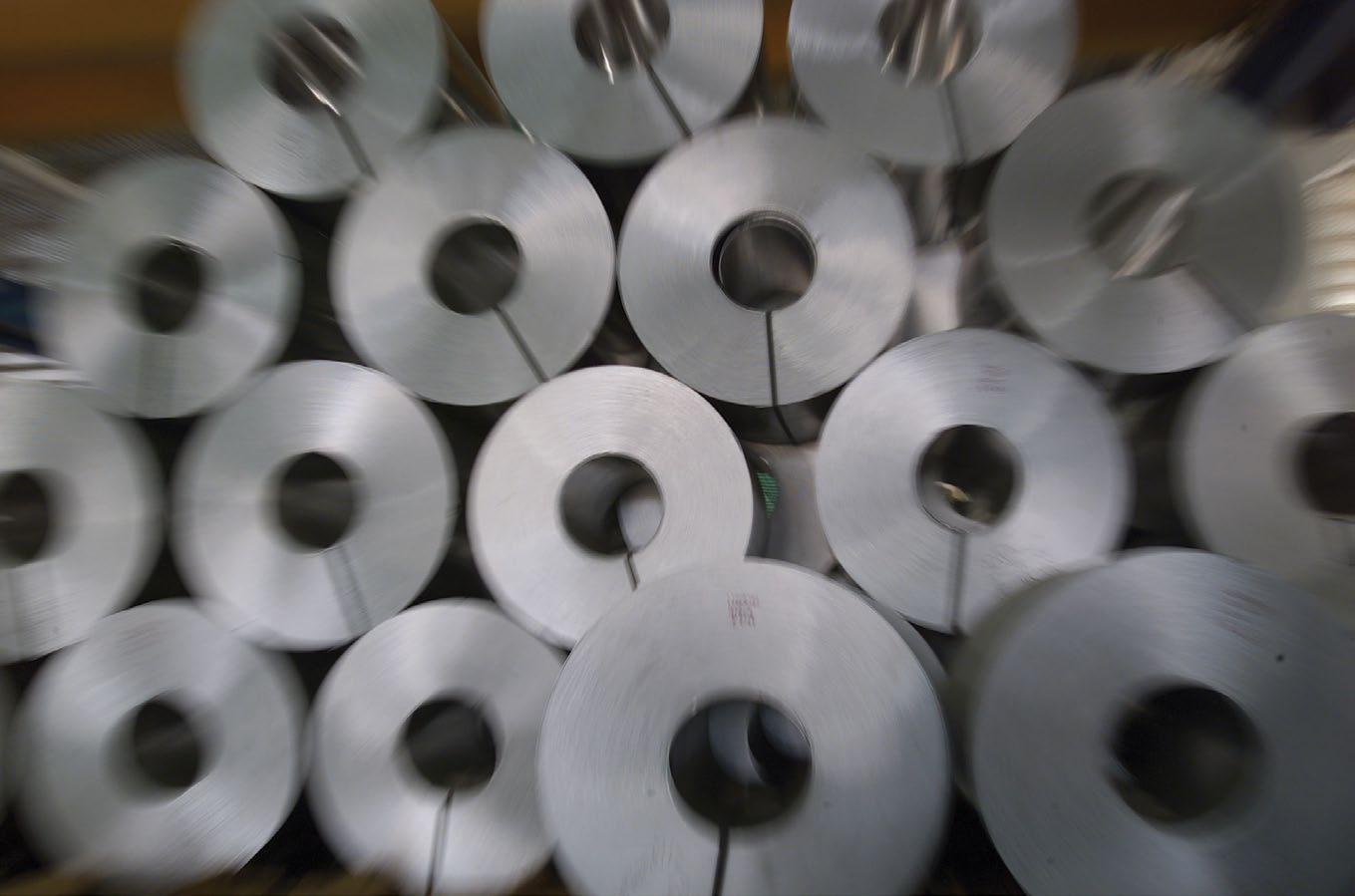
4 minute read
Same values, new profile Profilglass
saMe values, new profile
With a new image, Italy’s Profilglass is highlighting its continuing diversification and innovation in the aluminium industry
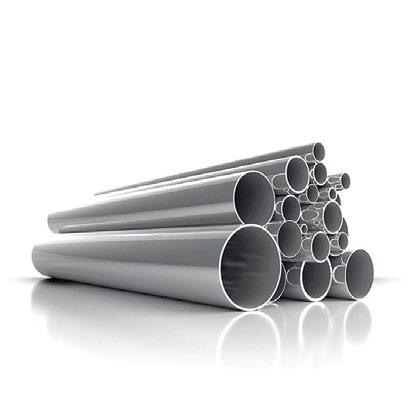

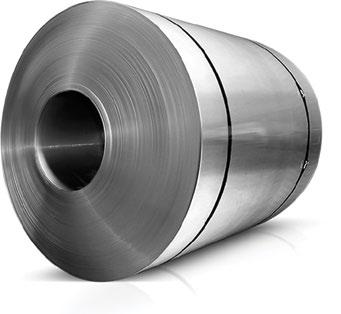
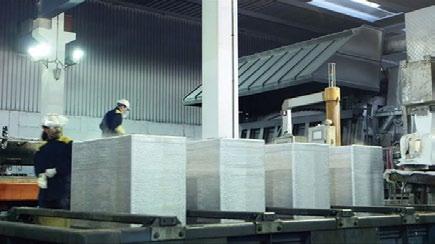
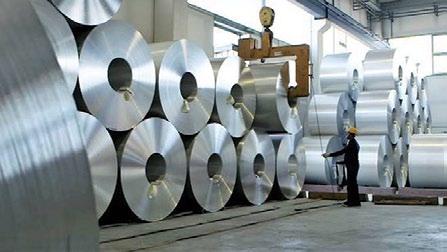
In June 2019 Profilglass, the Italian specialist in aluminium profiles and flat rolled products for the construction, automotive, electronics and household appliances industries, launched a new company logo and a new motto – ‘People, Passion, Aluminium’.
The new image represents both the company’s long experience of producing the highest quality aluminium for almost 40 years as well as its growth into a major group employing almost 1,000 people and exporting to almost 90 countries around the world.
“‘People’ stands for our conviction that our success rests upon our commitment to always working closely together as a cohesive team and also for our close relationships with the local community,” the company explains. “‘Passion’ declares our constant commitment to our work and our continuous investment in research and technology. ‘Aluminium’ is, of course, the heart of our history and, we believe, the metal of the future.”
Diversification strategy
