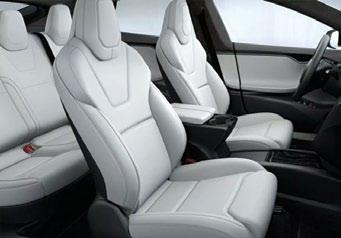
8 minute read
Textiles, Home & Personal Care news
NeWS
New developments in the Textiles, Home & Personal Care industry
Taking Ontex to the next level Tesla developing “loadbearing fabric architecture”
Ontex, the world leading supplier of disposable personal hygiene products, has announced its plans to leverage its strong market positions, develop further growth opportunities and implement the Transform2Grow program to drive sustainable growth and create further value.
Charles Bouaziz, Chief Executive Officer, declared: “Since its IPO in June 2014, Ontex has emerged as a leading international personal hygiene company, delivering consistently on its strategy to grow outside of Western Europe, increase branded business and expand its presence in Adult Incontinence. Faced with unprecedented headwinds and challenges in the last two years, Ontex has demonstrated the resilience of our business model. Yet, further action is required to take Ontex to the next level.
“Our comprehensive transformation plan, Transform2Grow (T2G) will step-change our operational efficiency and commercial practices. With T2G-enhanced commercial focus and competitiveness, we will accelerate execution of our two strategic priorities: Strengthen our current leadership positions and expand into new businesses and geographies within our core categories. Our objectives remain to outperform markets in which we operate and improve our profitability and cash generation. Together with committed teams, we will make Ontex a stronger and more profitable company, delivering growth and creating value for all stakeholders.” Visit: www.ontex.com
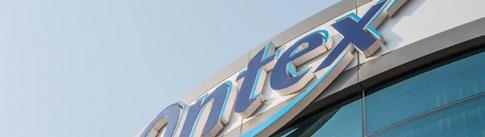
universal fibers opens new european plant in Poland
US-based flooring, transportation and industrial fibres company, Universal Fibers has celebrated the opening of its new European facility in Gorzów Wielkopolski, Poland.
“In support of our honoured customers in Europe, we are thrilled to be opening our newest manufacturing facility here in Poland,” said Marc Ammen, CEO of Universal Fiber Systems. “This aligns with our strategy for global growth which began in 2009 with expansion into Asia and later in the U.K. Since then, customer response has been tremendous, and we are winning in partnership with our industry leading products, quality and service.”
From extrusion to finished yarns in multiple chemistries like type 6 and 66 nylon, the plant is fully integrated. It also serves carpet manufacturers across the continent working in the residential, commercial and automotive sectors.
“This new facility marks another investment in our commitment to provide the highest level of quality and service to our customers,” said Phil Harmon, President of Universal Fibers. “As a global company, our leading technologies from the US and Asia are now deployed locally in the European market. We couldn’t be more pleased with this investment and the platform it provides Universal Fibers to expand in the region.” Tesla is currently working on a brand new “soft and durable” type of fabric to be used in seating in its electric vehicles.
The patent was filed by Tesla last year but it only just coming to public attention. The name of the developmental fabric is “load-bearing fabric architecture” and the intent is to make in-car seating last longer.
Tesla outlined the problems with current “automotive textiles” in the patent application. It said that soft fabrics were unable to withstand the continual sliding in and out. This problem has led to car manufacturers being forced to use tougher fabrics, which are not always soft to the touch.
Tesla feels that the solution to this problem is a new fabric architecture, that both durable and soft to the touch. It is a multi-layer fabric. The top layer being the softer, and the bottom, load-bearing material, would be made of something tougher.
When sat upon, the softer layer will compress and flush with the strong bottom later, making a more durable fabric.
How well the technique works and whether or not the softer upper layer lasts longer is still unclear. The price of the material is also an ongoing question and if the material will be more cost effective than the synthetic leather that Tesla is currently using for its seats.
