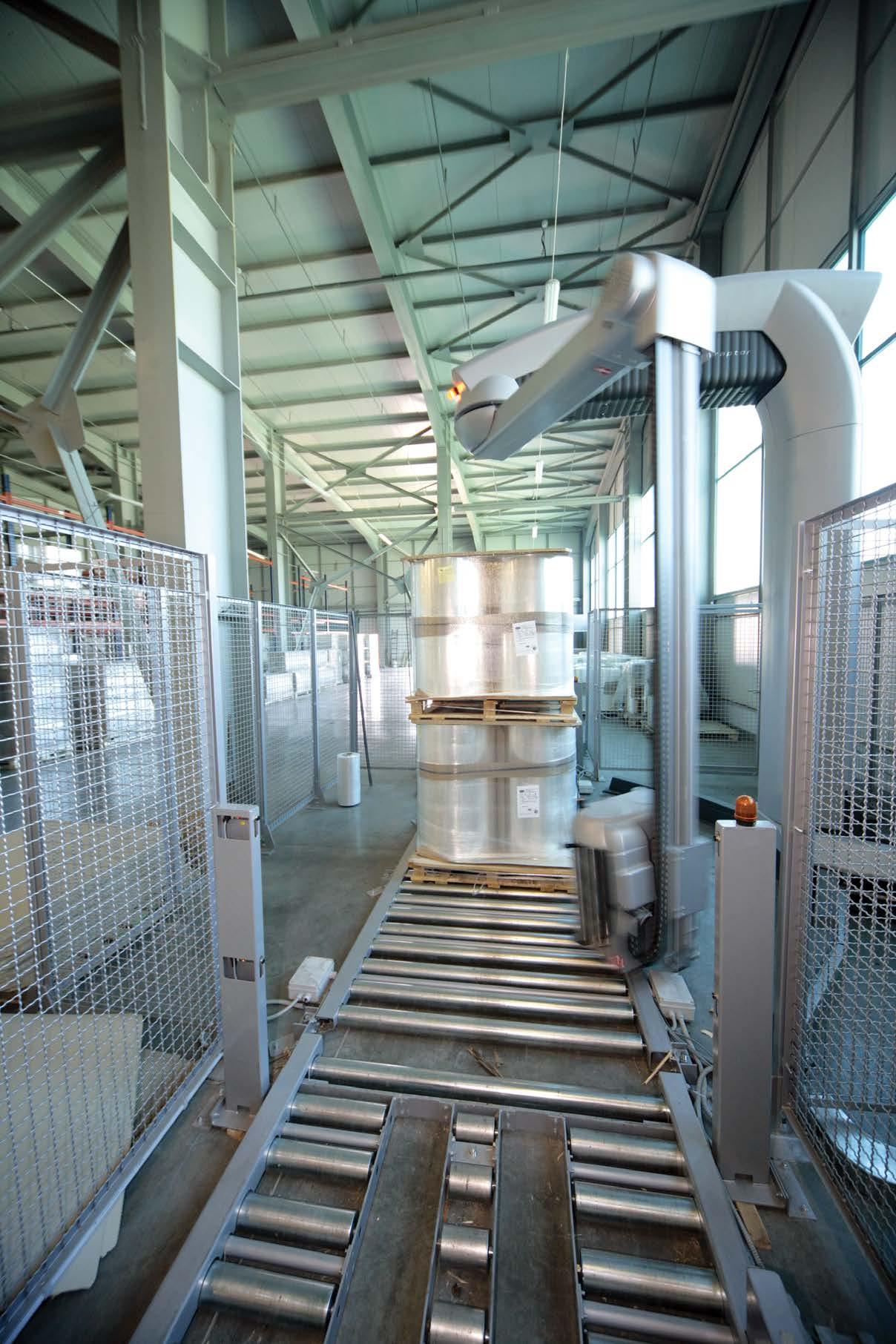
5 minute read
Big bopper Plastchim-T
BIG BOPPER
Plastchim-T is a packaging success story and a company that continues to lead the field in sustainability, quality and output. Working in close cooperation with Brueckner of Germany it has invested in their record-breaking 10.4m wide high-speed BOPP lines. Philip Yorke reports on the impact of Plastchim’s latest high-tech acquisitions.


