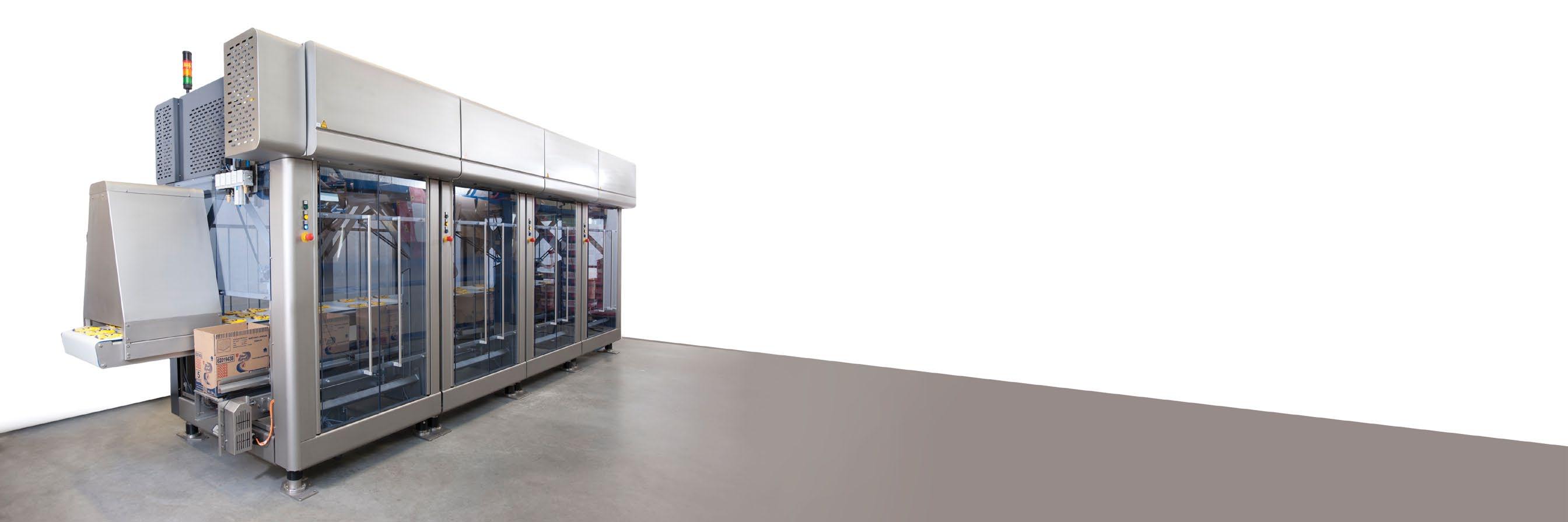
4 minute read
Top of the pile Blueprint Automation
Top of THe pile
Blueprint Automation is a global leader in the design and manufacture of packaging automation solutions. Innovation driven, the company continues to set new benchmarks in vision-guided robotics and ‘pick-frompile technology, as Philip Yorke reports.
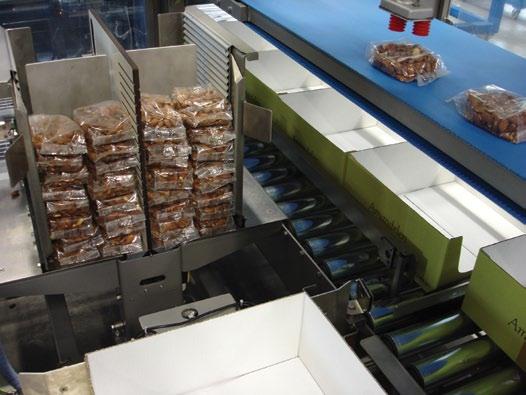

Blueprint Technology (BPA) was founded by Bob Prakken in the Netherlands in 1980. As an engineering innovator, he set out to bridge the gap in the automatic packaging of non-rigid packages.
The success of the company was instantaneous and within ten years there was a major manufacturing plant operating in the Netherlands, and a 40,000 sq ft. US subsidiary manufacturing visionguided robots in Virginia, and this was in addition to a substantial sales office presence in the UK.
