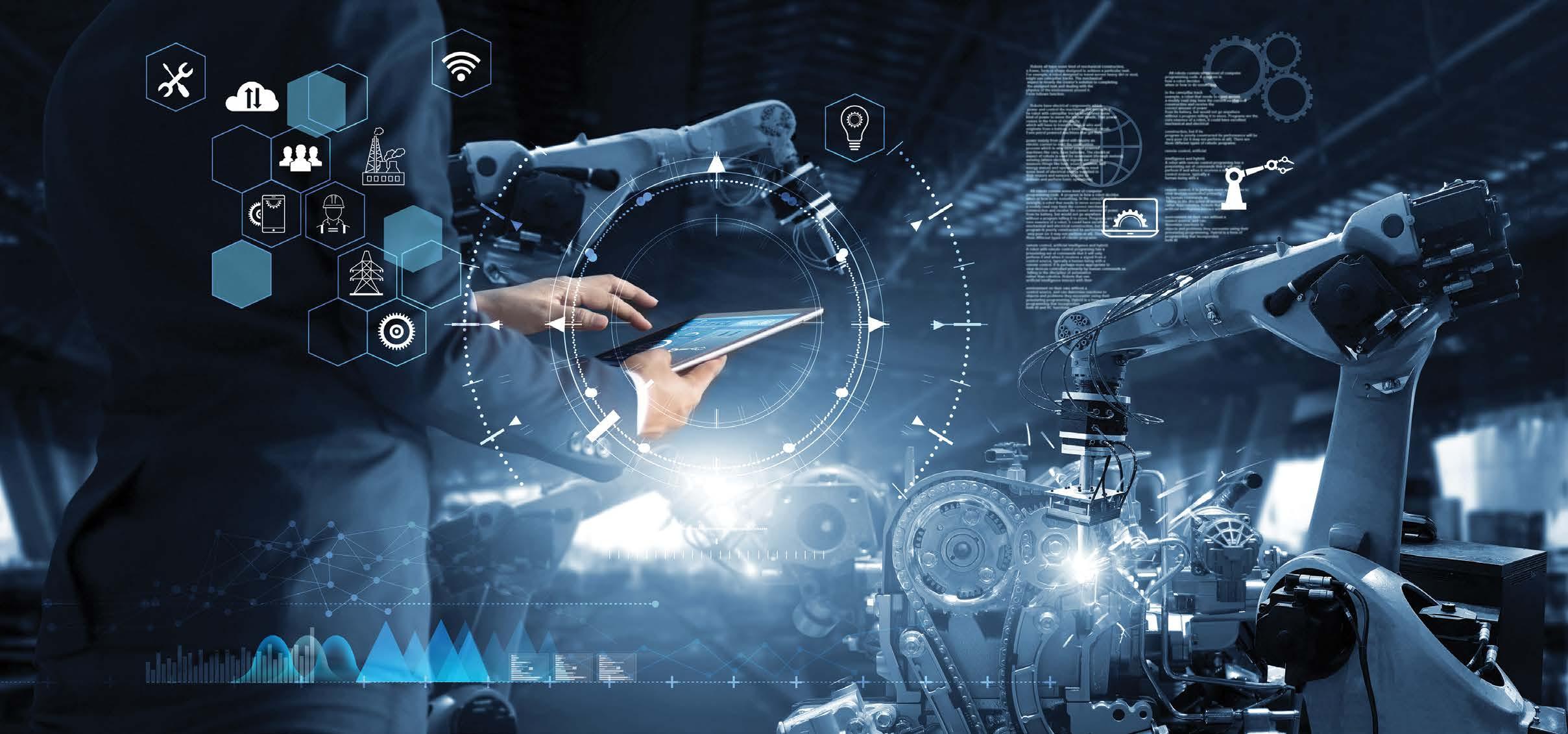
4 minute read
Manufacturers must adopt Industry 4.0
Despite the term Industry 4.0 having been in circulation for nearly a decade now, many manufacturers are yet to tap into the much-vaunted benefits. In 2018, just 20.7% of manufacturers rated themselves as “highly prepared to address the emerging business models the Fourth Industrial Revolution brings”. Even now, many manufacturers still remain slow to adopt the emerging technologies - from additive manufacturing to AI and machine learning – that are associated with Industry 4.0.
