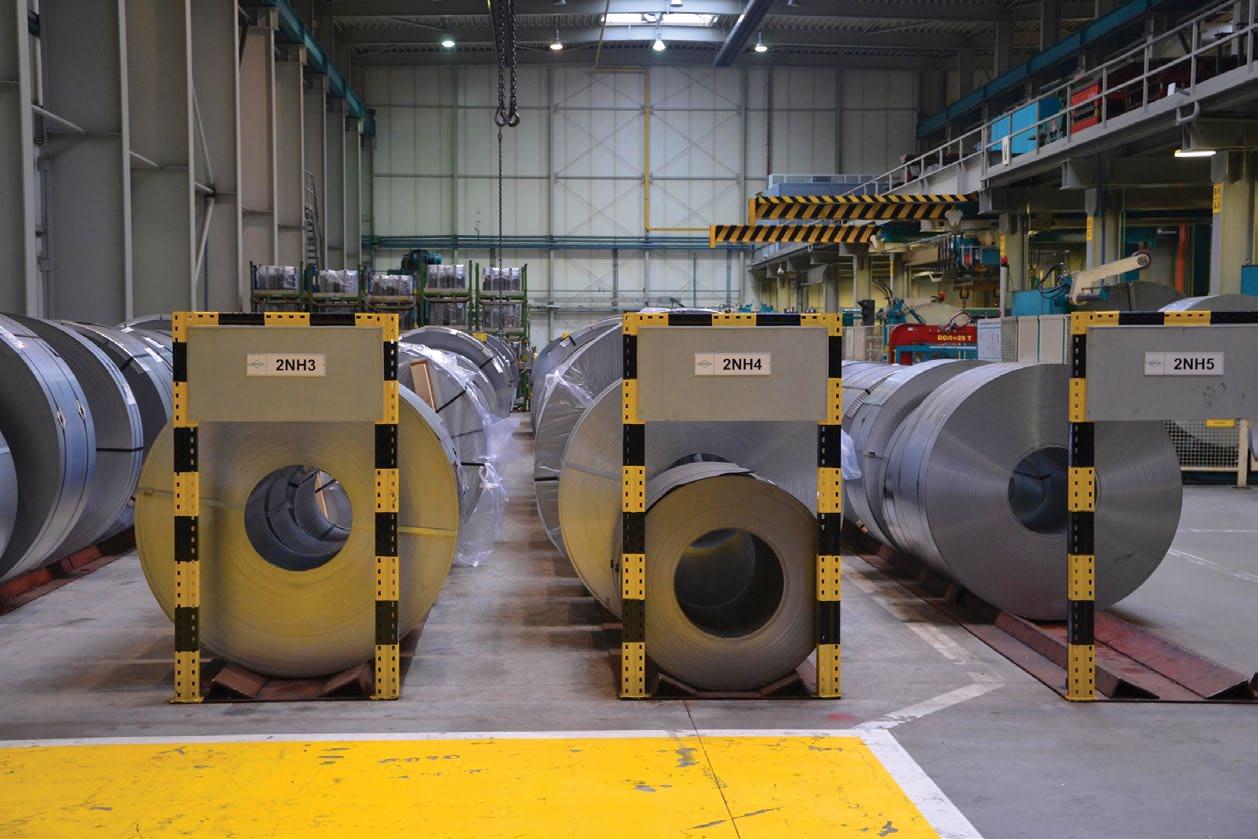
4 minute read
unique, performance-plus systems Gedia
unique, performAnceplus systems
Gedia Poland is a part of the international Gedia Automotive Group, an established TIER 1 supplier to the global automotive industry. Philip Yorke reports on the company’s latest developments, its innovative new technologies and revolutionary quality control systems.
