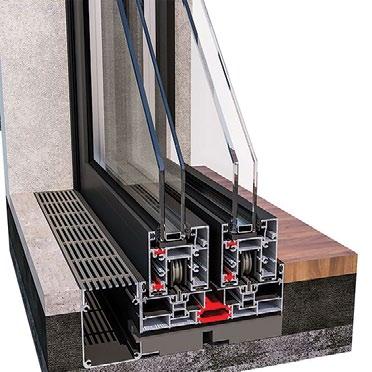
5 minute read
Innovation in aluminium extrusions Exalco
innovation in aluminium extrusions
Exalco S.A. continues to invest in the advanced technology that has made it one of Greece’s most important industrial enterprises

Exalco is not only one of the major players in the aluminium profiles industry in Europe, it is also one of the largest industrial companies in Greece. It is therefore committed to continuous investment in the latest technology to develop innovative solutions for its customers throughout the construction industry as well as to optimising its own production processes.
This commitment was evident in the company’s decision to invest in renewable energy systems with the installation of a 500 kWp solar array at its factory in Larissa, in the Thessaly region of Greece. More than 1,750 Hanwha Q.PLUS-G4.3 multicrystalline solar modules were installed in just two months in Summer 2018 by the Greek solar distributor and EPC Company Active Energy Solutions.
These 60-cell modules boast a power capacity of up to 290 Wp and offer a versatile and reliable solution to customers looking to generate long-term yields. The modules deliver excellent performance even in low-light conditions and harsh climates – making them even more effective in the fierce sun that shines on the Exalco plant’s rooftop for most of the year.
Exalco S.A. has been at the heart of the Greek aluminium industry since it was established in 1973. Today it is an integrated industrial operation producing aluminium profiles for all modern structural and architectural needs. It has developed an extensive sales network in both its domestic and its foreign markets and holds the leading position in the field of Greek aluminium extrusion.
As well as its main production plant at Larissa, Exalco also operates two subsidiary companies outside Greece - Exalco Romania SRL in Bucharest and Exalco Bulgaria SRL in Sofia.
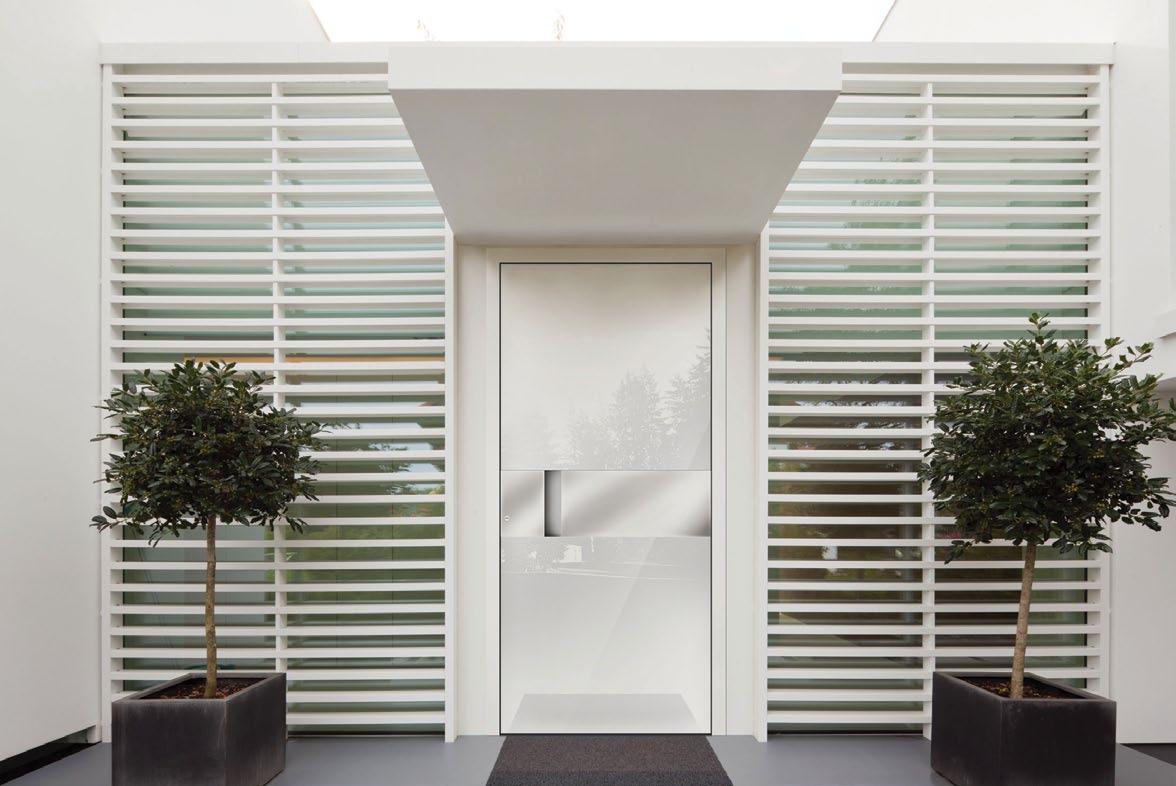
Advanced production