Anew McKinsey survey, ‘COVID-19: An inflection point for Industry 4.0’, which polled leaders at global manufacturing companies worldwide, found that just 26% were prepared to say they had scaled some or many Industry 4.0 use cases.
One of the reasons for this is that many manufacturers are being driven by a desire to keep up with industry trends or the latest competitor actions. CIOs and CFOs at these manufacturers are focused above all on getting a return on their investment or at the longest medium term and that tends to mitigate against making longer term investments in the latest advanced technologies.
The risk of not investing
For these manufacturers, there is a significant downside to keeping their powder dry over new investment over the longer term though. Manufacturers will find that they increasingly lose out on contracts where they are outbid by smaller, more agile specialists who are focused on bringing in technologies like Industrial Internet of Things (IIoT) or robotic process automation (RPA) to enhance their specialism.
Customers will increasingly look to these companies to meet their more specific needs and get better value for their money. The semiconductor industry is a good example. The number of players has shrunk significantly to the point where there are arguably just three in play that manufacture advanced semiconductors on a global scale down from around 20 in total. As of 2021,
there are believed to be only three firms able to manufacture the most advanced semiconductors: TSMC of Taiwan, Samsung of South Korea, and Intel of the United States.
The reason for the success of these firms has largely been their capability in the specialisation and optimisation of manufacturing technologies. Customers have increasingly realised that it is much cheaper to have their product made somewhere where manufacturing is more optimised. So, a failure to invest in technology to optimise processes and reduce the cost of manufacturing can be a big risk factor.
Relying too much on people to carry out processes will also increasingly bring risk. If manual processes are prevalent and there is no digital analytics capability in place to be able to predict the impact of a sudden change, like the advent of the pandemic on manufacturing processes and the supply chain in general, they will almost certainly struggle to keep up with smaller more specialised competitors that can rapidly adapt to the shifting market trends.
