
4 minute read
optimised precision-casting DGS Druckguss
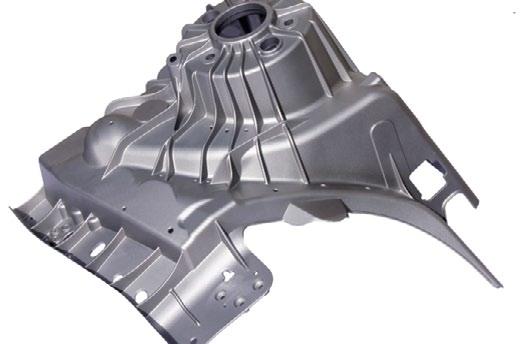
oPTimiSEd PRECiSioN-CASTiNG
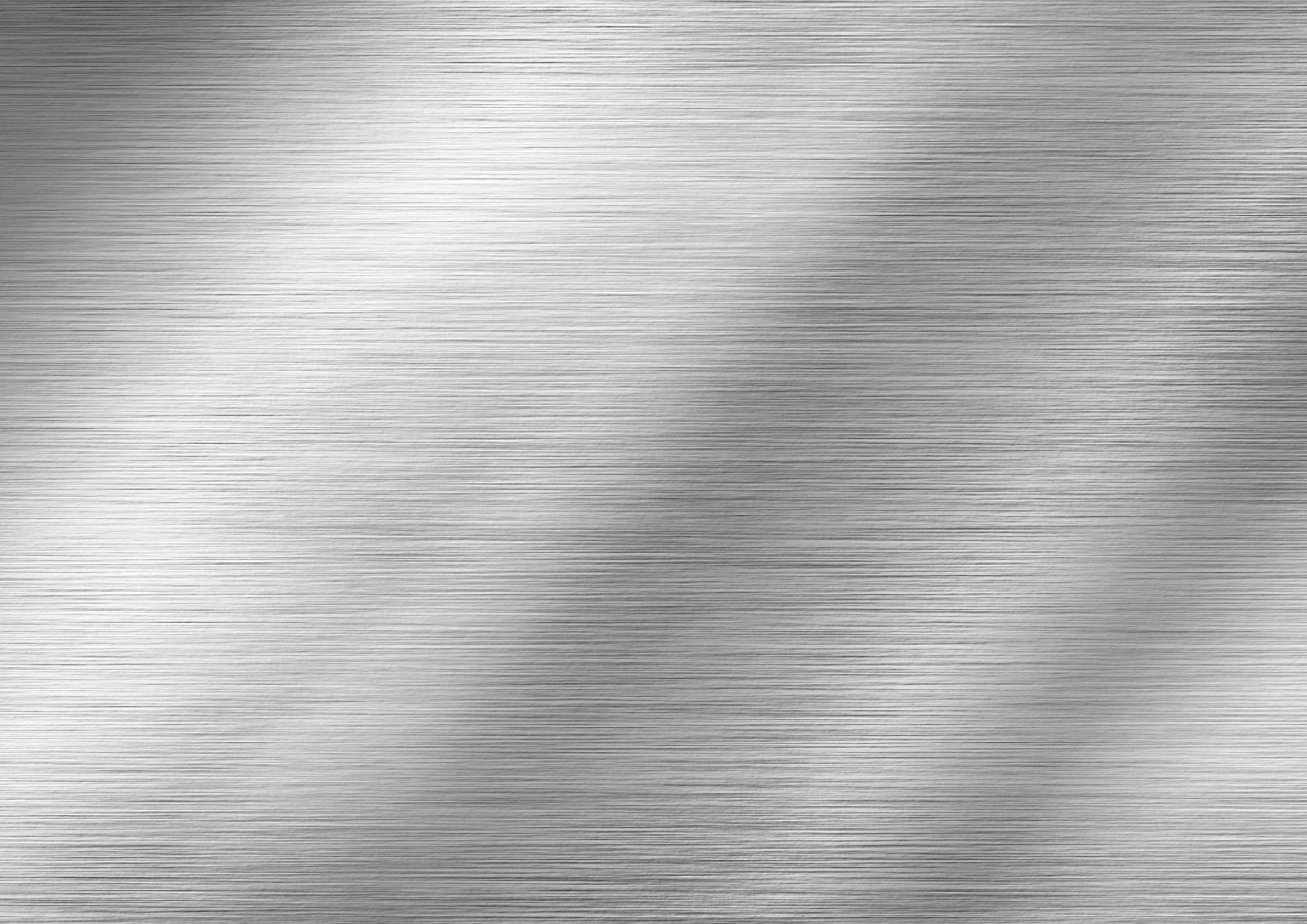
Precision components made in light metal alloys play an increasingly important role in the world’s high tech industries. DGS Druckguss leads the field in the structural casting of aluminium and magnesium for automotive and apparatus engineering applications. Philip Yorke reports
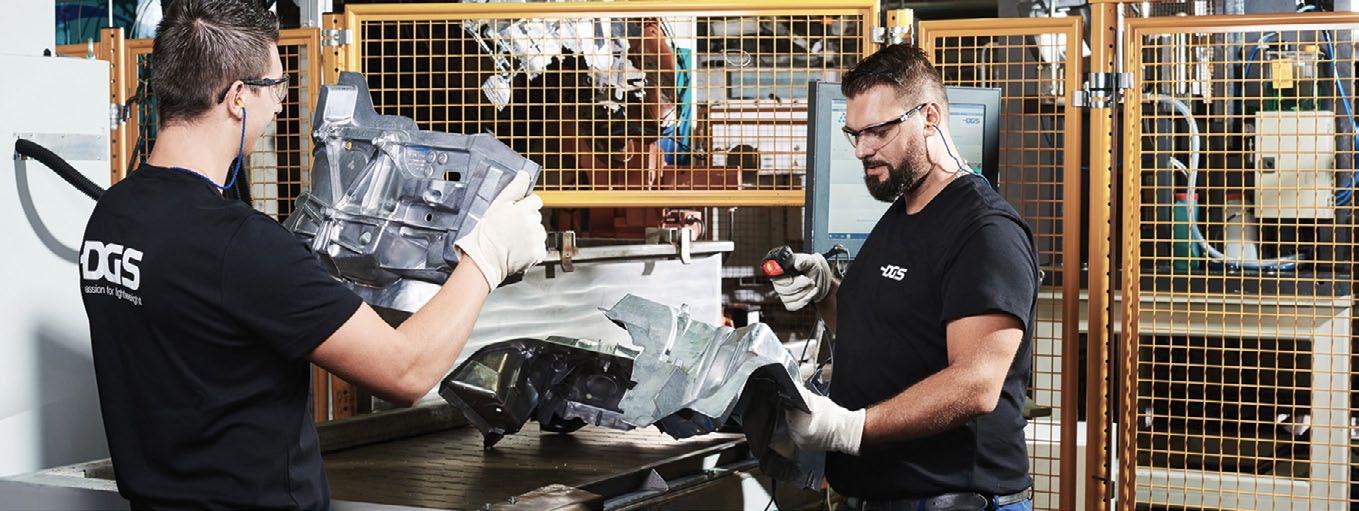
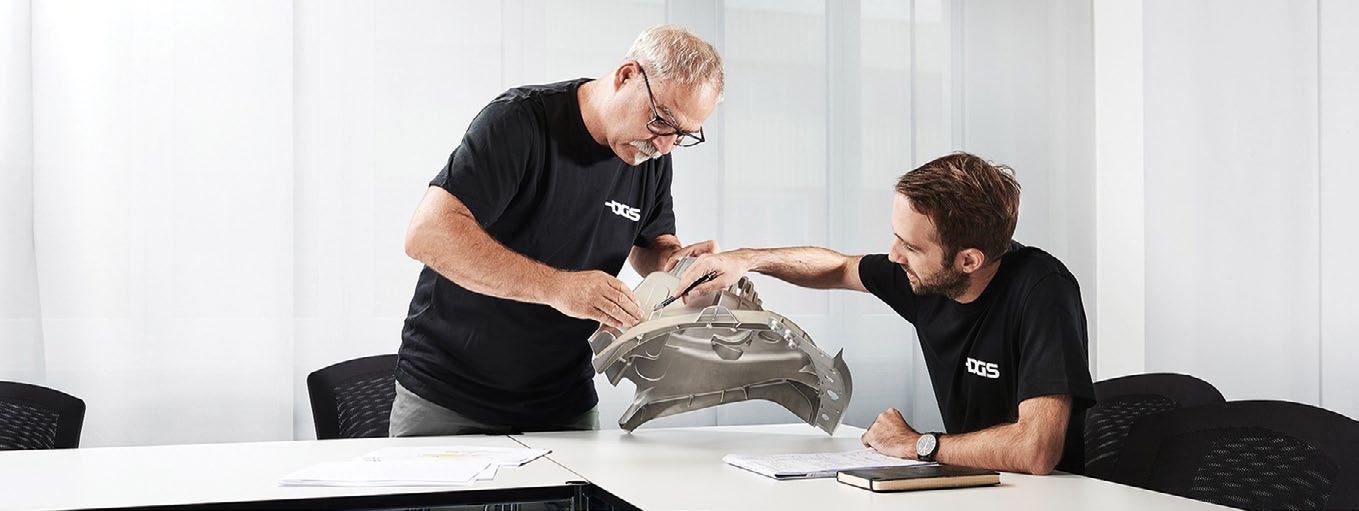
DGS Druckguss is a Swiss foundry company with over 80 years of experience in the production of high-quality die casting parts in lightweight alloys. Today DGS is a global player with three state-ofthe-art production facilities located in Switzerland, the Czech Republic and China.