Founded in 1982 in Fano, in Pesaro-Urbino, by brothers Giancarlo and Stefano Paci, Profilglass has expanded and diversified its business. Originally it produced spacing and decorative profiles for double glazing units but, especially since 2000, it has also established a significant presence in the flat rolled products industry, supplying customers in the construction, automotive, electronics and household appliances sectors
Today the company processes over 250,000 tonnes of aluminium every year and has established itself as major player in the international aluminium industry, currently exporting to more than 85 countries worldwide.
The spacing and decoration profiles for double glazing that have characterised Profilglass since it was established continue to represent a major part of its production. But these are now complemented by a wide range of flat rolled products.
Profilglass’ current range of flat rolled products includes discs, sheets, strips and bands that can be supplied to deliver tailor-made solutions to a wide variety of industries. The company’s roughturned and plate warehouses contain an average of 30,000 tonnes of material at any one time; together with its rapid production capability this stock ensures flexible and timely delivery to all customers.
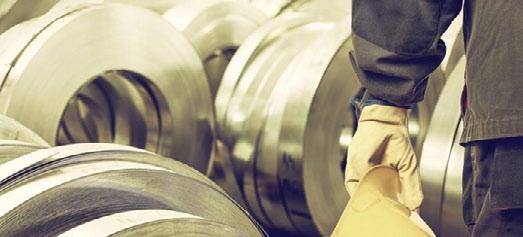
Advanced production processes
Profilglass’ foundry section is equipped with modern plate pouring furnaces and state-of-the-art degassing and filtering systems which guarantee high quality standards.