So how can manufacturers begin to break down the barriers to adoption and position themselves more strongly to accelerate this in the future? There has to be a sense of urgency brought into the equation and an understanding that the timing of investment is crucial. Visualisation is key and it is important that decision-makers within these organisations can see first-hand how the implementation of Industry 4.0 technologies will actually impact their supply chain processes in practical terms. Manufacturers should be encouraged to bring their specific problems to the table so that solutions can be discussed and provided.
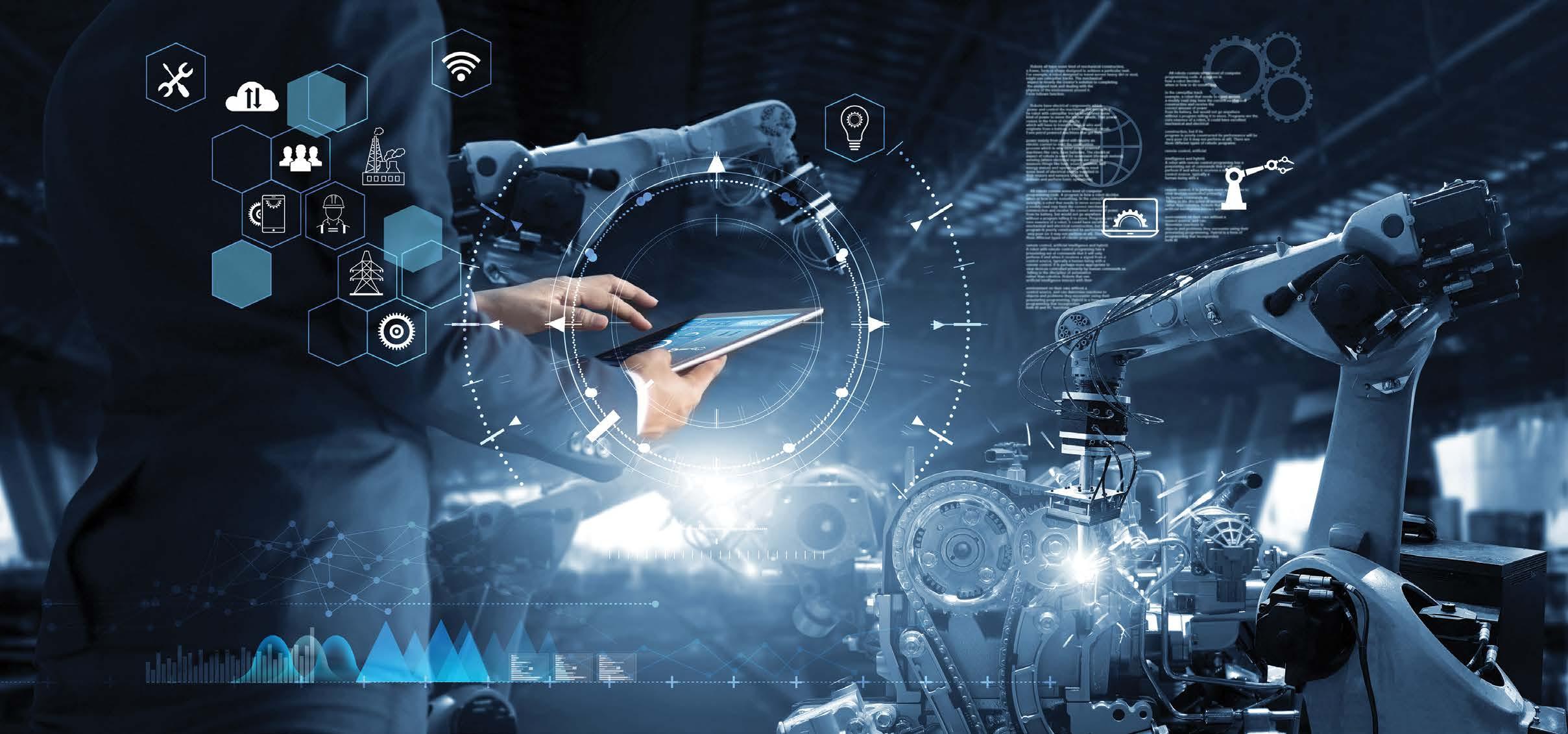
Finding a solution
There are a raft of technologies out there that can help organisations to address the challenges that they have. Some examples from Industry 4.0 are cloud computing to scale technology infrastructure based on shifting business needs (e.g. to support acquisitions or divestitures). Looking at business processes where technology-enabled, desktop-based process automation would be a good starting point. Additionally, looking at business cases for implementing RPA is one area that could be useful.
Another that would bring value within many manufacturers would be the physical implementation of machine-based manufacturing – where organisations can achieve a virtualised view of a project, through 3D modelling of factories, the visualisation of different scenarios and the impact of certain modifications etc, which can be analysed before significant changes are made.
While many manufacturers at the current time have restrained budgets, it makes sense for many to go back to the basics of automation and make sure these are being effectively implemented. It may be more cost-efficient and operationally effective to focus on improving processes where they may have a capability that they are not making optimum use of – the application of predictive analytics to supply chain processes may be a case in point, or the use of analytics to scrutinise large volumes of supply chain data and draw conclusions about patterns and trends.
Forging ahead
Ultimately, it is clear today that the slow adoption of Industry 4.0 technologies is putting many manufacturers at risk. If manufacturers want to be competitive moving forwards, it will be increasingly important that they look at the benefits of advanced manufacturing technologies and of implementing those to optimise processes and reduce the cost of doing business. In today’s increasingly competitive manufacturing environment, retaining a predominantly manual approach is no longer a viable option for organisations. It is time for manufacturers to take action and start moving positively forward on the road to industry 4.0. n
The author, Danish Sherwani, is a SAP S/4HANA Solution Architect at Delaware UK.