
4 minute read
meeting the Plastics Challenge STF Maschinen

meeting tHe plAstics cHAllenge
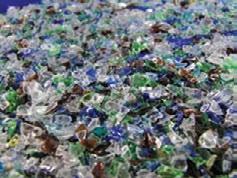
Plastics recycling has been a hot topic for some time and is becoming more prominent with every passing day. German company STF Maschinen- und Anlagenbau GmbH is an expert in this field - with a proven track record of recycling plant installed around the globe and decades of plastics recycling development. Romana Moares spoke to CEO Maximilian Söllner to find out more.
STF Maschinen- und Anlagenbau GmbH is part of the STF Group and, together with its sister companies STF Recycling GmbH and STF Thermoform-Folien GmbH, offers a holistic solution to plastics recycling. The STF Group is a specialist in PET recycling and production of recycling machinery and plants.
“The STF Group consists of three businesses – STF ThermoformFolien, today the smallest, is the founding company of the Group that my father established in 1980. The other two are STF Recycling focused on plastic waste processing, and STF Maschinen- und Anlagenbau, designing and producing plant and equipment for the sector,” Mr Söllner explained. “STF is a fully family-owned business, run by the second generation now but my father is still leading the R&D department.”
The company is headquartered in Aicha in southern Germany, where its operational capability is also located, including the polypropylene film extrusion facility, the recycling machinery construction, the Group’s engineering capability as well as