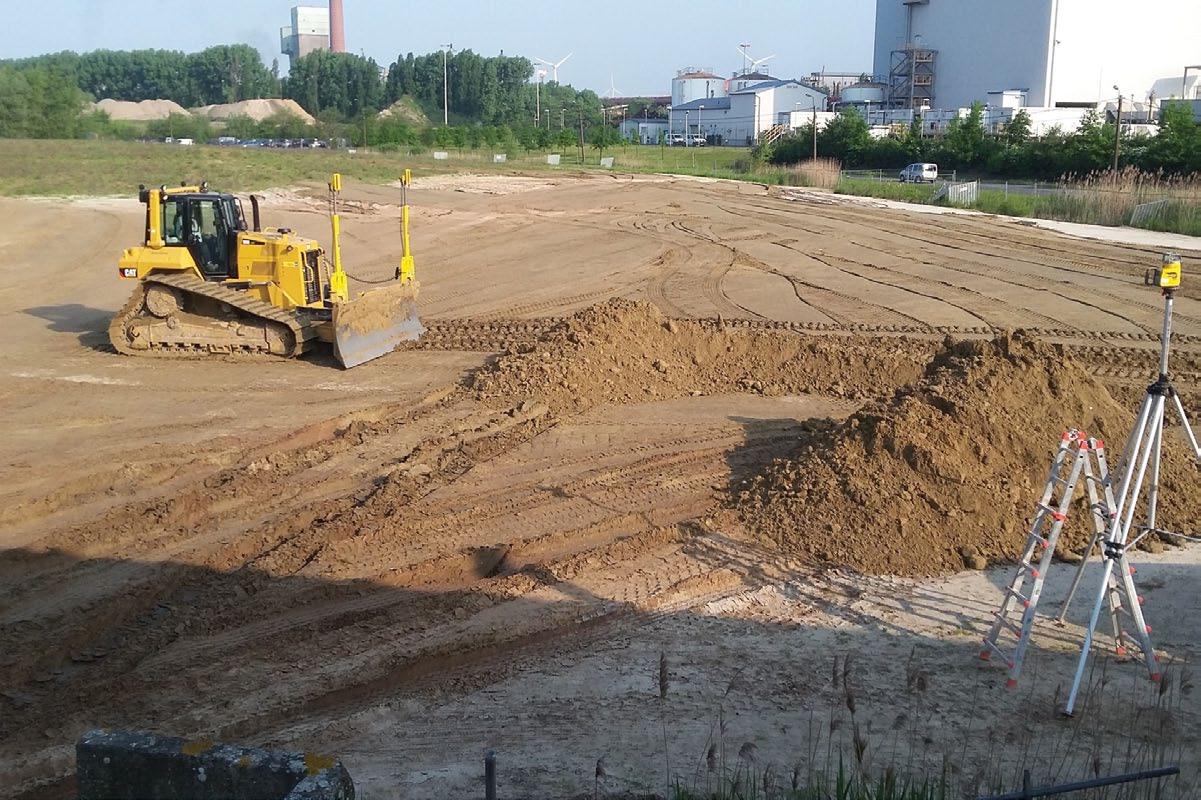
3 minute read
Fuel from steel
Turning carbon emissions from blast furnace gas into bioethanol at ArcelorMittal Gent.
Carl De maré, Arcelormittal Group CTo – Head of Technology Strategy Construction has begun on the first commercial-scale bioethanol plant in Europe to use waste gases from steelmaking as a feedstock. The plant at ArcelorMittal Gent will provide up to 80 million litres of bioethanol annually and demonstrate that flue gases from the blast furnace can be turned into a valuable resource. As well as bioethanol, the plant will also generate heat and energy which will be reused within the plant.
The plant uses a naturally occurring bacteria which feeds on carbon monoxide (CO). “It’s a very energy efficient process as microbes do all the work,” says Wim Van der Stricht, coordinator of the project. “The challenge is to incorporate that natural process into a large-scale, well-established industry. And we’ve done that by innovating and working with partners such as LanzaTech and Primetals Technologies. We’ve also received funding from the European Union’s Horizon 2020 research and innovation programme.” Circular economy in action
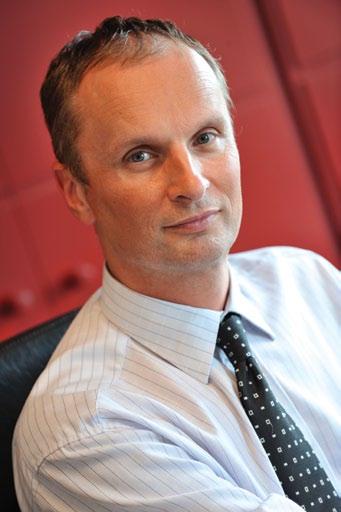
“This plant is a perfect example of the circular economy in action,” says Carl De Maré, vice president of Technology Strategy at ArcelorMittal. “A waste material from steelmaking is being converted into real-world products which are useful, valuable, and sustainable. This plant can produce enough fuel to power 100,000 vehicles using pure bioethanol for a year.”
In the ethanol conversion process, bacteria feed on carbon monoxide and produce ethanol as a by-product. Biomass waste, produced in the process, is digested to produce methane. This is burnt in a co-generation unit to create heat and energy which is reused within the bioethanol plant in processes such as distillation of the ethanol.