DGS is a well-known international casting and solution provider, with a special focus on aluminium and magnesium alloys. The company’s special competences lie in the fields of automotive structural parts for body-in-white, in which it enjoys a leading global position.
Pioneering ultra-lightweight castings
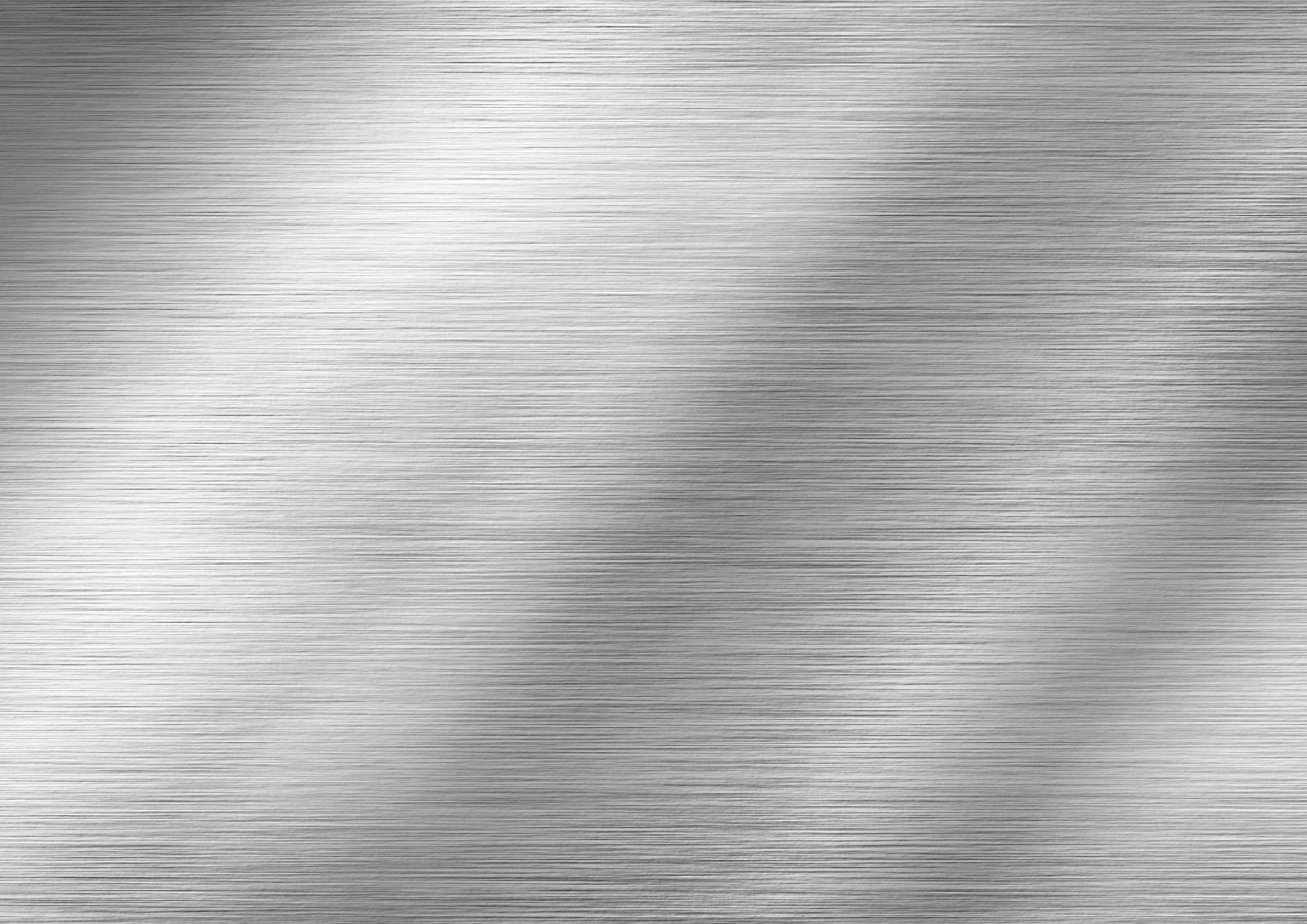
DGS is a technology-driven company that operates cross-site research activities for products, processes and materials which are coordinated globally from its headquarters in Gallen, Switzerland.
The company implements its ground-breaking and futuristic developments into commercial production before their global roll-out to its global distributors. In order to maintain its leadership position and innovative strength, DGS invests over 10 per cent of its turnover in advanced technologies and equipment every year. Its international research and development division is driving new innovations forward in close partnership with its customers.
Together with its clients, DGS develops and tests new alloys and processes and conducts regular workshops for the joint promotion of ideas and continuous improvements. The company is a leading global systems supplier with material, product and process development that involves die casting, heat treatment, machining, assembly and passivation. DSG operates more than 50 die casting machines, which work with a closing force of between 250 to 3,200 tonnes.
DGS recently achieved a milestone in lightweight construction technology in a joint development programme with Audi AG, when it was honoured with a top award at an international die-casting competition in Nuremburg. The special feature of the award-winning product was its optimised design which reduced the product’s weight by almost 20 per cent when compared to the functionally identical part of the previous model.
The pioneering breakthrough was achieved with a high-strength, optimised T6 heat treatment process. The thin-walled design also saves significant amounts of raw materials, thereby contributing to a more sustainable value-chain.