Many companies file patents for technology that they ultimately never use, and it’s also unclear whether the new Tesla patent will join those ranks. Visit: www.tesla.com
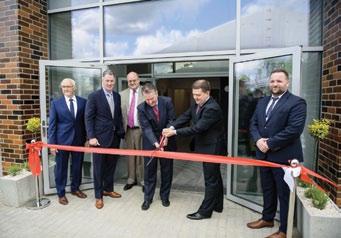
Fund opens to reduce waste from plastic packaging and textiles
The uK government is inviting organisations to apply for funding under a grant scheme to boost the recycling of plastic packaging and textiles. organisations in england can apply for government funding for solutions to improve recycling of hard-to-recycle plastic packaging such as plastic trays, pots and tubs, plastic films and pouches, as well as funding for projects that boost the recycling of textiles. For plastics this could include innovative sorting or segregation equipment, and smarter systems to enable sorting of different polymers. For textiles this could include machinery for recycling textiles, technology for disassembling or sorting textiles, and automated processes for removing items from textiles such as zips. The uK generates around 2.4 million tonnes of packaging waste annually. Around 40% of all plastic produced in the uK is used in packaging. In 2015, there were 300,000 tonnes of clothing in the uK going to landfill or incineration. Visit: www.gov.uk
INDUSTRYNEWS
arMor attacks the textiles market
ARMOR, a major designer and manufacturer of thermal transfer ribbons for printing of barcode labels, is moving into the textiles market. Based in Nantes, France, the manufacturer has taken four years to develop an ink perfectly adapted to highly-demanding textile media. A major new feature: in addition to the thermal transfer ribbon, for the first time ARMOR is also marketing a range of receptors composed of 10 care labels made of nylon, polyester and satin. With the new offering having required an equipment investment of EUR300,000, ARMOR estimates it can cover over 90% of its customers’ requirements. ARMOR launched the AXR TX, a new grade of thermal transfer ribbon dedicated to the printing of textile labels and is supplementing the offering with a range of 10 print substrates: specially designed for the textiles market, made of nylon, polyester and satin. They offer a variety of properties: printable on one or two sides, treated to avoid curling up during washing, stain resistant and widths of between 10mm and 120mm. Textile receptors are delicate products with a highly specific life cycle. To guarantee quality, ARMOR has conducted a battery of tests, both internally and at external laboratories operating under AATCC standards: washing, cold wash, ironing, sweat testing and skin test. The ribbon and labels of the AXR TX range are also Oeko-Tex certified and can therefore be used for baby articles. With this new range, ARMOR is targeting the textile cutting field. It is an activity the manufacturer used to do several decades ago, when it used to slit typewriter ribbons made of polyester or nylon. ARMOR has invested in the new slitting machine dedicated to textile ribbons. The slitting principle is the same as for thermal transfer ribbons, but the technique is totally different. It was therefore necessary to train operators to use the new equipment. With this combined ribbon-label offering, ARMOR is supplementing the demands of traditional customers who are yet to get to grips with the textiles market. But it also represents an opportunity to penetrate the existing market of the large textile label printing producers. “Innovation is an integral part of ARMOR’s DNA. The AXR TX product range has mobilised multiple departments... This collective effort now enables us to attack the textiles market with confidence”, states Yohann Froment, Marketing & Communications Director of ARMOR Industrial Coding and Printing. Visit: www.armor-group.com
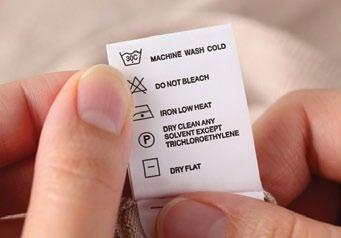
BASF, Estée Lauder & RSPO partner for sustainable palm oil project
Apartnership between BASF, Estée Lauder, the Roundtable on Sustainable Palm Oil (RSPO) and Solidaridad, a civil society organisation, will promote the use and production of sustainable palm oil and derivatives in Lampung, Indonesia. The project supports independent smallholder farmers in the Indonesian region, offering continuous education and other resources on the implementation and maintenance of sustainable palm oil. The target is to see one-third of the supported smallholders becoming certified according to the Smallholder Standard of RSPO within three years. The project aims to foster a sustainable palm oil production chain that is globally competitive and free from deforestation, as well as increasing social and economic benefits for farmers. Heske Verburg, Managing Director, Solidaridad Europe said: “We are delighted that [companies] are… providing direct support for sustainable palm oil projects. When palm oil is produced sustainably, and in a future-proof manner, it can actually contribute to resolving grave issues for both farmers and the environment.” Greg Polcer, Executive Vice President, Global Supply Chain, at Estée Lauder said: “Many livelihoods in this community are inextricably tied to the production and we support ensuring that it is produced sustainably - both for the long-term benefit to the environment and the community.” “Approximately 40% of world palm production comes from smallholder farmers who rely on it for their livelihoods,” said Daniele Piergentili, Vice President, Home and Personal Care at BASF in North America. “The partnership… enables us to support these farmers and increase the availability of sustainably produced palm oil.” “For sustainable production to become mainstream and fully inclusive, the RSPO believes it is imperative to support smallholders through a variety of different approaches,” said Ashwin Selvaraj, Head of Smallholder Unit in the RSPO Secretariat. Visit: www.rspo.org
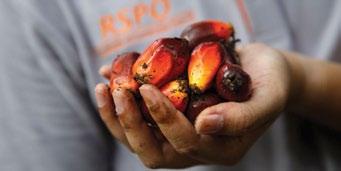
Sonoco Alcore introduces new EcoSPAN
Belgian paper tube maker Sonoco Alcore debuted its new, patented ecoSPAN engineered textile-based cores at the ITmA show in Barcelona in June. Sonoco’s ecoSPAN technology creates a tailored friction surface to drive optimal performance in Spandex yarn production. unlike current Spandex yarn cores, which creates friction-driven transfer problems and minimises customisation possibilities, ecoSPAN cores use a patented, customisable, aqueous coating, eliminating the need for additional film materials on the outer surface. This makes ecoSPAN cores 100% recyclable and a more sustainable option than comparable cores. “With ecoSPAN, we have the unique capability to customise the friction performance of the core surface to match each of our customers’ unique requirements,” said Ismael Hernandez, Sonoco Global Technology - Textiles. “And because our surface properties can be tailored so finely, we’re able to create a much more efficient transfer environment.” Visit: www.sonocoalcore.com