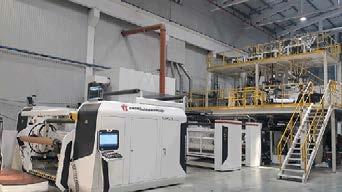
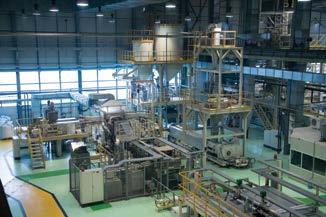
Plastchim-T is a leading, privately owned European manufacturer of biaxially-orientated polypropylene films (BOPP), cast polypropylene films (CPP) and a diverse range of flexible packaging products. Founded in Bulgaria more than 50 years ago, the company has grown from a domestic orientated business to a pan-European leader in packaging and related industries. Today Plastchim-T has two state-of-the-art production facilities in Bulgaria and employs over 1,000 people.
The company operates two distinct business divisions: Packaging Films and Flexible Packages Production. Both of its production facilities are located conveniently close to the country’s borders in Alaskovo and Tervil. The two modern plants occupy a combined total of more than 150,000 square metres of production space. Current annual production capacity is around 60,000 tonnes of BOPP films, 6,000 tons of CPP films and 2,500 tons of PE films. This is in addition to a further 10,000 tons of woven PP packaging. The company’s goal is to provide its customers and partners with the highest possible quality products and services, and to offer valuable business solutions to the packaging industry.
Breaking all records
A new BOPP film line recently launched by Plastchim-T has broken all international records for speed and output volumes. The latest 10.4 metre wide film stretching line has already exceeded its capacity speed mark of 600 metres a minute for the first time ever. This state-of-the-art equipment also surpassed the existing film orienting hourly production record of 7,600 kilograms per hour, according to the German manufacturer Brueckner Maschinenbau. The advanced high-speed line also chalked up another record with its specific energy consumption per kilogram of film produced, thereby achieving the lowest ever measured.
“Our new Brueckner BOPP plant was intended as an investment for the future. We had planned to realise speeds of 600 metres a minute sometime in the next two years, however, our team and the specialists from Brueckner have reached that milestone in much less time. Of course we are very pleased about that, not just for the sake of speed and efficiency, but because of the associated unique energy and production optimisation of the system” commented Plastchim-T’s owner, Aydan Faik.
This new line will also be capable of producing high quality special foils, such as those required for metallisation, at speeds of more than 500 metres per minute. Plastchim-T already runs other Brueckner lines with working widths of between 4.2 and 10.4 metres, which allows it to react flexibly to changing market requirements. This means that it can offer different film types in smaller or larger quantities, even with the shortest delivery times being demanded. In addition, Plastchim-T has also installed a residual heat recovery system in order to capture the heat generated from its compressor cooling system to warm its raw materials warehouse.
Focus on the environment
Platchim-T has been leading the field in Bulgaria for many years with its commitment to protecting the environment and reducing global warming. The company is dedicated to conducting its business in a manner that will protect the environment and it adheres to all the relevant legal requirements and environmental management practices.