Rapid growth continued into the 1990s with the establishment of new offices in China and Brazil set up to further develop the Asian and South American markets. Sadly, Bob Prakken passed away in 2012, after which, his son Martin who had grown up with the company, took over the reins and is now the CEO of Blueprint Automation.
Today BPA designs, develops and manufactures case and tray packaging solutions for flexible and other tough-to-handle packages such as ‘doy-packs’, pillow bags and four-sided sealed bags. These unique products have gained a global reputation for their quick change-over, flexibility and functional design. BPA’s fully integrated state-of-the-art technologies include gravity, pick-and- place, wrap-around and visionguided robotics.
3D vision
In keeping with the entrepreneurial talents of its founder, BPA continues to innovate with a number of exciting new technologies in the pipeline. Its broad product portfolio and turnkey capabilities cover such sectors as vision-guided robotics for stacking and loading, wrapper and carton loading, case packing, tray packing, and end load cartoning, as well as semi-automatic collating and dedicated packaging automation.
One of the most innovative products to be launched recently by BPA was its new “Pick-from-Pile” robotic technology and unique modular frames. These were showcased at Pack Expo recently where the company demonstrated its new 3D vision system that had been integrated into their successful Spider V series, which allows cameras to distinguish items that are in a shallow pile on a conveyer belt. This cutting edge “Pick-from-Pile” breakthrough eliminates the need for a product to be singled out by robots, thus significantly reducing costs for systems where packages come from bulk in-feed sources.
