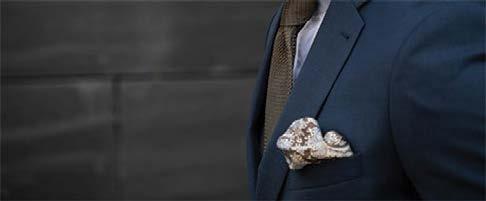
42 minute read
Setting new standards in style Yünsa
SETTING NEW STANDARDS IN STYLE
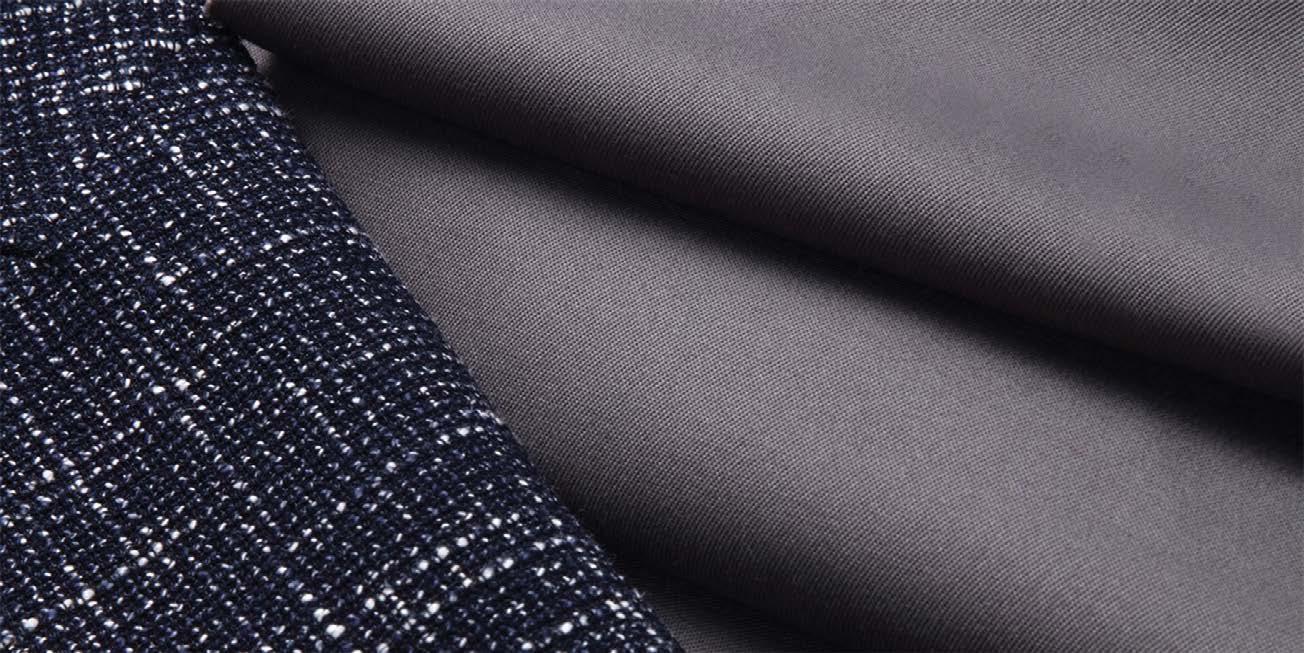
Yünsa is one of the world’s biggest producers of premier worsted fabrics and the largest in Europe. The company continues to set new standards in quality, style and diversity with its worsted yarns blended with cashmere, lycra, cotton and linen, as Philip Yorke reports.

Founded in 1973, Yünsa is the largest integrated high-segment worsted wool fabric manufacturer in Europe and one of the five biggest in the world. When Yünsa started producing worsted fabrics in 1973 it focused on the manufacture of men’s fabrics and later in 1998, it added women’s fabrics, according to information supplied to Industry Europe.
Yünsa primarily manufactures 100 per cent worsted fabric, as well as worsted fabrics blended with cashmere, lycra, viscose, cotton and linen. In addition to 4,500 tonnes of worsted yarn, Yünsa produces and uses its own yarn that has 12.5 million metres of worsted capacity per year.
Today Yünsa has customers in more than 50 different countries, with Germany remaining the company’s biggest market. In addition, it is the leading fabric supplier to some of the world’s most famous brands. The company was listed on the Turkish stock exchange almost 30 years ago.
Strengthening exports
Yünsa, the biggest integrated high segment worsted fabric manufacturer of Turkey and Europe, last year broke all previous records achieving revenues of more than 42 million euros. The company recorded an increase in sales of 19 per cent, according to a recent

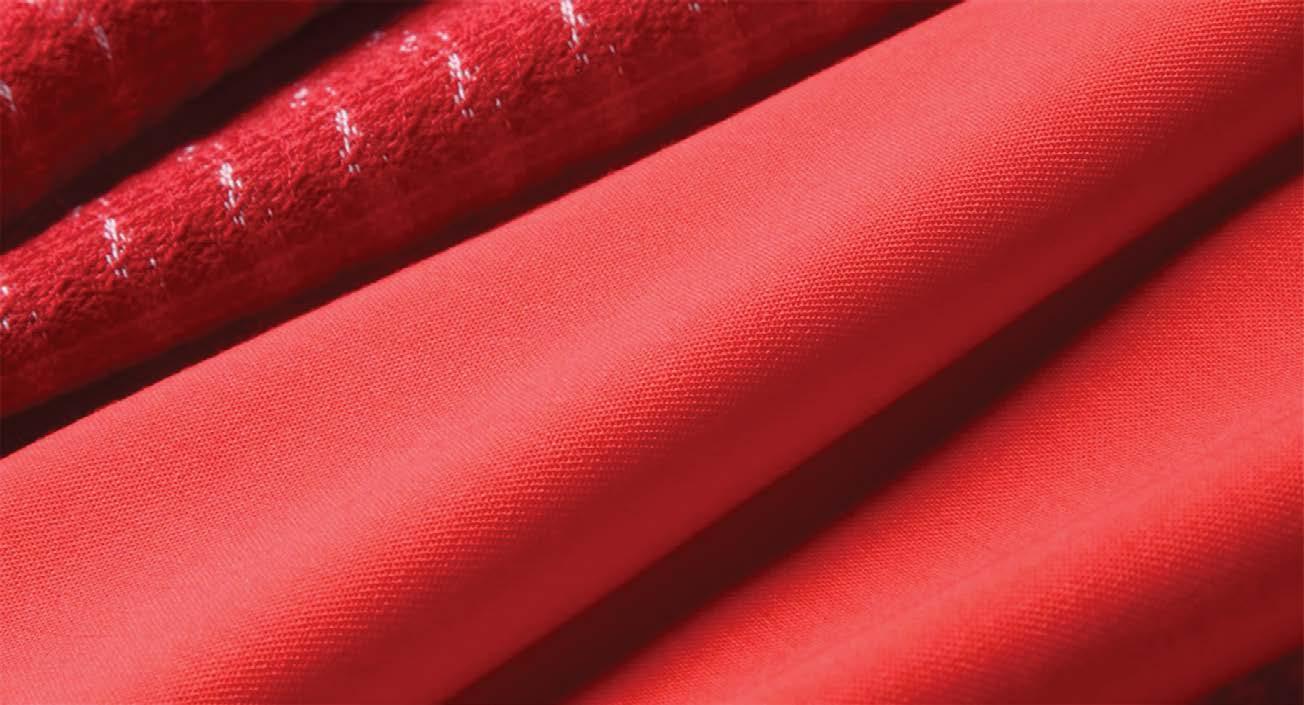
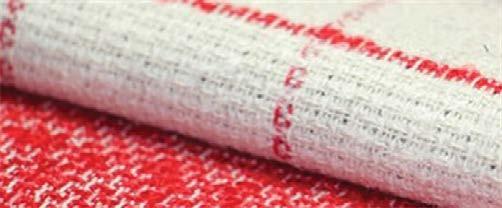
report. The company has also been included in the list of the 100 most valuable Turkish brands by Brand Finance.
“Today, we are exporting to more countries, and offering more than 400 products to our customers. In Turkey, we represent 70 per cent of the global exports in our sector. Exports consist of 2/3 of our annual turnover and we supply over 5 per cent of the world’s total worsted market. In the last 5 years, we exported products worth more than €42 million to the international market. Today, we are one of the five largest high-segment worsted fabric exporters in the world and we are doing business with many international brands,” said Nuri Refik Duzgoren, general manager of Yünsa.
Yünsa has continued to strengthen its position in export sales with its distinctive brand value. In a newly released survey by the international brand rating agency, Brand Finance, it rated the brands operating in Turkey in the automotive, finance, energy and many other industries. The report reveals that Yünsa improved its brand strength from rating from ‘BBB’ to ‘A’ and has been since registered as one of the most valuable brands in Turkey
“The textile sector is a challenging one compared to the other sectors in Turkey and in the world in terms of changing dynamics, production process and the supply of raw materials. We produce high-segment products in this sector. We manage our financial and operational processes with the right strategy. We have a large customer portfolio including countless global brands. We are successful in exports, which is an important factor that in turn increases our brand value,” added Duzgoren.
Four-season success
Recently, Yünsa launched a range of new fabrics suitable for all four seasons. With volatile seasonal changes, Yünsa fabrics can be a saviour, with its breathing and humidity controlling features. The col-
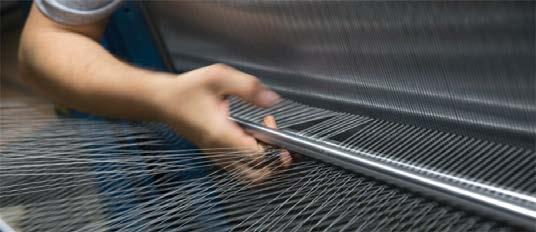
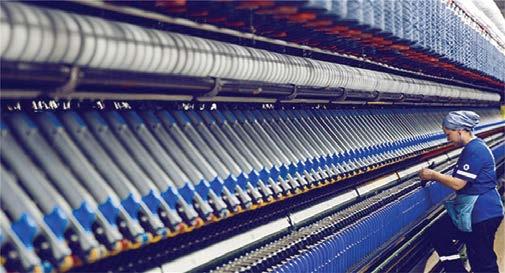
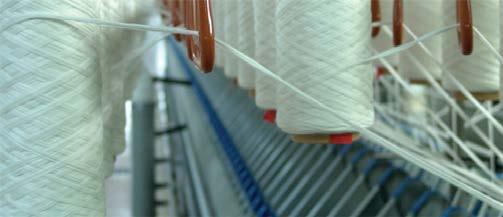
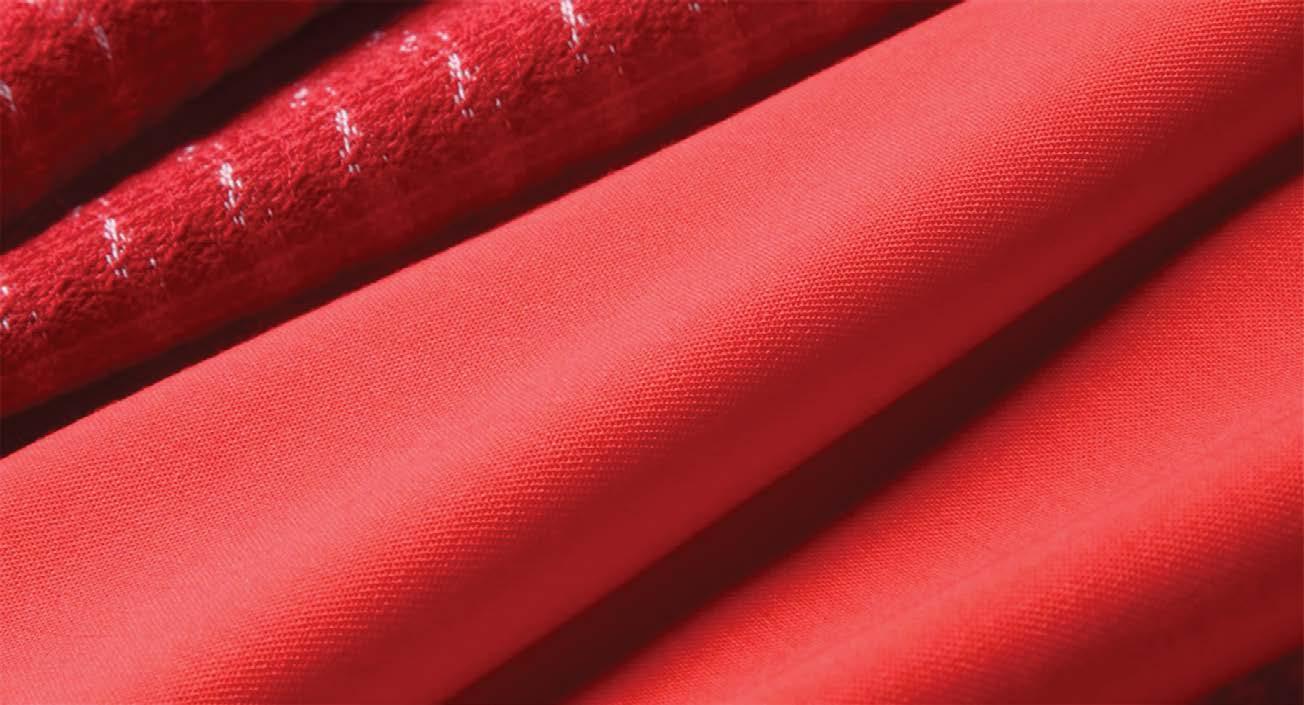

lection is made with blending wool, which is a natural and sustainable raw material, with linen, silk, and cashmere.
In the autumn season, one can see a minimal casual street style with blazer jackets and chino trousers that can be worn with knitwear during the time when the winds of change are felt during the autumn months. At other times when the weather is unpredictable, the items made of wool-blended fabrics have the ability to keep humidity control in balance and allow customers to enjoy the season in comfort. The casual fabrics from Yünsa Laboratory, in which the cotton is glossed with linen and lycra, will provide many benefits to consumers, especially in assisting in the layering process, the company said.
In the autumn when weather conditions are tough, cashmere clothes are one of the most desirable. People can choose to wear trench coats that can be worn with a shirt, pullover or blazer jacket. A calm, dignified style can be seen with trench coats with narrow cuts or loose patterns, which can also help individuals adapt to the effects of the changeable autumn season. For protection from sever or rainy weather, trench coats produced from the water-repellent fabrics of Yünsa are the most sought-after.
When the temperatures start to rise above the seasonal norms during summer, the most preferred items are shorts and basic t-shirts. When choosing, the issue that should be considered is whether the fabric is breathing or not. With its breathable and flexible structure, the YünsaLab collection with linen-cotton blend that adjusts the body-environment relationship is the best way to make the most of this comfortable combination by preventing overheating and sweating in humid summer weather.
Growing product portfolio
Today Yünsa is the apparel fabric powerhouse of Europe and is turning its sights towards upholstery, specifically wool and wool blends combinations. The company produces 14 million metres of wool fabrics a year and is a key supplier of mens’ suits to top brands such as Hugo Boss and Zara. Yünsa is based in the Levent district of Istanbul. The new home collections were showcased for the first time recently, although the upholstery line has been on the market for the past two years and has been quietly on display at Villa Berlusconi during Proposte.
“We’re focused on contract wool fabrics with 50,000 double rubs but we have wool for residential use also,” says Ersin Samsa, upholstery sales manager. The range is priced 10-18 euros per metre. We are also able to make a Zirpro finish that enables our products to pass flame tests like BS5852 – 0 (Cigarette) and 1 (Match) tests for use in domestic environments. n
For further details of Yünsa’s latest innovative worsted fabrics and stylish seasonal collections visit: www.yunsa.com
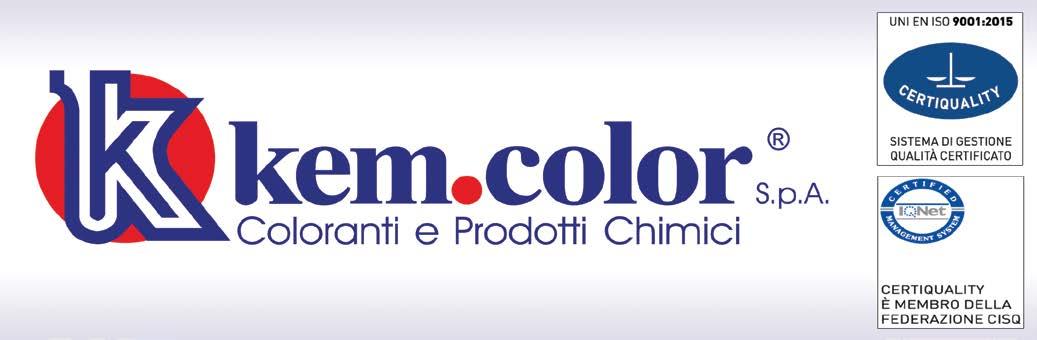
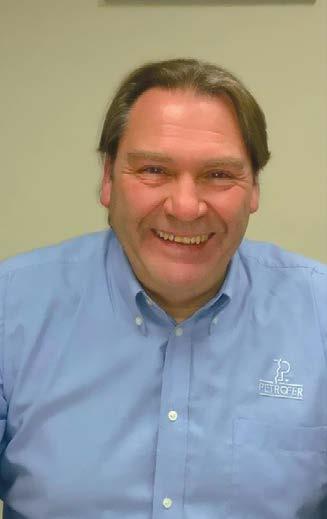
Stuart Gregory, the Managing Director of Petrofer UK