Arable land protected
Many existing bioethanol plants use agricultural products as a feedstock. Typically, this comes from crops such as sugar cane, wheat, and
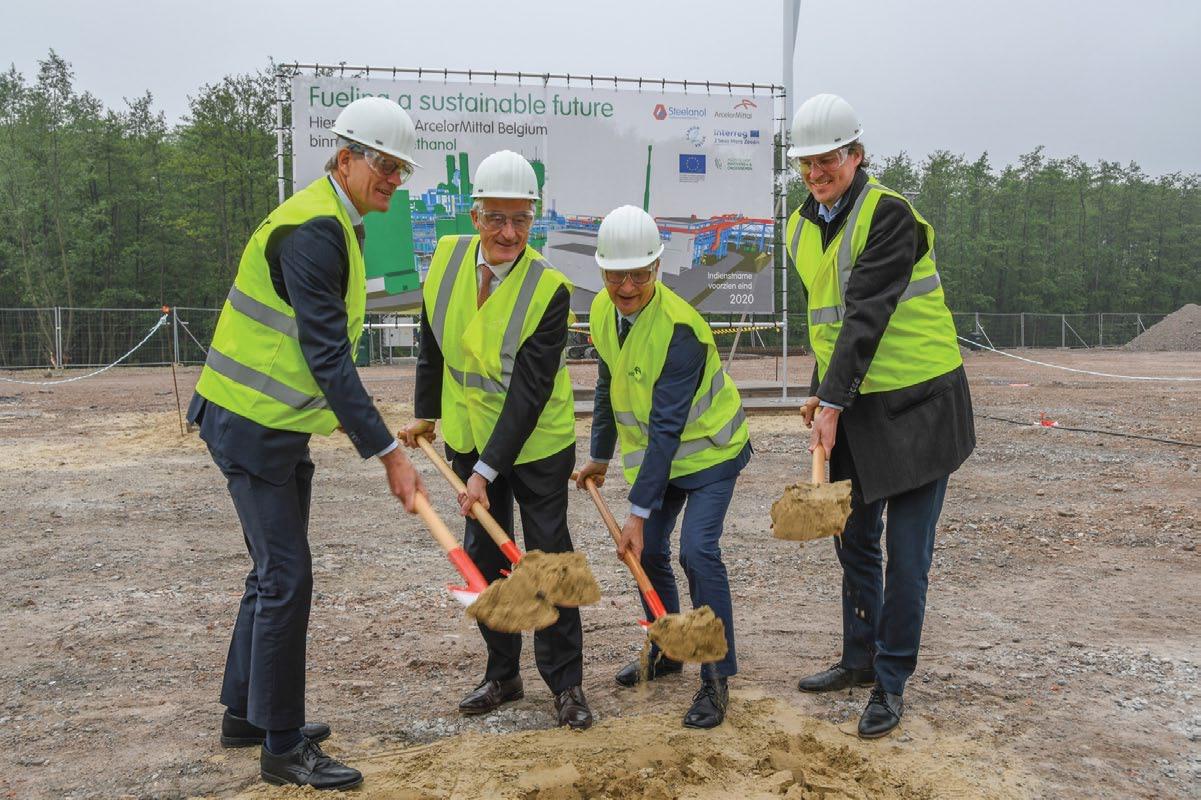
corn which take up land and resources which could be used for food production. “With our technology, we use recycled carbon, so there is no need to tie-up valuable arable land,” explains Wim Van der Stricht.
Although the plant will not be fully operational for at least two years, ArcelorMittal is already getting enquiries from potential buyers. “We’ve had a lot of interest from fuel blenders who use bioethanol as a substitute for petrol (gasoline),” says Wim Van der Stricht. “But we were surprised just how many of our own customers require bioethanol for their applications. From paint to household cleaning products, there are hundreds of important uses.”
ArcelorMittal’s aim for this project is to show that it is possible to create a carbon-neutral steel industry, not just one that produces low levels of carbon dioxide notes Carl De Maré: “The circular economy is critical to achieve that carbon-neutral status, but ArcelorMittal can’t do it alone. We need additional partners in this new value chain and to help close the loop, we want our customers to be a part of this innovative technology. I urge every customer that utilises bioethanol, or is active in recycling waste streams, to get in touch through the project’s website.”
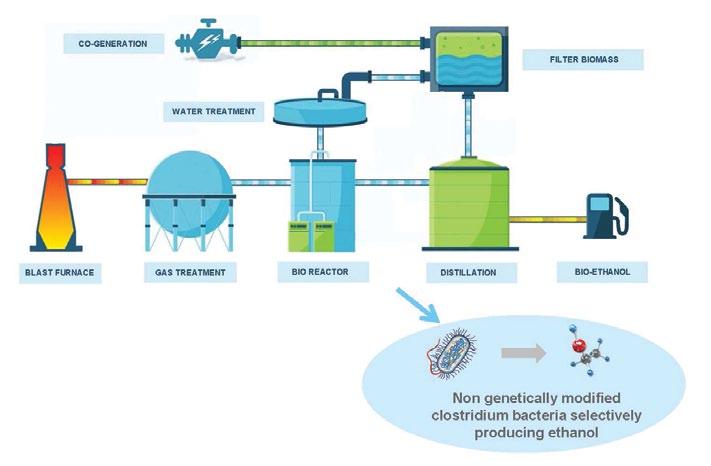
Proven technology moves to industrial scale
Ethanol plants like the one being installed at ArcelorMittal Gent have been trialled in China, proving that the technology works. However, the ethanol conversion plant in Gent will be the first to produce bioethanol on an industrial scale and in a cost-effective way with a high level of energy efficiency.
Preparatory work for the conversion facility has already started. Engineering work for the plant has been finalised and equipment based on best available technologies (BAT) was ordered in mid-2018. That equipment is expected to be delivered by summer 2019. The plant will start producing bioethanol around mid-2020 before ramping up to full production.
More than 500 temporary engineering jobs will be created during the construction phase. Once commissioned, the plant will be run by a team of around 30 people including bio-engineers, operators, and technicians.