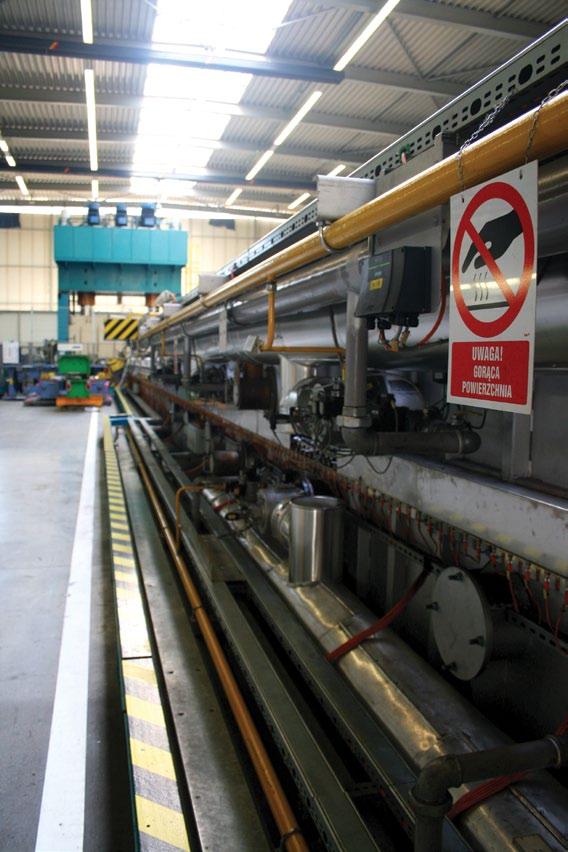
The Gedia Group was founded in Germany more than a hundred years ago and has been manufacturing products for the automotive industry since 1955. The company produces structural parts and assemblies for the construction of automotive lightweight body panels and chassis components.
The Gedia Group is a truly global player with a total of eight production sites located in Germany, Poland, Spain, Hungary, China, India and Mexico. In addition, the company has joint ventures and strategic alliances with specialist US companies. Gedia Poland is one of the group’s most important production facilities. The extensive site operates state-of-the-art equipment for the machining of complex steel and aluminium automotive components.
Gedia Poland is constantly following its clients’ latest developments and market expectations. Its production processes also involve the latest technologies for hot and cold stamping, welding and laser cutting as well as for specialised adhesive processes.
Today the company’s list of blue-chip clients number many of the world’s leading automotive manufacturers including: Audi, BMW, Daimler, Chevrolet, Ford, Fiat, Porsche, Skoda, Vauxhall, Volvo and VW among many others.
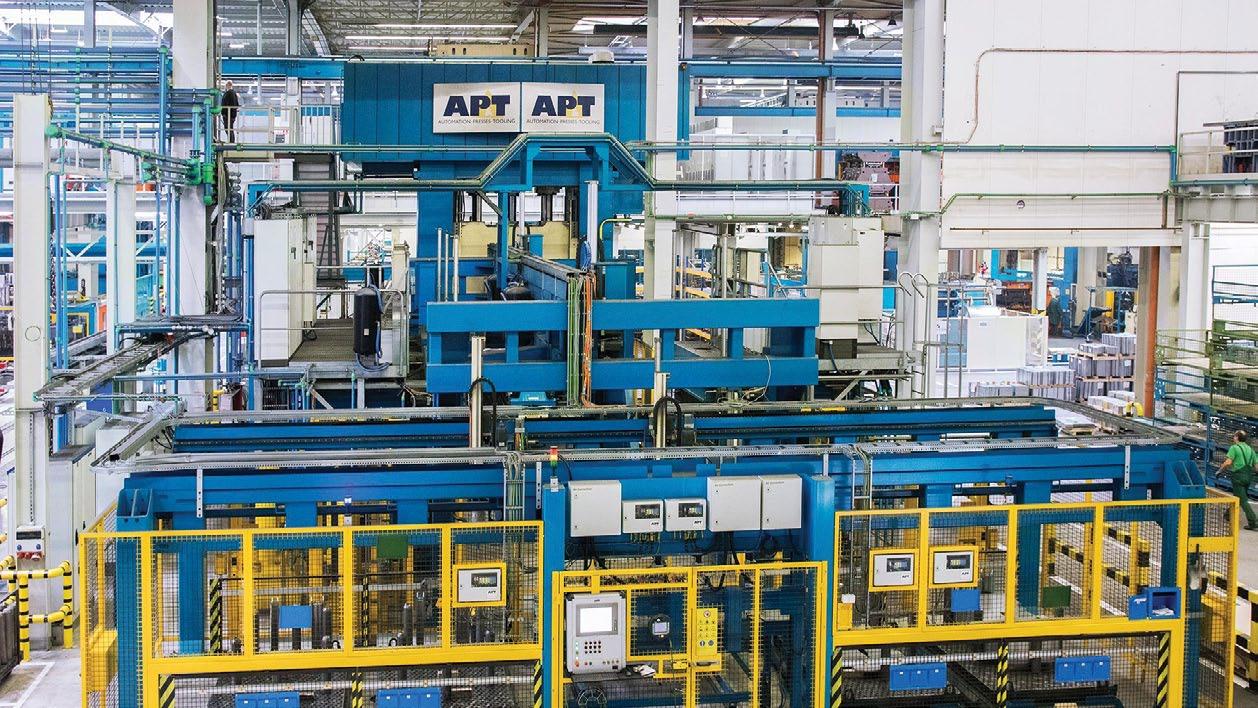
Performance by design
Technical innovation and an ongoing quest for perfection are at the heart of the culture at Gedia Poland. A spokesman for the company told Industry Europe, “Each automotive part produced in Gedia Poland has its beginnings in trust, with which we are endowed as a result of a client entrusting us with a given project. Our Technical Production Preparation Department is involved from day one. Our DTPP design engineers and automotive specialists participate in design meetings for the development of new devices and the manufacture of lightweight production parts”.