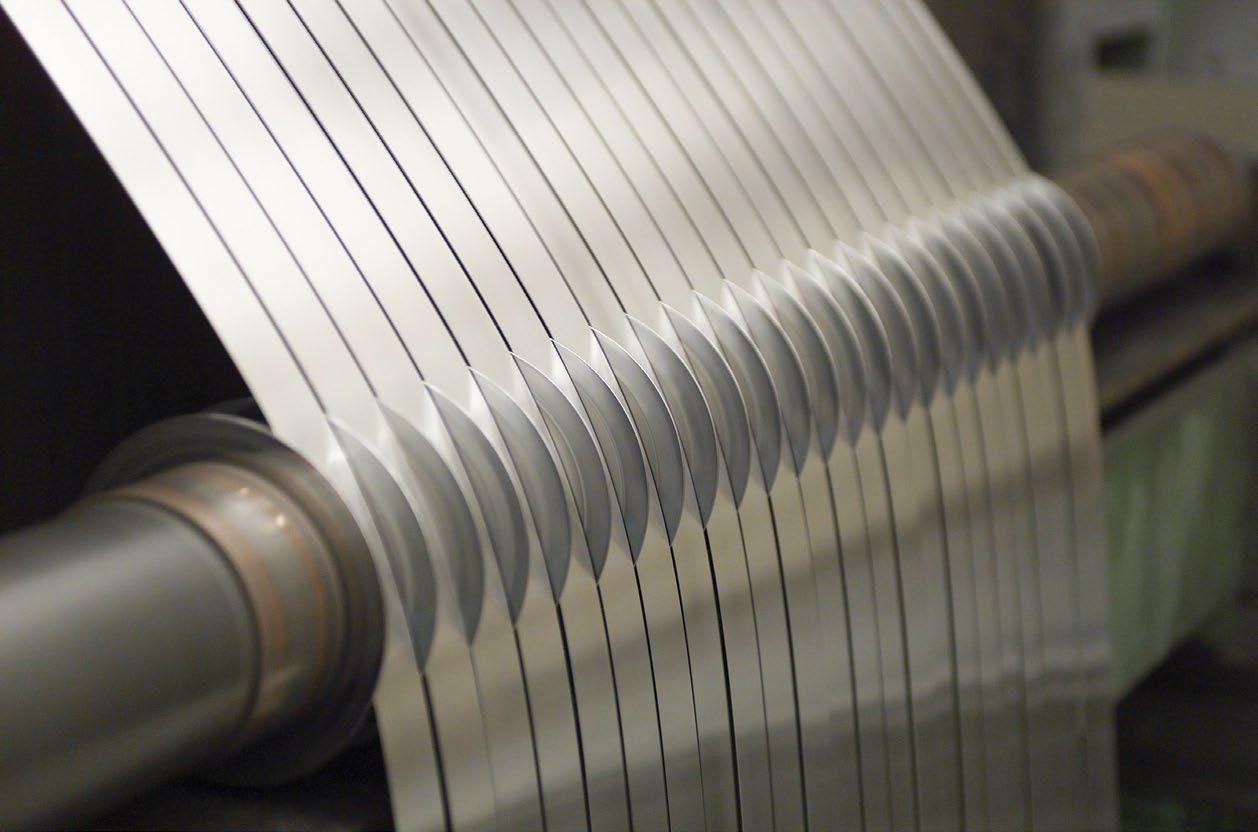
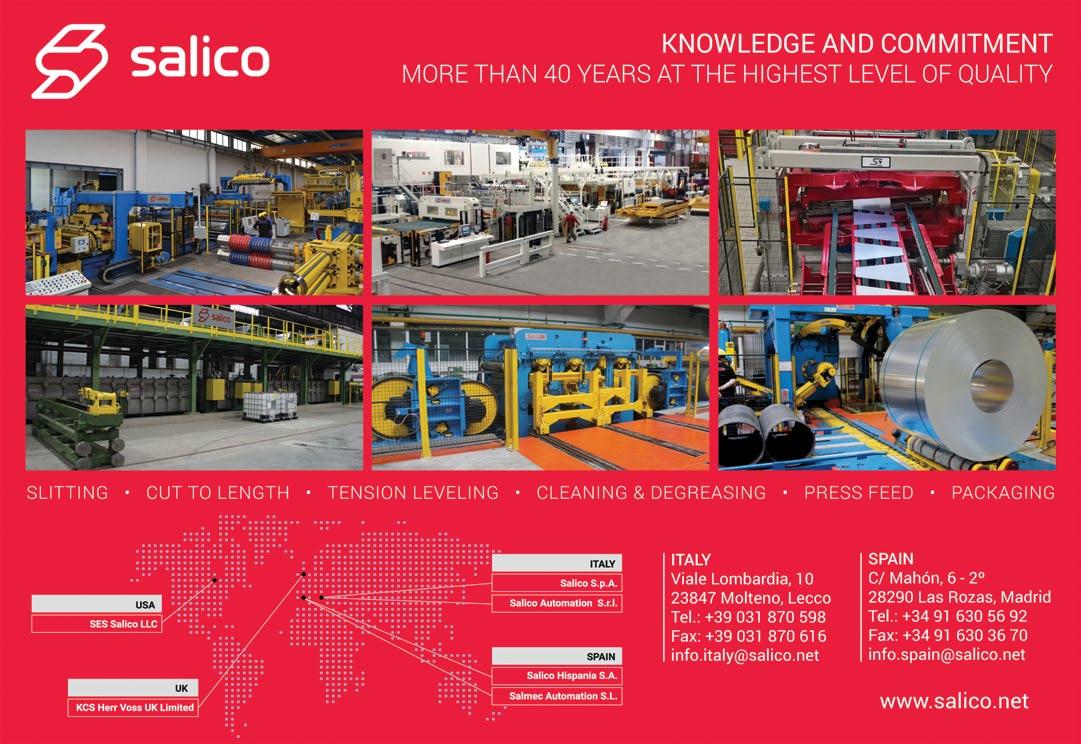
The six lines for continuous casting at Profilglass are fitted with furnaces using innovative liquid metal treatment systems which allow for perfect homogenising as well as degassing and filtering devices which ensure the correct quality standards in aluminium.
The company’s hot rolling mill is designed for the hot lamination of about 150,000 tonnes/year of aluminium plates up to 4 mm thick. The coils obtained from intermediate forging, continuous casting or bought from others, can then be processed in four cold rolling systems, where they reach the thickness required by the client, from 8mm to 80 microns. Equipped with efficient automation systems to control the process, thickness and planarity, these reversible and single-direction installations can reach a production capacity of about 180,000 tonnes/year.
After lamination, the aluminium undergoes heat treatments which give the material the necessary mechanical characteristics for processing during the finishing phases.

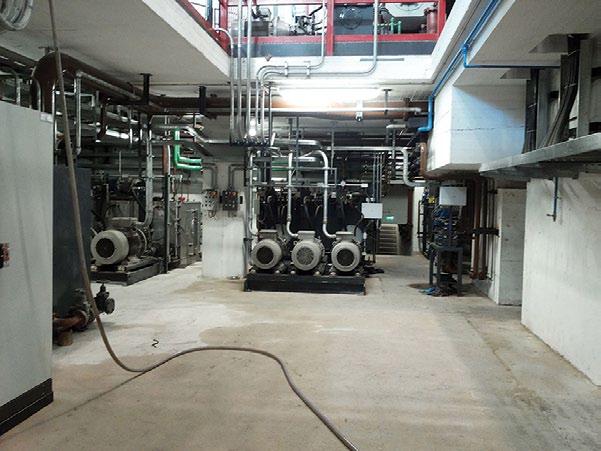
The aluminium cycle at Profilglass is then completed by various kinds of annealing - partial, complete or homogenising - in ten dedicated furnaces, which allow for precise and accurate temperature control and, thanks to the inert atmosphere inside, preserve the typical sheen of aluminium.
Three degreasing, alkaline and electrochemical lines carry out surface treatments to improve the material’s performance levels, for example by facilitating the adhesion of coatings/paints or decoration and protecting it against corrosion to preserve its appearance over time.
The finishing phase is the pride of Profilglass, As many as 20 machines ensure the production of belts, slipped coils, discs, metal sheets, strips, ovals or triangles with the utmost cutting accuracy and exact compliance with the tolerance values, no matter how small, required by final customers.
Specialised companies
Profilglass’ aluminium tubes and pipes are produced by Eurotubi, a company within the group that specialises in items for the home furniture, garden, sport and leisure, and healthcare markets. With a large number of profiling machines, the company is a leader in the production of electrically welded aluminium pipes in different alloys and sizes from 5 to 70 mm in diameter.
Established in 2017, LamiAl, is a new company within the Profilglass group that specialises in the production of aluminium flat rolled products for automotive, transport and industrial applications. LamiAl’s advanced technologies enable it to process materials to the very highest standards throughout the production process, from cold-rolling of aluminium to finishing and surface treatment.