LUBRICATING THE LUBRICATING THE WHEELS OF GROWTH WHEELS OF GROWTH
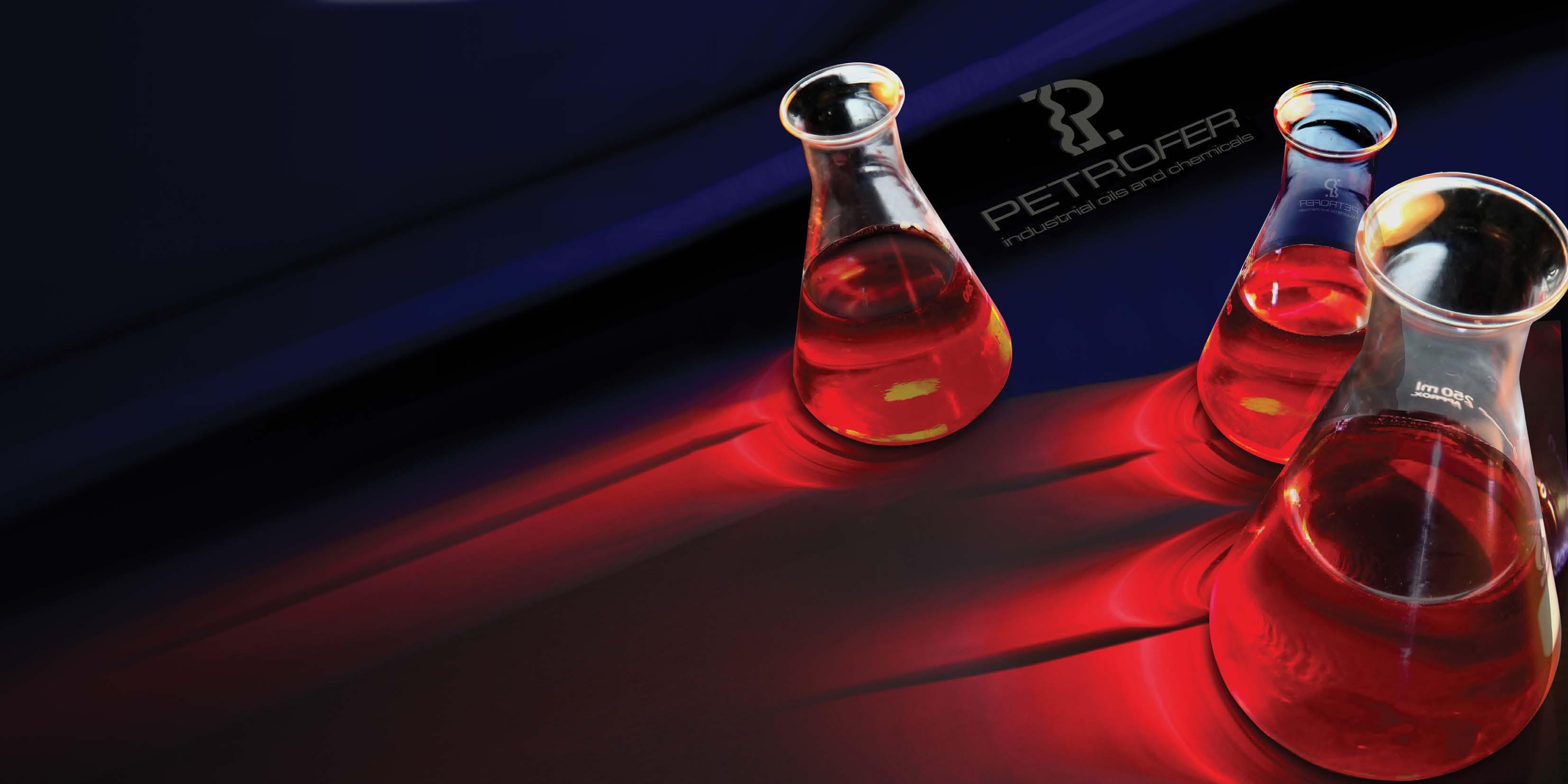
PETROFER UK, a wholly owned subsidiary of PETROFER Germany, one of the world’s leading companies for industrial lubricants, oils and specialised fluids, is set to embrace emerging sector changes. Stuart Gregory, the Managing Director of Petrofer UK and a member of the Global Executive Committee, spoke to Romana Moares about the latest developments and upcoming challenges and opportunities.
Established in 1948 in the northern German city of Hildesheim, PETROFER has developed into a leading company in its sector, offering a combination of chemical products, services, and technical expertise in almost 50 countries throughout the world, supported by 14 manufacturing sites. Combining tradition and vision, this privately owned company builds on innovation, quality, expertise and employee dedication.
PETROFER’s portfolio of process fluids and products is divided into ten distinctive product groups; these are used in applications such as metal forming, forging, die-casting, pressing, metal cutting, cleaning, hydraulics, general lubrication, heat treatment and corrosion prevention. All of the products exceed current environmental, H&S and legislative requirements.
Embracing change
Mr Gregory, who has been with the company for 24 years, and is also the Technical Co-ordinator for Japanese Business in Europe, as well as the President of the UK Die Casting Society and the ViceChairman of UK Cast Metals Federation, explained that in addition to its sales team, the UK subsidiary has service engineers covering the whole of the UK along with a laboratory providing regular fluid analyses on the majority of our products to all our customers.
“Our core business is very much market led,” he noted. “Different countries have different sectors which are in focus; for example, Germany is a very much an automotive led country, while Turkey, on the other hand, is perceived as a metal processor or a component supplier. Our product offering reflects local needs and local demand. However, our global market perspective generally focuses on hot metal industries around the automotive sector and its supply chain.”
He further acknowledged that the company is ready to embrace market developments. “The biggest challenge that we see in the formulated chemistry industry is the huge change in the automotive technology worldwide in terms of electric drives, lower weight, new materials and new techniques. The market is further affected by factors such as the REACH registration of chemicals, restriction of certain products as well as the geopolitical situation in terms of
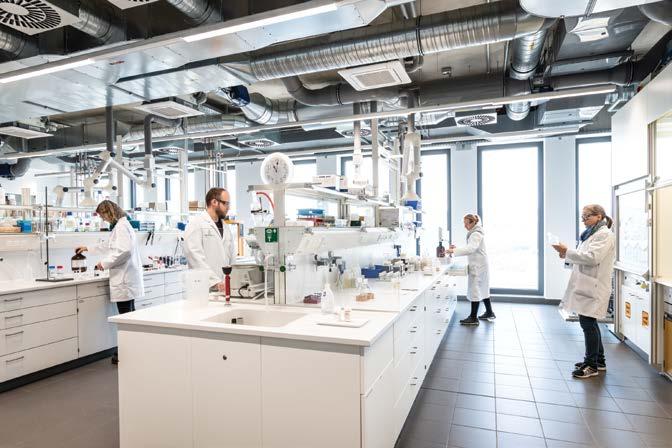
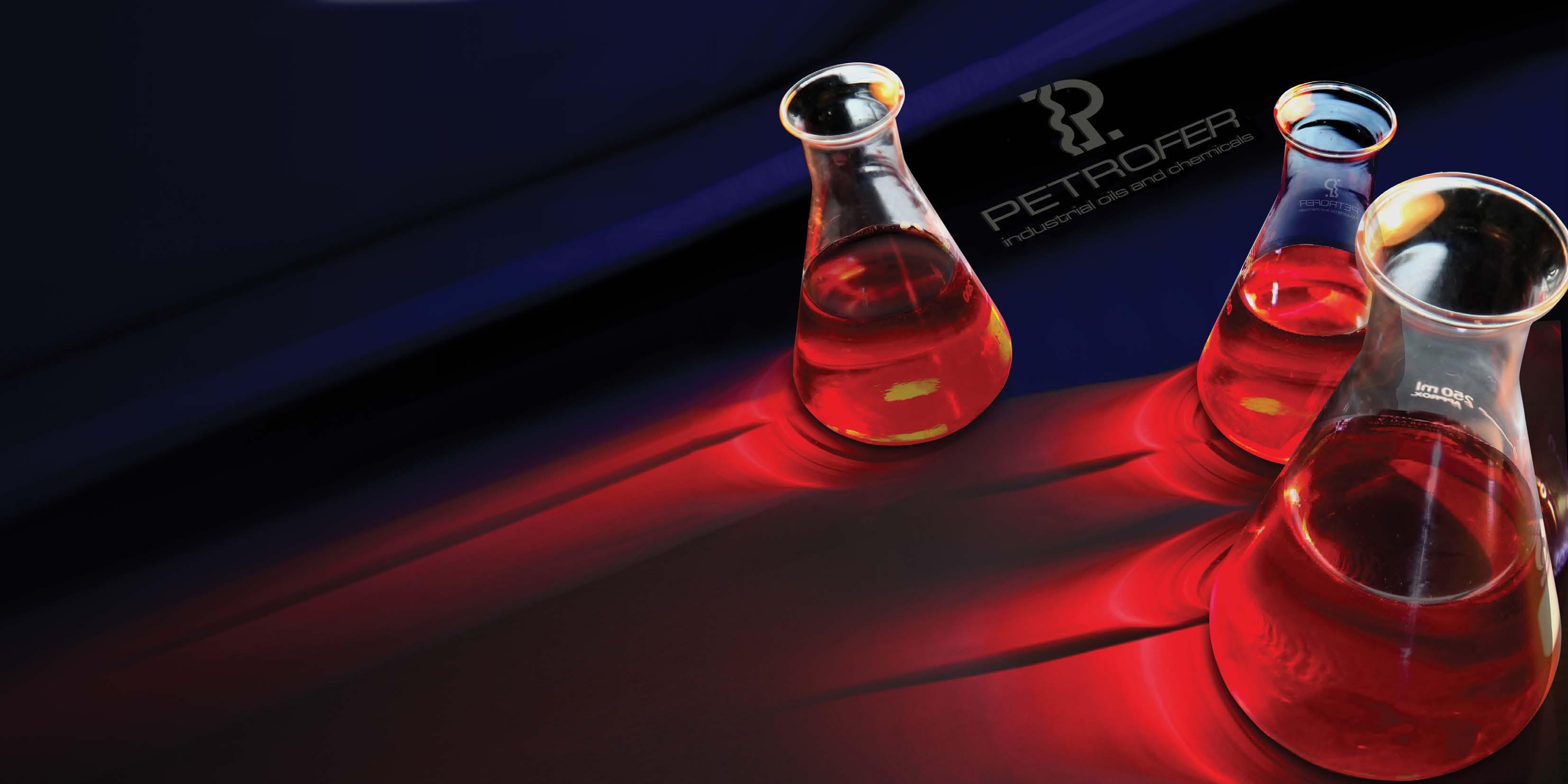
availability of raw materials. So there are several winds hitting the ship, so to speak – a changing society, changing raw material availability and changing legislation.”
“Responding to the new challenges in the die-casting and metal forming processes, we have developed a whole range of new die-casting products that are very efficient, with minimum losses. They have been very well accepted in the marketplace,” Mr Gregory affirmed.

Ergon, Inc.
Ergon has been refining the definition of service since 1954 and is the world’s largest producer of naphthenic specialty products and second largest producer of bright stock. The company has earned the trust of customers in more than 90 countries around the world by offering reliable, consistent supply and products of the highest quality. With both naphthenic and paraffinic refineries and a global terminaling and distribution network, they are committed to meeting customer needs for solvency and viscosity. Ergon continues to invest in leading manufacturing practices, innovative service and global distribution, which is enhanced through relationships with suppliers such as Petrofer Chemie H.R. Fischer GmbH + Co. KG.
• World Largest Producer of Naphthenic Base Oils • Global Distribution Network • Regional Offices and Depots • Secured Raw Material Resources • Reliable, Consistent Base Oil Supplier
Learn more at ergoninternational.com. Sustainable chemistry
As one of the leading suppliers of quality products including industrial lubricants, chemicals and specialised fluids, PETROFER bears a high responsibility for people, nature and the environment. Certified according to ISO 9001 in the UK and ISO 14001 and ISO 50001 at the German manufacturing plant, the company is committed to remaining a preferred partner for quality products and services in the coming decades.
“With our sustainability claim, we strive for ecological, economic and social balance. Specifically, this means for our commercial actions: the conservation of natural resources, the avoidance of environmental pollution, the use of environmentally sound and energy efficient processes and the selection of suppliers according to quality and environmental aspects.”
“All of our facilities are run with environmental protection in mind. This is reflected in such things as chemical cleaners. With modern chemicals, these can achieve great performance with ambient temperatures, thus improving energy savings as well.”
Speaking about current trends, Mr Gregory acknowledged that just like in other sectors, the focus on sustainability is increasing in the chemicals sector. “We produce about 600 formulations
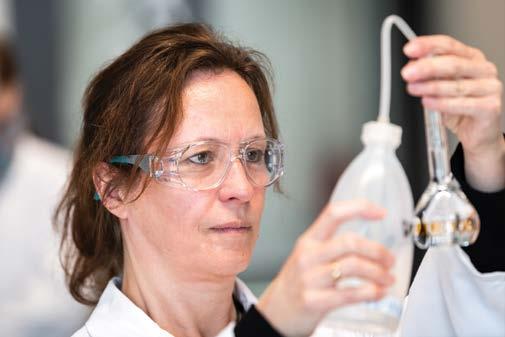
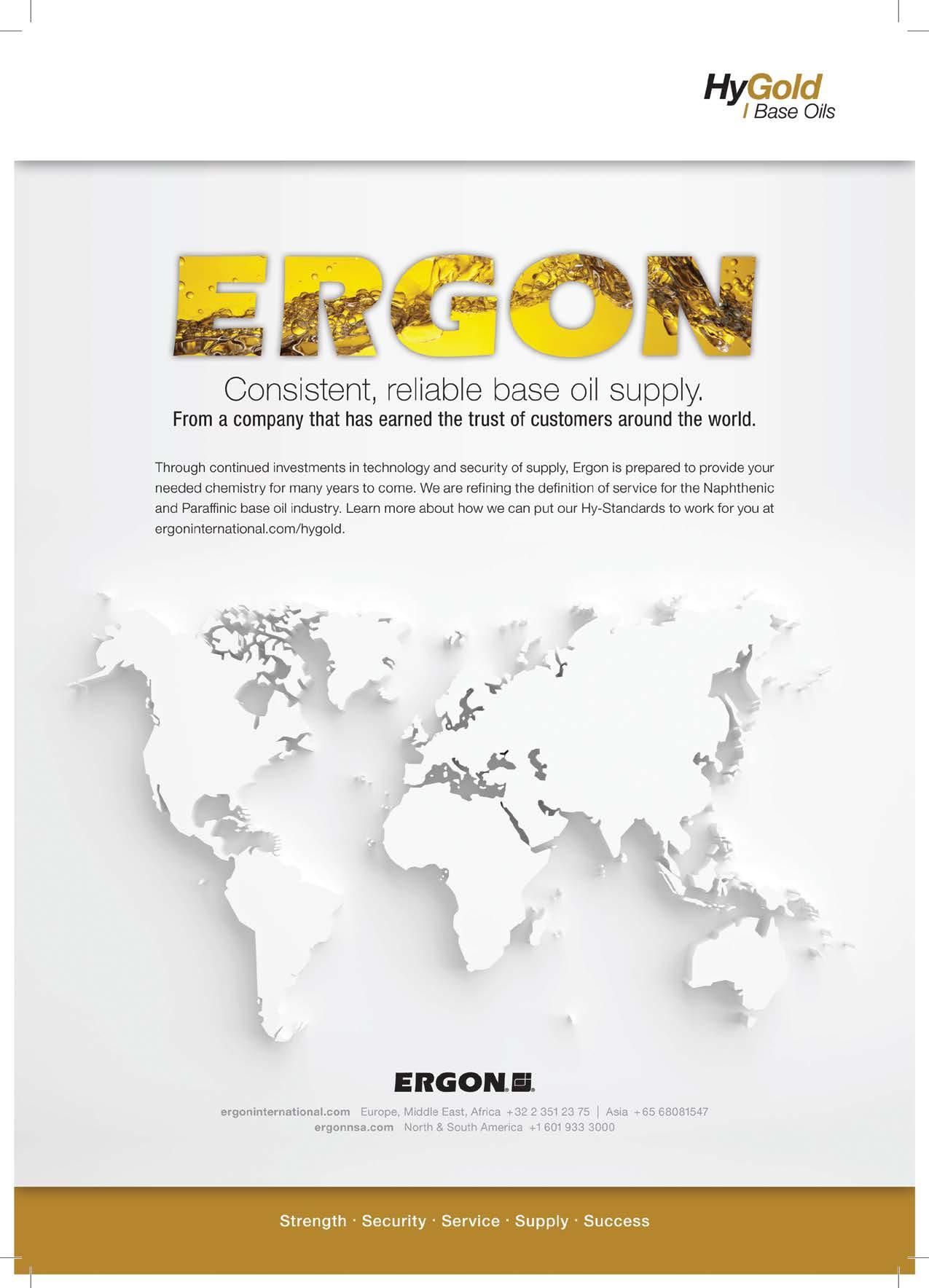
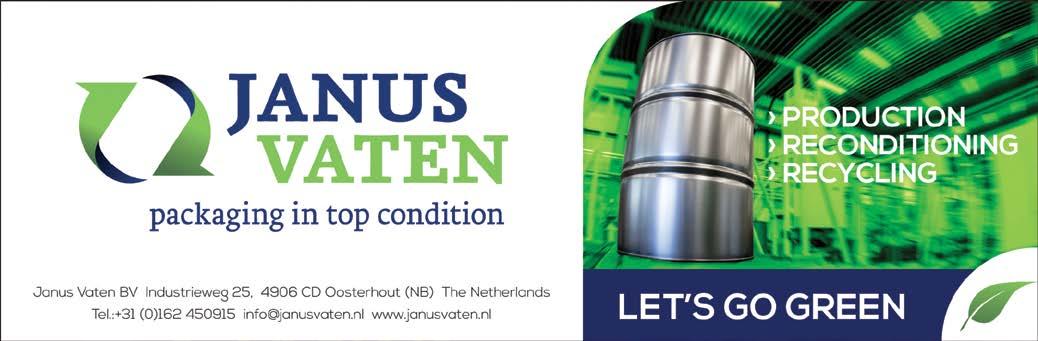
globally, and the main drive is to be part of sustainable chemistry for the future. Efforts are directed, in particular, at a reduction in disposal costs, i.e. towards products with longer life expectancy that are sustainable, commercially attractive and offer higher performance for emerging technologies, while reducing impact on the environment.”
Setting the benchmark
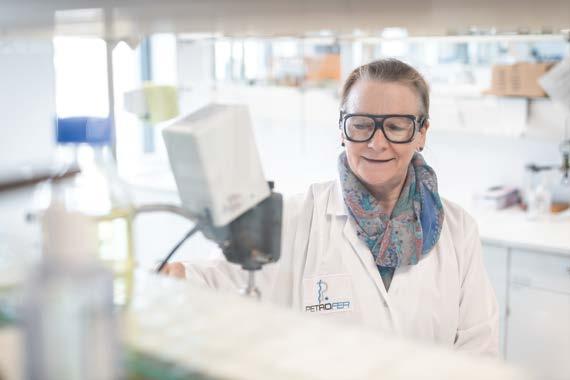
Today, just like in the past, PETROFER is committed to continuous improvement and technical advancement. The company is growing its global presence, and its research and development sets international innovative benchmarks and quality standards utilising unique know-how.
“Growth is supported on several fronts. We are building a new facility in China, have a new grease manufacturing facility in Turkey and are expanding our operation in India. We are also looking at building a new facility in Brazil. These expansion plans follow the developing economies in those countries. China, India, Turkey, Brazil, and also Mexico with its rising automotive industry are all high growth markets with substantial potential.”
He affirmed that PETROFER’s future is to move quickly with a rapidly changing world and adjust the product range to new technologies. “With new emission regulations looming, many countries are building smart, modern and highly advanced super factories. We need to monitor these developments and match our products to future demand, to continue to stay at the forefront of our sector.” Our company motto reflects this; “We listen, We develop, We deliver”. n
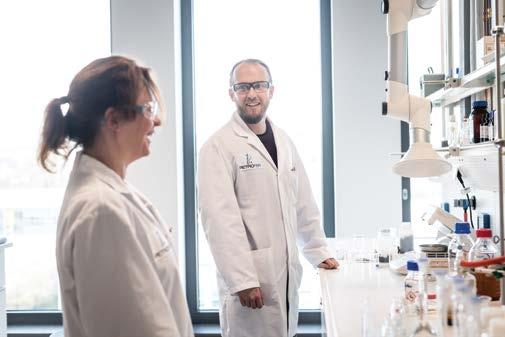
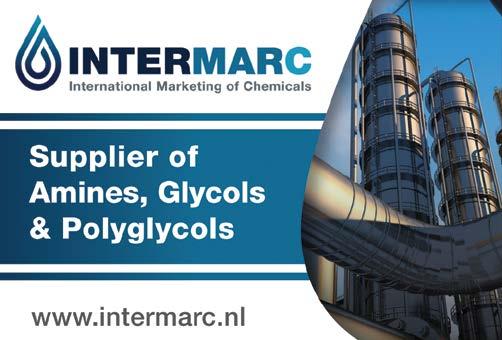