“Then based upon our client’s guidelines, in collaboration with our design engineers in Attendorn, Germany, we plan further processes and operations. These can include stamping, laser cutting or welding processes, followed by initial testing of the prototype and the monitoring of the progress of the project until it is transferred to final serial production”.
To underscore the success of the Gedia Technical Preparation Department, BMW recently honoured Gedia Poland with a visit to its modern manufacturing facilities for its futuristic sports car, the BMW 18 Roadster, for which Gedia Poland makes the lightweight aluminium trunk, which is the largest aluminium component in the car. This exceptional automobile is powered by a hybrid drive system consisting of a 231 bhp petrol engine and a 143 bhp electric motor. The total power output is a massive 374 bhp and the torque is an astonishing 570 Nm. Gedia Poland is proud to have contributed to such an innovative world class automobile.
Revolutionary quality-control
Until recently Gedia has focused on standard tactile measurement techniques for its quality control measurement systems. These utilise coordinated measuring machines and gauges for the quality control of assemblies, as well as for tool making processes.
However, today this approach to quality measurement has reached its limits as the company continues to expand its output and number of manufacturing locations. The inspection of sheet metal parts has also become time and labour intensive as parts must be transported several hundred metres from the press or fabrication production areas to the central measuring room.
In order to streamline the quality control processes, a new optical 3D measurement coordinate system has been developed by Gedia and installed with the implementation of new optical metrology
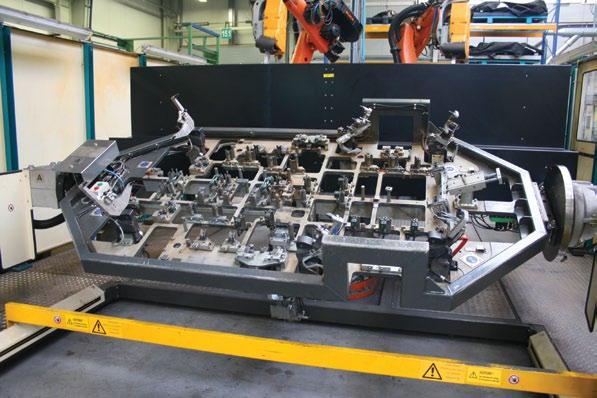
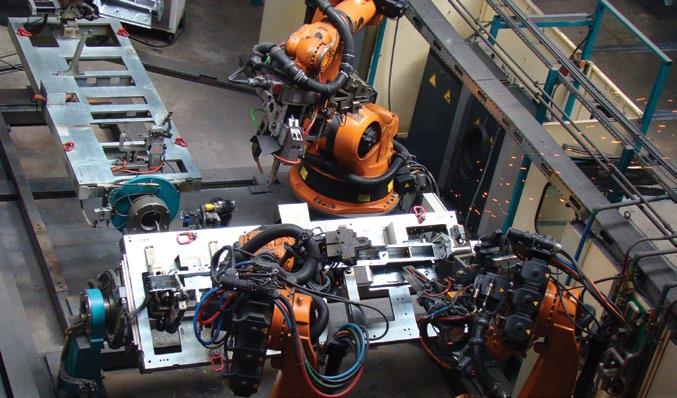

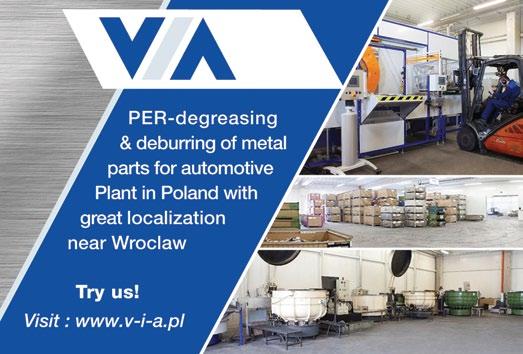
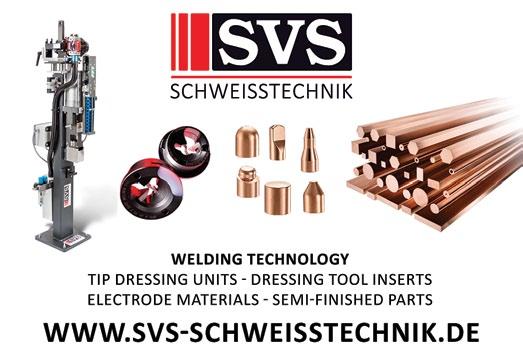
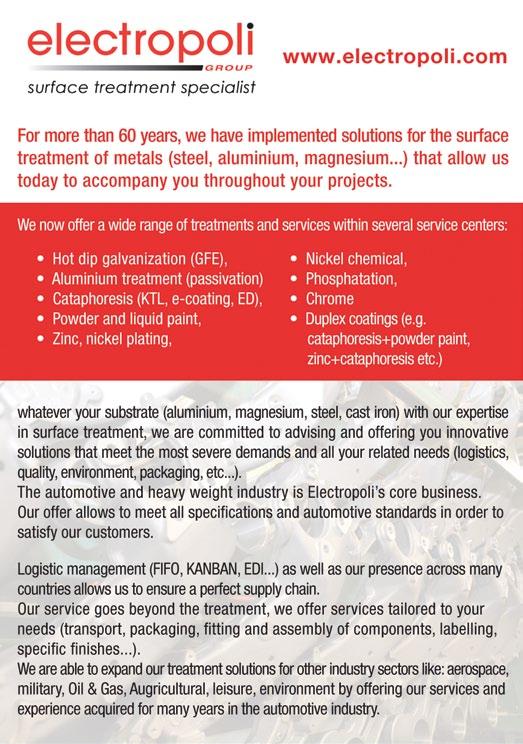
systems. This makes the measuring process more flexible, as well as cutting costs and dramatically reducing the time involved.
This innovative quality control approach is an important step in realising the Gedia Group’s goal of leading the industry in production technology. As a result of these technical advances, the new, revolutionary, full-surface optical 3D coordinate measurement systems are now being implemented worldwide at all Gedia production sites.
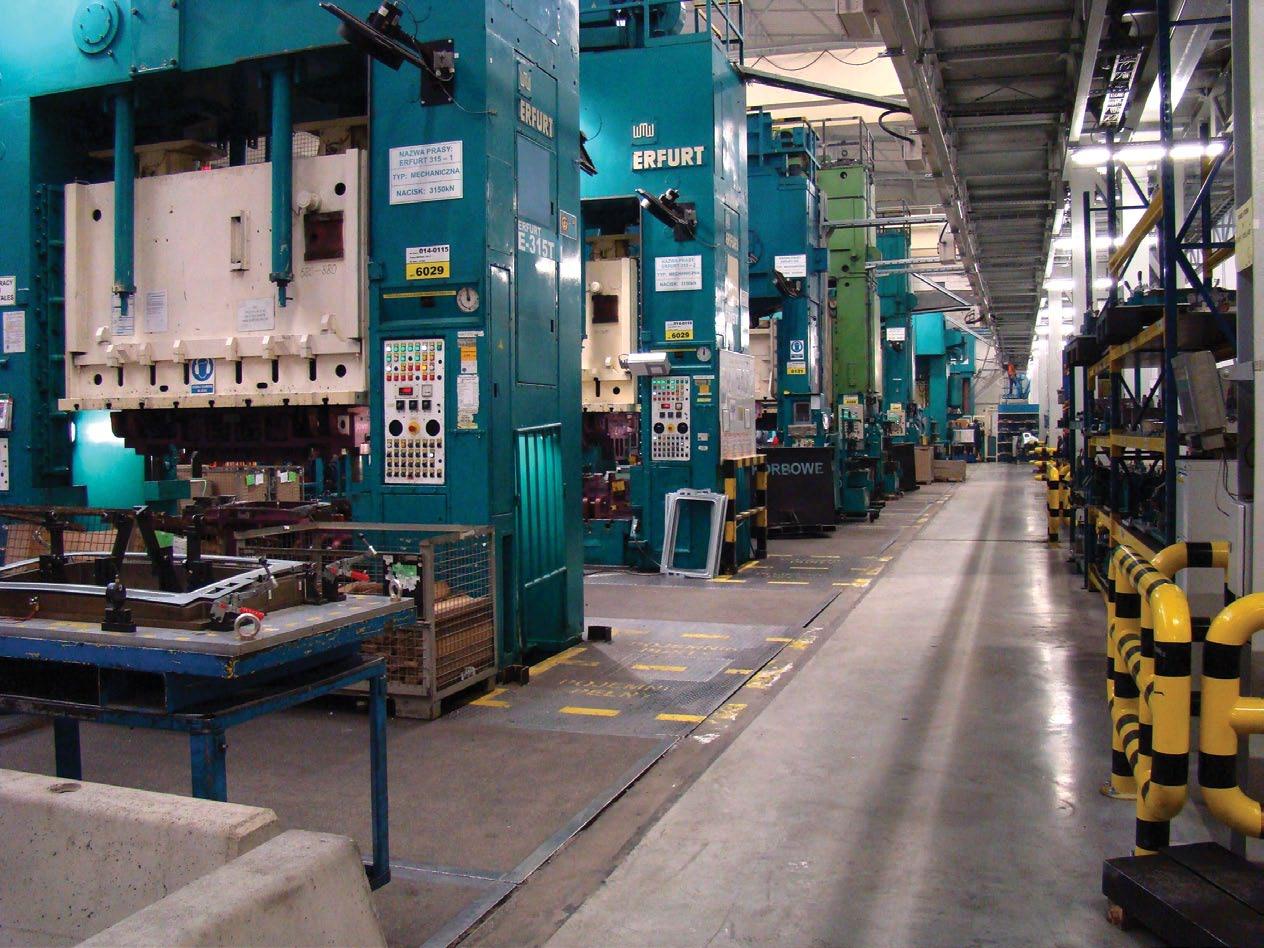
unique single-technology system
