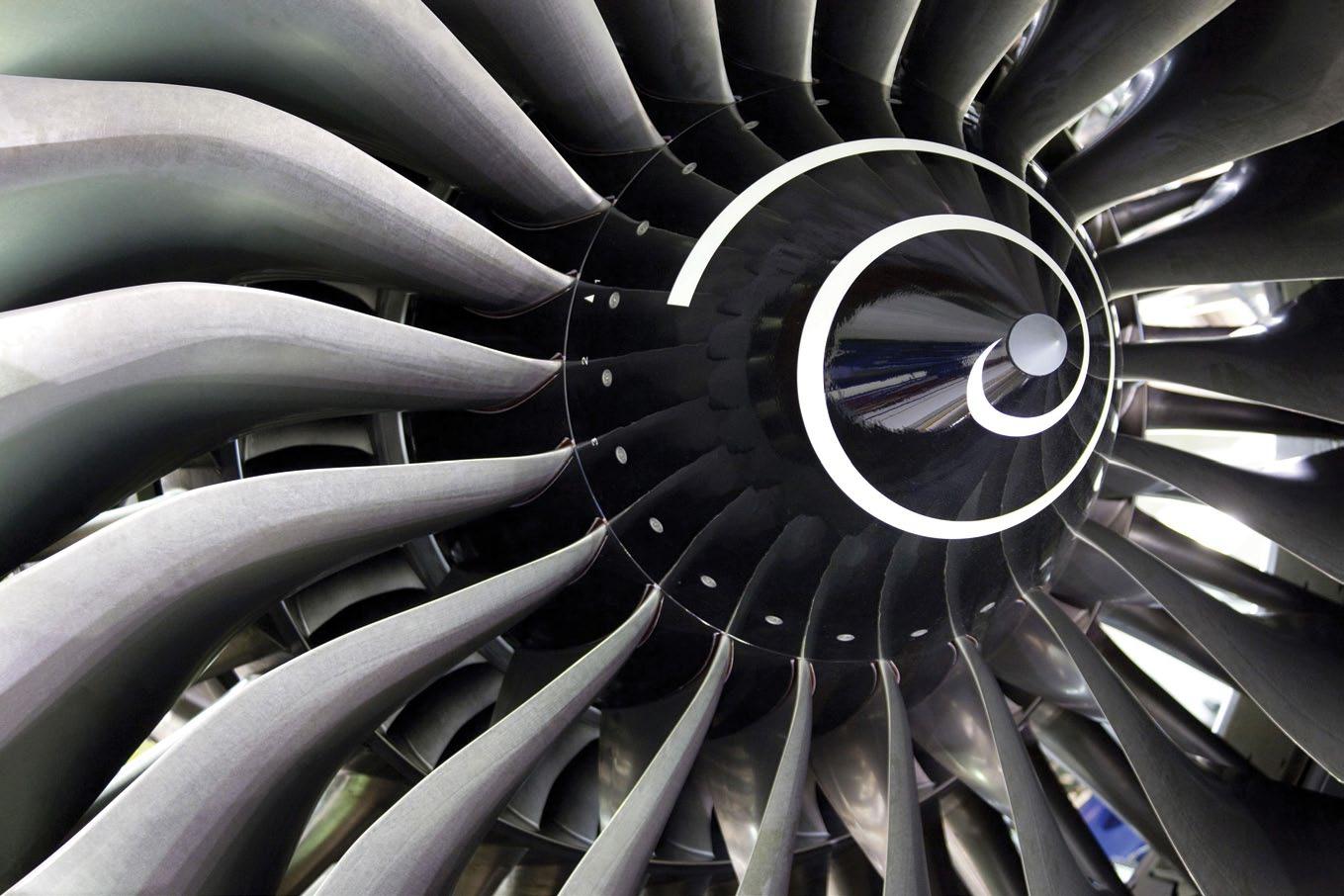
5 minute read
Ready for take-off Forgital
Ready FoR take-oFF
Until recently a family-owned Italian company, the Forgital Group is now positioned for global growth
In August 2020, Forgital Group, the Italian-based manufacturer of large forged and machined components for the global aerospace and industrial sectors, announced that Aldo Carrabino had been appointed acting Group CEO. Luca Zacchetti, the previous CEO, was stepping down from his full-time role for personal reasons.
Aldo Carrabino, who joined Forgital as CFO in November 2019, will continue to act as CFO alongside his interim Group CEO position. The company is evaluating candidates to take over the Group CEO role on a permanent basis, while Luca Zacchetti will join the Strategic Committee of Forgital to continue to closely support Forgital in its future development.