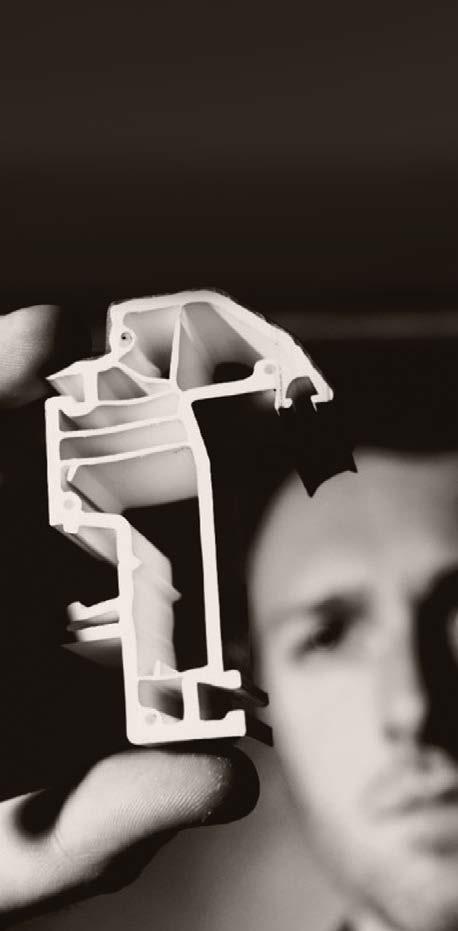
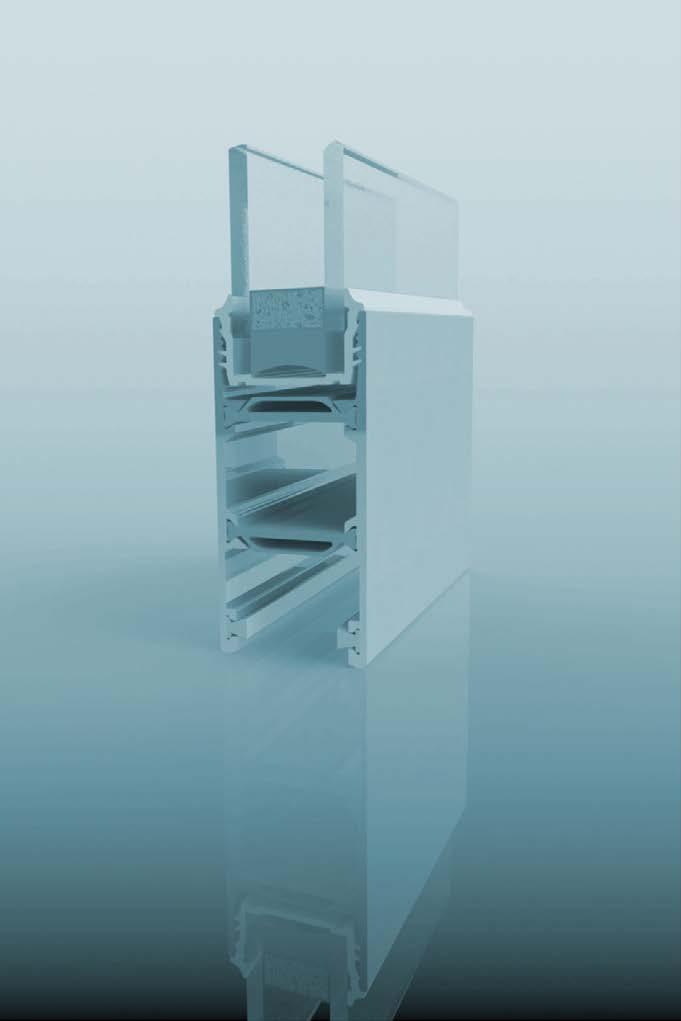
NEW PROFILE TECHNOLOGY LIFTS THE GULF
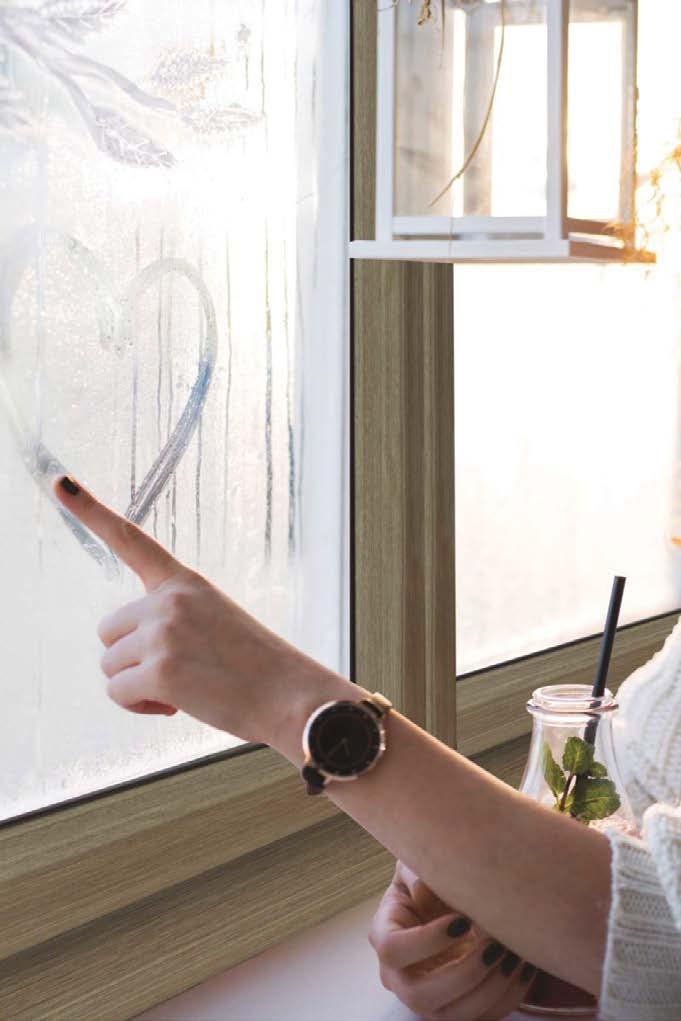
Alphacan is a global leader in the design and manufacture of customised U-PVC profiles for windows, doors and facades. Recently the company showcased its latest extrusion technologies at the world’s largest dedicated windows, doors and facades exhibition (WDF) held in Dubai. Philip Yorke reports on an interview with the company’s Export Sales manager, Edwardo Jimenez and Alphacan’s expanding and uplifting presence in the Gulf region.
With more than 50 years of experience in the production of U-PVC profiles for windows and doors, Alphacan has earned itself an enviable reputation for its high-quality products and continuous ground-breaking innovations. The company operates three state-of-theart production facilities in Europe; these are located in: France, Italy and Croatia and between them employ over 600 people.
Today Alphacan specialises in the lamination and finishing of U-PVC profiles and has developed exclusive technologies designed to customise windows, doors and facades according to the latest fashion trends. The U-PVC profiles are guaranteed by the quality labels issued by authoritative European Quality Management organizations. All Alphacan products offer excellent insulating properties and are reliable, maintenance-free and available in a wide range of colours and creative textured finishes.
Innovation and vision
Recently Alphacan Srl exhibited its latest products at the Windows Doors and Facades Event 2019 in Dubai. The company’s Export Sales Manager, Eduardo Jiménez described his strategic objectives and participation in the largest dedicated sales platform for windows, doors and facades in the Middle East region.
“At the big WDF event we showcased our exclusive range of U-PVC profile systems for windows, facades and doors. This is a complete range of high-performance products driven by Italian style and design, which are designed to appeal to windows manufacturers, architects and designers, as well as to contractors, real-estate agents and construction companies.
Our ‘System Master’ is a unique casement window system that is both compact and modern and especially suited to the Gulf region and Asian countries. Our sliding window systems such as In’Line’ and ‘PFS Mini’ are extremely versatile and offer multiple solutions for every kind of construction need. The former allows the construction of in-line sliding windows and doors for wide openings, whereas the second is a compact system intended for smaller spaces”.
Unique louvre shutter system
Also, on show at the exhibition was Alphacan’s innovative ‘Persiana’ series which offer an external louvre shutter system that is available with fixed or adjustable slats. This system enables users to darken and protect their homes from sunlight. In addition, it guarantees customers a fully adjustable ventilation system that provides them with complete privacy.
Furthermore, Alphacan’s world premiere of its customised finishing options available in the form of ‘My- Design’, were showcased via a window made with Alphacan’s System ‘In’Alpha70’, which offers fully optimised thermal and acoustic properties. The ‘My-Design’ collection is based on an entirely new printing technology developed exclusively by Alphacan, which allows the customisation of any of its U-PVC windows with any graphic, image and colour that is desired.

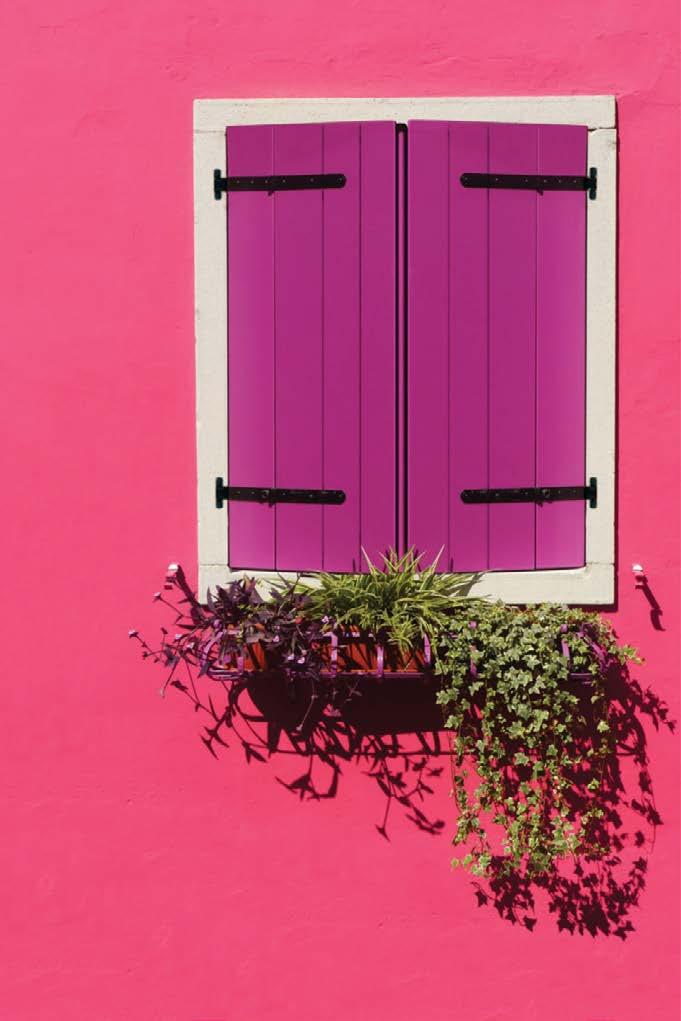
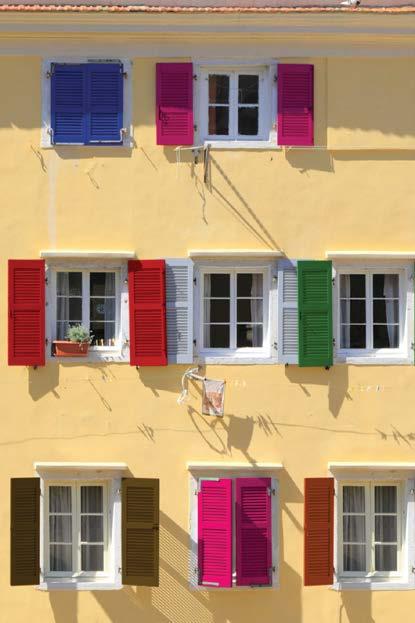
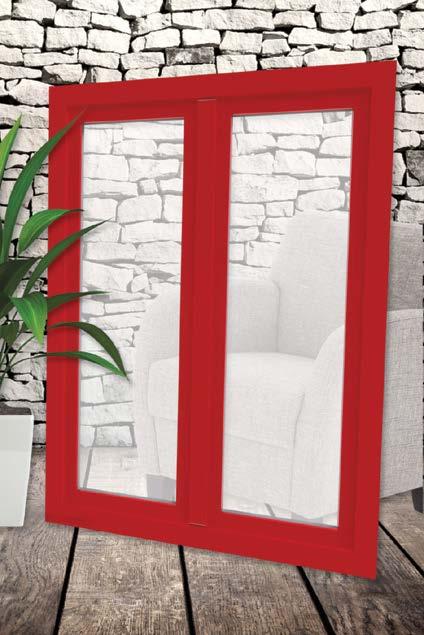

