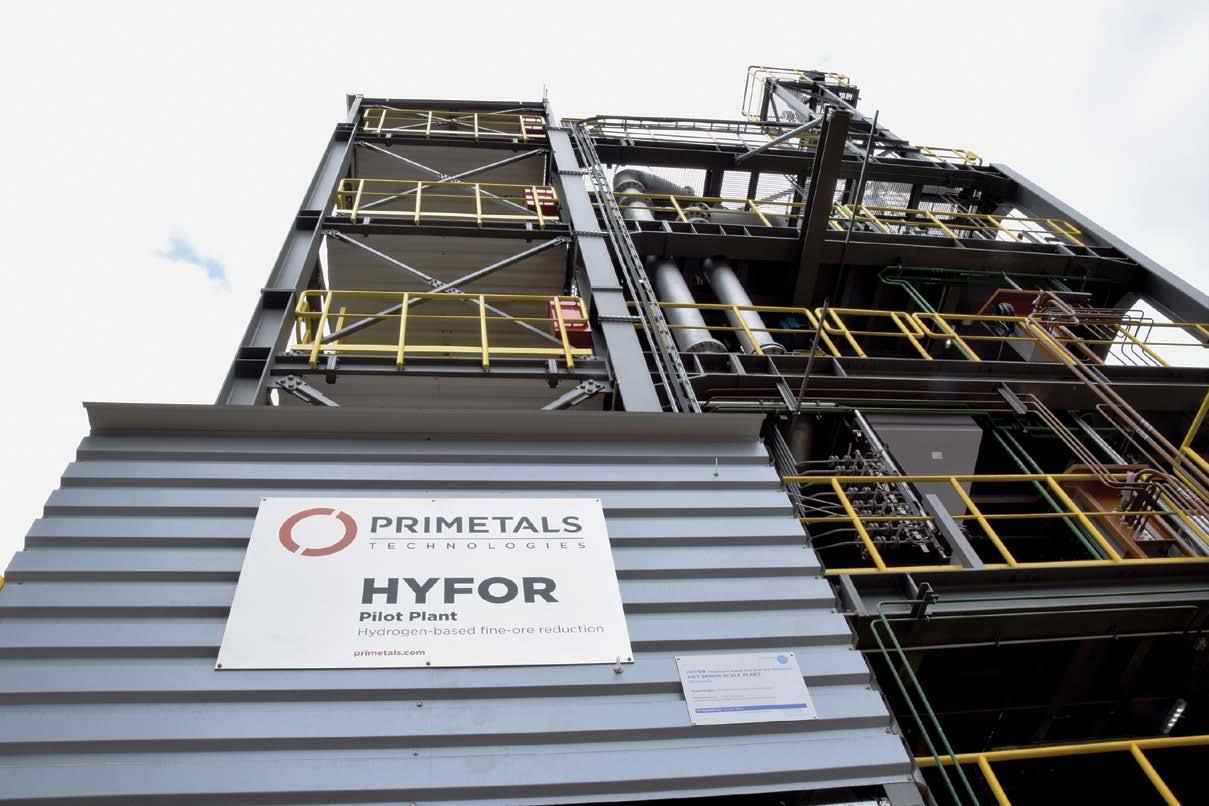
7 minute read
Harnessing Hydrogen for Green Steel
STEELING THE FUTURE: USING HYDROGEN TO MAKE GREEN STEEL
IE Speaks To Primetals' Dr Alexander Fleischanderl About The Innovative HYFOR Green Steel Project In Austria.
In 2020, the global steel industry produced a total of 1.86 billion metric tonnes and turned over hundreds of billions of dollars. Steel, with its high strength-to-weight ratio and relatively low production costs, is an invaluable material for many sectors such as construction and automotive.
However, in the context of the climate crisis, the sector has come under increased scrutiny due to its reliance on carbon-intensive fossil fuels, primarily coal. Global steel production accounts for around 8% of total global carbon emissions, and its hunger for coal continues to drive excavation. For every tonne of liquid steel produced using the traditional integrated process method, 770kg of coal and coke is burned, releasing 1.8 tonnes of CO2 into the atmosphere – meaning the steel industry is actually a bigger producer of carbon dioxide than it is of steel.