The production facilities at Exalco’s 52,228 metres squared Larissa plant comprise five extrusion presses (of 1,100 tonnes, 1,600 tonnes, 1,750 tonnes, 2,200 tonnes and 2,840 tonnes respectively) with a total annual production capacity of 45,000 tonnes, as well as a section producing extrusion dies. Just over a year ago a new KAUTEC extrusion line of 1,700 MT force for 7” billet was installed and successfully started up at the Larissa plant.
The plant’s fully automated surface processing and anodising unit has a capacity of 6,000 tonnes annually and a new INOX colour anodising unit has a capacity of 9 tonnes daily. Coating facilities include a vertical system unit producing 10,100 tonnes annually and a horizontal coating system unit producing 5,000 tonnes annually as well as a powder coating system unit for wood and imitation marble with the V.I.V. DECORAL method.
Exalco’s current product range includes aluminium profiles for general structural and industrial applications, aluminium systems (ALBIO) for doors, windows, building facades, atriums, and many other architectural constructions, aluminium Shading Systems (Albio Solar) and aluminium Railing Systems (Exrail System). The company also produces aluminium Composite Panels EXALCOBOND, aluminium systems for support bases and aluminium frames for photovoltaic parks, rooftops, roofs and industrial roofs.
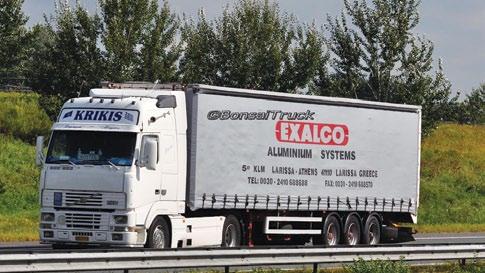
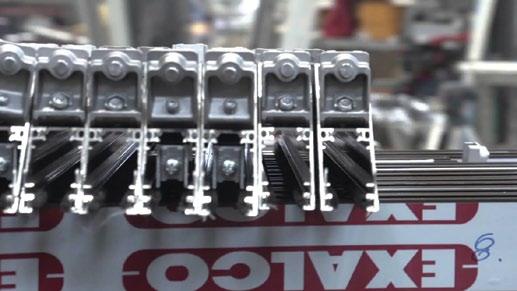
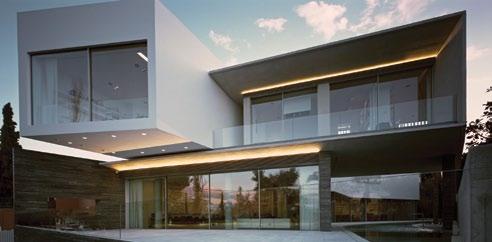
Innovation continues
Among Exalco’s latest products is a new aluminium system for entrance doors, Albio 135 Super Thermo. This system, which breaks new ground in the European extrusion industry, offers the highest insulation (Uf = 0,6 w/m2K), compared with corresponding systems, and sets new standards in any new building or renovation project. It also ensures maximum protection thanks to a quad-locking mechanism which ensures burglary protection and security. It can also support new door technologies such as fingerprint recognition, digital insertion codes etc.