The Board of Directors at Forgital Group, said: “We are grateful for the significant contribution Luca has made to the development of Forgital in his time as CEO, including securing a smooth transition from an entrepreneurial and family-owned company to its current role as part of a global group. Thanks to Luca, the company has strengthened its relationships with existing customers and started new strategic commercial partnerships, paving the way for a major global growth platform, notably in the aerospace sector.”
“We are also delighted that Aldo has agreed to be Group CEO ad interim while the Board finds a permanent successor. Since joining Forgital, Aldo has successfully led the finance function delivering on many opportunities to improve efficiency and performance and we have every confidence in his ability to steer the company as CEO for the months ahead.”
Joining a global group
Founded in 1873 in Vicenza, Italy by the Spezzapria family, Forgital is a specialist manufacturer of machine-finished forged and laminated rolled rings, made from several different materials, including steel, aluminium, titanium, and nickel-based alloys. Its products
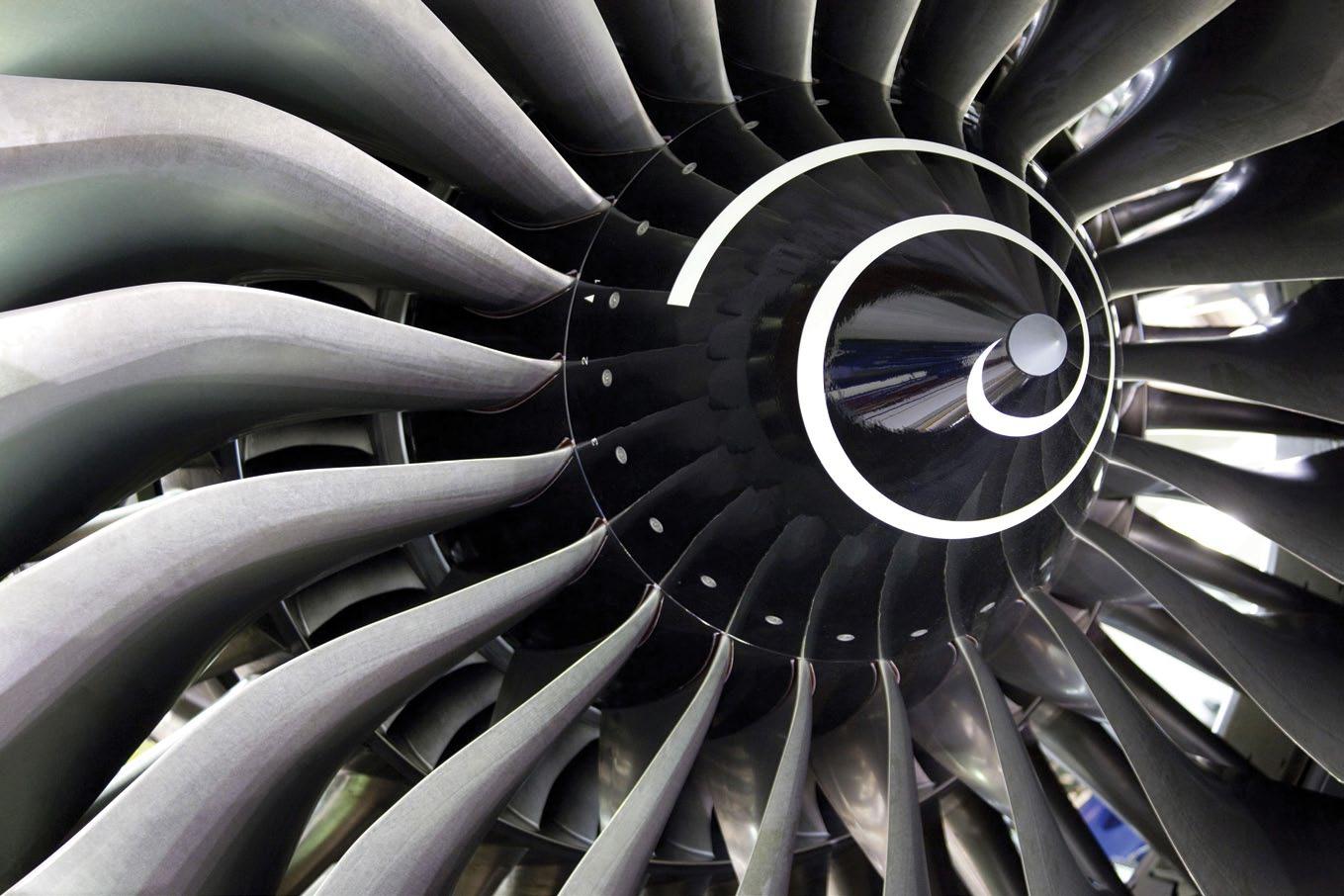
are used in several applications across many industries, including aerospace, oil and gas, construction, mining, and power generation. Forgital employs over 1,100 people across nine facilities in Italy, France, and the United States in its dedicated global salesforce. Today the Vincenza factory has three hot-working lines, a complete range of over 20 furnaces for heat treatments and an extended machining capacity.