In recent years, governments across the world have been looking for ways to meet the goals of the 2015 Paris Climate Agreement, and as such, the political pressure on the sector to decarbonise is also mounting.
But it’s not only governments putting the pressure on. Increasing financial pressures like the price of carbon and the rise in the popularity and credibility of Environmental, Social and Governance scores amongst a younger, more environmentally conscious generation of investors looking to put their money where their morals are, both increase that pressure and offer ever-stronger incentives to decarbonise the sector.
Against this backdrop, several small-scale “green steel” projects have begun popping up in Europe and beyond. One of these is Primetals Technologies’ hydrogen-based fine-ore reduction (HYFOR) pilot project, at the voestalpine steelworks in Donawitz, Austria.

Dr. Alexander Fleischanderl
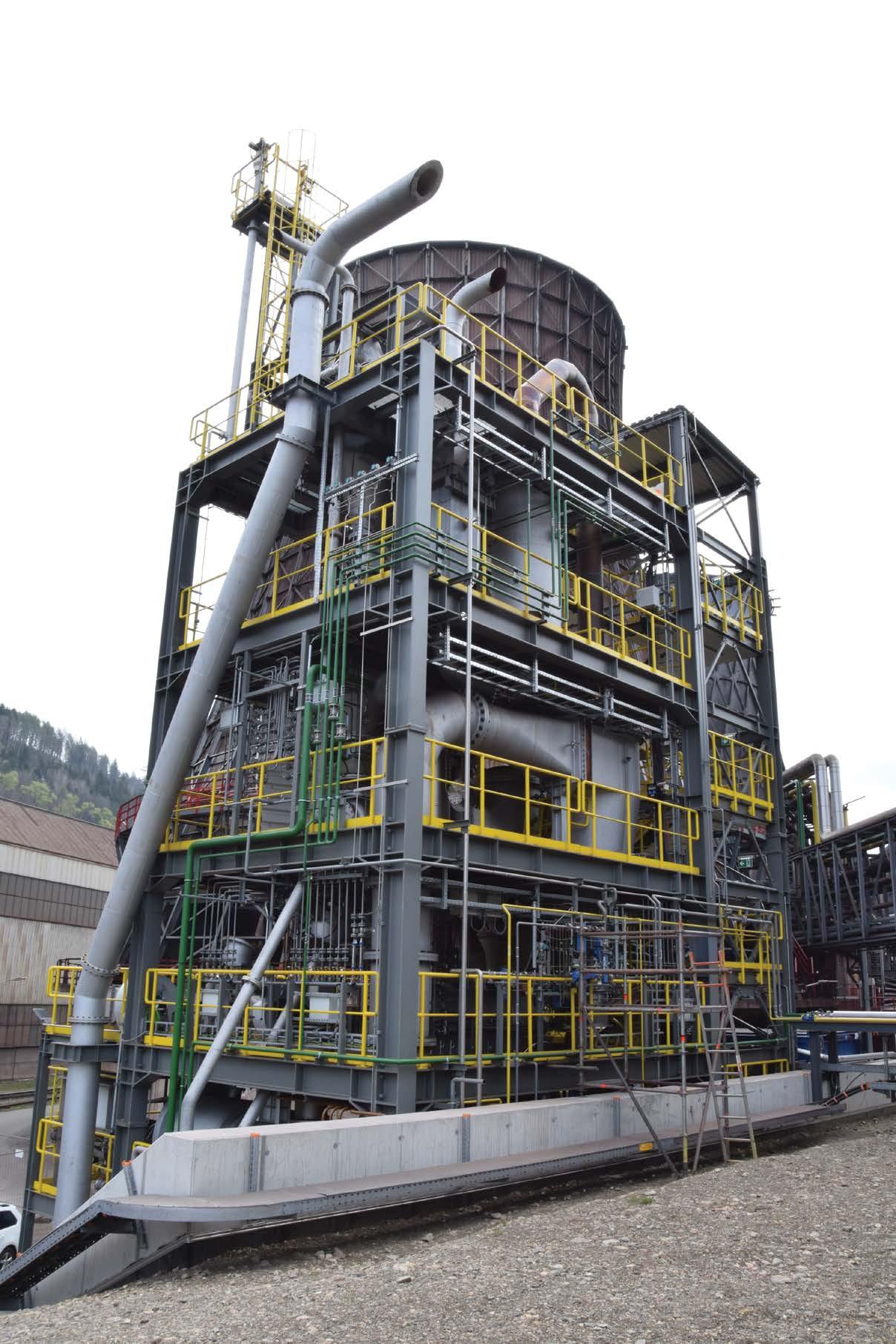
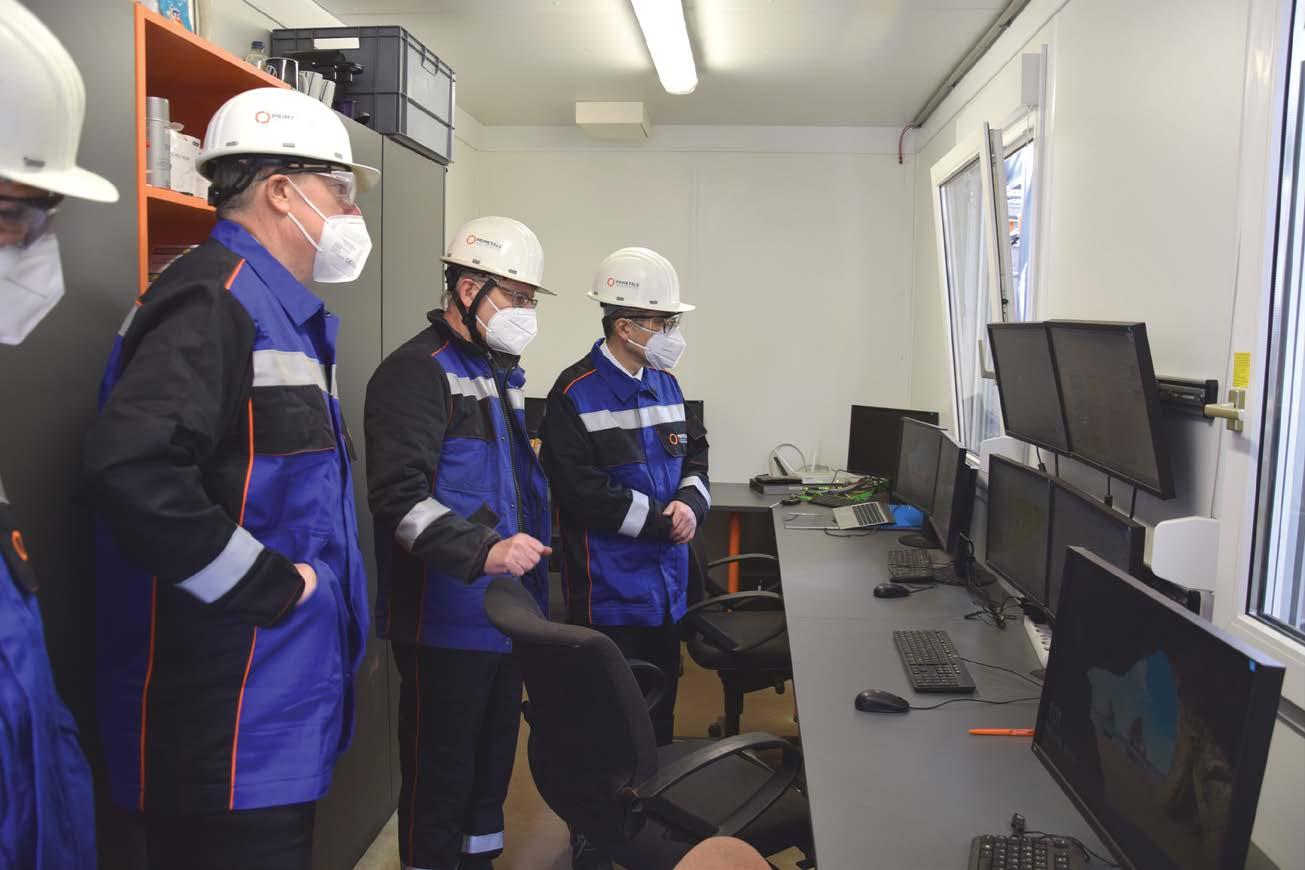
After years of development and two months of initial tests, HYFOR became operational in June and since then, has caught the attention of many in the industry for its innovative direct reduction process for iron ore concentrates – the first of its kind in the world. HYFOR is powered with 100% hydrogen, which slashes emissions by as much as 90% and the pilot is set to be operational for the next two years at least.