Another new innovative product is ORAMA, a sliding system for doors and windows featuring a minimal 2 cm vertical profile to give a sense of freedom, together with excellent thermal qualities.
Exalco has also invested in one of the most exclusive production process technologies in the world. This is a new machine which
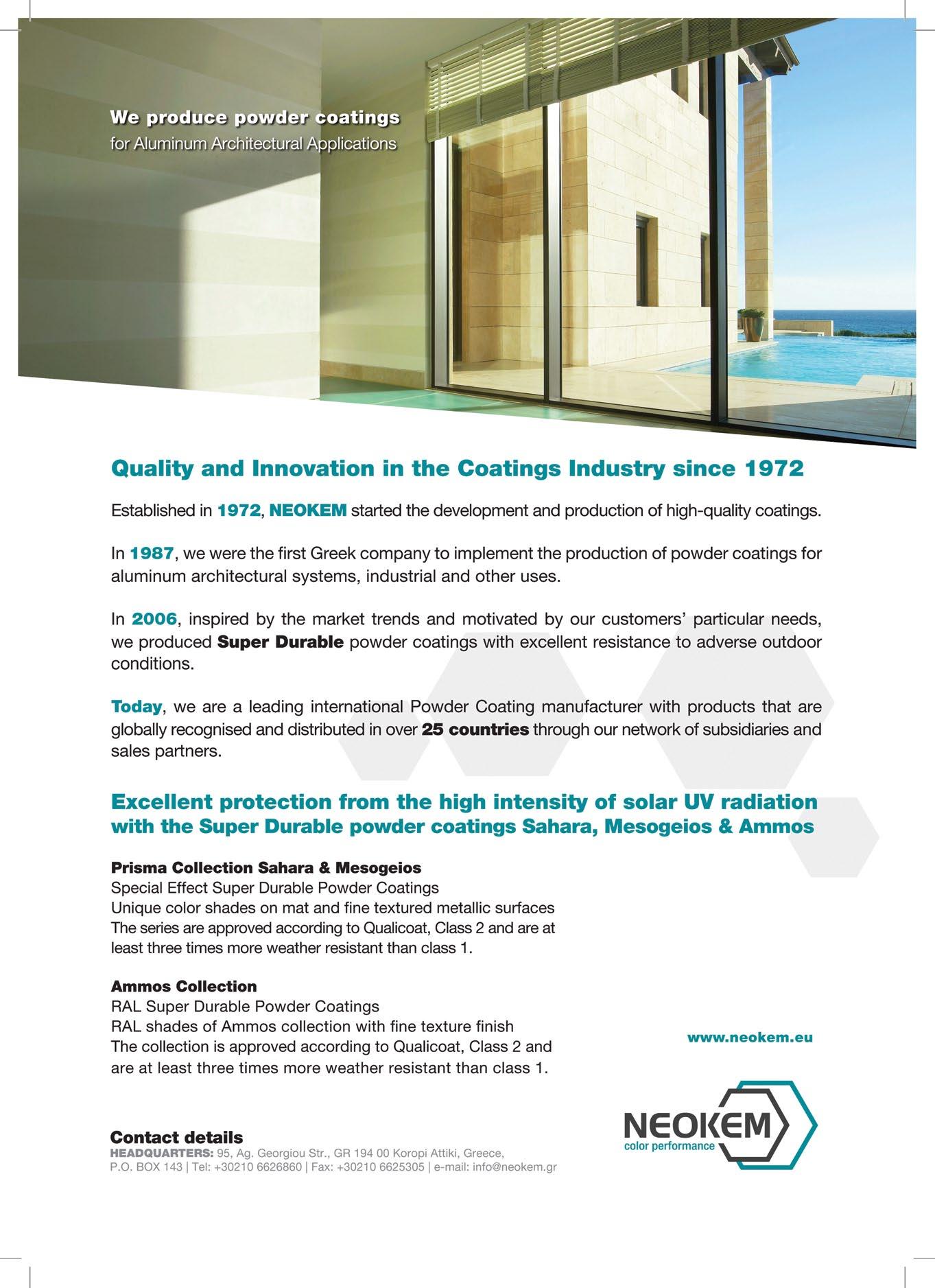
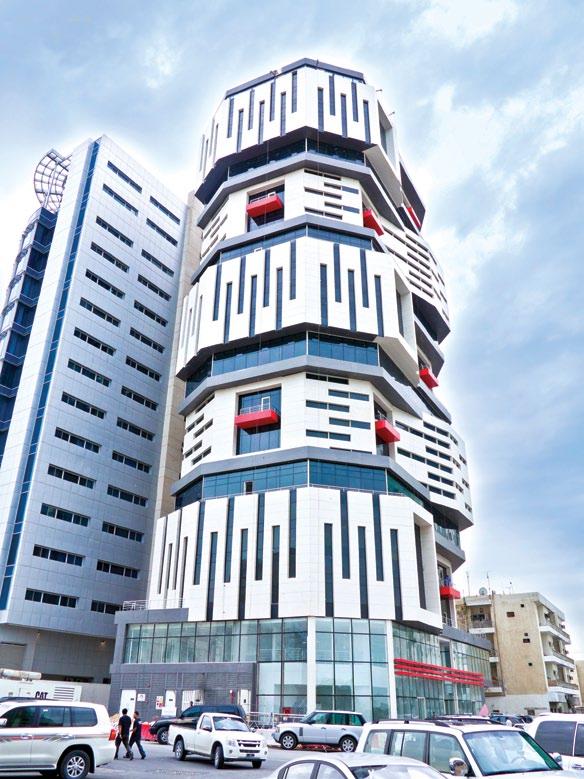
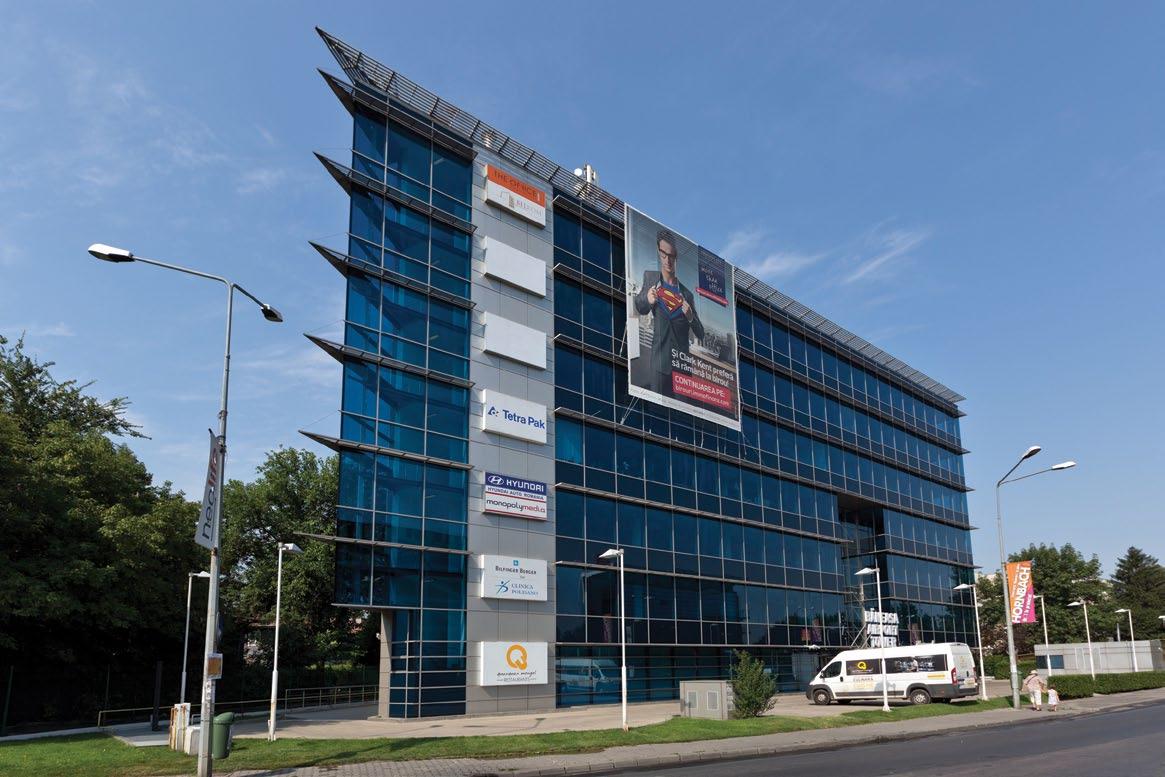
applies a special rubber double extrusion directly on to the profile to ensure a perfect fit and the complete sealing of the frame. This integrated product significantly reduces the installation costs and construction times of window frames. Exalco is the only company worldwide that owns this technology.
Projects across the world
