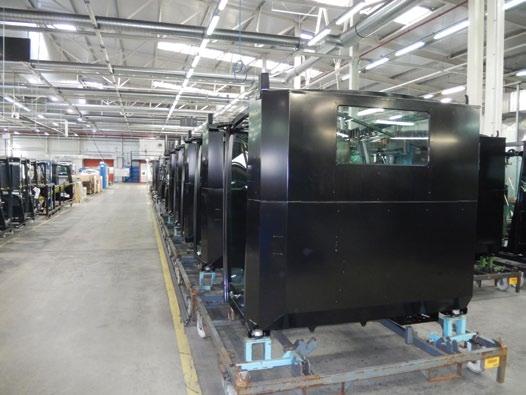
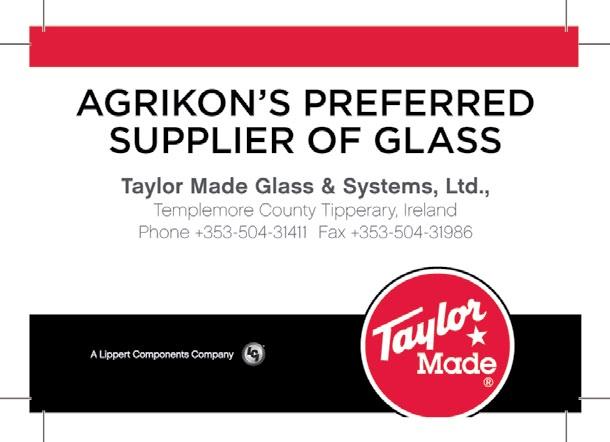
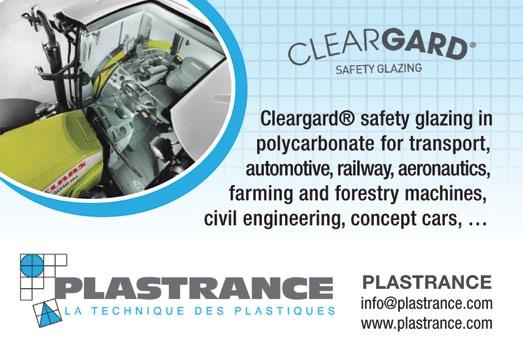
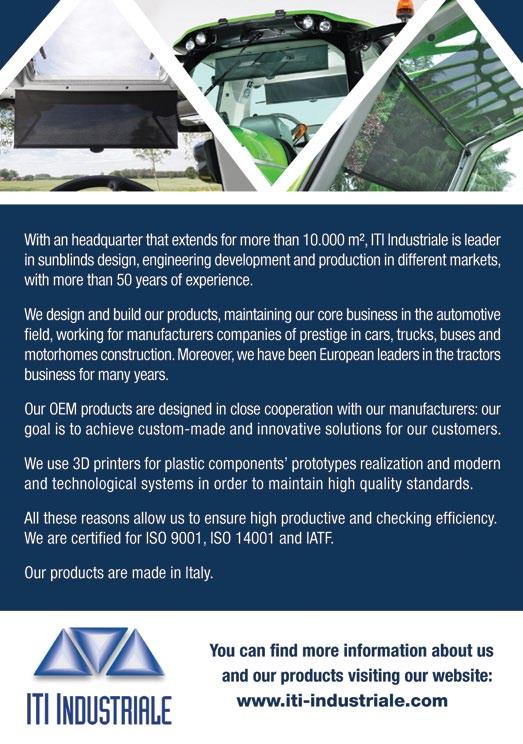
active angle control which helps to identify and correct the different mechanical attributes of the sheets during the bending process.
The company’s welding machines are regularly replaced and upgraded to the latest technological solutions. Smoke ventilation is available in all areas of welding now. The separate welding hall is equipped with 14 welding robots and is complemented by another production hall where 70-80 manual welding machines are used.
The KTL facility had a full reconstruction in recent times and now meets the highest customer demands. From surface coating to powder coating Agrikon is able to meet all specific requirements. In order to increase energy efficiency the company has made major investments to reconstruct their existing buildings and implement new lighting technologies.
As in the car manufacturing business, quality expectations in measurement accuracy in this segment are continuously increasing. At the Agrikon site staff have to move 2-3 metre long work pieces and prompt measurements are vital to fit them into welding machines and then for assembly. In order to increase measurement accuracy and speed, Agrikon has invested in the two most modern measuring systems; HandyPROBE and HandySCAN systems have increased the efficiency of measuring processes by 30 per cent.
In the past decade Agrikon has become one of the most significant driver’s cabin manufacturers in Europe. The firm is in a fortunate position as there are no rivals in the cab manufacturing sector in Hungary; the company has the largest production capacities and is the most experienced operator in its field in the whole of eastern and central Europe. The management believes that its 40 year industry experience and expert teams will enable Agrikon to reach even greater levels of success. n