Committed to sustainability
Aluminium, Profilglass’s raw material, is, of course, 100 per cent recyclable but the company has also developed a comprehensive range of sustainability policies over the years, with a strong commitment to managing its resources in a responsible way.
A huge advance in making the company’s facilities as environmentally friendly as possible was achieved by the installation of a large-scale photovoltaic system on the factory roofs. This solar system has a power capacity of 16.2 MWp, enough to meet the energy requirements of more than 4,500 households. n
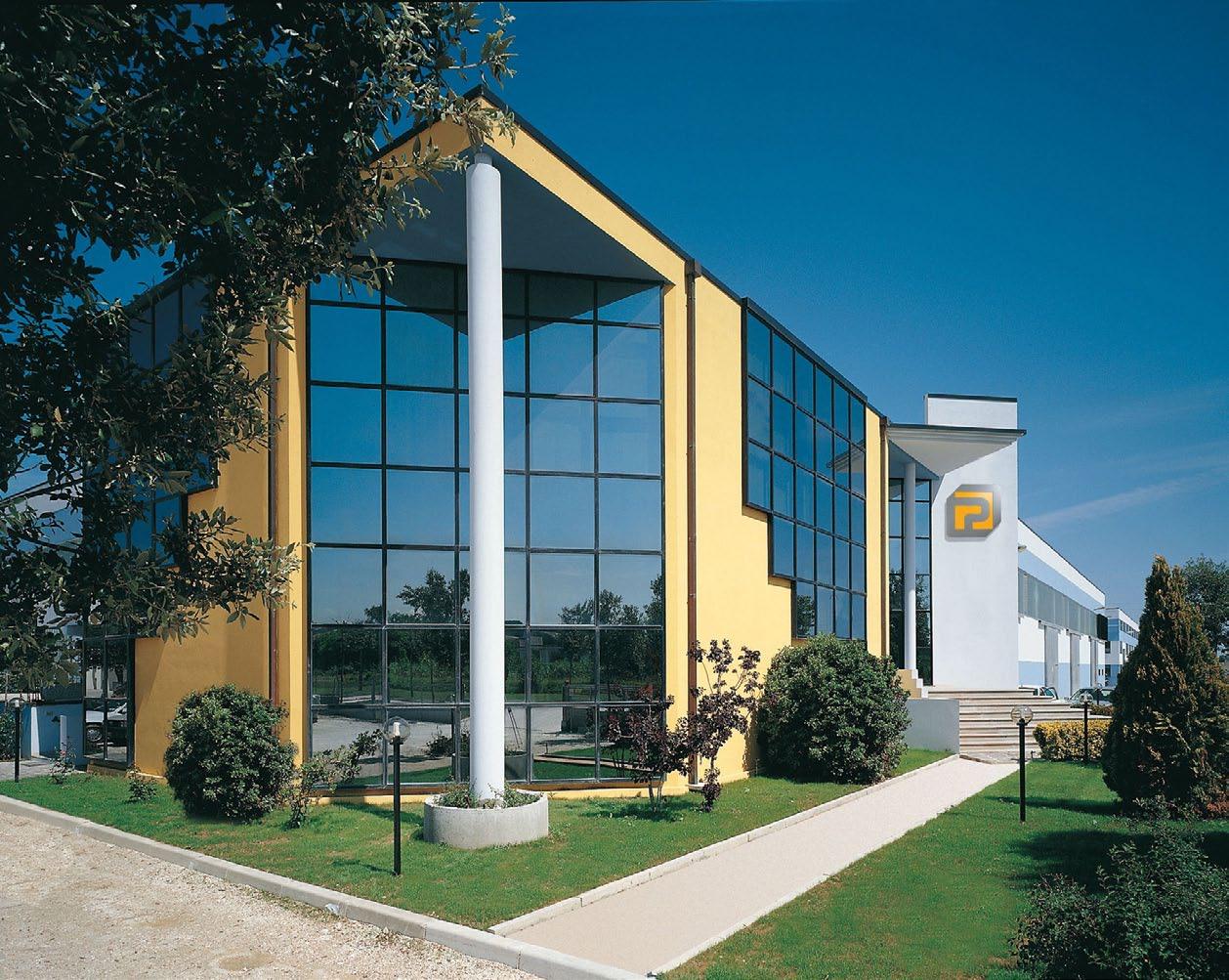