“The energy for 75% of global steel production comes from carbon, with the rest coming from gas and electricity. The only thing that we can change is to get rid of coal,” Dr Alexander Fleischanderl, the Head of Eco Solutions at Primetals Technologies told Industry Europe.
“However, we also need to remove the oxygen from the iron ore, which leaves us three options. We can burn carbon, which releases CO2. We can use hydrogen, which releases water. Or the third option is using electrons, to turn iron ore into steel with direct electrolysis, the technology for which is only in its infancy.”
Energy efficiency, or process optimisation, Dr Fleischanderl believes is the first phase for decarbonisation of the sector.
“There are many opportunities to decarbonise using existing assets. They should be utilised otherwise they will end up as stranded assets. You can optimise sinter plants, pelletising plants, and blast furnaces. You can inject gas, starting with natural gas, but also hydrogen. You can implement other energy efficiency solutions like waste heat recovery, where the heat is recovered from slag. Most customers have still not implemented such solutions.”
The reason for this, Dr Fleischanderl says, is usually about return on investment. “Most customers want a return in one or two years. These solutions take five or six years to pay off. Nonetheless, in the future, it will be mandatory.”
Recycling scrap steel will also go some way towards cutting emissions. The problem there is availability, he added.
“The issue is that the production rate is higher than the scrapable stocks. If we look to 2050, we estimate there will be around 900 million tonnes of scrap to be recycled, but we will produce more than two billion tonnes of steel. So, there is still a gap of more than one billion tonnes that we have to close with the virgin feed coming from iron ore.”
While advances in energy efficiency and circular economy initiatives play an important role in the greening of steel, they can only do so much - around 30% in carbon footprint reductions at most. Carbon Capture and Storage (CCS) looks certain to also play an important part in the sector’s drive to cut emissions, allowing some of the carbon to be sequestered.