A new chapter opened for the Forgital Group in September 2019 when it was acquired by the multi-national private equity company The Carlyle Group.
Welcoming the new member of the Carlyle Group, Derek Whang, Principal on Carlyle’s Aerospace, Defense and Government Services team, said: “We look forward to partnering with all Forgital employees as we embark on this next chapter. The Company has a tremendous heritage, and we are committed to upholding Forgital’s exceptional track record and delivering its mission critical parts to all customers.” expanding in aerospace
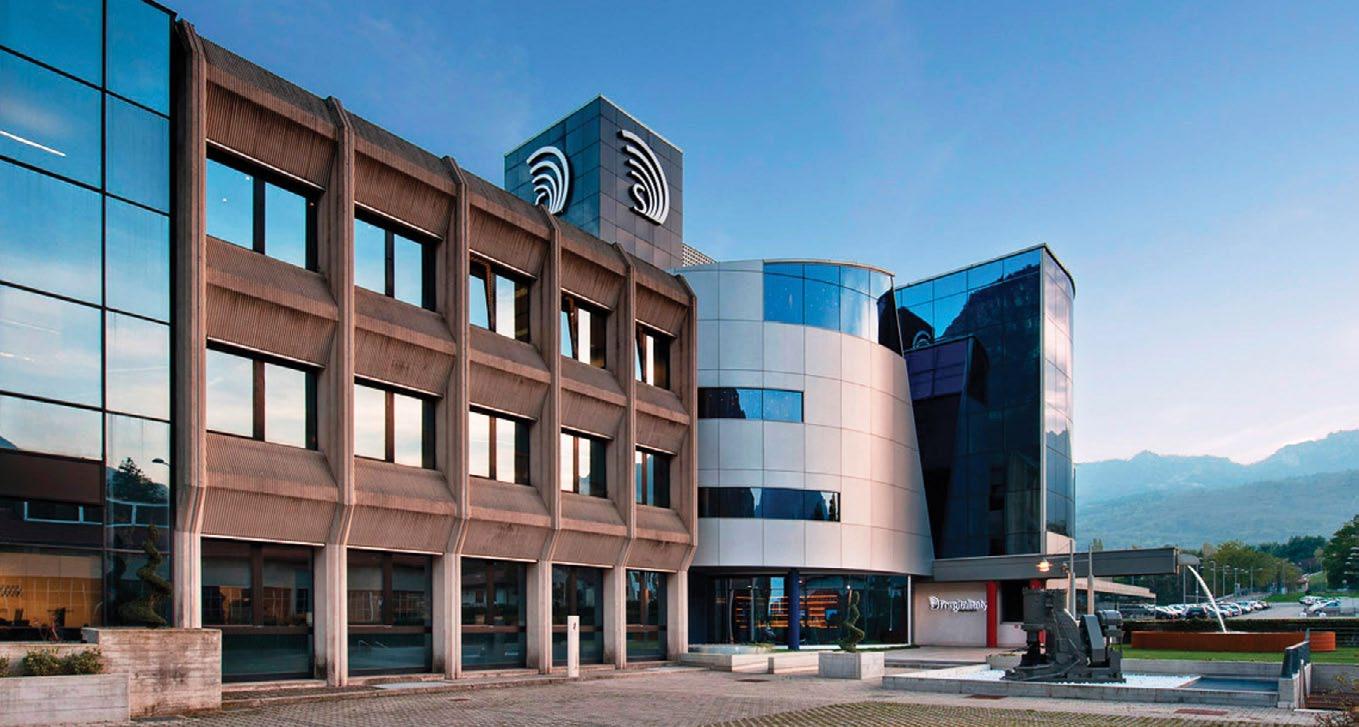
The rolled rings manufactured by the Forgital Group cover an extremely wide range and are used in applications in many industries. In recent years the Group has expanded into the aero engine market and has become one of the small number of companies qualified in the supply of important airplane engine components for many of the most important aircraft currently in production.
Forgital’s development in the aerospace sector began with the project for the Ariane IV launcher and developed along with Ariane V, Vega, PSLV and GSLV programmes. Today, the Group provides components used in the manufacture of jet aircraft engines, space launchers, satellites, and orbital stations.