In addition, by combining all controls within a single system, BPA’s standard modular design reduces costs still further by minimising wiring content. Its environmental footprint has also been significantly reduced by eliminating the need for bulky external electrical cabinets.
Healthy assets
A little earlier this year, BPA announced the launch of a major “Asset Health and Reliability Programme” (AHRP). This customisable, valueadded addition to its long-term repair and maintenance service delivers significant cost-saving benefits to customers. AHRP allows customers to increase asset health, optimise performance of existing machinery and validate new equipment performance. Clients who
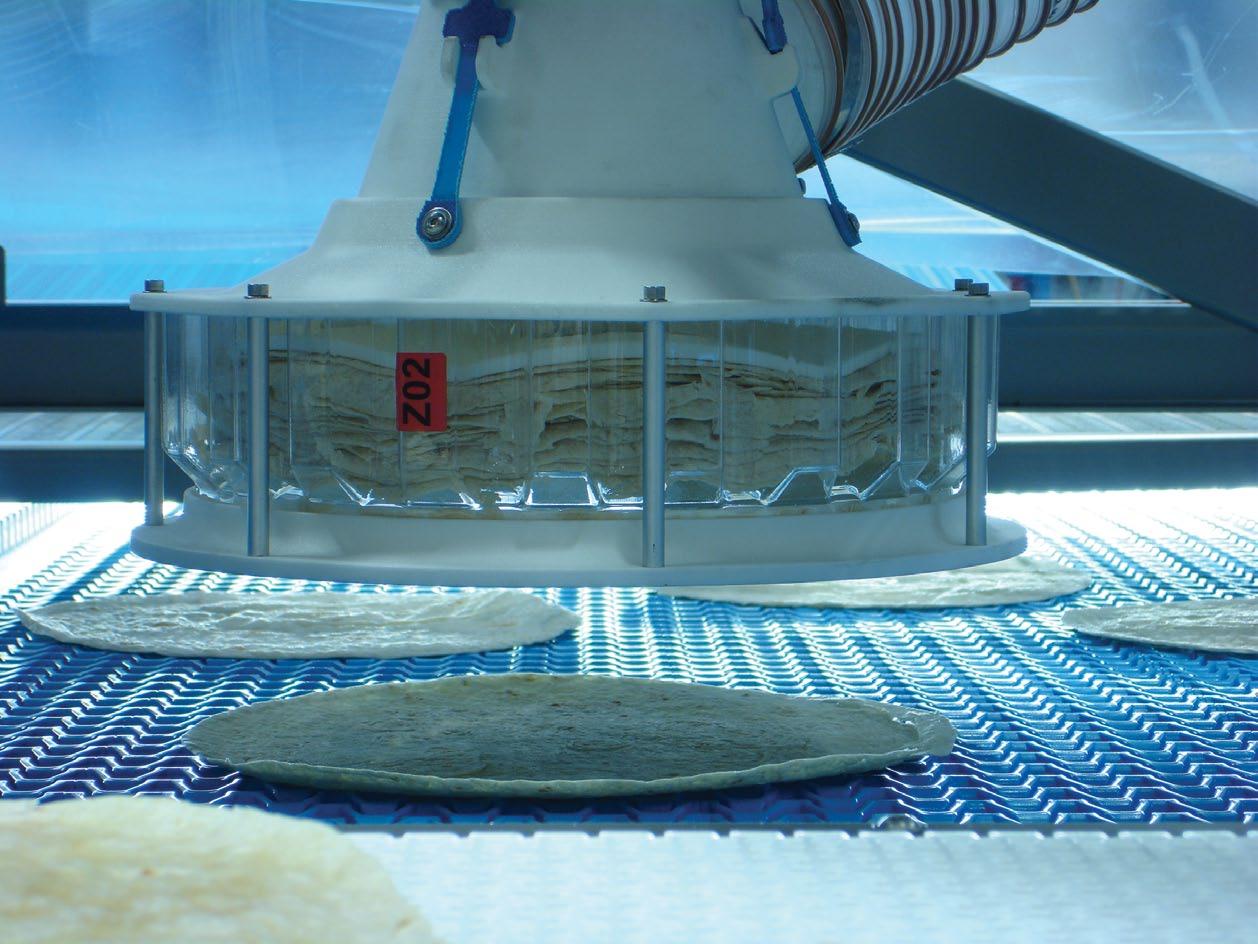
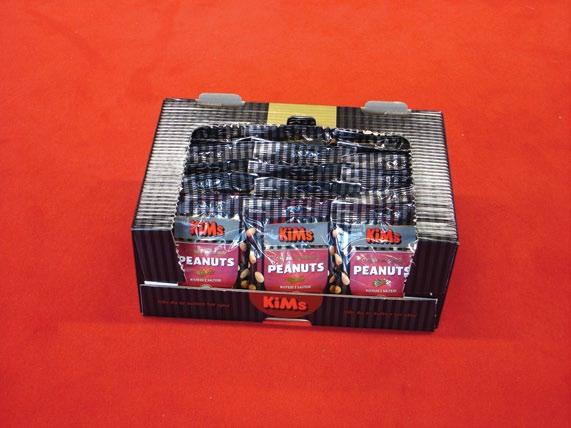

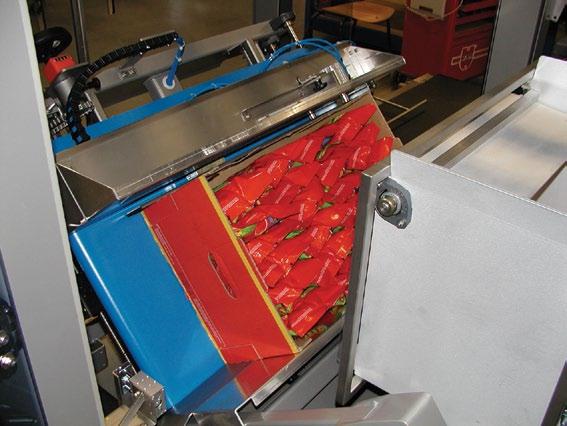
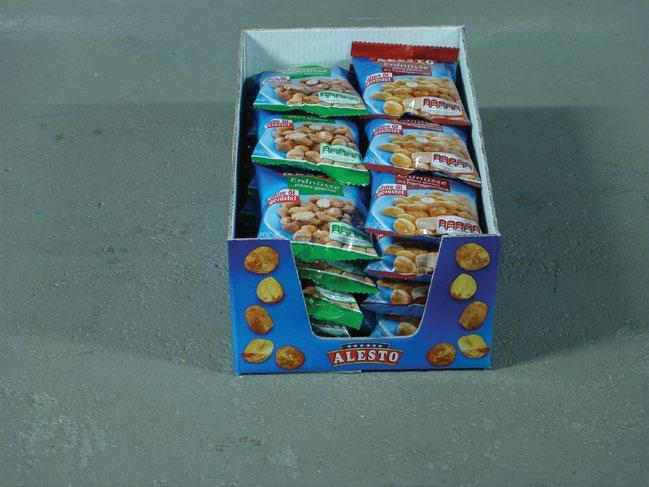

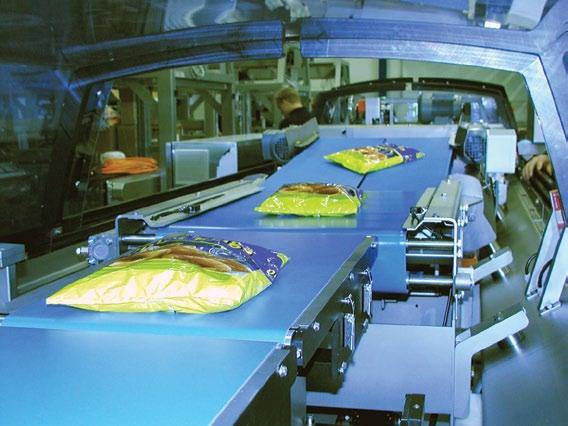
take advantage of this innovative programme can expect to receive a complete asset health inspection to identify any parts failures, a report identifying issues relating to repairs, upgrades and programming and training, as well as a long-term repair and preventative maintenance service.
These value-added benefits will result in optimised system performance, increased machine life and improved knowledge on the care and maintenance of BPA systems. Gary Marker, Asset health and Reliability Specialist at BPA said, “Our goal is to bring added-value to our customers through a proactive approach to identifying repairs needed to eliminate unexpected downtime and increase uptime, as well as ensuring optimisation of machine performance and an increase in equipment lifespan”