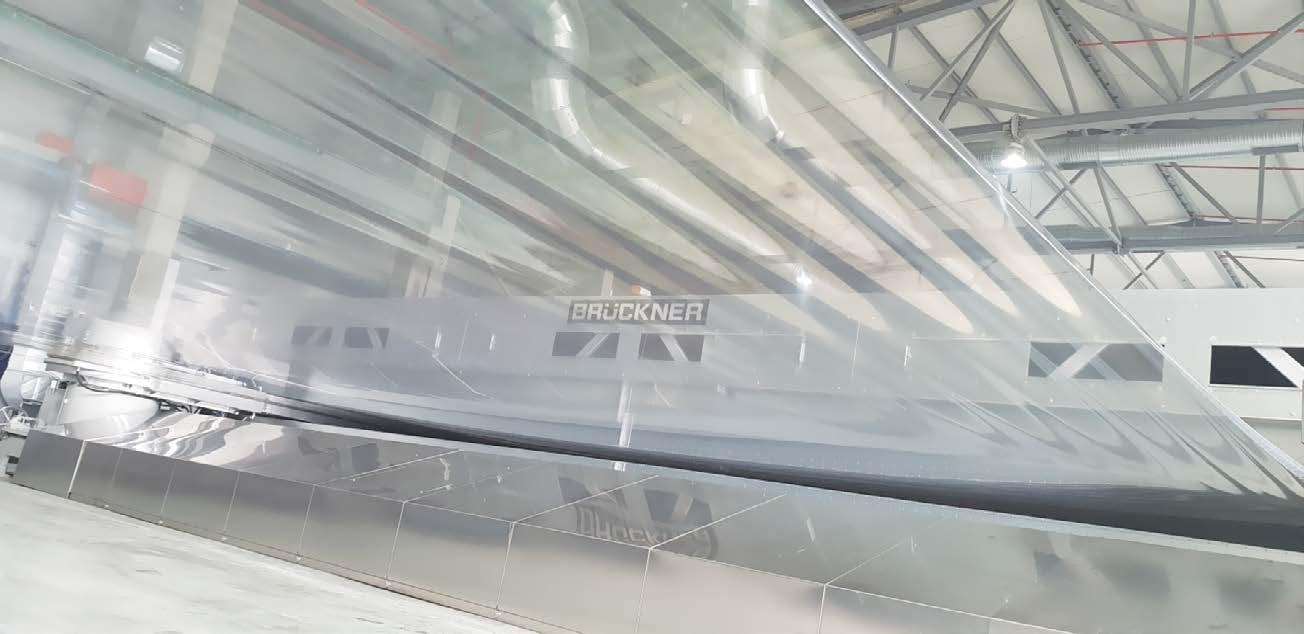
In order to reduce its overall environmental impact and use of resources, the company continuously reviews and improves its diverse operations. Plastchim-T has implemented pollution prevention practices that are controlled by clear action planning, as well as risk assessments and a continuous programme of staff training. As a result, all PlastchimT’s staff are fully aware of their environmental responsibilities.
Wherever possible, the company also minimises the waste created by its activities by promoting practices such as recycling and energy saving procedures. The waste disposal is organised in accordance with the best industrial practices.
To further underscore the company’s commitment to protect the environment a specialist recycling company: Next Generation Recycling Maschinen GmbH (NGR) produces specialised machinery for Plastchim-T for the reprocessing of thermoplastic waste back into high-value raw materials. With NGR’s “One-Step” technology, a patented cutter-feeder-extruder combination, there is no additional pre-cutting necessary, not even for difficult-to-cut materials. As a result, reprocessing costs are low and manpower requirements reduced to a minimum.
Furthermore, due to the gentle cutting in the shredder and extrusion process, which ensures minimal degradation, NGR’s recycled high-quality pellets are guaranteed, and as a leading producer of BOPP film in Europe, Plastchim-T is proud of its sustainability record having been operating NGR recycling systems for many years.
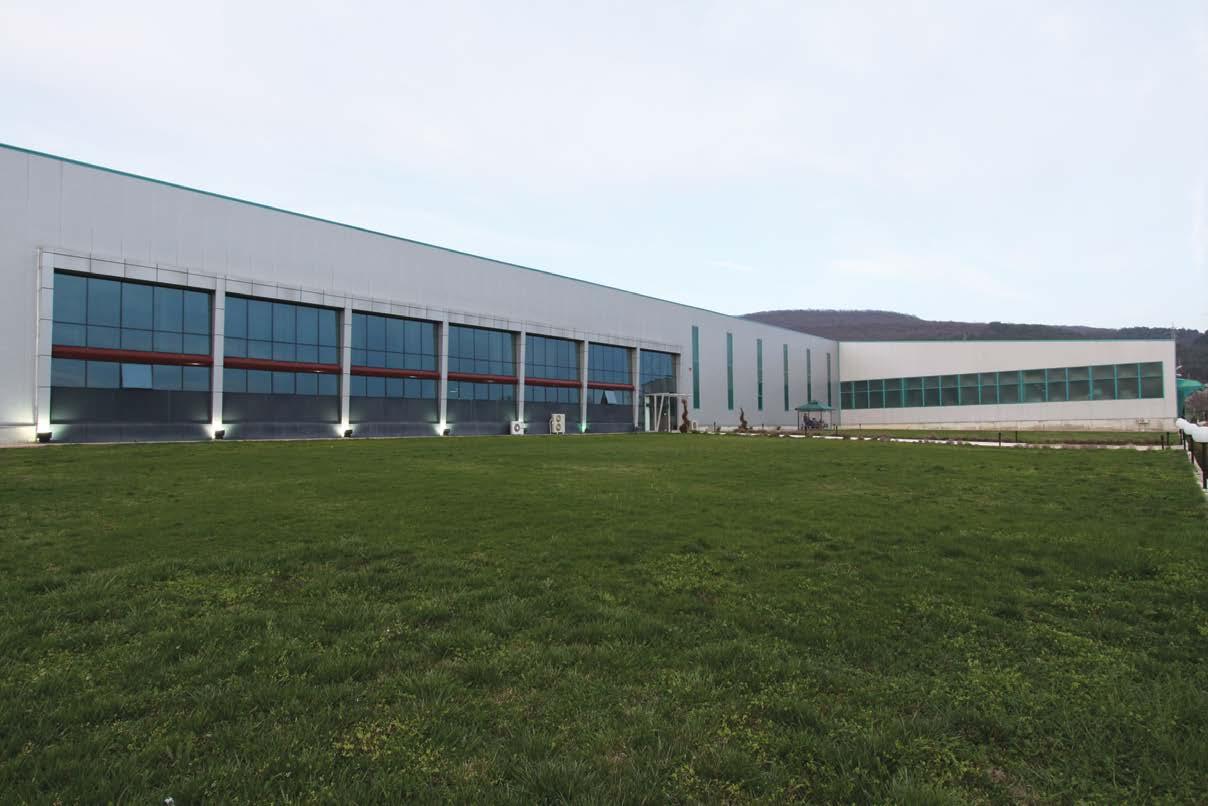
Bags of flexibility