However, with global demand rising, bringing steelmaking down to net-zero will require a fundamental shift in technology. Which is where HYFOR comes in.
The focus of the pilot at Donawitz is the continued development of the HYFOR technology up to a point where it is ready to be scaled up into its first industrial prototype - a decision on which is expected at the end of the year.
What separates HYFOR from its green steel peers, Dr Fleischanderl said, is what it feeds on.
“We directly feed in iron ore fines and ultra-fines concentrate, and so on. We can avoid beneficiation – the pellet dicing step – and feed ore fines directly. It removes the requirement to invest in a pelletising plant which is a big burden asset.
“The other thing is the operational costs. You avoid the fossil fuel requirement for heating up and cooling down of the pellets before feeding. By using iron ore fines and ultrafines, you can easily reduce these ore grains completely, much quicker, and staying at a
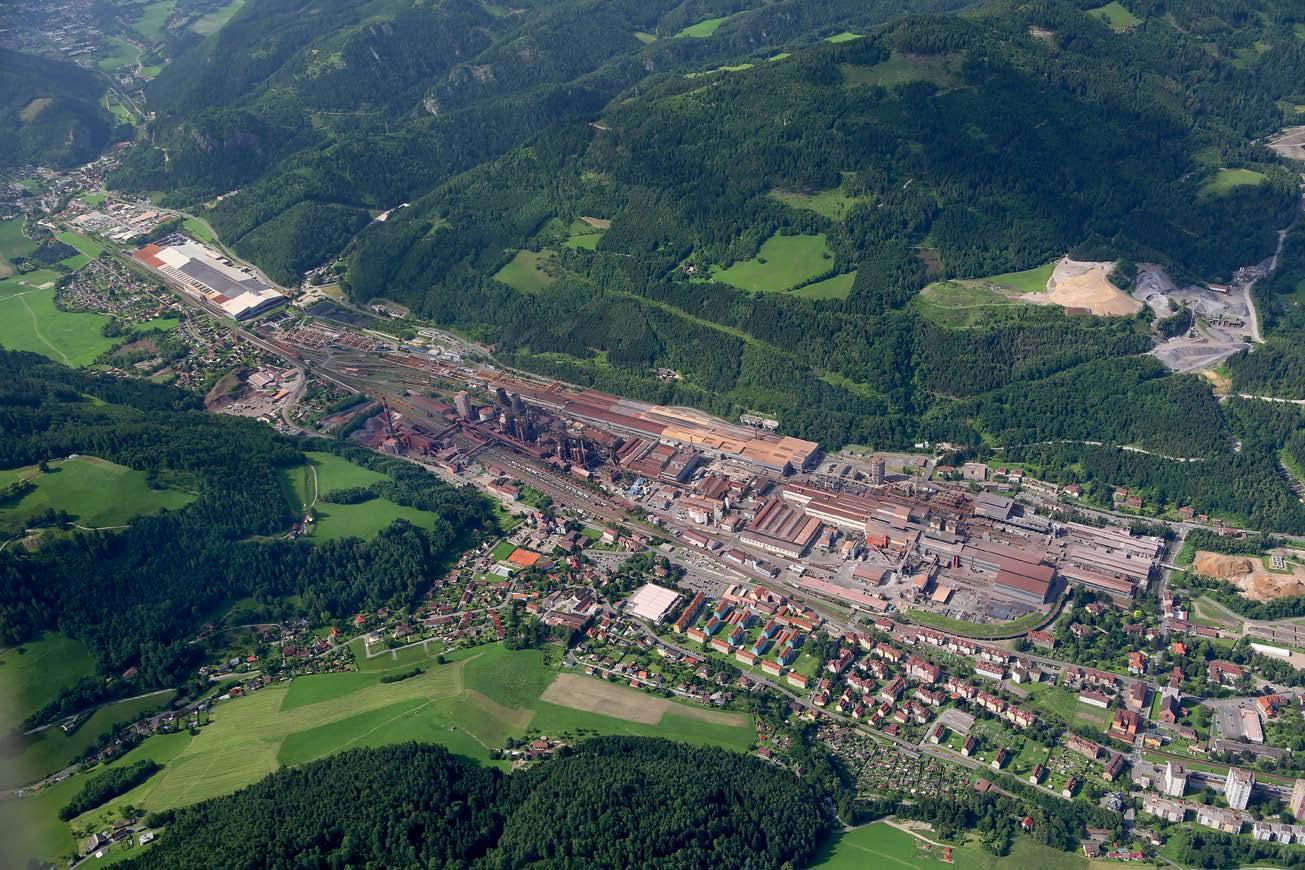
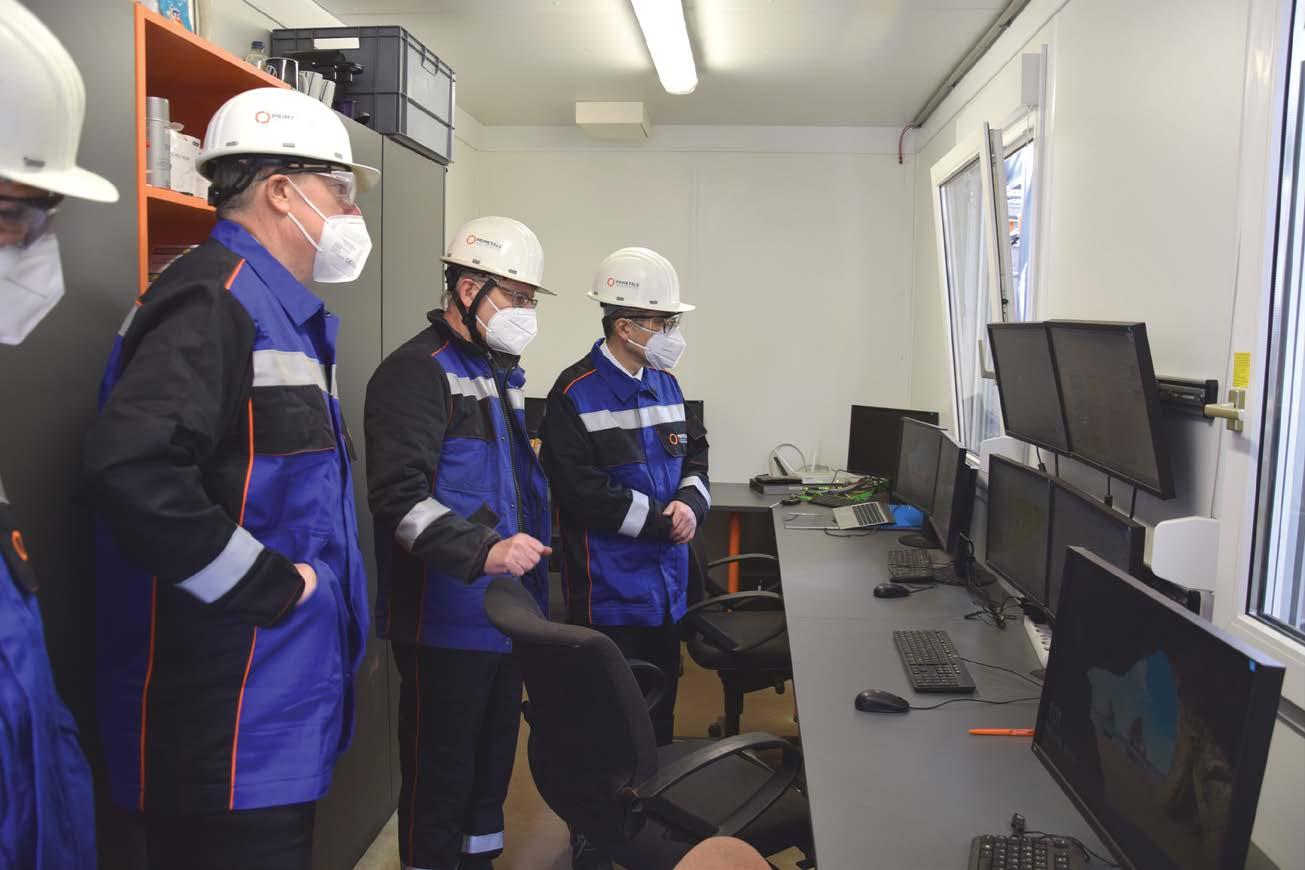
lower reduction temperature and process pressure means more energy efficiency.”
This is part of what Dr Fleischanderl describes as the ‘transformation phase’ - the next step in steel’s decarbonisation after process optimisation. He expects to see more electric arc furnaces and fewer blast furnaces in the future, with those electric arc furnaces being fed with scrap and direct reduced iron.
“The important thing is now to enable plants that can gradually switch from natural gas to hydrogen in the future,” he said, pointing to a recent project in Russia with which Primetals became involved in February.
Based in Zheleznogorsk, in Russia’s Kursk region, and run by Mikhailovsky HBI, it is the world’s largest Hot Briquetted Iron (HBI) plant. Production there will start by using natural gas but will switch over to hydrogen “whenever it's feasible”.