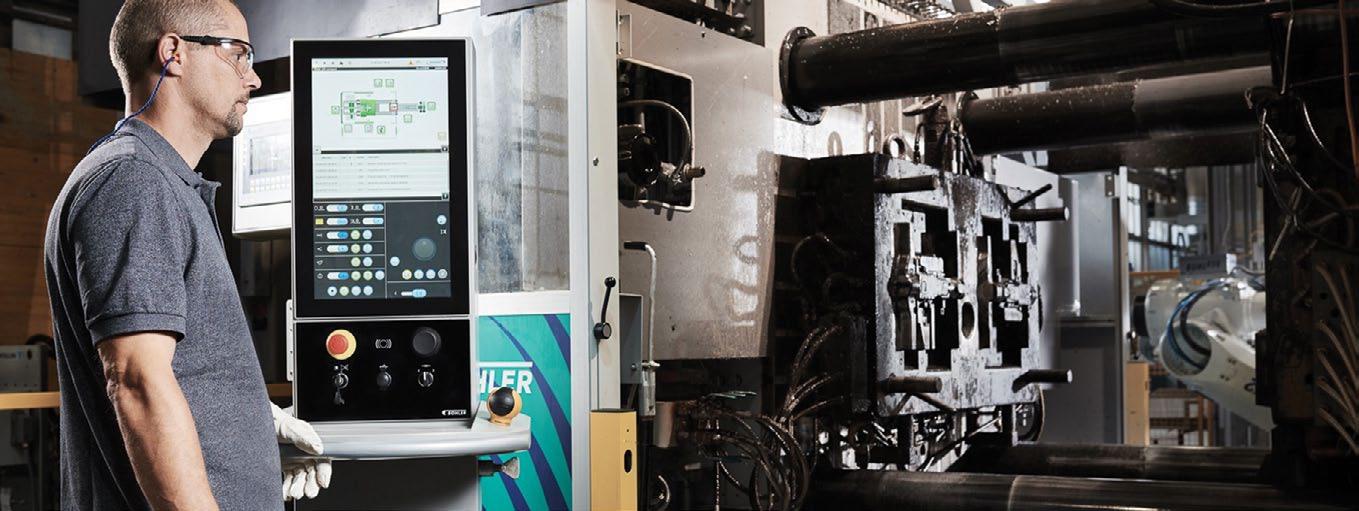
Record-breaking technology
DSG has recently produced one of the largest die-castings ever made in Europe at its Swiss factory (outer dimensions are 2050mm X 54.5mm) The unique die-cast part serves as a frame for an innovative solar collector made by Hoval, a leading European producer of solar power installations.
The new module is equally suited for rooftop applications as well as for in-roof installations. Despite its exceptional size, the finished part weighs only 6,400 grams and the frame is designed to resist wind speeds of up to 140km/h and snow-loads of up to 700kg/m2. An additional project requirement was that under all conditions the tightness of the gasket protecting the solar modules must be guaranteed in order to prevent water ingress, which would impair the function of the solar collector, which in turn could result in a total module breakdown.
Compared to a welded part, which would usually be made from pre-formed profiles, the new casting solution offers a number of key


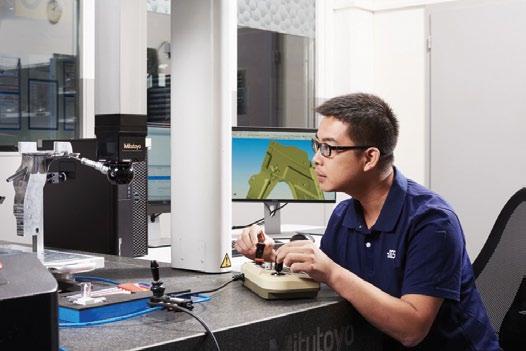
advantages, such as the integration of attachment parts including edge reinforcements, consoles and stops. Furthermore, the special aluminium alloy used for the complex part requires no surface protection.
This unique, very large casting is produced on a Buhler SCD 320 die-casting machine with a locking force of 3200 t. The size of the die alone and the need to ensure a high-quality and uniform casting despite the 2 metre long flow-paths, represented a particular challenge. However DGS was able to meet all its customer’s requirements especially with respect to dimensional precision, accuracy and productivity.
World-class development services
DGS offers a comprehensive, world class range of development services to its customers. The company’s unrivalled experience and competence in die casting alloy and process development enables it to provide the best possible solutions for built-in components, assemblies and systems for its customers.
DGS is recognised as a proven development partner for advanced technology and production competences in casting, along the entire value chain. Its know-how enables it to offer optimised and customised solutions in the fields of materials, products and processes.
Axel Schmidt, head of technology at DGS said, “A satisfied customer will always return to us, either with new development tasks or with sophisticated and innovative products. We want him to become the best in his class”.