Futuristic finishes
Alphacan’s designers and engineers have produced an unlimited range of windows and doors that suit perfectly any interior decorative finish. The exclusive and futuristic finishes shown at the event included ‘Tropical Leo Tiffany’ which is a graphic pattern created by Italian designers and is a novelty in the Middle East region. This clearly demonstrates the diversity of Alphacan’s technologies and what they can achieve in the areas of flexible design and decoration.
All Alphacan’s U-PVC systems are available in a wide range of laminates and colours that boast around fifty different options. These in turn are divided into either solid colours, wooden effect finishing’s or metallic textures. In addition, it is possible to add an external aluminium cladding which makes it possible for Alphacan windows to suit any façade style and colour, with a clean metallic finish.
This year Alphacan exhibited its product portfolio in partnership with the Italian windows manufacturer Tonini Serramenti, which is already present in the Emirates. This strategic partnership enables Alphacan to give accurate consultancy to its customers on the design and finish of its windows, doors and facades for the Middle East region. Furthermore, Tonini showcased the exclusive finishing of its ‘Fashion Tonini’ collection, a series of luxury windows decorated by hand with real leather and other exclusive fabrics.
Alphacan strongly believes that its products, especially those driven by Italian design and creativity, represent new and interesting building solutions, which are all dedicated to this high-end market segment. This strategy is very much in line with the Saudi Arabia Saudi Vision 2030 program. More specifically, the possibilities of innovative decorations, such as fully customised designs, the use of special designer materials such as aluminum or leather and many more aesthetic novelties help to create a greater share of the Middle East market.
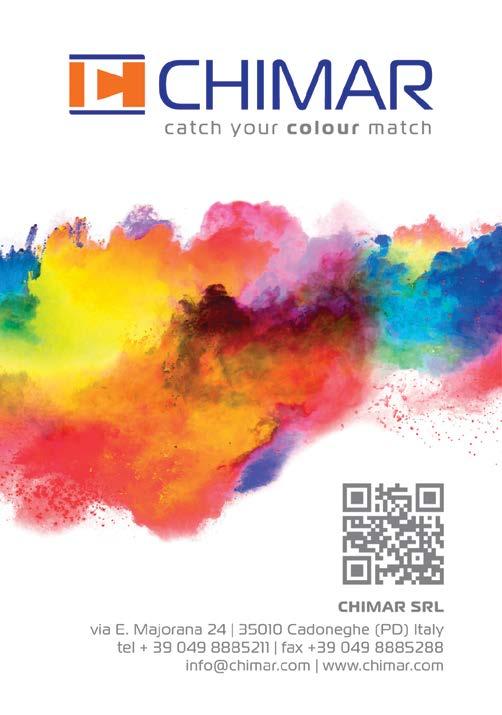
Uplifting urban environments
Today the Gulf region has achieved a very high level of design, construction and architectural techniques, as exemplified in the many exciting buildings recognised all over the world from its skyline. Alphacan also values its capacity for adopting new technologies and innovations in order to create the world’s most pleasing and uplifting urban environments.
Jimenez added, “We aim to come across with local partners interested in our products and innovations, partners who share our vision on customized architecture and decoration, and who are driven by innovation and design. We believe that all visitors will have appreciated our ‘Made in Italy’ creativity, finding inspiration for their projects, their homes, and entirely new concepts for windows, doors and facades. We want to transmit our passion in all that we do”. n
For further details of Alphacan’s latest innovative windows, doors and facades visit: www.alphacan.com
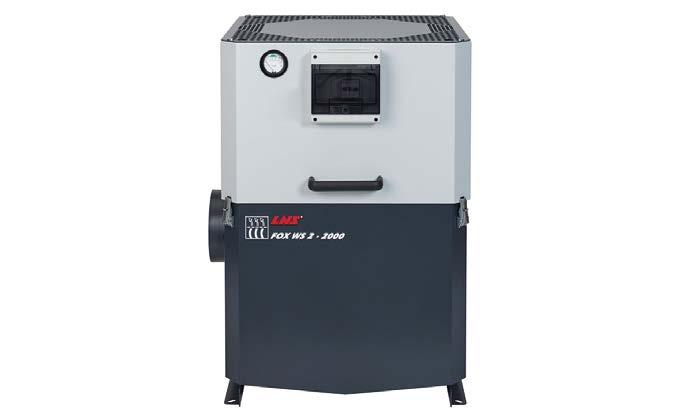
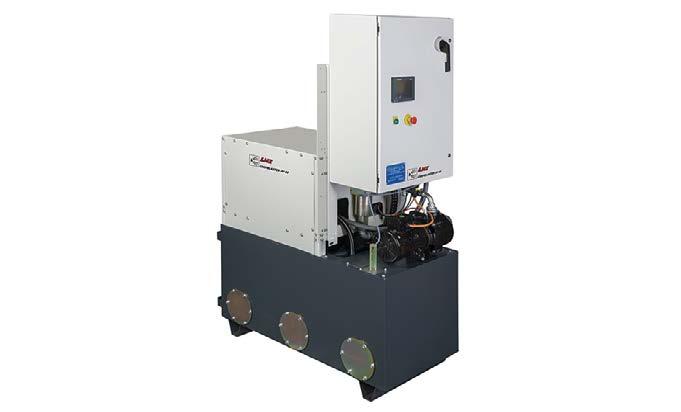
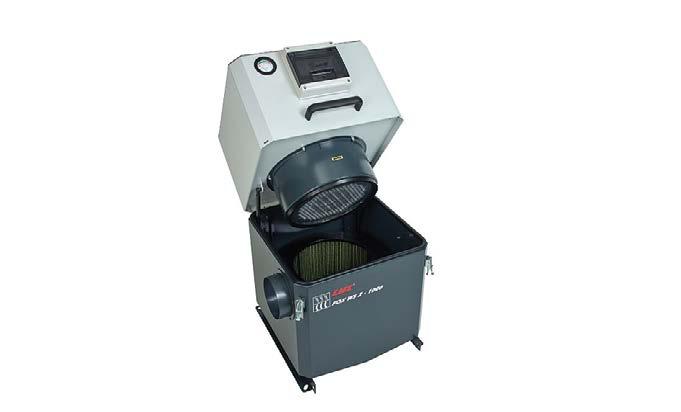
OPTIMISING MACHINE TOOL EFFICIENCY
LNS, the one-stop shop for machine tool peripherals, has introduced a new product line to its global customers
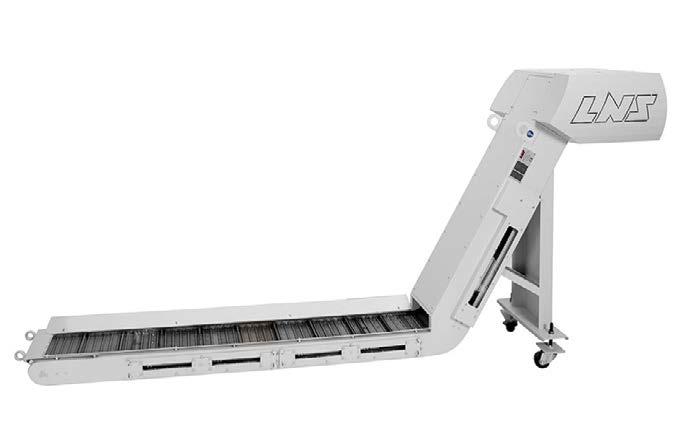
At the EMO machine tool exhibition in Hannover, September (2019), the world leader in bar feeding, air filtration, coolant management and chip management systems for machine tools, the Swiss-headquartered LNS Group, introduced its new “Chipblaster” product line.
With over 1000 employees, a global sales and service network and nine production sites on three continents, the LNS Group intends to leverage its worldwide presence to introduce the “Chipblaster” product range to the world-wide market.
The LNS Group acquired Chipblaster Inc. in October 2018. Founded in 1994 in Pennsylvania, USA, Chipblaster Inc. is an established market leading manufacturer of high-pressure coolant systems, coolant chillers and cyclonic filtration systems – making it a perfect fit into the LNS Group portfolio of products and services.
The Chipblaster Inc. range of integrated machine tool accessories include the “Chipblaster” high-pressure coolant system, the “Chipchiller” series of high-performance coolant chiller units, the “Skimblaster,” oil skimming unit to eliminate tramp oil and the stand-alone or modular Cyclone filter system for fluid filtration down to 2 microns.
Commenting upon the acquisition, LNS Group CEO Gilbert Lile says: “Chipblaster” is a market leader in the U.S. high-pressure coolant industry and is a natural fit into our machine tool peripheral product portfolio. At LNS, we plan to leverage our global sales and service network to sell “Chipblaster’s” technologically advanced products on a worldwide basis. A common thread running through both companies is the goal of helping manufacturers optimize the efficiency of their machine tools to improve performance, productivity and profitability.”
Covering machine tool needs
Since it was established in the Jura Arc region of Switzerland in 1972, originally to develop mechanical bar loaders for precision-machining used by watchmakers. LNS has grown to become the global machine tool industry’s leading supplier of advanced barfeeders, chipconveyors and cooling air-filtration systems.000 air filtration systems
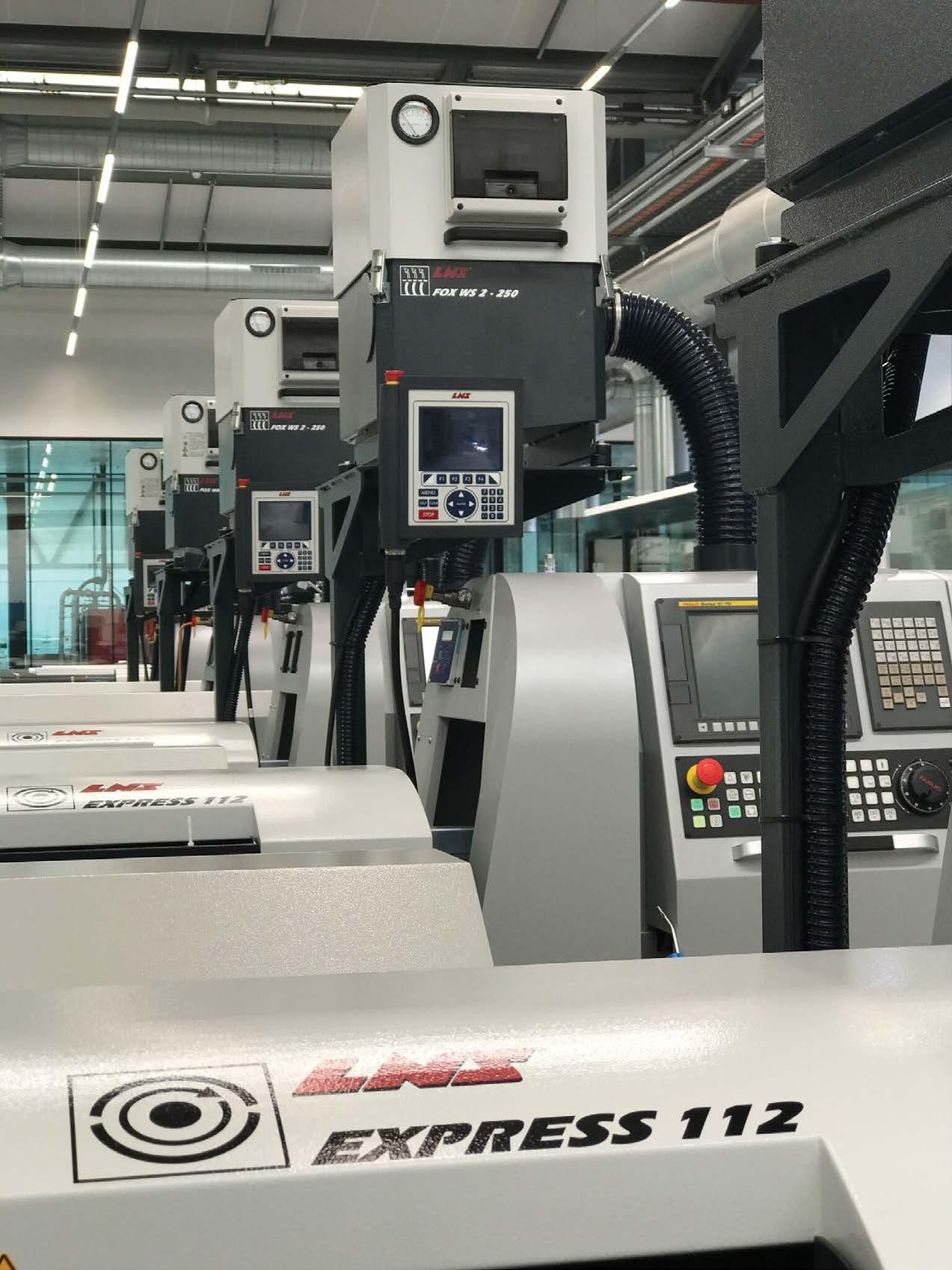
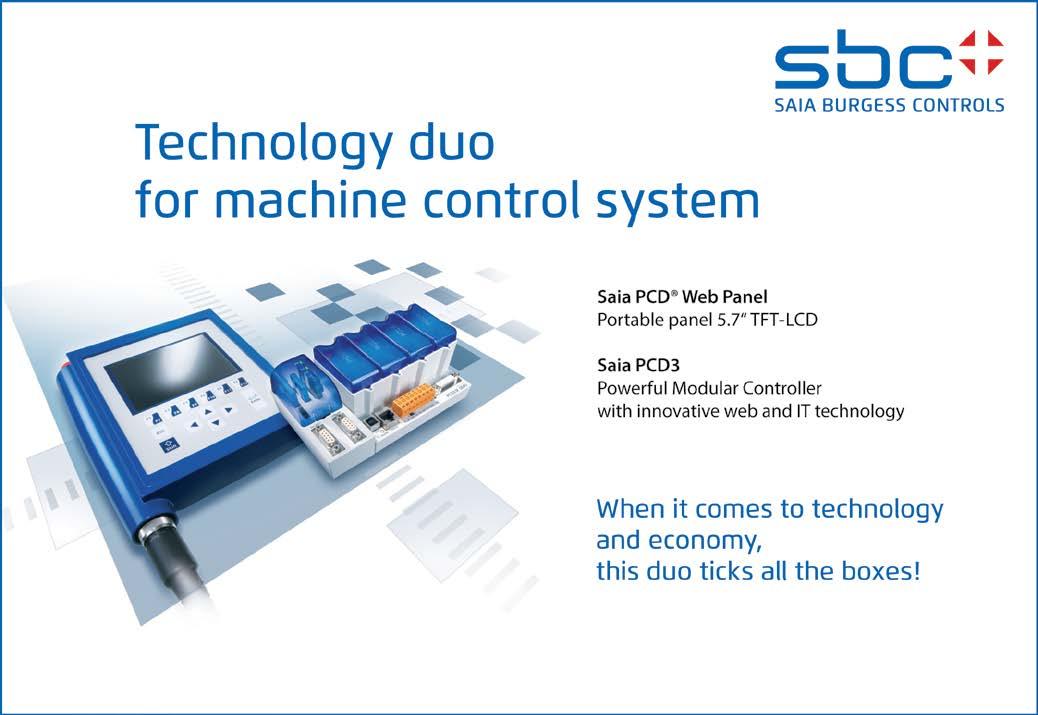
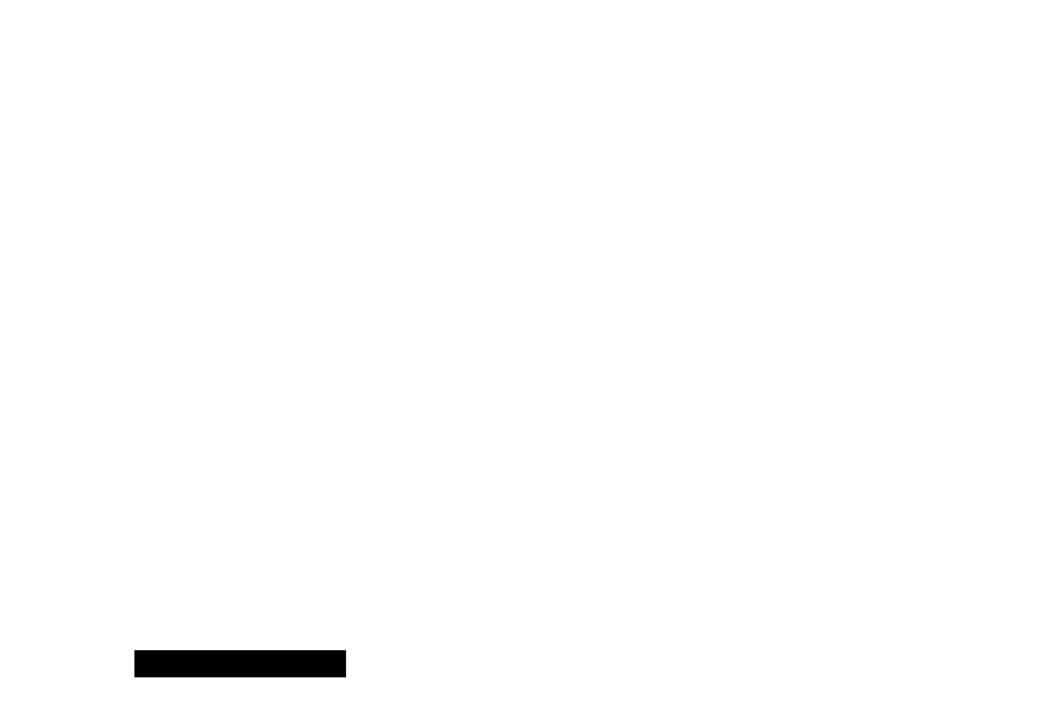
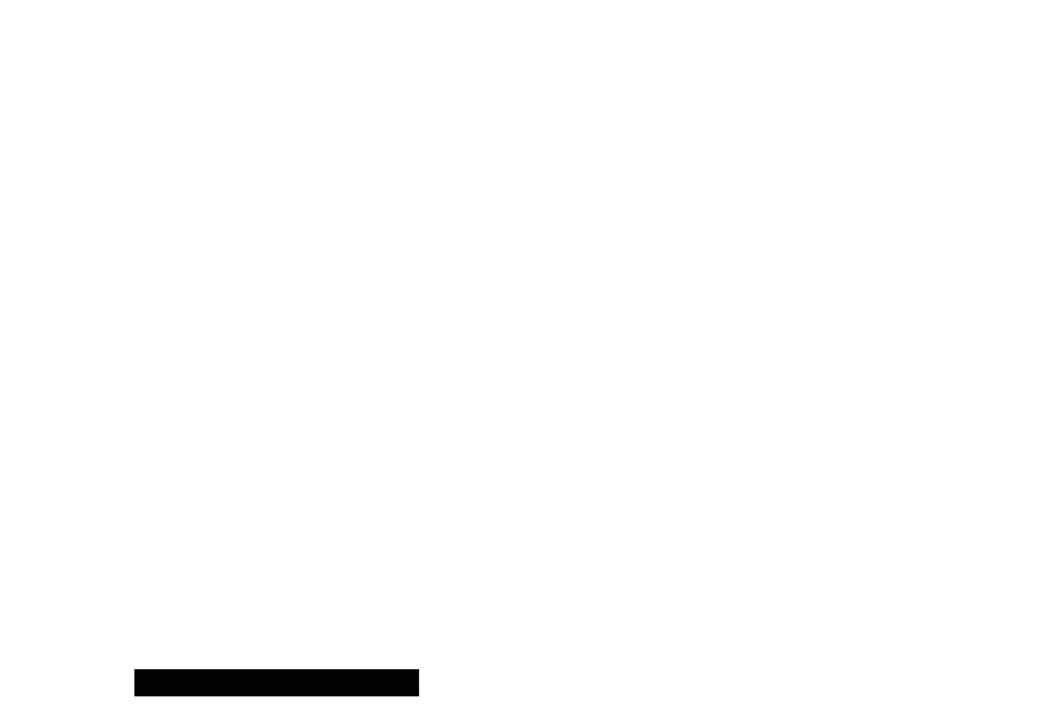
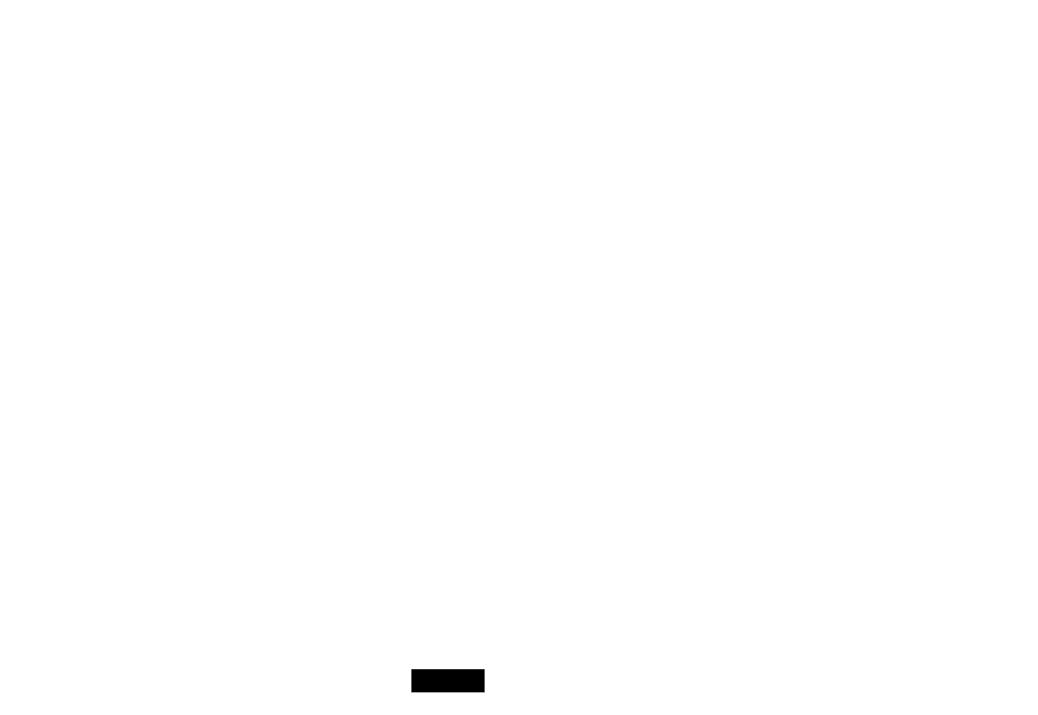
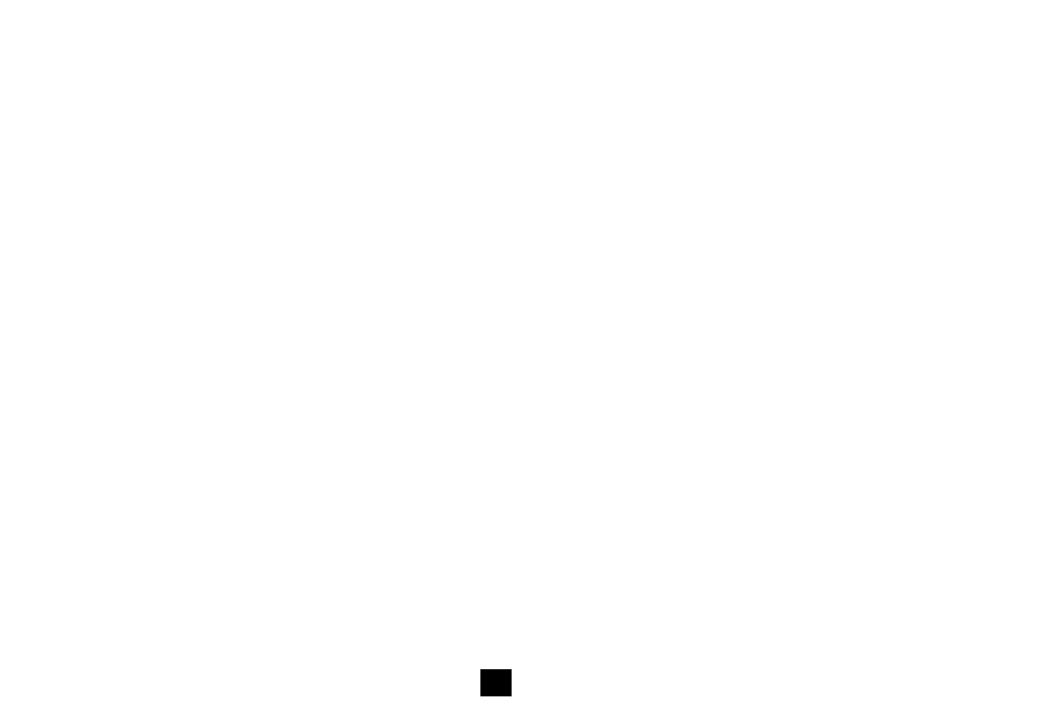
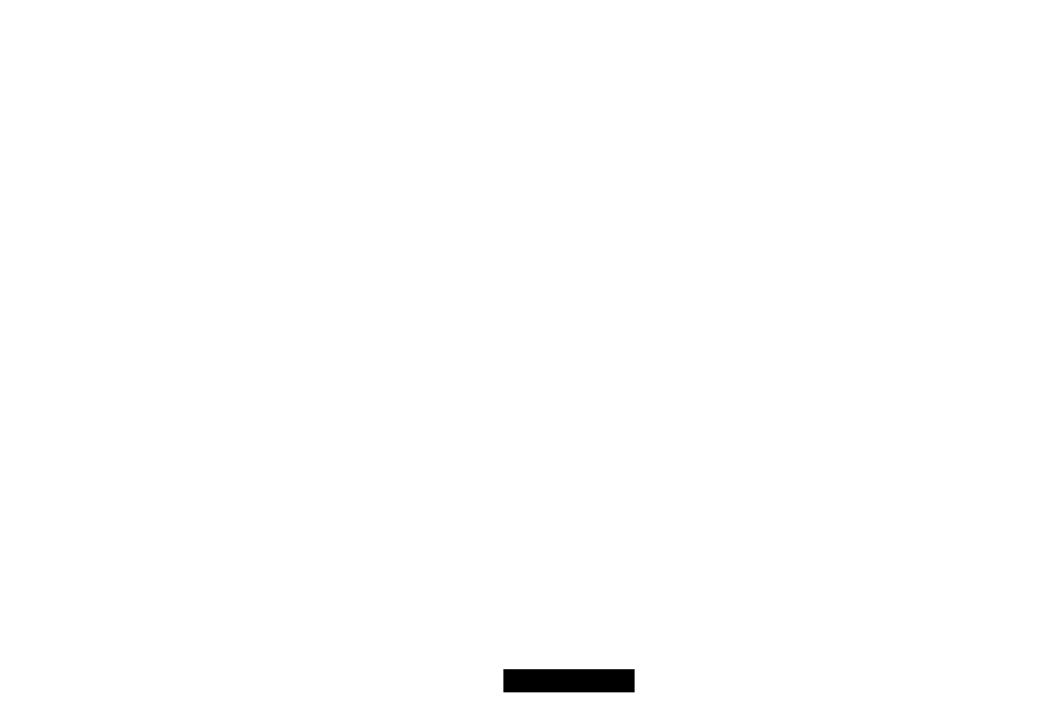
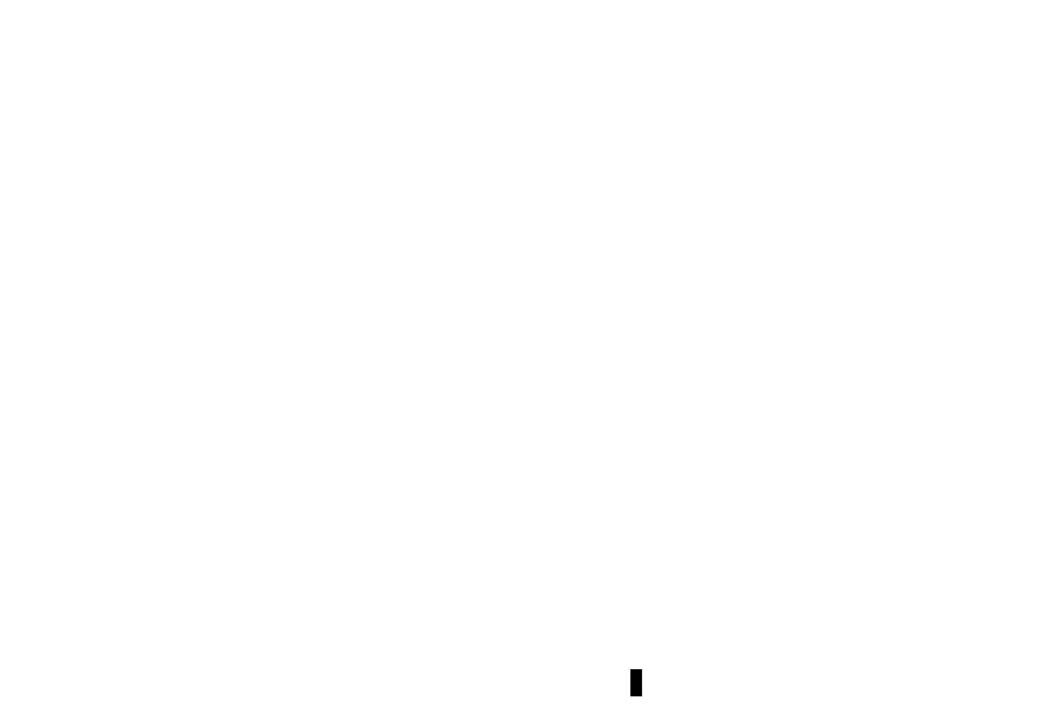
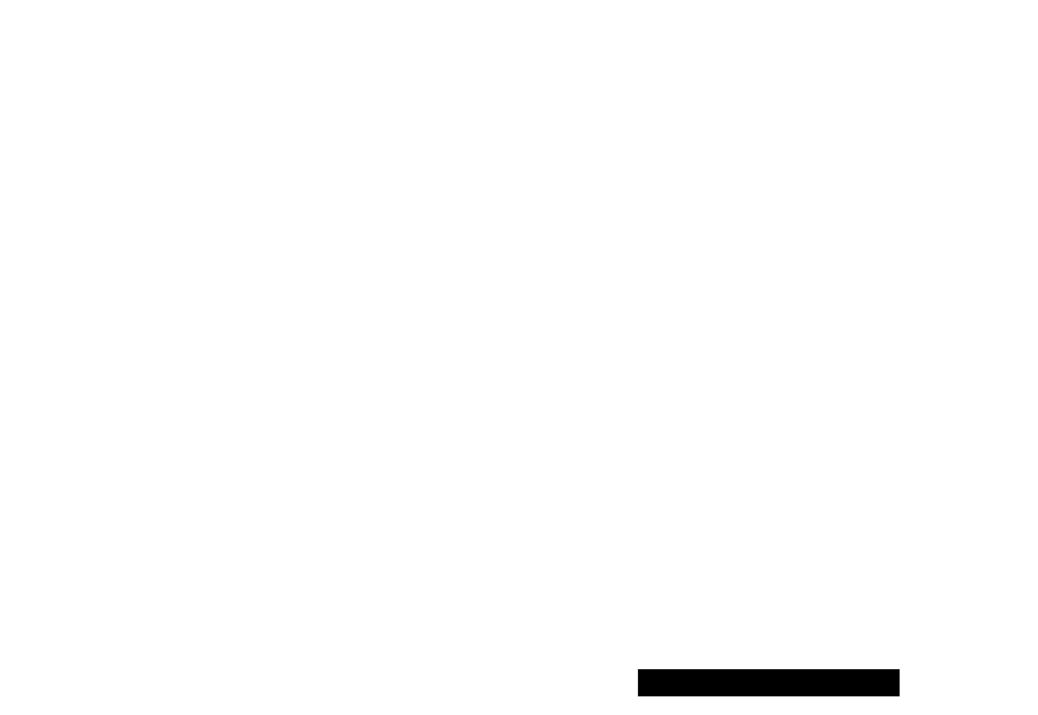