Recipe for success
Following the publication of an important research report from PMMI Business Intelligence, a packaging company called White Castle, decided that it needed to increase efficiency further and although it had used robotics for ‘Pick-and-Place’ in the past it had not used Vision Guided Robots. The patented BPA system includes two ABB IRB 360 Flex-Pickers, three-axis delta-style pick-and-place robots that together operate at speeds of 160 two-packs/min. All three carton sizes, 4,16 and 18, are all handled by the one system. In addition, each carton size has its own dedicated carton erector and sealer.“The only change-over we needed is for the robot itself and it’s pretty simple” explained White Castle Project Manager, Brad Rife.“It’s just a menu selection recipe for each different product.”
With the installation of the BPA cartoner, White Castle was able to re-deploy three operators per shift to other operations at the plant, who had been manually loading cartons. “The BPA robots are able to load at a consistent, uniform rate in tandem with the on-going rate of production. There is no accumulation anywhere, it is loading in real time as product frames come down the belt, and that is far better for the product. It’s fast getting to the point where delta robots and robotic guided-vision systems, offer rapidly advancing capabilities and where it’s guaranteed that it will result in a cost-effective and operable system – especially if you are working with a reputable vendor.” Rife concluded. n
For further details of Blueprint Automation’s innovative packaging systems and services visit: www.blueprint automation.com
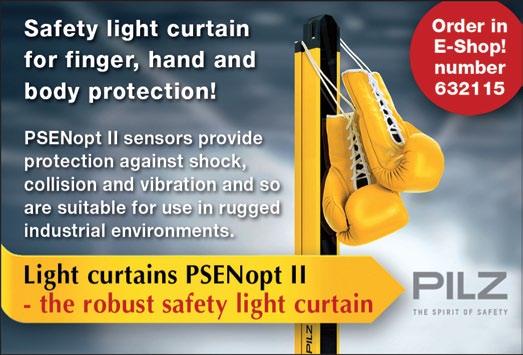