Despite the many promising signs that one of the biggest industrial emitters is starting to rein itself in, there is, however, still a long way to go globally, he warned.
In the EU, the Commission is looking at ways of using carbon pricing as a tool to drive down emissions in the sector. Also backing from the European Investment Fund and recovery fund can play a role in the European part of the story.
However, Europe only produces around 8% of global steel and this figure is more likely to decrease than to increase. Some major steelproducing countries still have a long way to go, he said, pointing to India as one such example.
“In 2019, India produced 111 million tonnes of steel, and they are predicting 300 million tonnes in 2030.”
The problem, he says, is that “India has no policy. It has no carbon taxing and no intention to go for that over the next years. India is still commissioning new blast furnaces, knowing that they last for 50 or 60 years or so. A mid-term solution for India might be Carbon Capture and Storage.”
China, which does have a net-zero goal - in 2060 - is also likely to keep increasing its carbon footprint until at least 2030 and is still building coal plants.
Nonetheless, says Dr Fleischanderl, HYFOR will keep moving forward.
“The long-term view is that we must utilise low-grade iron ore. At present, direct reduction plants only take high-grade ores. But in the future, we will see the gains of using lower-grade iron ore in direct reduction plants.
“Seeing a direct reduction plant using low-quality iron ore feed, going on to produce hot metal and slag in an electric-powered smelter, which would then be industry certified for use in the cement industry to get a circular economy going.
“This will help us go forward, gradually step-by-step. We need to use green hydrogen and carbon capture storage and utilisation, and we need to power the electric arc furnaces with renewable energy.
“This will get us close to a zero-carbon footprint in the future, as we look towards 2050.” n

Voestalpine Donawitz steel plant Image credit: voestalpine AG / voestalpine.com