When it comes to flexible packaging and the production of industrial bags, Plastchim-T is the manufacturer of choice. It offers a broad range of high quality bags that provide unrivalled strength and flexibility. Its small sewn bags are produced from Polypropylene (PP) circular woven fabric with a capacity from 5 to 100 kilograms. They can also be supplied coated or uncoated as well as with or without a gusset and with or without an inner polyethylene bag with an open top or ventile finish.
The printing of its small bags can be done on one or two sides and in up to six colours. These bags are ideal for the packaging of fruit and vegetables. Platchim-T’s ‘Block bottom bags’ are made of a coated fabric, with glued bottom plates. After filling, the shape of the bag is closer to Parallel-piped, and this can offer an advantage in some cases to sewn bags. n
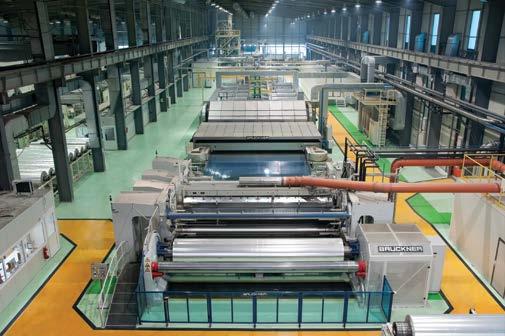
For further details of Plastchim-T’s innovative packaging products and services visit: www.plastchim-t.com
Windmöller & Hölscher Machinery – competence in woven sacks
For 40 years Windmöller & Hölscher has been developing and manufacturing machinery for the production of flexible packaging made from woven PP.
In 2005 the company began to complete the woven PP product portfolio under the brand BSW. The successful brand BSW was renamed in 2017 and now continues under the new name of Windmöller & Hölscher Machinery.
Highly skilled employees design and produce tape stretching lines, circular looms, extrusion coating, fabric printing and woven sack converting machinery.
Plastchim as a reliable European partner have been operating W&H machines successfully for many years.
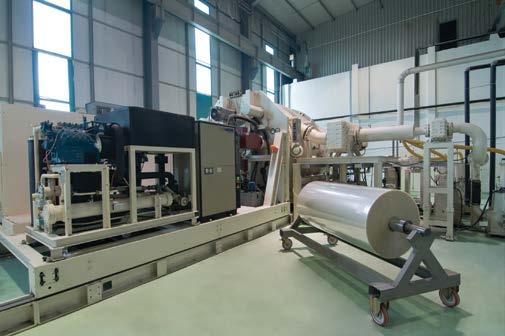