In 2007, Forgital established its FLY specialty machining and custom fabricating operation in Grigno, Italy, to serve its aircraft and jet-engine customer OEMs and subcontractors. Services include quality control, testing, and coordinate measuring service, as well as


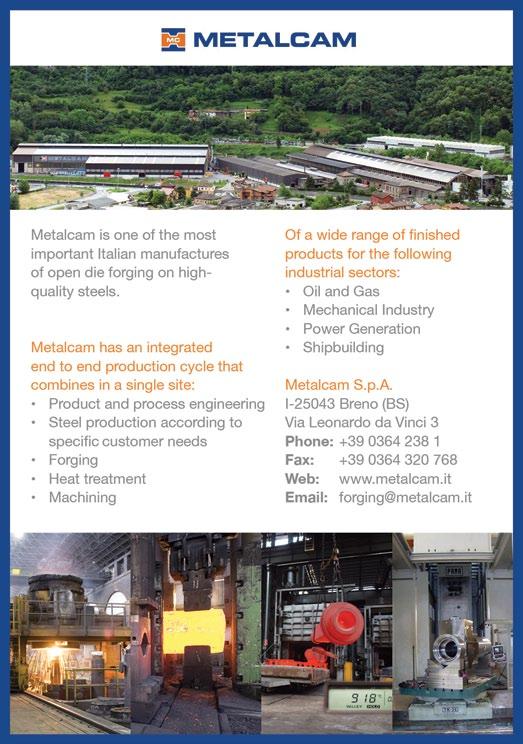
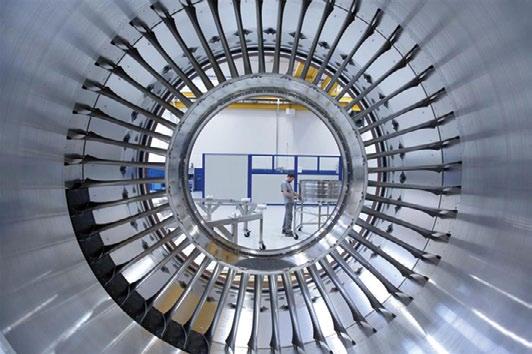
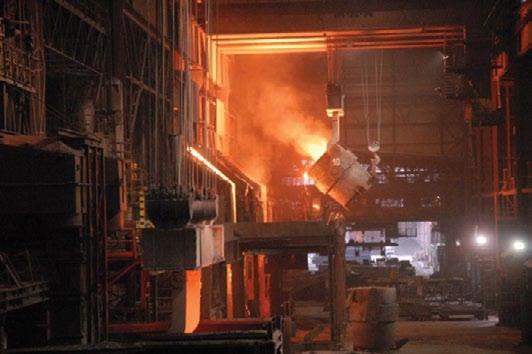
specialty machining. Among its current customers are the RollsRoyce Trent XWB engine program, and the Ariane Space consortium producing a launch system for the Ariane 5 rocket.
Since its establishment, FLY has grown from the initial five employees to some 200 and from a production site of 5,000 square metre to a plant now exceeding 25,000 square metre. It has developed into an innovative machine shop able to complete Forgital’s production chain with the supply of complete finished and fully assembled components for aviation and aerospace customers worldwide.
Forgital’s aerospace business took a major step forward four years ago with the award of a contract from Rolls Royce for components for the RR Trent XWB engine. The very first Trent7000 Fan Case Assy Module, which will equip the Airbus A330 Neo aircraft family, was delivered to the Rolls Royce headquarters in Derby, UK, in 2016. For this module, Forgital provides titanium components for the Front Fan Case and the Mount Ring.
In 2017, the Forgital Group announced that its FLY plant was to double in size. It allocated 27 million euro for the construction of a new 6,600 square metre plant adjacent to the existing factory.
Capabilities across sectors
The Forgital Group is also a major supplier of products for the oil and gas sector. For surface applications it supplies ball valve components for pipelines. For deep water operations it supplies components such as connectors and riser flanges for submarine well-heads and for conveying petroleum products to the surface. Forgital components for the transmission markets include bearings, gear wheels and shafts that are widely used in port and naval cranes, crane trucks, cranes for the building industry and excavators
The Forgital Group’s operations in the power generation sector go back to the early seventies with its involvement in nuclear energy development projects in Europe. Today, its power generation business provides components for steam turbines, gas turbines, nuclear power plants, hydro power plants and wind power plants
Operating across all its business sectors, Forgital Group’s ‘Compact Supply Chain’ is an integrated system of technologies and services that supports all phases of the production process, from ingots to assembly. It offers customers direct, full product responsibility, simplifying their procurement process, as well as bringing significant cost and logistics advantages. The system also reduces lead times and working capital across the board. n