Today there are over 160,000 LNS bar feeder units installed worldwide as well as 140,000 chip conveyors, 35,000 coolant systems and 13,000 air filtration systems.
LNS bar feeders are universally recognized for their groundbreaking Hydrobar bar-guiding technique. In the most varied applications, LNS bar feeders ensure maximum productivity on all types of fixed or sliding headstock lathes. In addition, LNS bar feeders offer record reliability and flexibility and the fastest diameter changeover available today.
LNS also specializes in a wide range of airfiltration solutions for the elimination of pollution related to the metal manufacturing environment. Originally developed for the elimination of mist, aerosols and smoke typical of metal cutting operations, these filters can also be employed in applications like Grinding and Electro Discharge Machines.
Introduced in 2016, LNS’ Turbo SFcompact is a completely new approach to fine filtration. With its compact size, self-cleaning filtration to 50 microns, easy handling of most materials and chip types, excellent return on investment, modular design for easy maintenance and low energy consumption, the SFcompact is, the company believes, a revolutionary system in air filtration.
“The SF-compact combines more than 30 years of knowledge in designing, manufacturing and servicing chip and coolant management products for the machine tool industry. It is the culmination of
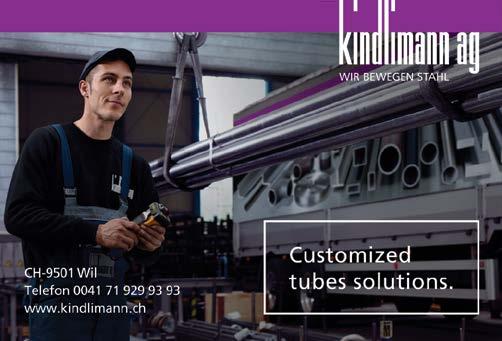
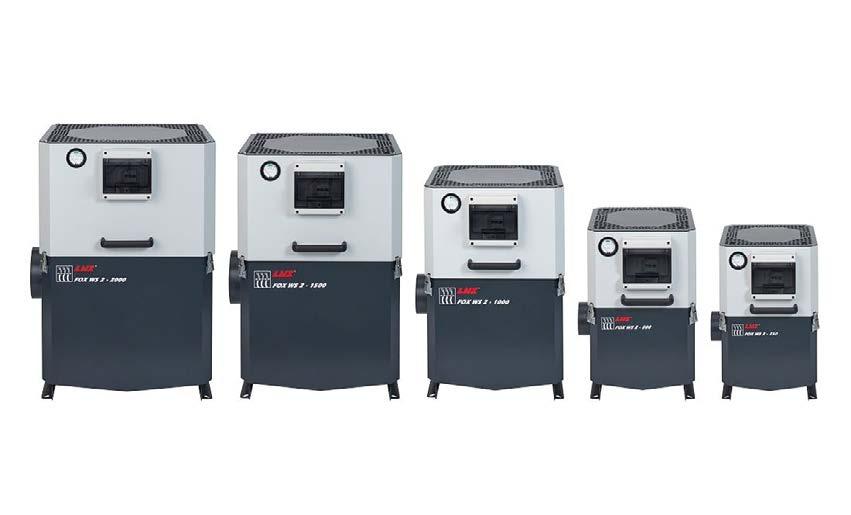
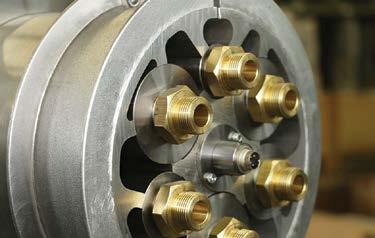
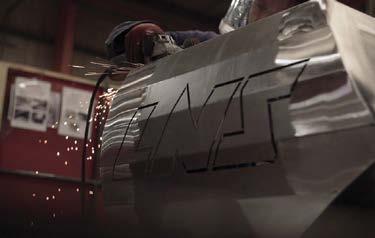
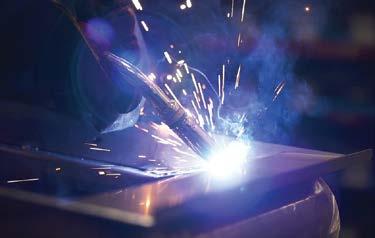
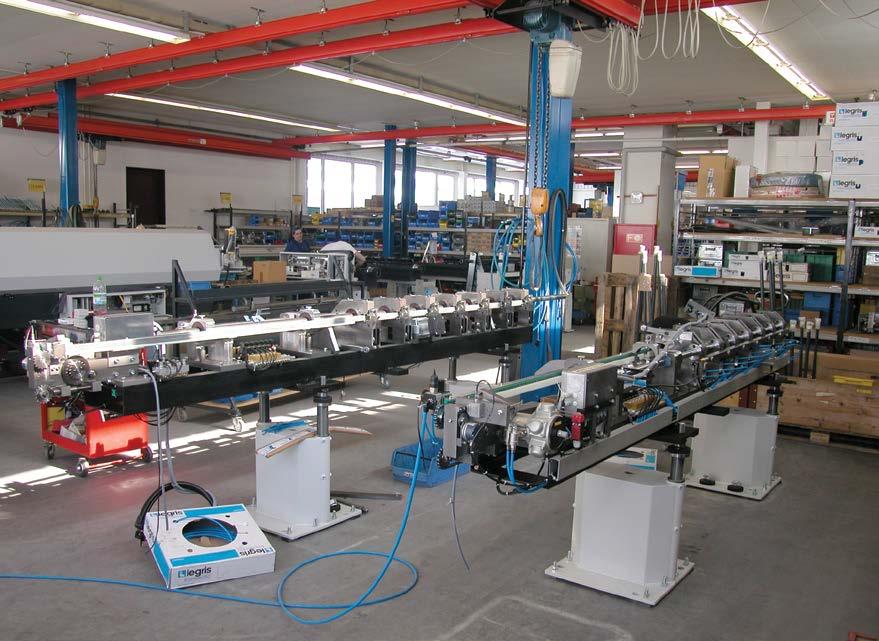
years of development and testing – a true high-tech fine filtration solution complementing the rich product portfolio of LNS”, explained Jamie Towers, Global Product Manager CCM at the LNS Group.
Chip conveyors and coolant systems
LNS’ conveyors and complete chip disposal systems are designed for all machine types (milling, turning or machining centres) For the most varied applications a complete range of conveyors covers all material types and chip shapes. Additionally, LNS chip conveyors can be equipped with up to 50 microns filtration systems.
LNS offers a complete range of high-pressure coolant systems and tramp oil removal systems that guarantee optimal lubrication allowing a considerable increase of machining speeds. The additional benefits are an improved surface finish of the parts, increased lifespan of the cutting tools and superior chip management.
Expanding markets
As well as offering a complete product range, LNS is engaged in a constant search for new technologies and solutions that will allow customers to maximize their productivity. The experience gathered since the creation of LNS in 1973 has allowed the group to be finetuned to be even closer to its regional markets and to respond even faster to the future technology evolutions.
The LNS market is managed through a network consisting of sister companies and exclusive agents. This global distribution network, which has been built over nearly 50 years, allows the Group to create customer loyalty and to acquire new customers. This distribution network is being constantly expanded in order to cover new regions as efficiently as possible. n
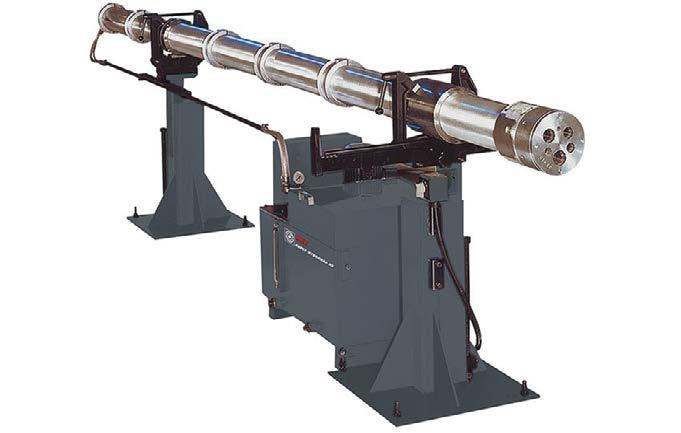
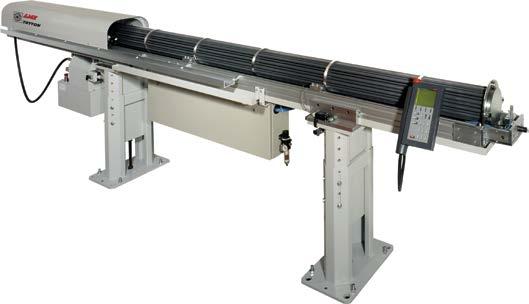
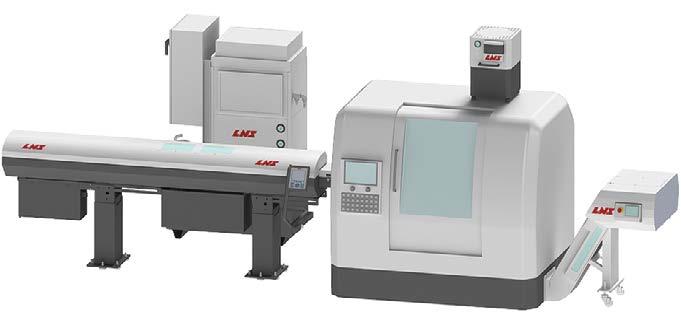
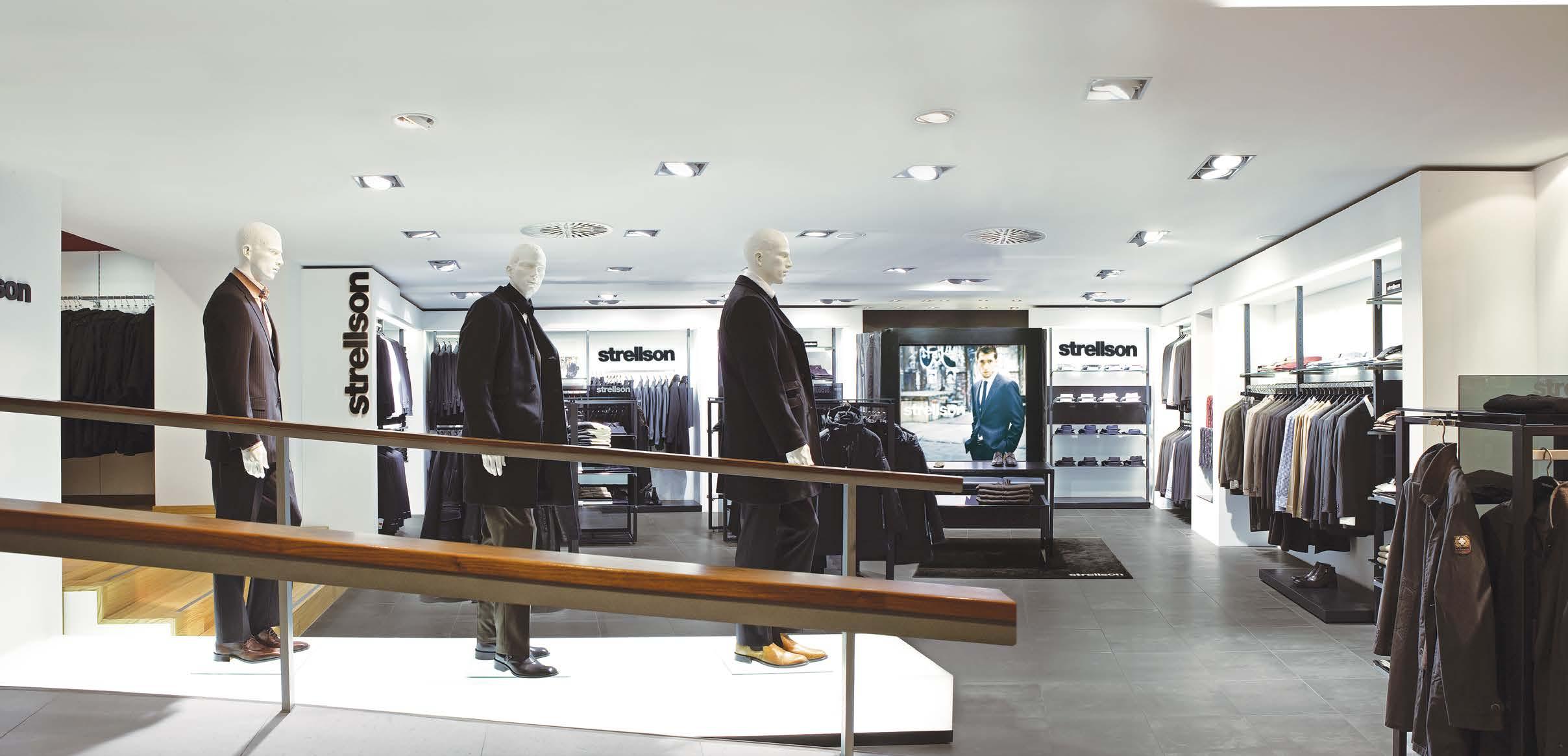
A LEGENDARY BRAND
With the recent relaunch of its iconic Swiss jacket, Strellson marks a quarter century of the finest fashion in modern menswear.
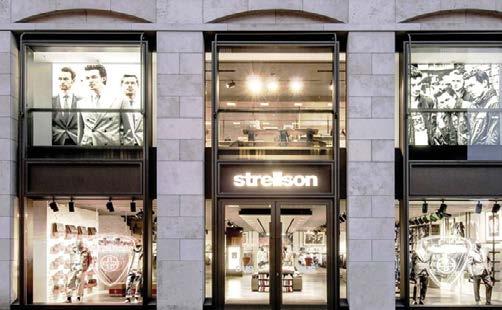
Last year (2018) the Swiss producer of quality menswear, Strellson, launched an anniversary collection to mark 15 years of production of its legendary Swiss Cross coat. This iconic casual jacket was originally developed from old Swiss army blankets and launched as a limited edition in 2003.
The hooded jacket became instantly famous thanks, in part, to headlines in the British press pointing out that it included a Swiss Army-style knife attached by a chain in a pocket. As the sale of knives to minors was illegal in Britain, retailers in the UK were initially forced to withdraw the product.
In fact, the Swiss Cross coat swiftly became a must-have item. Strellson had started with a limited production of 3,000 pieces but after the company placed an ad in one of Zurich’s main newspapers, the whole lot sold out in a few days. For a while, the company couldn’t even get its hands on enough army blankets to meet demand. As one its designers said at the time, “Somehow we just managed to hit the Zeitgeist.”
Over the years, the shape of the coat has been refined, but the integrated penknife remains part of the design. And the jacket actually led to Strellson’s expansion into two product lines – the brand was split into a sportswear and a business line, each with individual distribution strategies.
Ever since, Strellson’s Premium Line has focused on business suits, while the Sportswear Line continues to revolve around the coat.
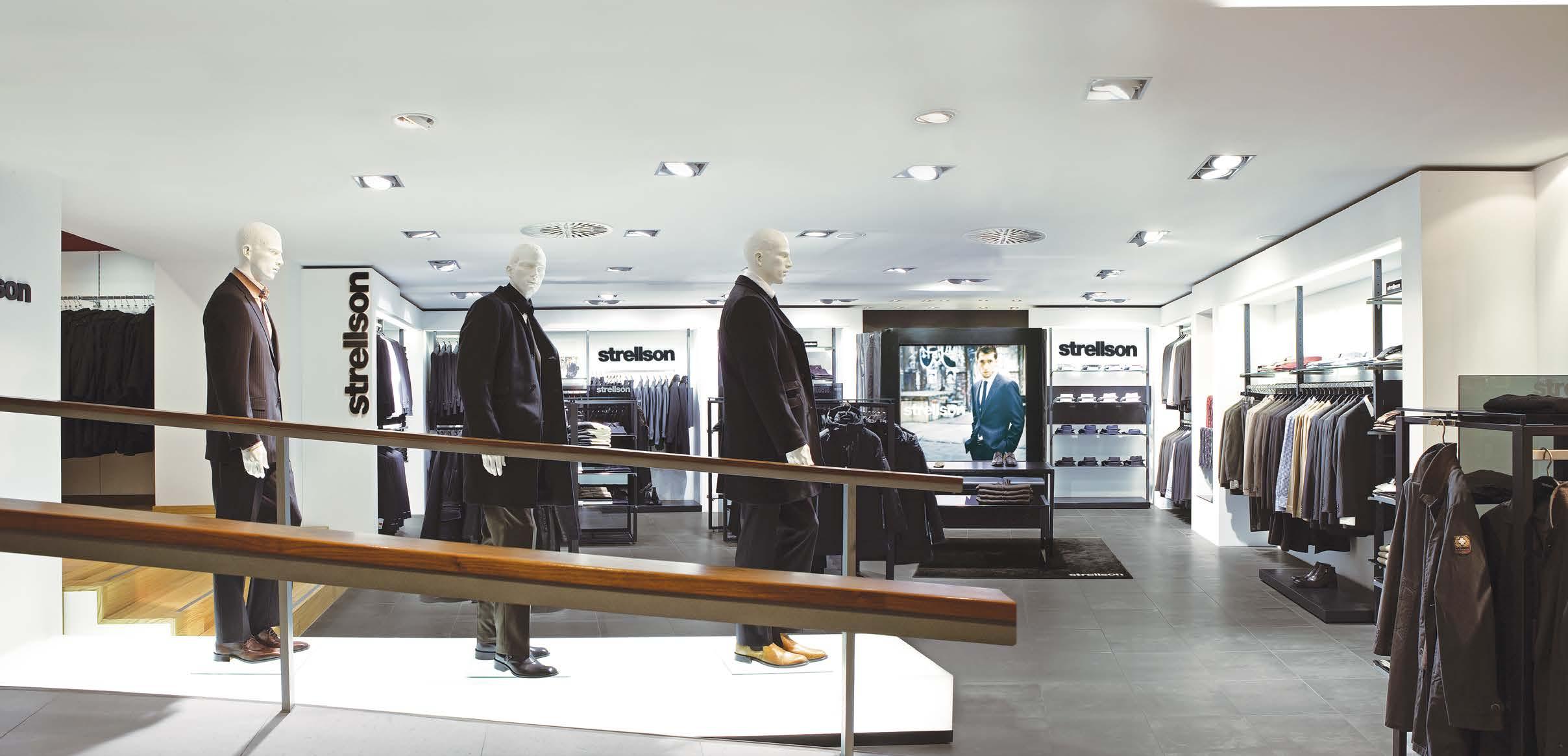
Three brands
Strellson AG is an international fashion and lifestyle company based in Kreuzlingen, in Switzerland. It is the country’s largest menswear manufacturer, producing mid-range products aimed at men between 25 and 40. Together with the well-known fashion
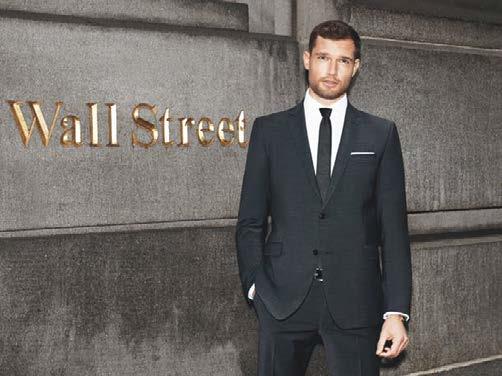
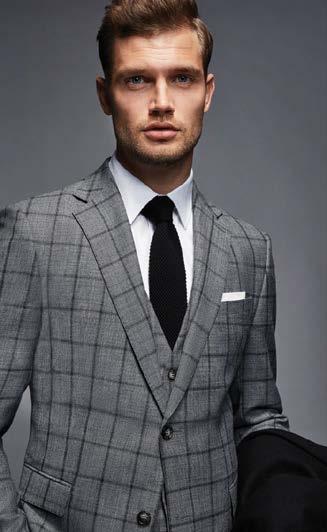
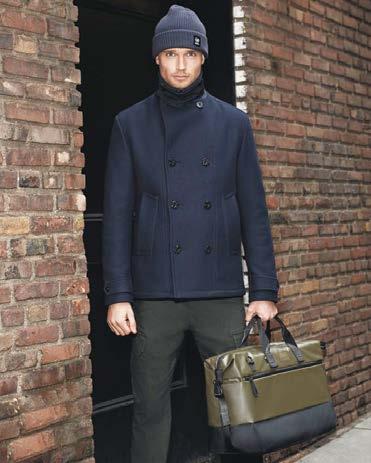
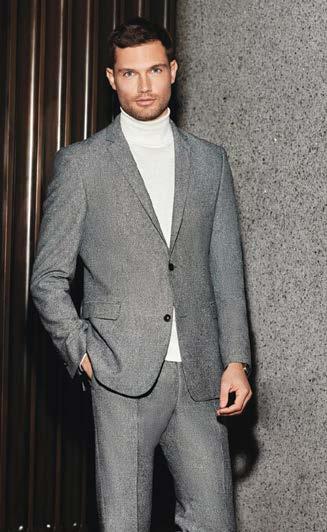
brands Windsor and Joop, it is today part of the Swiss-owned Holy Fashion Group. All three brands are managed individually, each with their own distinctive strategy and orientation
The Strellson range is characterised by bold and straightforward design that is Innovative and cosmopolitan. The brand stands for premium fashion with a distinctive silhouette for ambitious men. The aim is to produce both tailored and casual clothing for active and stylish men of today and tomorrow. All Strellson garments are designed in Switzerland.
JOOP! is the premium design brand of German origin with a clear market position and a high degree of recognition. Its comprehensive product portfolio offers a modern lifestyle for men and women who value fashion and design. JOOP! stands for the natural combination of a sense of style and the finest quality – always with the unmistakable signature of the brand: contemporary and effortless.
Windsor, for the Holy Group, is more than just a brand - it stands for not just fine menswear but a whole way of life. Windsor, characterised from its beginning by elegant English fabrics and styles and now known for the finest Italian wool used in its suits, jackets, blazers and coats, caters to people for whom quality and modernity are core values. The brand has indeed been synonymous with premium fashion for over 100 years.