For some years after its foundation Exalco focused on meeting the needs of its domestic market in Greece. Soon, however, the reputation of its products led to a much increased export activity and brand awareness worldwide. Today it exports 75 per cent of its production to five continents.
Its strong presence in the Balkans is established through its subsidiaries in Romania and Bulgaria but today Exalco extrusions can also be found in countries throughout the world, including France, Nigeria, Canada, America, Saudi Arabia and the United Arab Emirates. From the huge glass Ehgo skyscraper in France, to the ING office building in Bulgaria and from the Cargo Airport in Qatar to the Tadawul skyscraper in Saudi Arabia, Exalco has delivered its technologically advanced extrusion products to major construction projects of all kinds.
This January, Exalco was awarded the most important prize by the Hellenic Business Association, the leading Greek institution in the field of entrepreneurship. For the 19th time, the Athens Chamber of Commerce and Industry honoured business excellence, its values and corporate success stories. Exalco was recognised for its unrivalled export activity and its international presence. In fact, Exaclo is responsible for 30 per cent of all Greek exports.
The grand opening ceremony of the UEBA 2020 Awards took place at the Athens Concert Hall in the presence of Greek President, Prokopis Pavlopoulos, and the Minister of Development and Investments, Adonis Georgiadis. n
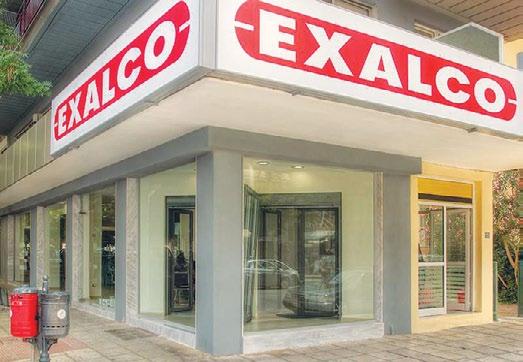
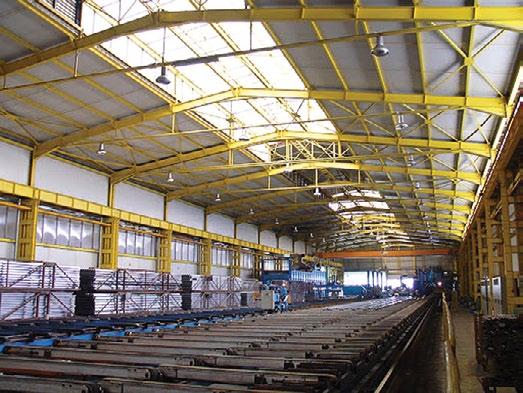