Today, with its fast supply of precise measurement data, the high resolution optical ATOS 3D digitiser has fulfilled all the company’s criteria for its vast range of diverse component sizes and the surface characteristics of its complex automotive components. From prototype development to serial-production measurement, part analysis, digitalising and up to virtual joining of assemblies, all of these processes can be performed by a single-technology, as opposed to the much less versatile, more traditional tactile measurement methods.
In order to streamline the quality control measuring process still further, the decision was made by Gedia to have the new optical measuring system transported to the component instead of transporting the component to the measuring system. As a result, new measuring transportation equipment was specially designed in order for the system to be fully mobile for its use in a busy production environment.
Gedia’s suppliers are carefully chosen and assessed. Amongst their key partners are VIA Technika Obróbki powierzchniowej Sp. z oo, EXACT SYSTEMS Sp. z o.o., and Electropoli Group. n
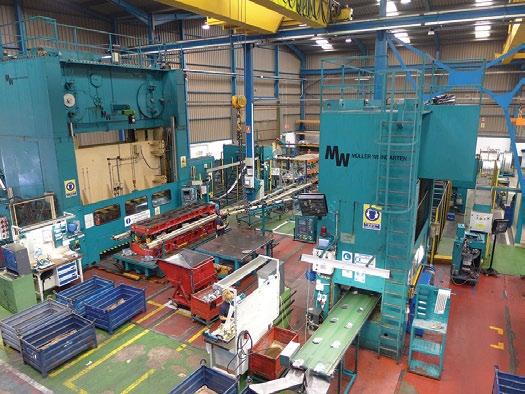
For further details of the latest innovative products and services developed by the Gedia Group visit: www.gedia.com
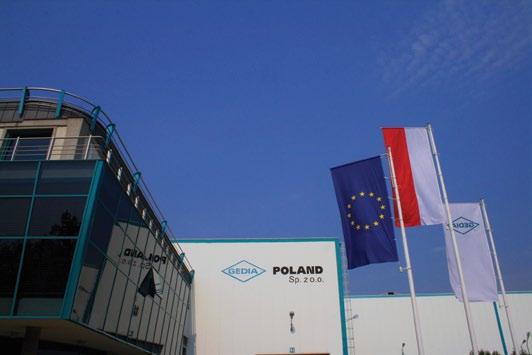