the PET bottles recycling and granulation facility. “We have also three other sites for PET bottles recycling - in southern Germany towards Regensburg, in Eastern Germany and the newest one, commissioned just a few months ago, in Pilsen, Czech Republic,” Mr Söllner noted.

PeT processed
Today, STF Recycling GmbH is one of Europe’s largest recyclers and annually processes 130,000 tonnes of recyclable PET bottles. “In summary, recycling machinery is our main product. We focus on the PET bottle market as this is where we have the most experience and expertise,” Mr Söllner affirmed.
PET packaging is accumulating in increasing quantities not only in the form of beverage bottles but also as containers for cosmetics and detergents, pharmaceuticals or technical products, which hints at a
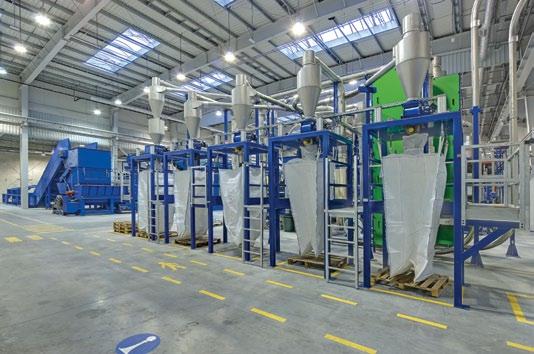
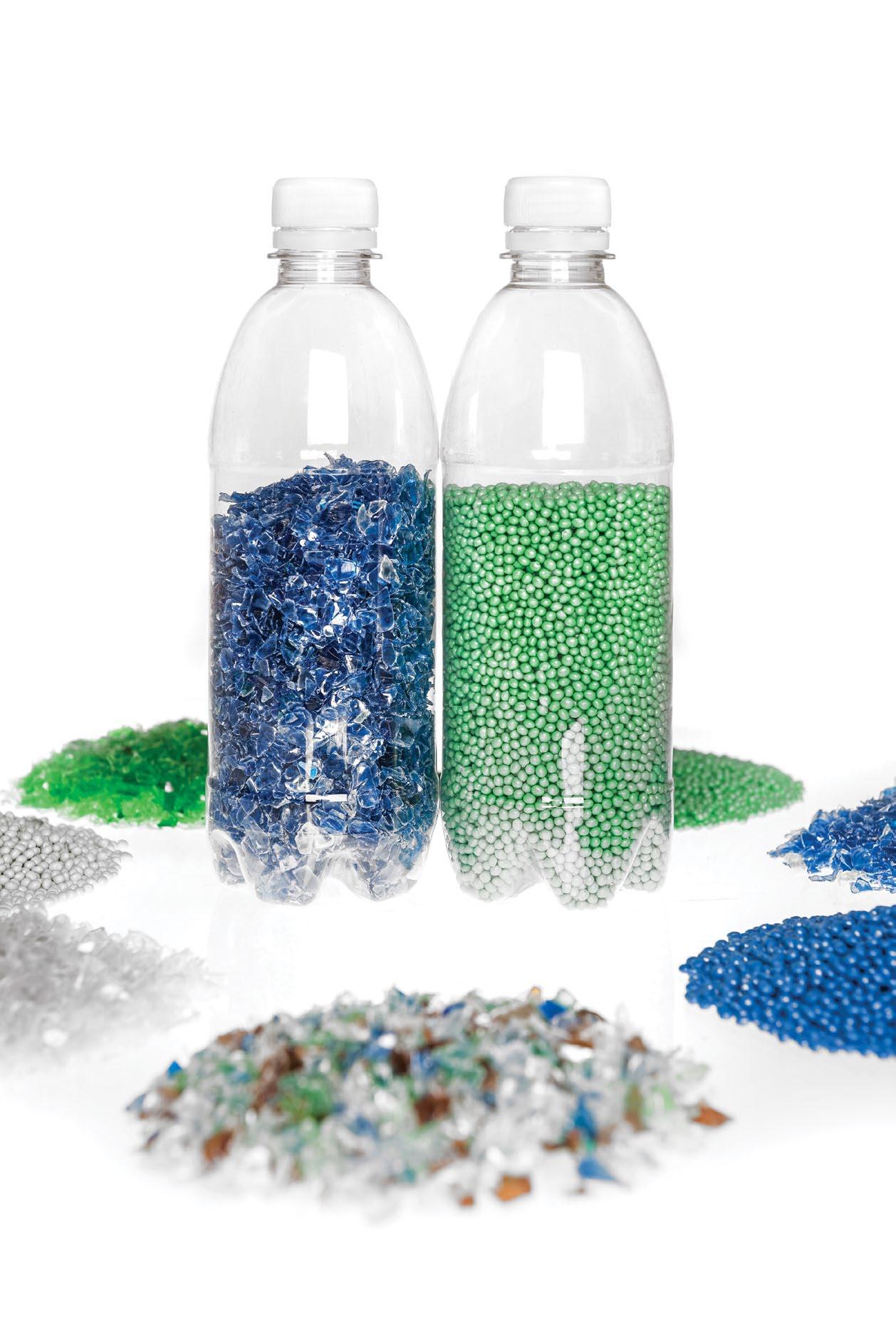
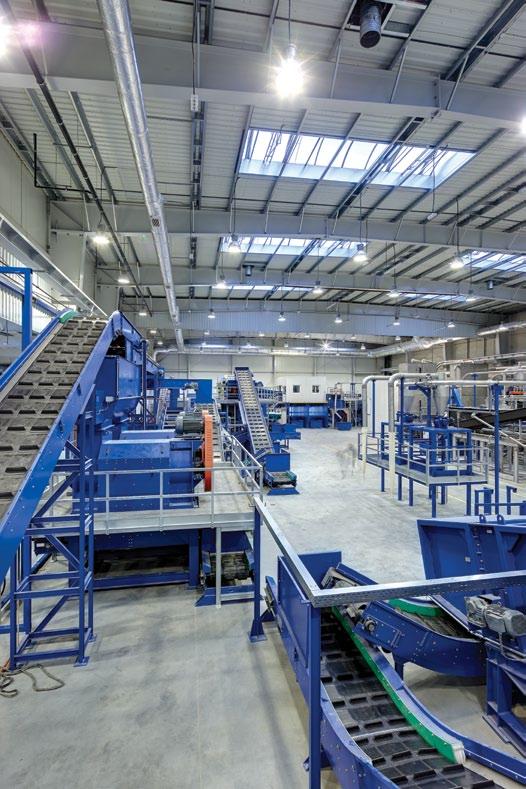
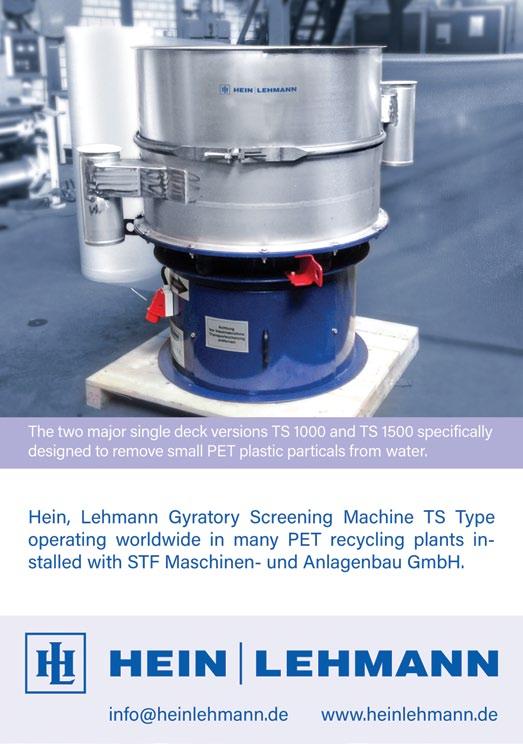
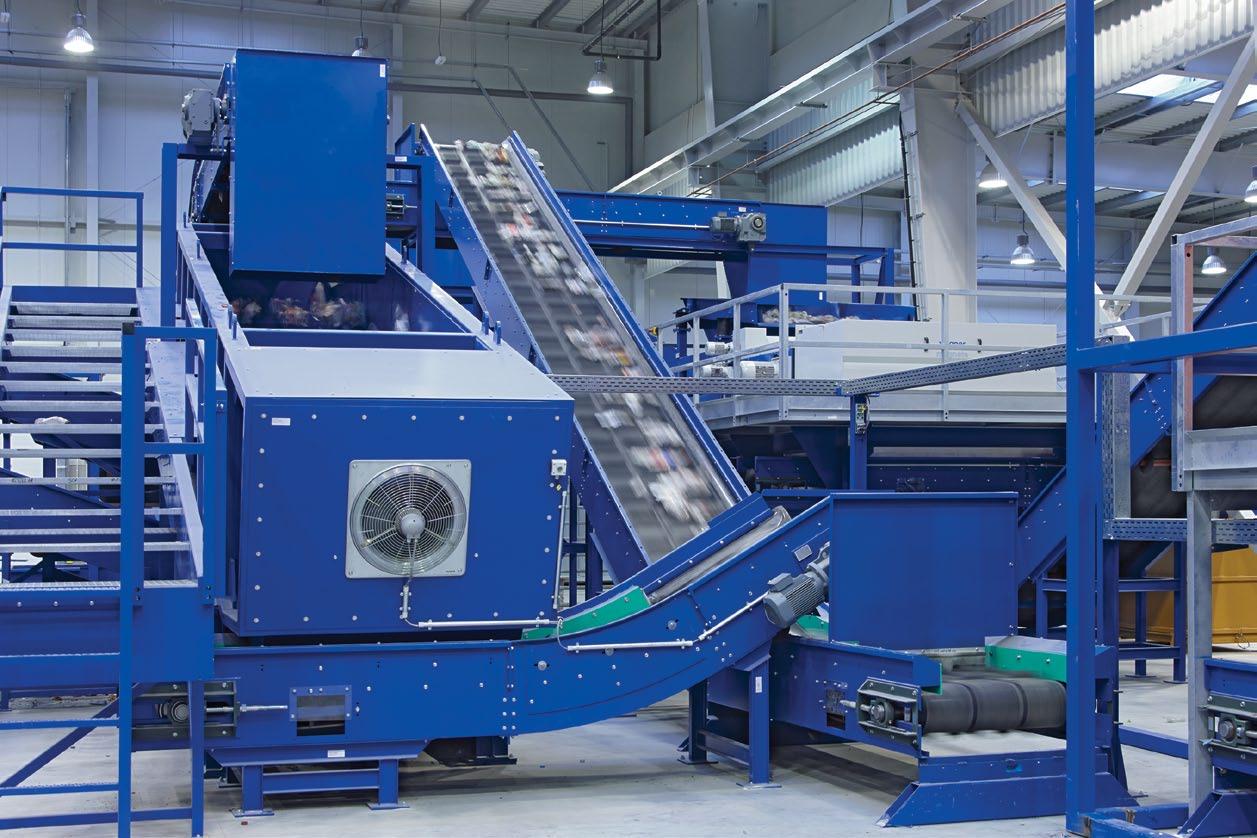
growing recycling market. “We have delivered and installed over 75 plants all over the world, and our recycling lines are running in North and South America as well as in Asia, particularly in Japan and India, which is a highly promising market,” the CEO pointed out. “At the same time, around 70-80 per cent of PET bottles in Germany are recycled on our equipment. Germany is the strongest market for PET recycling at the moment, with a very good collection and infrastructure system. I predict that the next few years, half of our machines will be installed in Europe, with the other half sold to global markets.”
The undeniable fact is that despite current negative media coverage, plastics are here to stay. They still represent the best material for food packaging for example, significantly reducing food wastage and increasing hygiene standards. Therefore, rather than reduce their use, focus will increasingly be on their recycling.
“Even though plastics recycling - unlike metal recycling - may not be that interesting from the economic point of view as the margins are small, the market will inevitably grow,” affirmed Mr. Söllner.
Quality and performance
The company’s R&D efforts are now focused on achieving high quality in PET Tray recycling. As some packaging materials consist of multilayer plastics, such as meat packaging, the recyclability is limited. “High quality has always been our creed so this is an area we are focusing on now - we have the technology, we are almost there. The plan is to have another facility recycling 30 thousand tons of this type of plastics into high quality materials,” Mr Söllner remarked.
“The second direction of our R&D is to further improve the bottle recycling. The quality is already very high, we are now focusing on increasing the yield. Also, we want to achieve good quality of other waste streams - it is not just PET bottles but also PET caps, labels and other such plastics,” he noted, explaining that the recycled material is mostly used for industrial use, mostly injection moulding.