Reaching new markets
Strellson’s European expansion began in 2008 with the opening of a Strellson Sportswear monostore in Berlin, Germany. In the next year more monostores were opened in Graz (Austria), Lille (France) and Moscow (Russia) as well as a number of stores in China.
In 2011 the first flagship store opened in Düsseldorf, Germany. Further stores were opened in Lyon (F), Toronto (CA), St. Petersburg (RUS) and Poland.
These were followed in 2013 and 2014 by stores in Munich, Cologne, Frankfurt, Shanghai, Minsk, Hong Kong, Gdansk and Mexico City.
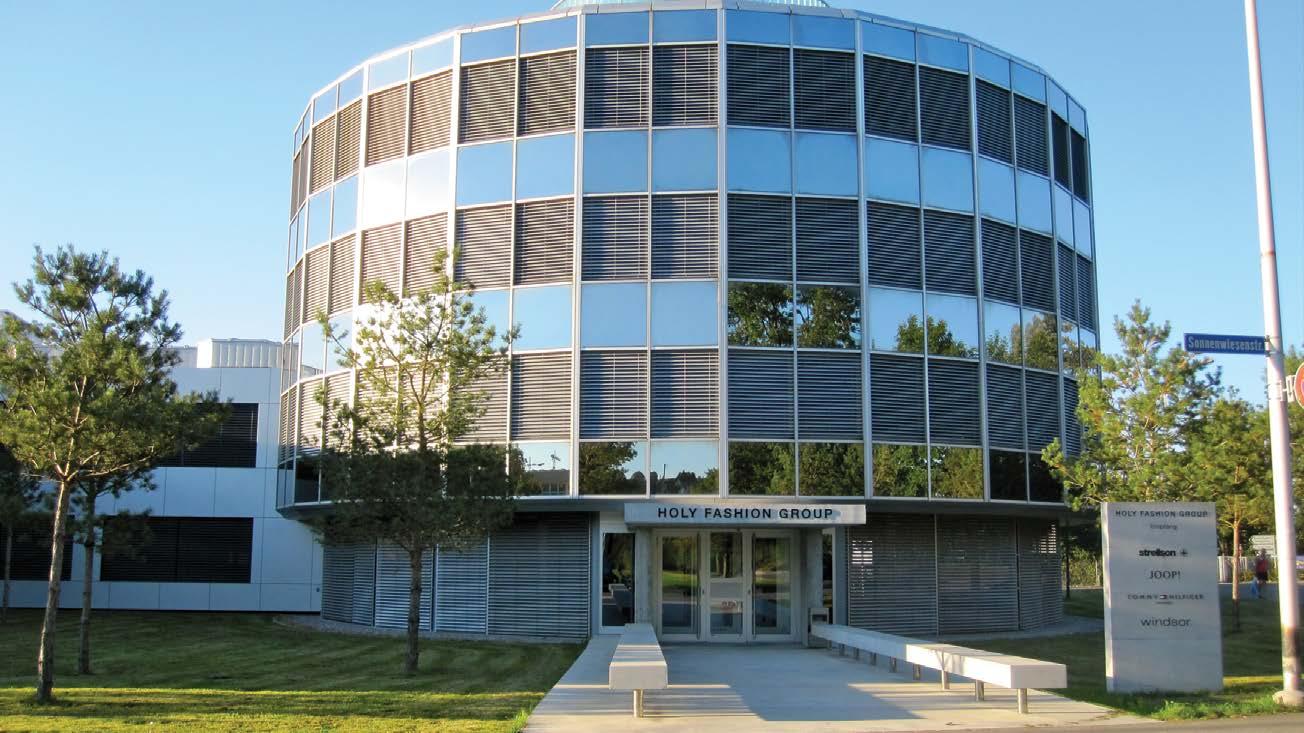
In recent years the company has strongly focused on the expansion of its e-business, with the launch of new branded online shops for Strellson, Windsor. and JOOP!
In 2015 the HOLY FASHION GROUP strengthened its individual brands through differentiated positioning and organizational focus. Windsor womenswear and JOOP! womenswear were established at the headquarters in Kreuzlingen while JOOP! moved into the spectacular JOOP! Villa in Hamburg, where the brand’s history began. 2016 saw Strellson entering the US market and the foundation of the Russian subsidiary Strellson Russia OOO. This was followed in 2017 by the establishment of the Canadian subsidiary Strellson North America Ltd. in Toronto.
Welcome to New York
Strellson’s Winter 2019 collection is themed around New York, USA. The campaign identifies the city as the place where English attributes merge with the clarity, openness and modernity of New York and the urban lifestyle of the ‘New Generation’. The new lines combine a natural simplicity and authenticity with a rediscovered elegance. New shapes and volumes influence the look and accordingly formal and sporty-looking elements are represented in the styling over a soft, relaxed silhouette. The workmanship and interplay of style and fabric become a central aspect.
The collection also features an outdoor material mix in which nylon and bonding qualities come into play. This material mix combines with the finest finishing and treatments to give the individual styles and qualities new authenticity for the fabric. n
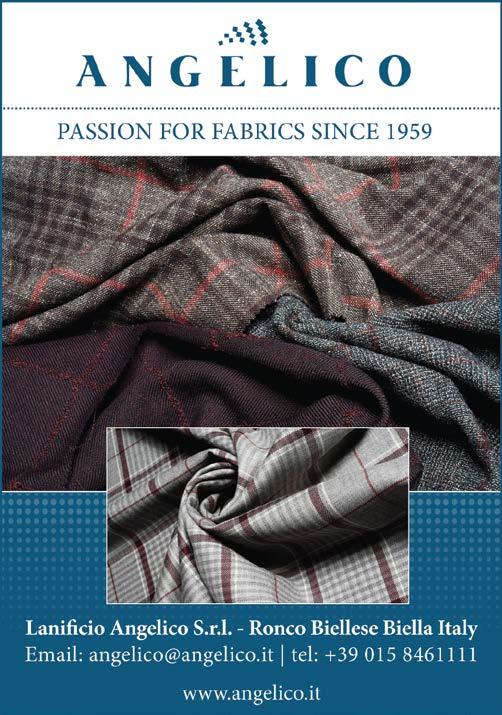
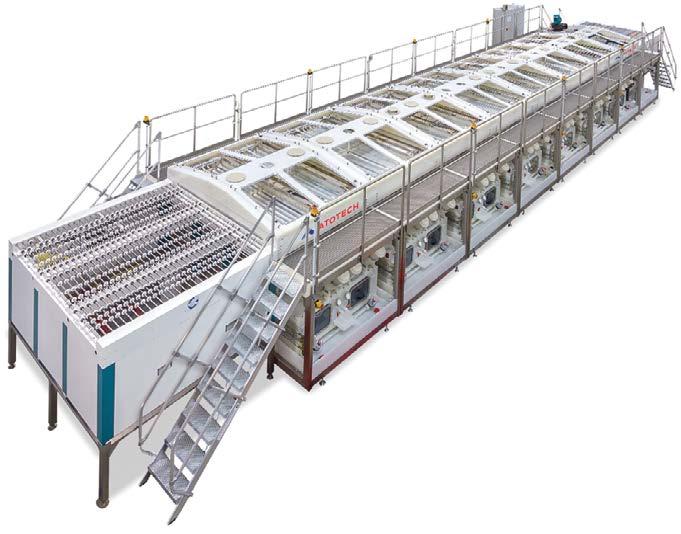