Together with its key customers and suppliers, DSG continues to develop and test new alloys and processes for the world’s leading automotive brands. It also works closely with universities and practicaloriented development projects for best-in-class outcomes. For further details of DGS’s latest innovative products and services visit: www.dgs-druckguss.com


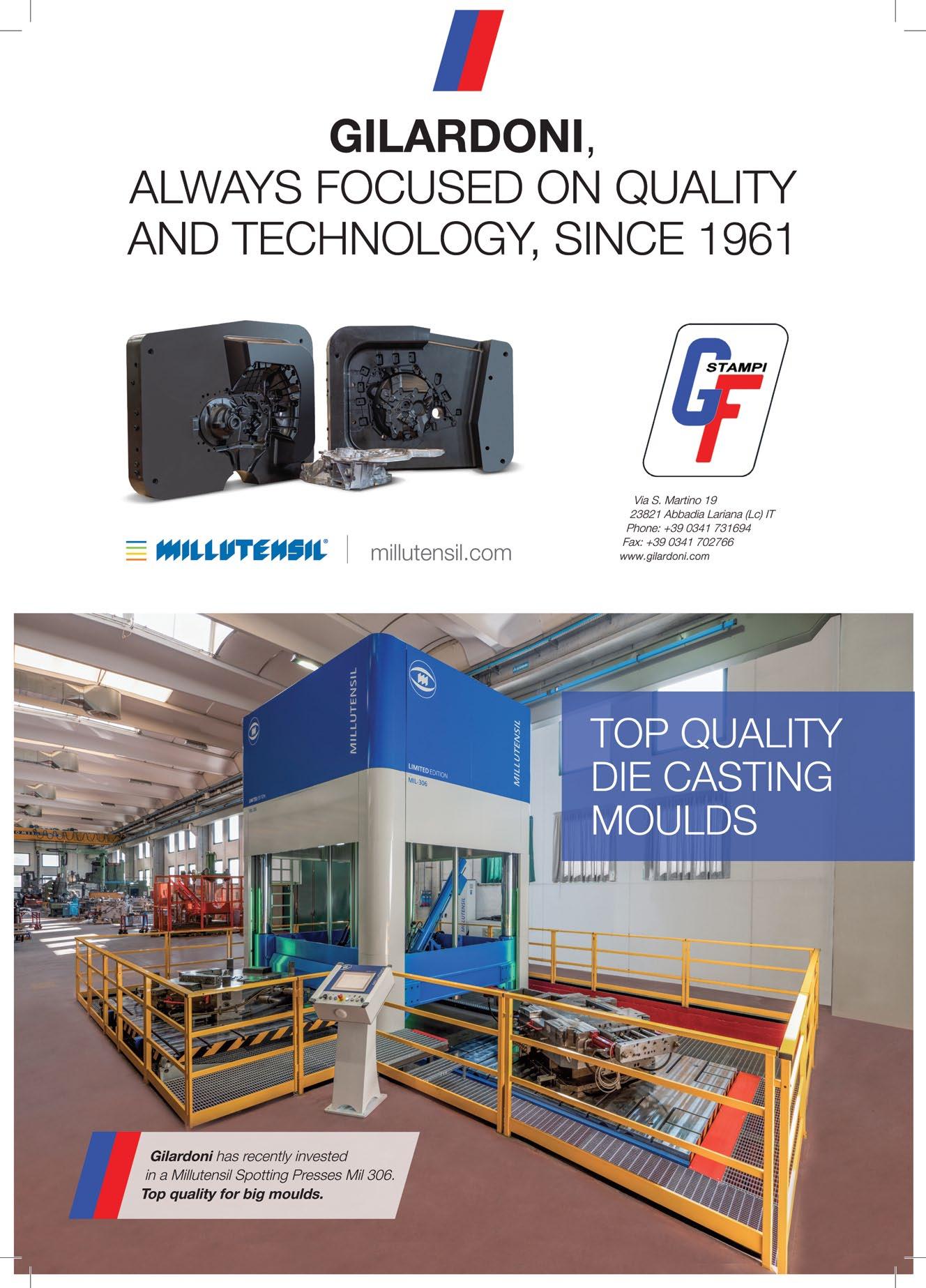