As mentioned earlier, the potential is huge. ‘Made in Germany’ is a sought-after brand guaranteeing top quality and performance, well justifying the higher acquisition cost. “Of course there are cheaper manufacturers in Asia but what has been changing in the last few years is that global brand owners, such as Coca Cola, Pepsi or Procter & Gamble, put increased emphasis on waste sorting and recycling in the same, consistent top quality all over the world. A quality that European manufacturers can still provide better that their Chinese counterparts.”
As for STF’s plans for the future, Mr. Söllner summarised them in one word - expansion. “My idea is not so much to expand geographically but to focus on different types of plastic packaging and grow this business. At the moment, we recycle 130,000 tons of plastics every year. We want to get to 200,000 in the next five years. With our solid experience, we are ready to meet the challenge.” n
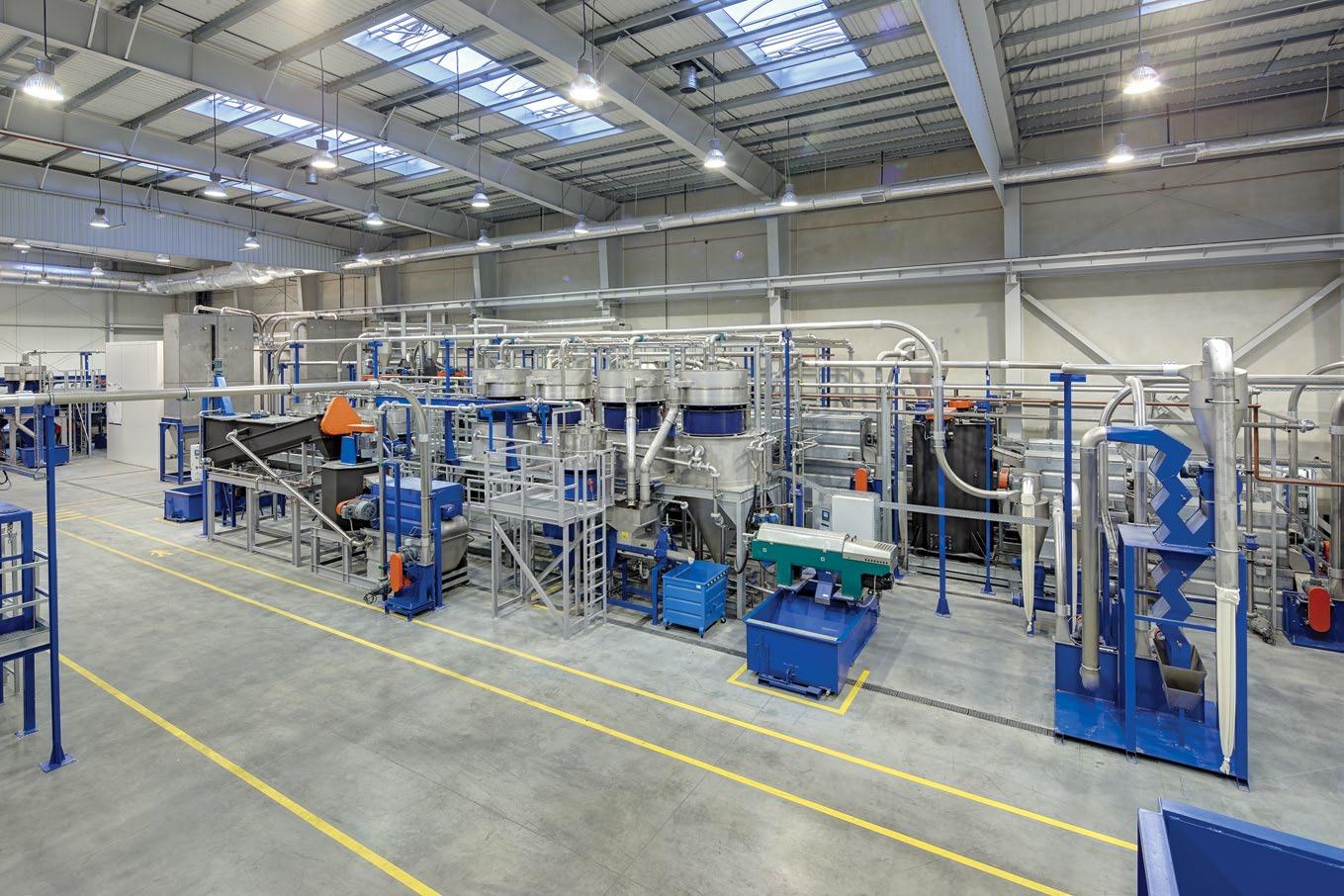