LEADING THE WORLD IN SURFACE FINISHING
Germany’s Atotech continues to expand its technologies and its markets with strategic acquisitions and new product development.
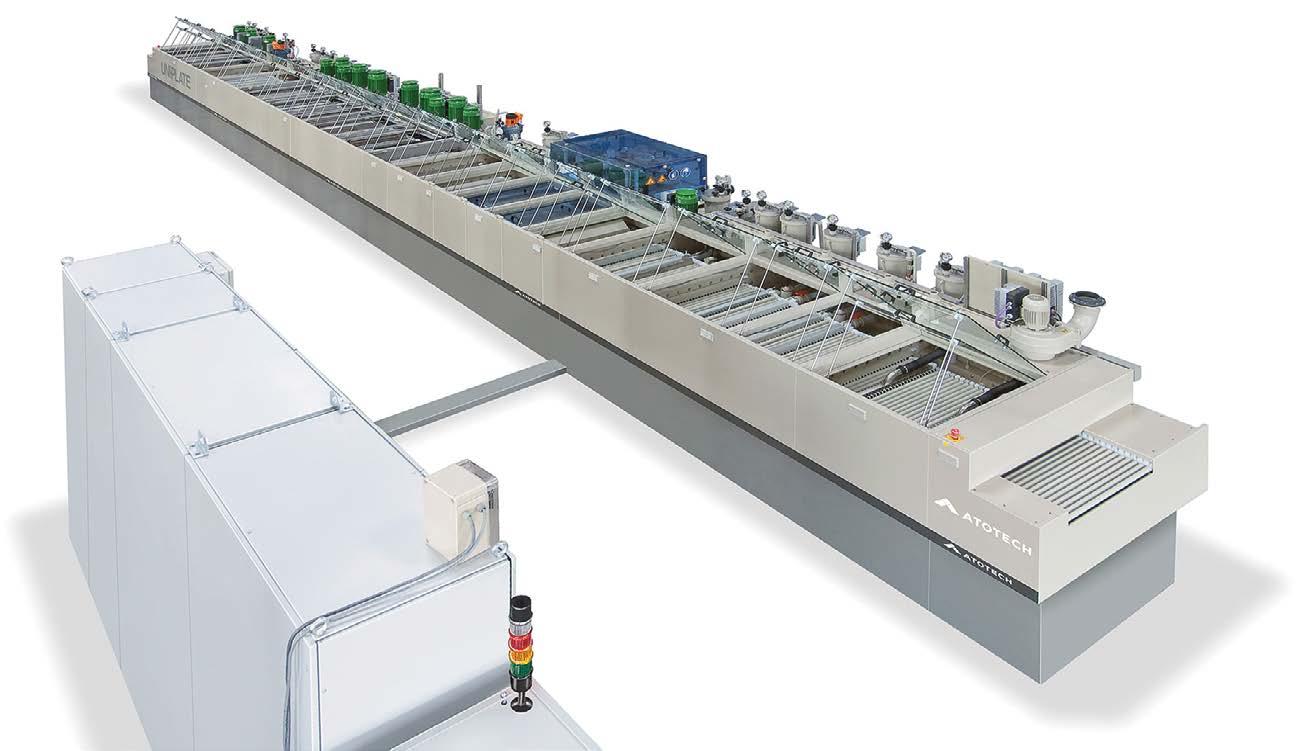
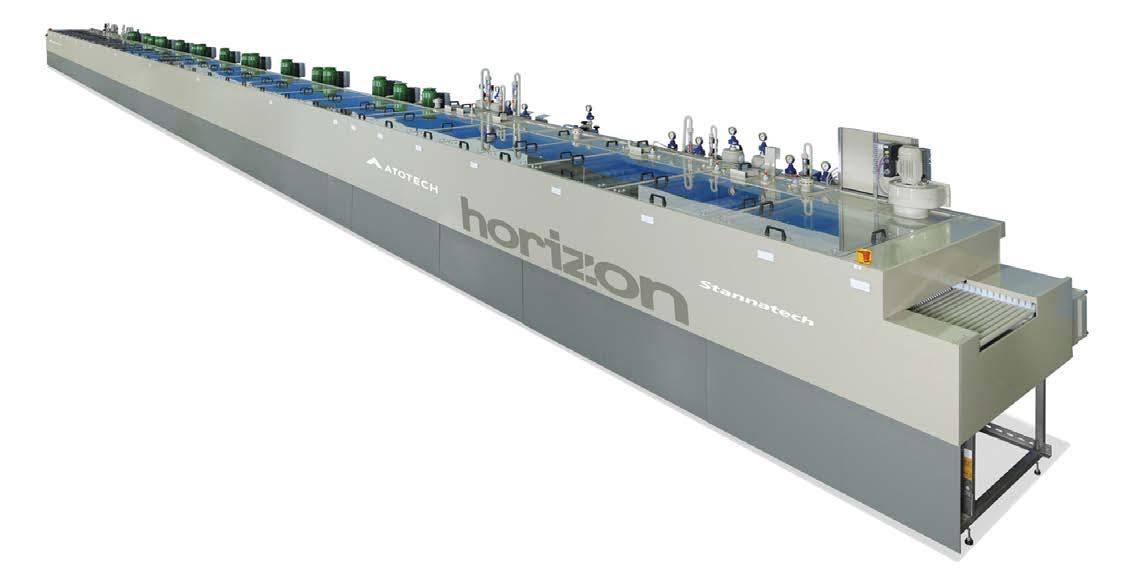
In August 2019 Atotech, a global leader in advanced plating chemicals, equipment and services for the printed circuit board, IC-substrate, semiconductor and surface finishing industries, announced that it had acquired J-KEM International. Based in Rosersberg Sweden, J-KEM is a global supplier of highquality chemical products and processes for the printed circuit board and general metal finishing industries. J-KEM’s strong technology and customer relationships complement Atotech’s product portfolio and will help expand addressable markets and drive future growth.
J-KEM’s customers now have full access to Atotech’s regional and global product development, production and technical support capabilities, including its world class and accredited material science and analytical services.
Geoff Wild, Atotech’s Chief Executive Officer, commented, “We are thrilled to add J-KEM’s strong products and technologies to Atotech. We see substantial opportunities to further grow our business with this set of new and excellent products. In particular, J-KEM brings to us a graphite process that gives superior performance, an accelerator-free system in collaboration with an EDTA electroless copper process, as well as a palladium-based direct metallization process.
“These additional capabilities will help expand our reach into exciting growth markets like flex-PCBs and exotic materials. J-KEM’s strong reputation for technical performance fits well with our unique solution-based approach that combines a comprehensive offer of proprietary process chemicals and equipment with best local service.
“This acquisition is representative of our strategy to drive growth and expand the scope of our technology so we can address a greater share of the market. We will continue to look for opportunities that make us a more important partner to our customers.”
Johan Lundqvist, J-KEM’s Chief Executive Officer, added, “We are pleased J-KEM is joining the Atotech family, as it makes sense for both sides. J-KEM will contribute to Atotech’s portfolio, and existing J-KEM customers will benefit from Atotech’s best-in-class service. We look forward to being part of the Atotech team.”
A Vital partner
Atotech is one of the world’s leading suppliers of specialty chemicals and equipment for the printed circuit board, chip carrier and semiconductor industries, as well as decorative and functional surface refinement.
Since it was formed in 1993 from a merger of the Elf Atotech group of companies with M & T Harshaw and Schering’s electroplating division, it has become a vital partner for countless industries that require both functional and decorative surface-finishing solutions.
Today Atotech is present in more than 40 countries and runs 17 TechCenters, 14 chemistry, and 2 equipment production sites It is a
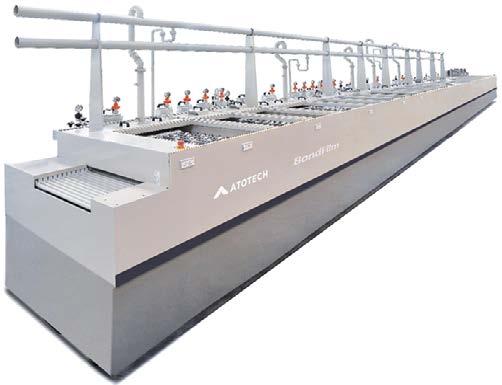
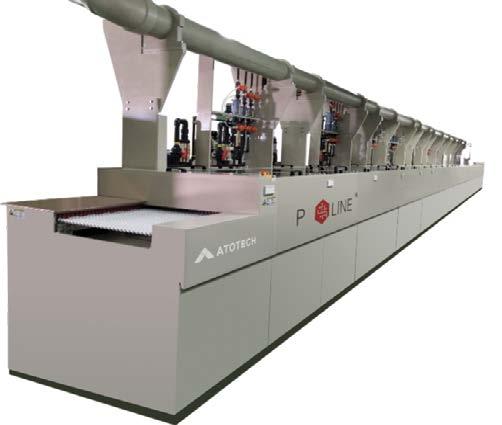
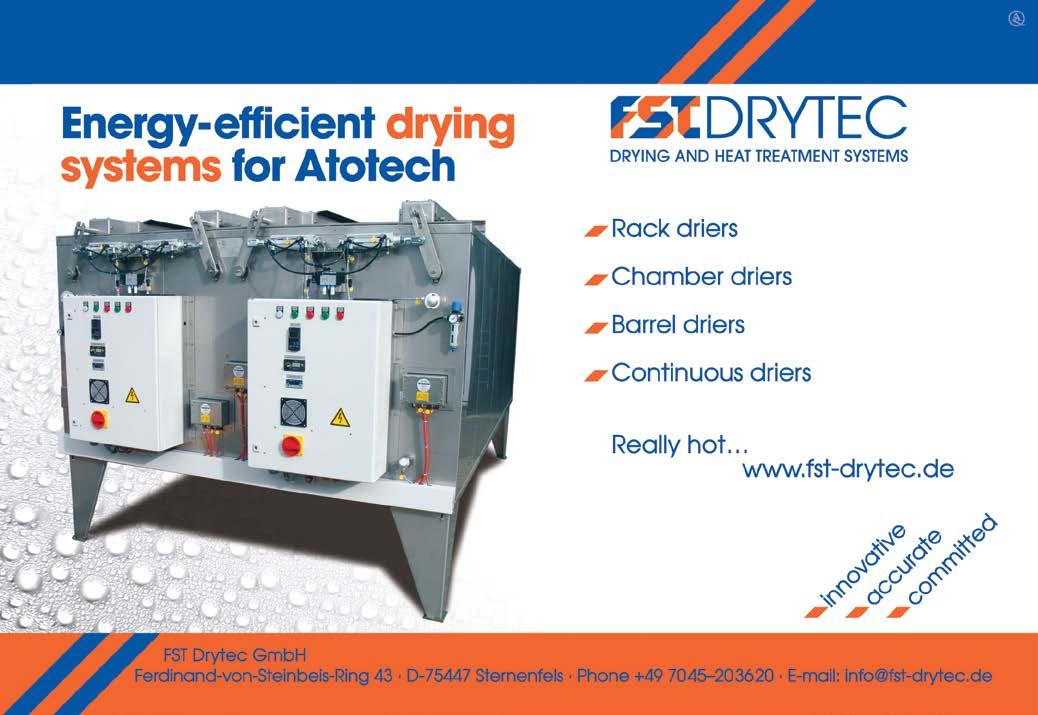
world leader in pioneering innovations in the industry, with over 2,100 registered active patents - 1,700 for chemical processes and 400 for equipment. Its global headquarters are in Berlin, Germany, and its regional HQs are in Yokohama, Japan, and South Carolina, USA.
The company currently operates in two business segments: Electronics (“EL”) and General metal finishing (“GMF”). Its systems and solutions enable the creation of the electrical conductivity integral to the function of printed circuit boards and semiconductors and also provide functional and decorative surface finishing for a wide range of applications, including applications subject to stringent environmental regulations
Atotech products and solutions can be found in a wide variety of crucial end markets. These include surface finishing and electronics for the automotive industry, communication applications for smartphones, next generation connectivity and cloud computing, big data processing infrastructure, medical equipment, household appliances and much more.
Polygon PLB
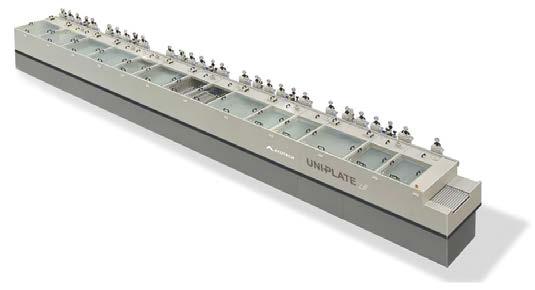
In June 2019: Atotech announced a new line of innovative horizontal production equipment – the POLYGON PLB LINE. This new production equipment is designed for printed circuit board manufacturers with high reliability and high performance demands in multilayer, rigid-flex and HDI panel processing taking advantage of a complete wet-in-wet in-line solution.
The POLYGON PLB LINE is a new de-smear and electro-less copper production line that provides Atotech’s customers with numerous production advantages, including excellent process performance due to an advanced fluid delivery system, reduced consumption rates for chemistry and water, and an operator-friendly design for best-in-class process control and maintenance.
Designed in Feucht, Germany, and built in Guangzhou, China, Atotech’s new POLYGON Line series features all production-critical characteristics and applies them to a highly reliable, high-volume, and cost-effective machine.
Employer award
In 2019 Atotech once again received a top employer award in Germany from the Top Employers Institute. Atotech’s focus was on employee development through talent management and training and development programs, leadership development, career and succession planning, and compensation and benefits.
Dirk Schepers, Personnel Manager of Atotech Deutschland GmbH, said “We are very happy about this special award as Top Employer. It not only rewards our aspirations and activities for ongoing employee development, but also reflects the outstanding achievements of our colleagues working and making Atotech successful. “
Annette Döring-Nahas, HR Business Partner at Atotech, adds: “We are particularly proud of our initiatives to digitize HR processes and roll out talent management programs that we will continue to invest in the future.” n
SOUND SLEEP SOLUTIONS
Smart technology and environmental commitment are driving success for mattress fabric specialist BekaertDeslee
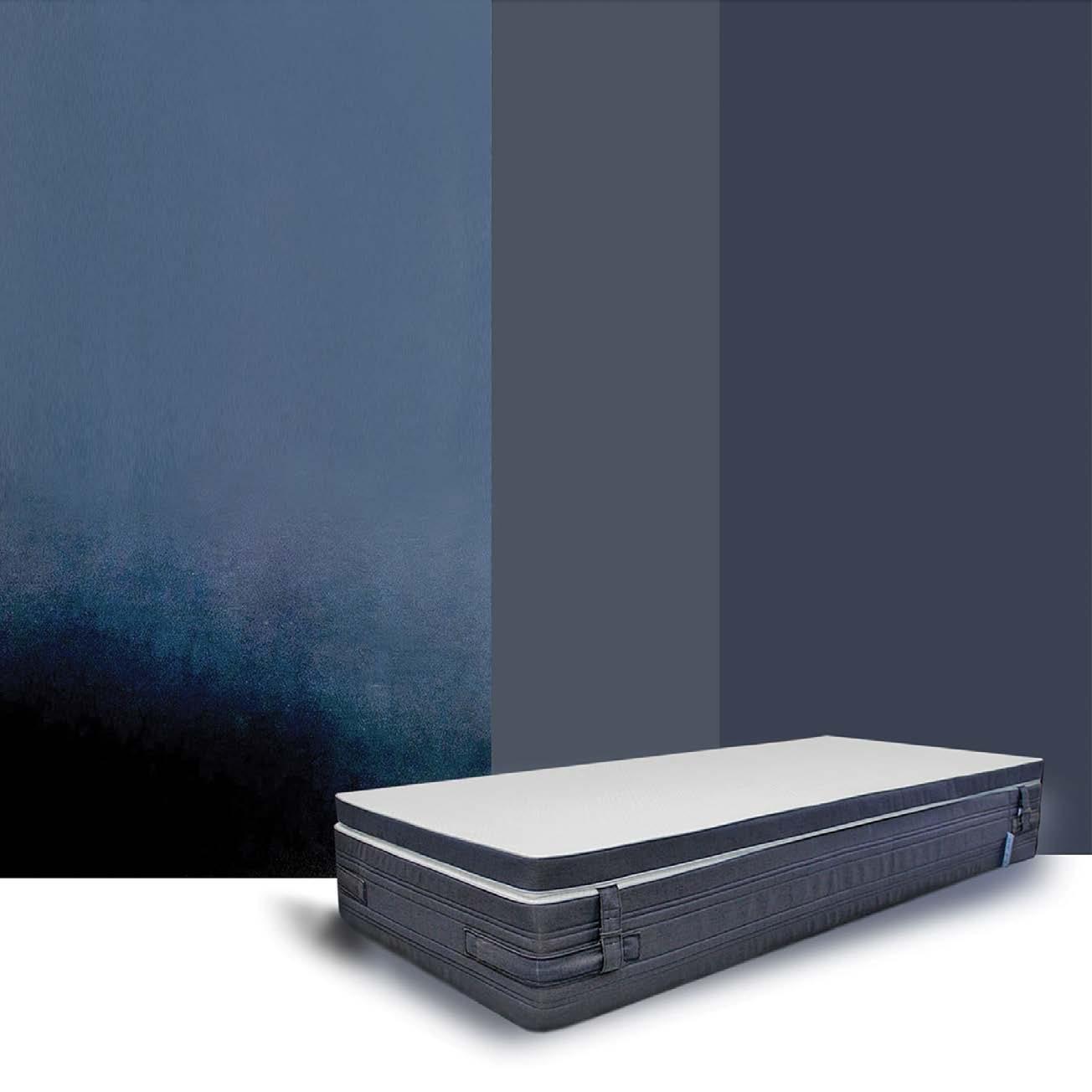
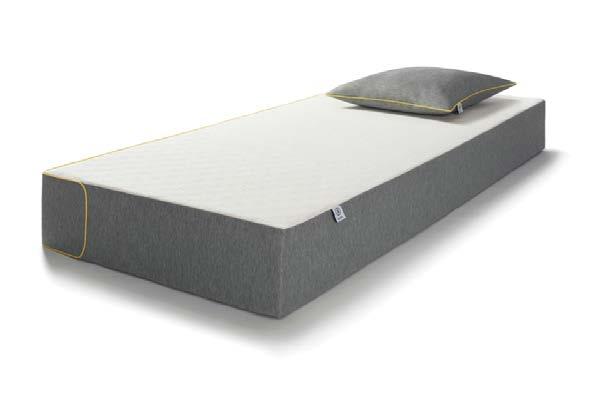
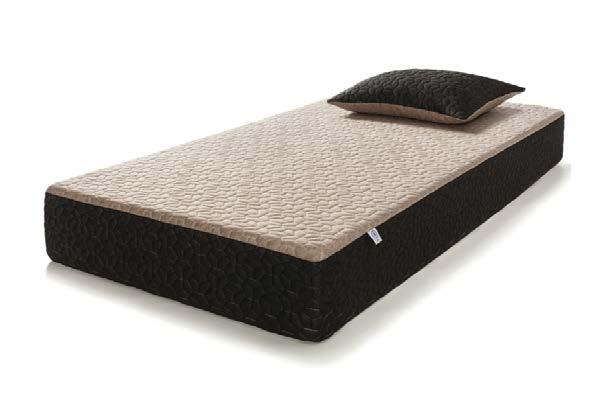
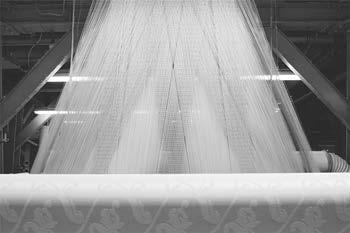
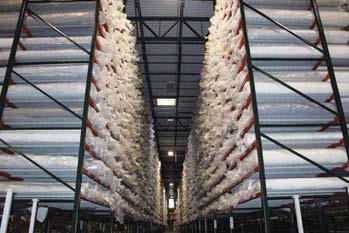
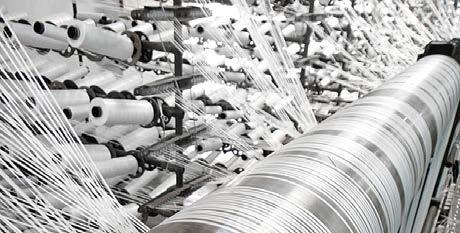
In 2018 BekaertDeslee, the world’s leading specialist in mattress fabrics and mattress covers, completed the construction of a new Innovation & Design Center (IDC) in Waregem, Belgium. The new, 3,575 m² building is located at Groenbek, a business area across the street from BekaertDeslee’s headquarters. The BekaertDeslee IDC is the “home” for the creative and technological heart of the group: the pilot plant, R&D, Engineering, Design, and Marketing & Communication.
“600 million people sleep on our fabrics every night. We spend years on research and development to improve their sleep quality,” said the company. “With the new IDC we are putting a bigger focus on innovation than ever before in order to transform the way we serve our clients, develop our people, and lead our industry.
“Through BekaertDeslee IDC, our nine business units are connected across the globe as one virtual network to scan the world for new trends in sleeping technology. This worldwide radar allows us to translate upcoming technologies into innovative products fit for the bed environment.”
BekaertDeslee IDC’s facilities include full production size machines, to enable the development of the latest technology in weaving, knitting and finishing. This fully integrated approach ensures all the company’s units worldwide get rapidly geared up for full production.
BekaertDeslee IDC is also home to BekaertDeslee Academy, a platform for open innovation, where suppliers, customers, scientists, universities and research institutes are able to engage with the company in the co-creation of unique products and services.
Merger of equals
BekaertDeslee was established in 2016 through the merger of two Belgium based textile companies, Bekaert Textiles and DesleeClama, creating the worldwide leader in mattress fabrics.
The new company brought together 19 production facilities worldwide and about 2,600 employees. Both companies have a long history in the Belgian textile industry. Bekhaert Textiles was founded in 1892 and Deslee Textiles in 1928. The global expansion of both companies accelerated in the 21st century with Deslee Clama opening new factories in Brazil, Romania, China and Estonia and Bekaert expanding its operations to China, Argentina, Mexico and Turkey.
“The Bekaert Textiles - DesleeClama deal fits both companies’ growth strategies and creates important new market opportunities, in particular the increased awareness surrounding the importance of sleep and the increased growth in the worldwide mattress market”, said a company spokesperson in 2016.
Smart solutions
BeekaertDeslee declares that change and continuous improvement are at the heart of everything it does, driving innovation in design, technology, services, communication and manufacturing.

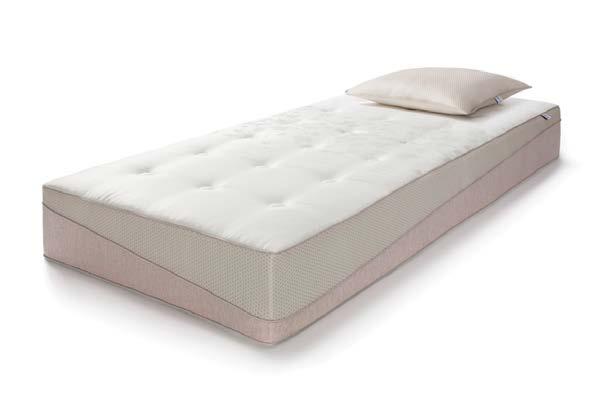
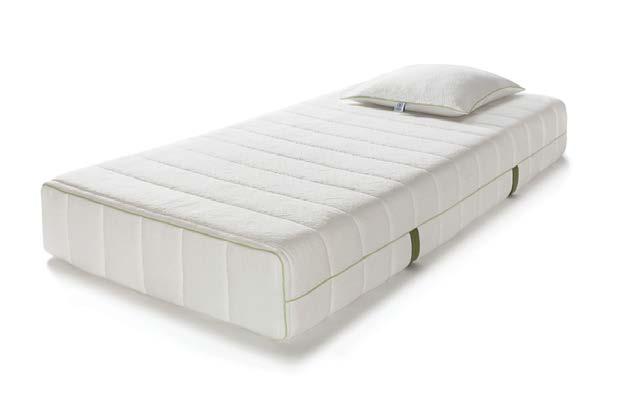
Its goal is to bring relevant innovation to the market, close to the customer, to meet the worldwide awareness that sleep is crucially important for health, mental wellbeing and performance.
BekaertDeslee ‘Solutions’ offers on trend “sleep solutions” for the consumer who is increasingly aware that quality time in bed is important. With cut & sew manufacturing units in the US, Mexico and Romania, the company produces ready-made mattress covers fitting customers’ exact and unique requests.
SmartSleeve®, for example, is a revolutionary mattress protector that optimises sleeping comfort, health and the hygiene of the mattress. SmartSleeve® combines three top technologies that offer the optimal conditions for a good night’s sleep. The fabric is knitted in a special 3D-structure (CAIRFULL) that permanently ventilates the mattress and reduces the pressure of the body on the mattress. SmartSleeve® also regulates the moisture level and temperature of the sleep environment while a probiotic biotechnology in the fabric keeps the mattress clean in a 100 per cent natural way.
BekaertDeslee also develops ‘smart’ textile solutions for healthcare markets through its Meditiss division. Here the main focus is on the welfare of young and old people who need to spend a lot of time in bed, either at home or in the hospital. The Meditiss products provide an answer to the most common causes of bad sleep such as dust mites and allergies, incontinence and heat and perspiration.
Supporting ocean cleanup
BekaertDeslee has recently announced that it is taking part in a massive ocean cleanup initiative – Seaqual.
Every year, 8 million tonnes of garbage reach the seas. 75 per cent lies underneath the ocean’s surface, forming an immediate threat to marine life. Governments, businesses and consumers share the responsibility to preserve the oceans for future generations.
The Seaqual™ organisation pays fishermen from the Spanish coasts of the Mediterranean Sea to collect garbage and bring it ashore. For this initiative, additional garbage harvesting platforms will be built in the Americas and in Asia. Each material, including aluminium, metal, glass or plastic, goes to its own unique recycling chain. Textile technology enables BekaertDeslee to take the plastics found in the ocean and upcycle them into new yarns that are used to produce its high-quality mattress textiles and mattress covers.
Awarding excellence
BekaertDeslee has been named ‘National Winner’ in the 2019 European Business Awards, one of the world’s largest business competitions. BekaertDeslee was chosen from 2,753 businesses named as Ones to Watch in a list of business excellence published in July and selected as a National Winner by a panel of independent judges including business leaders, politicians and academics. It is the best business in Belgium in the category Social Responsibility and Environmental Awareness and will now go on to represent Belgium in the final stage of the competition.
Adrian Tripp, CEO of the European Business Awards said: “This is a significant achievement and BekaertDeslee is an outstanding leader in its field. To be chosen as a National Winner means you show great innovation, ethics and success. It also means you are one of the best businesses in Europe. We wish BekaertDeslee the best of luck in the final round.” n
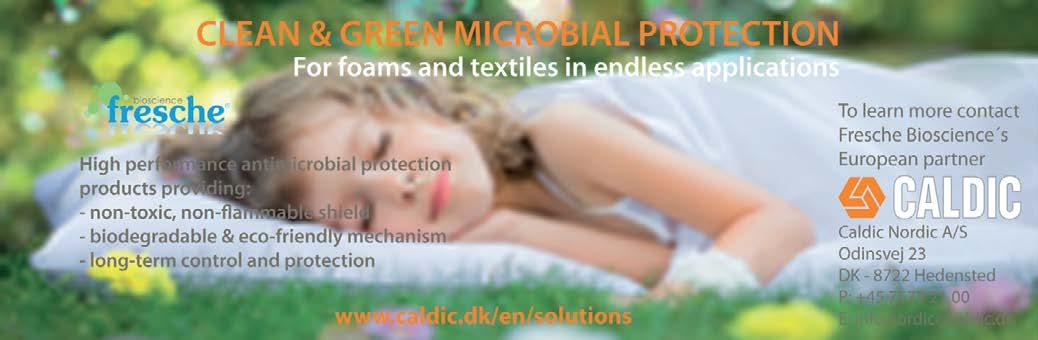

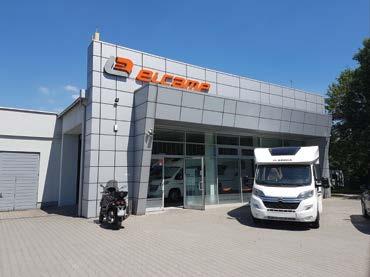
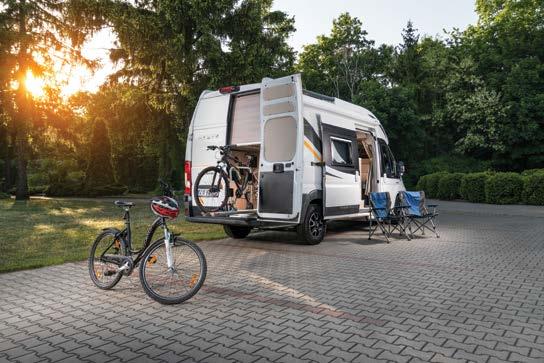

HOUSES ON WHEELS
The Elcamp Group, a company from Krakow, is Poland’s leading manufacturer of premium motorhomes under the Globe-Traveller brand. It is also a distributor of motorhomes and caravans of such famous producers as Hymer, Adria and Westfalia.
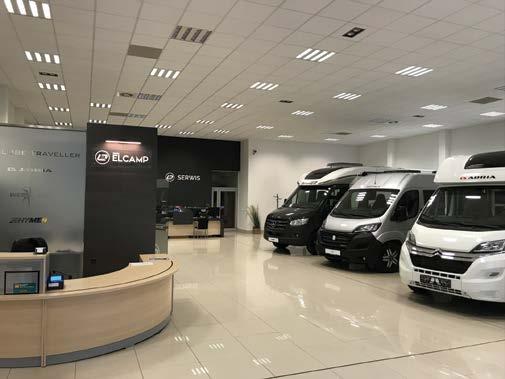
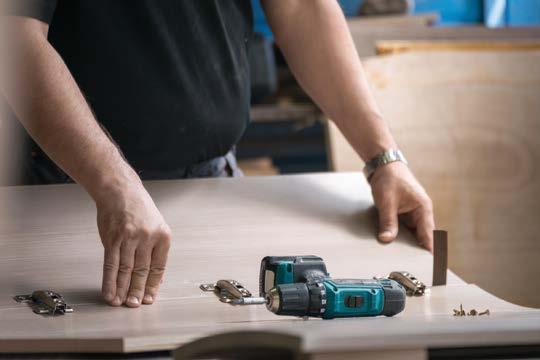

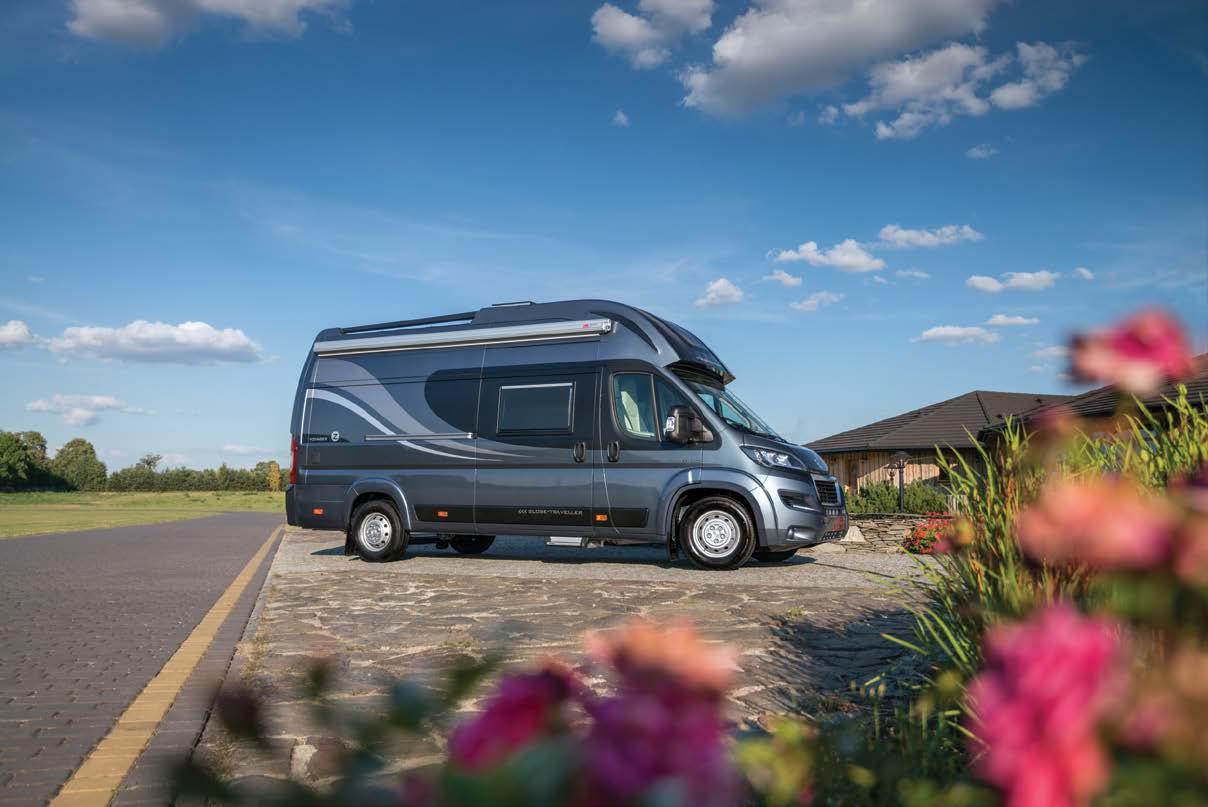

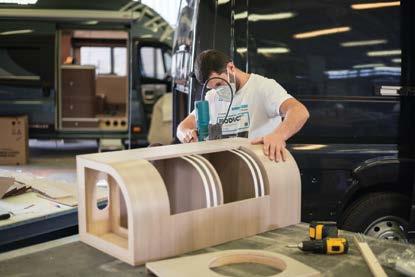

The Elcamp Group provides comprehensive maintenance services for motorhomes and caravans. It also offers full pneumatic suspensions, which are the most modern solutions among currently available on the suspension market. Finally, it runs a professional repair centre for damaged tourist vehicles.
“We are appreciated by our customers for the highest quality and timely implementation of even the most demanding maintenance services. We all love to travel by motorhomes and our goal is to create a place where fans of houses on wheels will be able to take full care of their vehicles in a friendly atmosphere, from consultancy, through the service to the purchase of parts and additional equipment for their vehicles”, explains Mr Andrzej Zawilinski, the group’s CEO.
Sport and caravanning
The Elcamp Group is a part of the Zasada Group, one of the oldest and biggest Polish corporate groups, bringing together more than 30 companies, in sales, production and services in Poland and throughout Europe. In total, it employs more than 3,000 people.
The Zasada Group was established by Mr Sobieslaw Zasada, one of the most successful Polish sportsmen of all time, who after a sporting career successfully turned to business. As a rally driver he won the European Rally Championship three times (and was the runner-up three more times) at a time when the European champion was in fact the world champion. Furthermore, he was Rally Champion of Poland 11 times and in his entire sports career he has won more than 150 rallies all over the world.
Mr Zasada is an avid fan of caravanning, which helped the Elcamp Group to develop. The company has been operating since 1996 and offers a whole range of motorhomes and caravans: from small vehicles “Westfalia”, through “Adria”, “Carado”, luxury “Hymer” and “Eriba”. In 2011, it opened in Krakow a new facility with a six-storey service hall, a shop with camping accessories, a car wash, a spacious and convenient parking lot as well as a camper park, where guests from all over the world can stop and stay overnight.
Icing on the cake
“Our flagship product is the Globe-Traveller camper van, which is made entirely by ourselves and has been on the market since 2009. It is an exclusive vehicle from the market’s premium segment, based on the Fiat Ducato or Peugeot Boxer chassis and handcrafted using the best quality components in our workshop in Karczew, near Warsaw. In terms of aesthetics and the sense of space, our vehicles resemble yachts or luxury liners. Standard equipment is the most comprehensive available on the market”, points out Mr Zawilinski.
The way Elcamp makes camper vans is not a on typical assemblyline. At each step of the process, the uniqueness of each motorhome is considered; all details are adjusted so that the whole construction is complete, and everything perfectly fits together. The company operates its own carpentry shop where furniture for each vehicle is made; it also has as well a technology and design office.
Since the Globe-Traveller is a premium camper van, its standard equipment includes several components, which in the case of other manufacturers, are on the list of extra options. Electric step, passenger airbag, leisure battery, heating, skylights, ‘turbo vent’ are just a few examples of what is included in the base equipment. For those customers who wish their camper van to stand out from the others, the company offers a long list of optional equipment to allow true personalisation of their motorhomes. Leather upholstery, leather steering wheel and gear knob, automatic air conditioning, GPS navigation, solar panels, TV set with satellite receiver, and many more options are available.
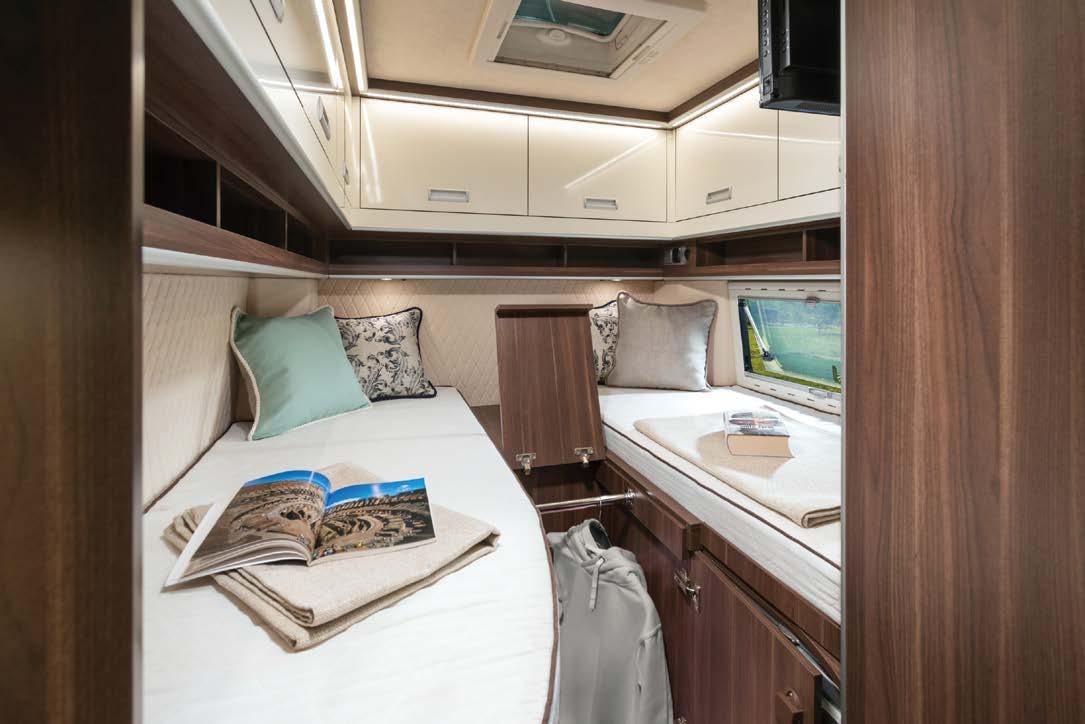

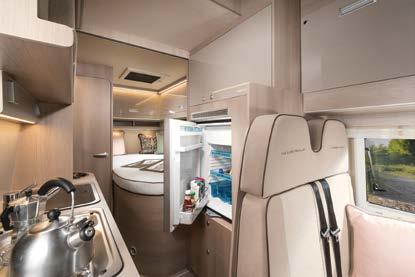
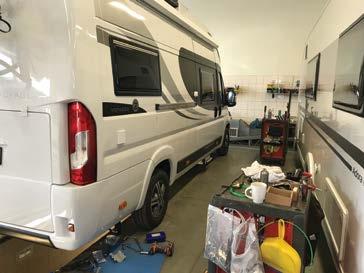
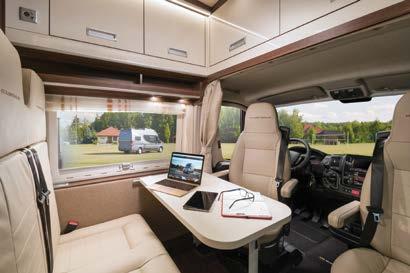
Strong European market player
The company employs more than 60 people, primarily a team of professionals and enthusiasts who genuinely love what they do. The Elcamp Group’s annual sales reached more than €10 million in 2018; its production output in 2018 was 150 vehicles, while in 2019 it is estimated as 180-200 units. Most of the production goes abroad. In recent years annual foreign sales have totalled 100-130 vehicles. Such European countries as Sweden, Norway, Denmark, Germany, Switzerland, France, Belgium, the Netherlands, Czech Republic, Romania and Hungary are the Elcamp’s main foreign markets.
“We have a wide group of regular customers and an increasing number of new owners of campers and caravans who trust in our team. Interestingly, we have also a group of younger customers who quickly got bored with the traditional kinds of tourism and turned to motorhomes to be able to take active holidays. They prefer to visit many interesting places instead of lingering in one place”, says Mr Zawilinski.
The market success of Elcamp has not encouraged the company to rest on its laurels. It intensively invests in its further development, e.g. recently it purchased the latest design computer software; it plans to build a new production facility to increase capacity. It also is preparing to expand the range of engines used in its camper vans (currently they are diesel engines) with ecological engines that are the future of mobility. n
Visit: www.elcamp.pl Visit: www.globe-traveller.eu
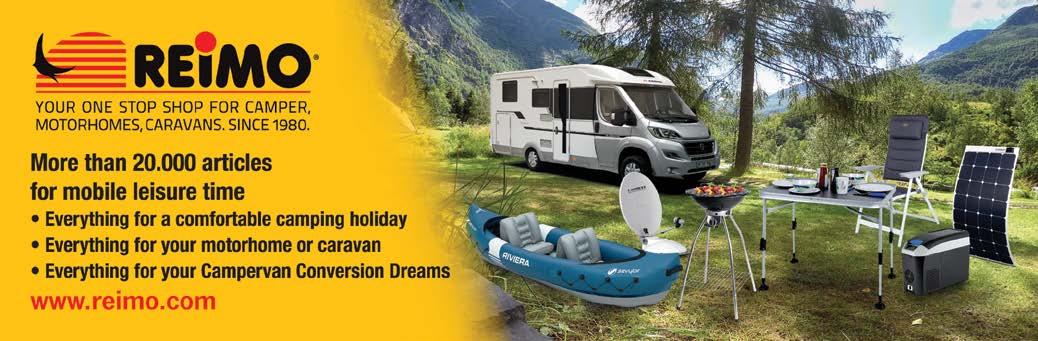
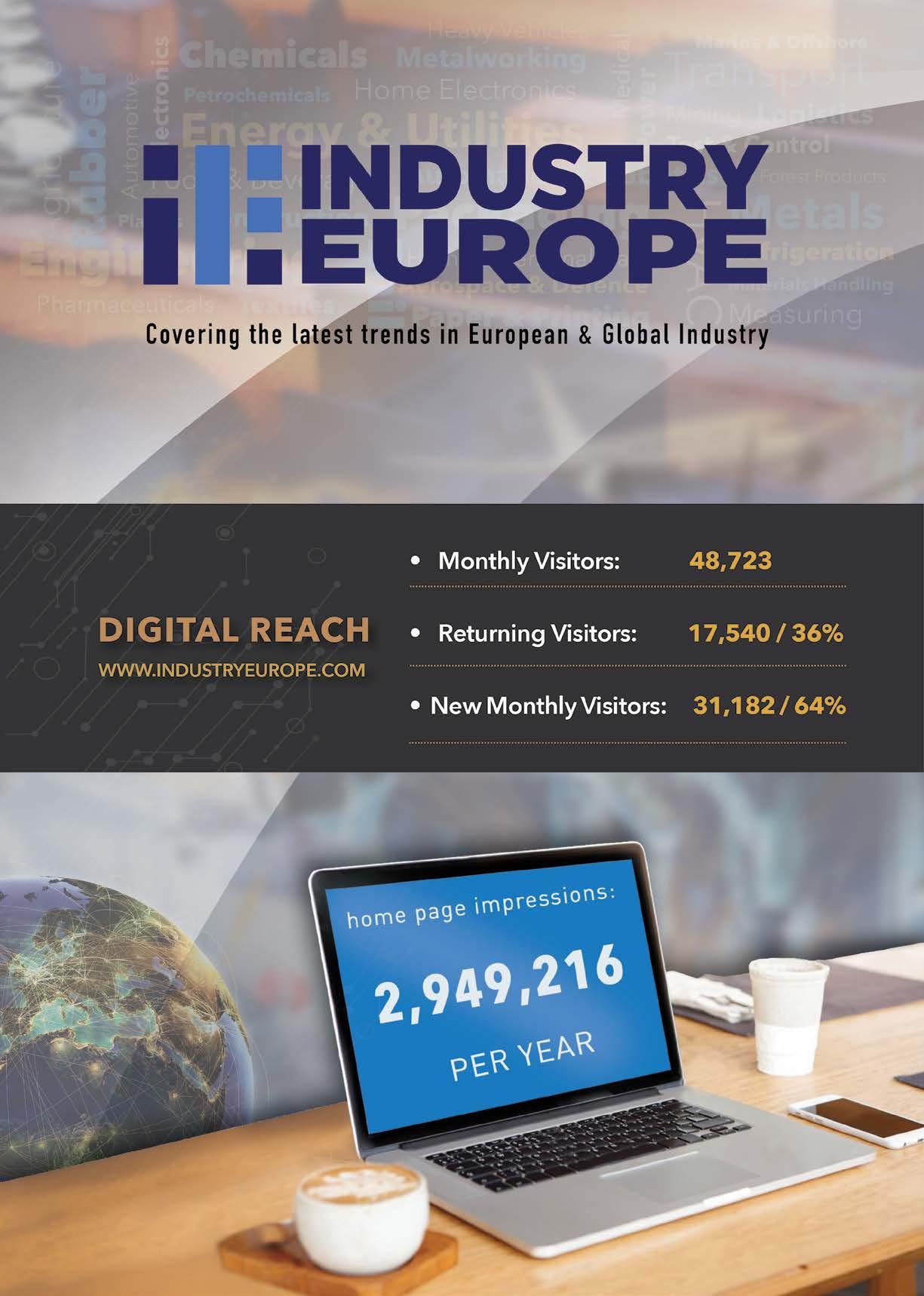
ADVERTISERSINDEX
Ahlstrom Munksjo Ahlstrom-Munksjo AkzoNobel Alfaplast Angelico Archroma ATD Cardox
Ballerstaedt Birla Cellulose BOPP Brevis
CAAC Pioneer Logistics CAEM Chimar
DMN Westinghouse
Eko-Chemia EMB Ergon 79 148 108 102 197 Outside Back 94 Industrial Technics Intermarc Investkonsult Sweden 134 186 24
Janus Vaten 186 Jujun Mechanical Technology 121
170 17 144 131 Kemcolor Kindlimann Knorr-bremse Kraton 181 192 70 52
44 128 189
82
117 111 185 Langzauner Liberty Ostrava Lubrizol Lumson
37 61 52 168
Nidec NLMK 165 Inside Front
Optima Packaging Group Inside Back SMAG SMT Technologies Soulis Kuehnis Swedev
Technoform Teknosavo Tenzana TES Technika Thermasys Tubing TSE
40 121 173 164
98 156 49 99 73 67
Wibax 157 Windmöller & Hölscher Machinery 153
Zetterstroms 144
FEPAC Frana Polifibre Fresche Bioscience FTS Drytec
44 178 203 200
Geo Globe Polska 90 GFE Metalle und Materialien 137 Green Group 178 Guarniflon 141 Gutmann Aluminium Draht 73
HS Umformtechnik 82 PMG Prokom
Reimo Reitz India Rekopol Renolit
Saia-Burgess Controls Senator International SIG S.I.P. 56 64
206 86 117 105
192 53 86 125
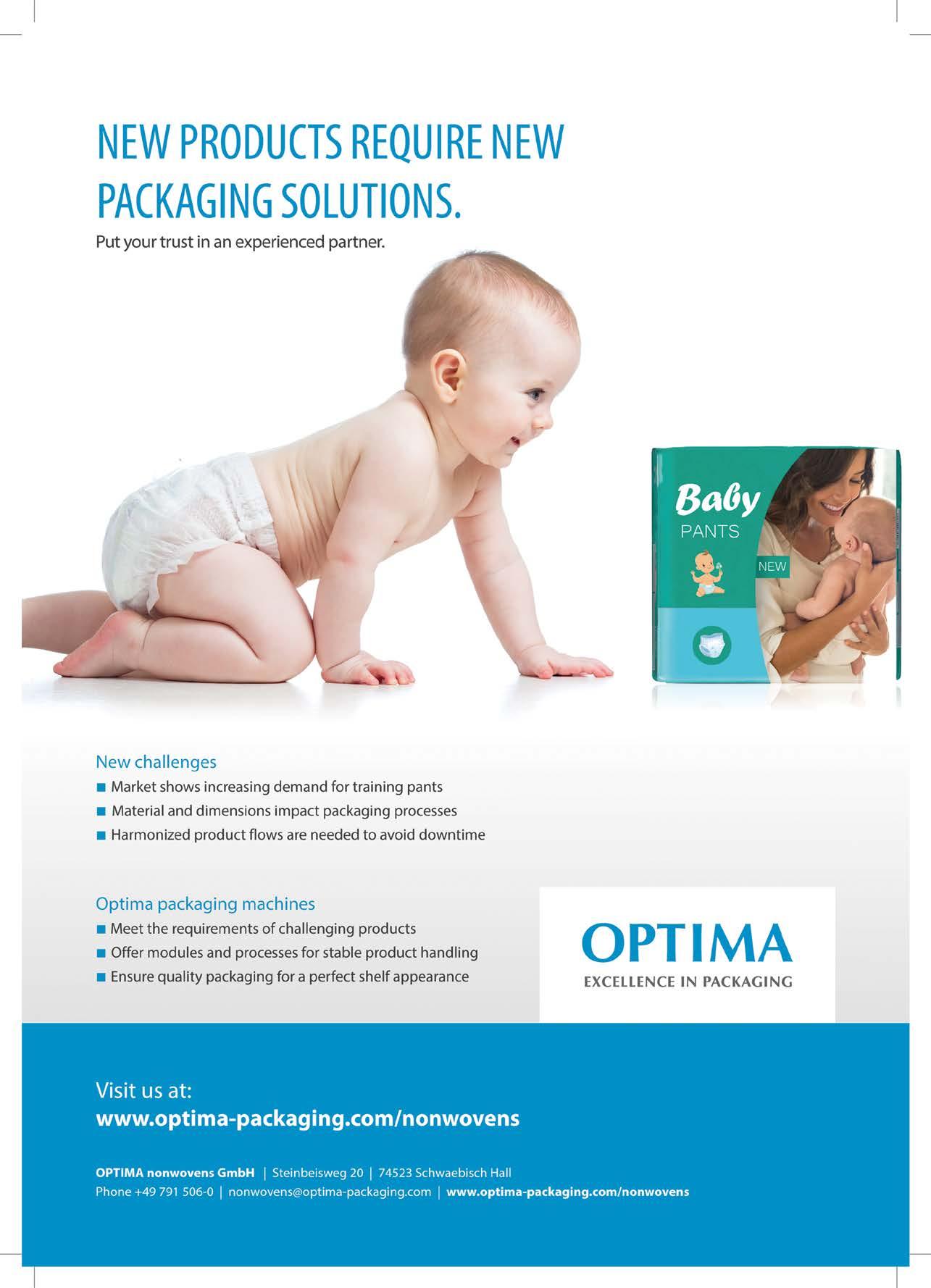
